Osteobotics Pavilion
Adamantine. Dependable. Complacent. Phlegmatic. Bones emulate an unyielding character. When you come upon a man who has been dead many years, his bones will still be lying there, in place, content, patiently waiting. Some might allude to their presence as sophisticated debris, while the ingenious lot writhes aspirations from the basic miracle of their structure and appearance. In a new project from Architectural Association DRL students Soulaf Aburas, Maria Velasquez, Giannis Nikas, and Mattia Santi, utilize Polycaprolactone, a biodegradable polyester that can stretch and also retain its compressive strength, is used to create a framework for temporary pavilions and installations. Constructed using programmable robotic arms, the resulting product is a joint-less, self-supporting mono-material that shares a visual similarity to the structure of bones – giving the project its name, “Osteobotics”. At just 60 degrees centigrade, polycaprolactone boasts a low melting point. At this temperature, the material’s structure breaks down into a soft, sticky, taffy-like consistency, allowing the polyester to be stretched into form and then hardened using a freezing spray. The Osteobotics method uses a robotic arm to stretch a triangular deposition of the material between tetrahedral nodes, a shape determined following multiple experiments of differing patterns, nodes, and heights. As one robotic arm stretches, another operates the freezing spray.
Polycaprolactone is also a highly-recyclable, fully biodegradable material, its malleability constituted only part of the project’s material choice. According to the project team, architecture and construction account for up to “seventy percent of the overall waste production in London“. Osteobotics solve this issues, as once a pavilion has finished its run, it can be melted down and used again to create new structures or simply left to biodegrade.Osteobotics’ load-bearing lattice structure requires precise calculations of pulling angles, lengths, and node orientations in space to create geometric networks. As a result, and to facilitate ease and speed of construction, pavilions are constructed in prefabricated units, so that assembly on site requires just a heat gun to join meeting surfaces. Once cooled, the units work together in one structural system.
The lifespan of these pavilions has not been streaked with complete certainty, although experimentation and analysis have been done, recyclable and biodegradable it may be, but the methods practically would still be limited if structures can only be used for a week. Additional testing will need to be done to prove its architectural viability, but thanks to its environmental nature and malleability, it is not a stretch to argue that Osteobotics could be applied for practical purposes in the near future.
Project Name: Automated Robotic Fabrication for Temporary Architecture
Team Name: Osteobotics
Team Members: Soulaf Aburas, Maria Velasquez, Giannis Nikas, Mattia Santi
Team Tutor: Shajay Bhooshan
Year: 2013-2015
Institution: London, AADRL, Architectural Association School of Architecture
Credits: Vishu Bhooshan, Theodore Spyropoulos
Robots used at Robofold.IO, London, UK2 ABB robots
By: Aleeshba Saigol
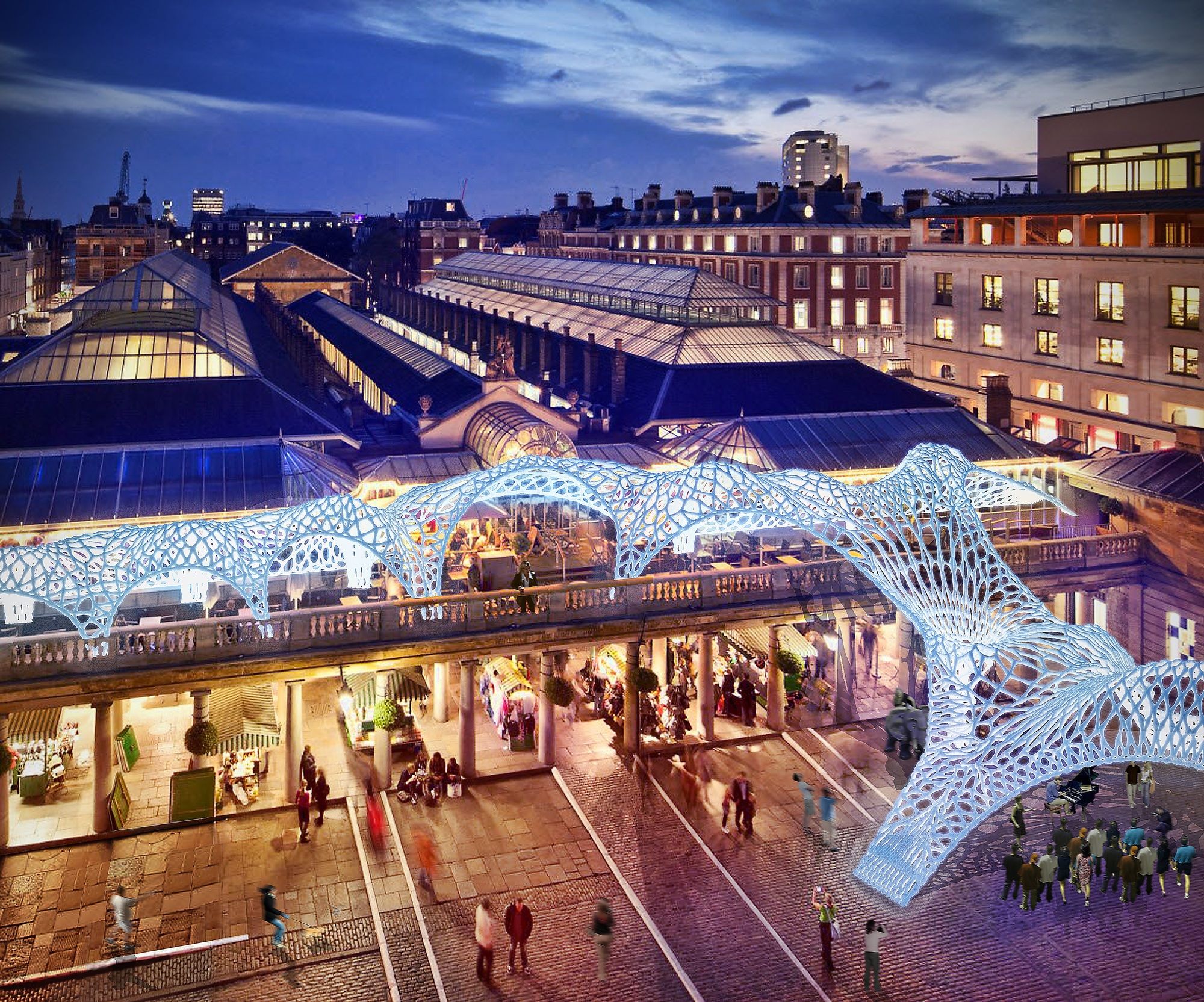
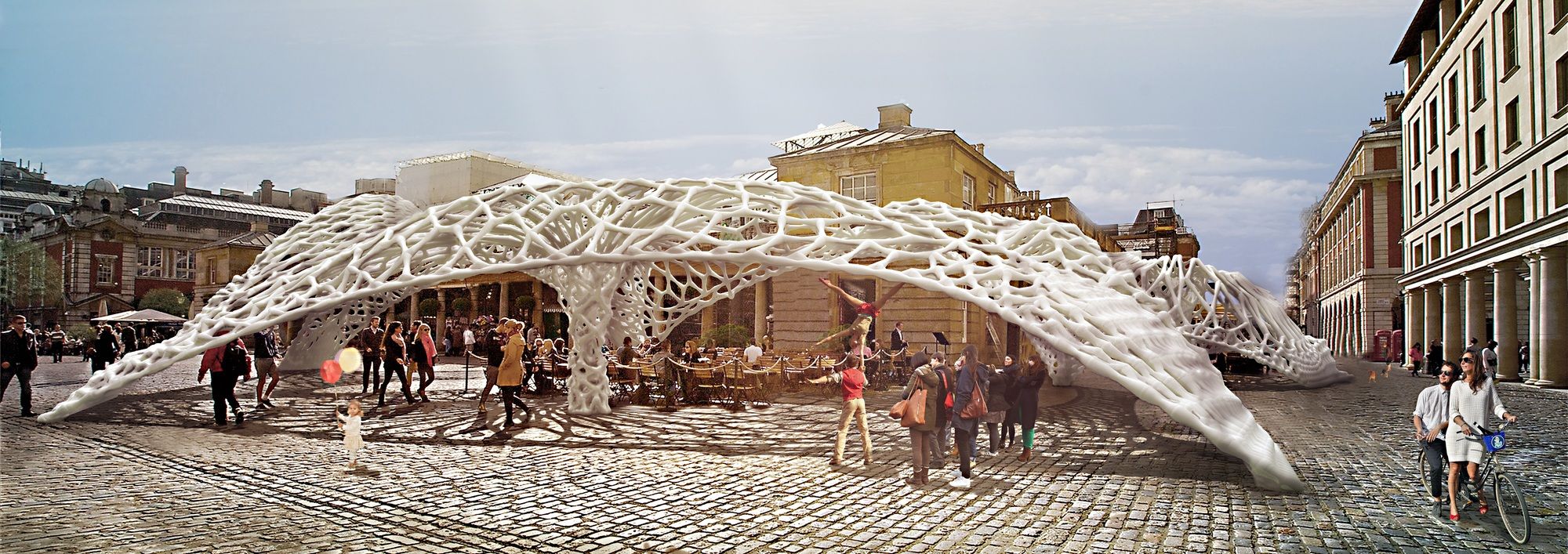

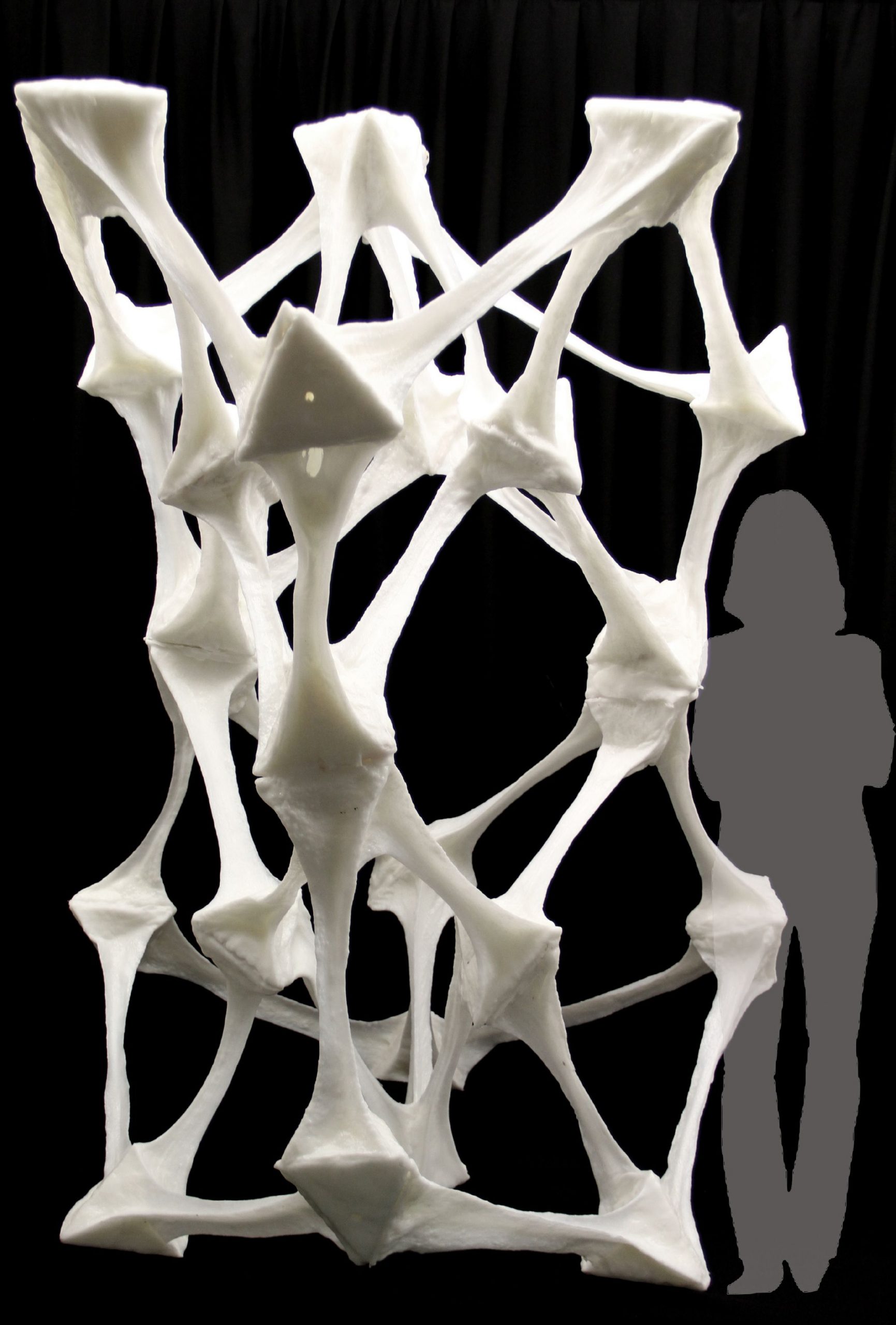
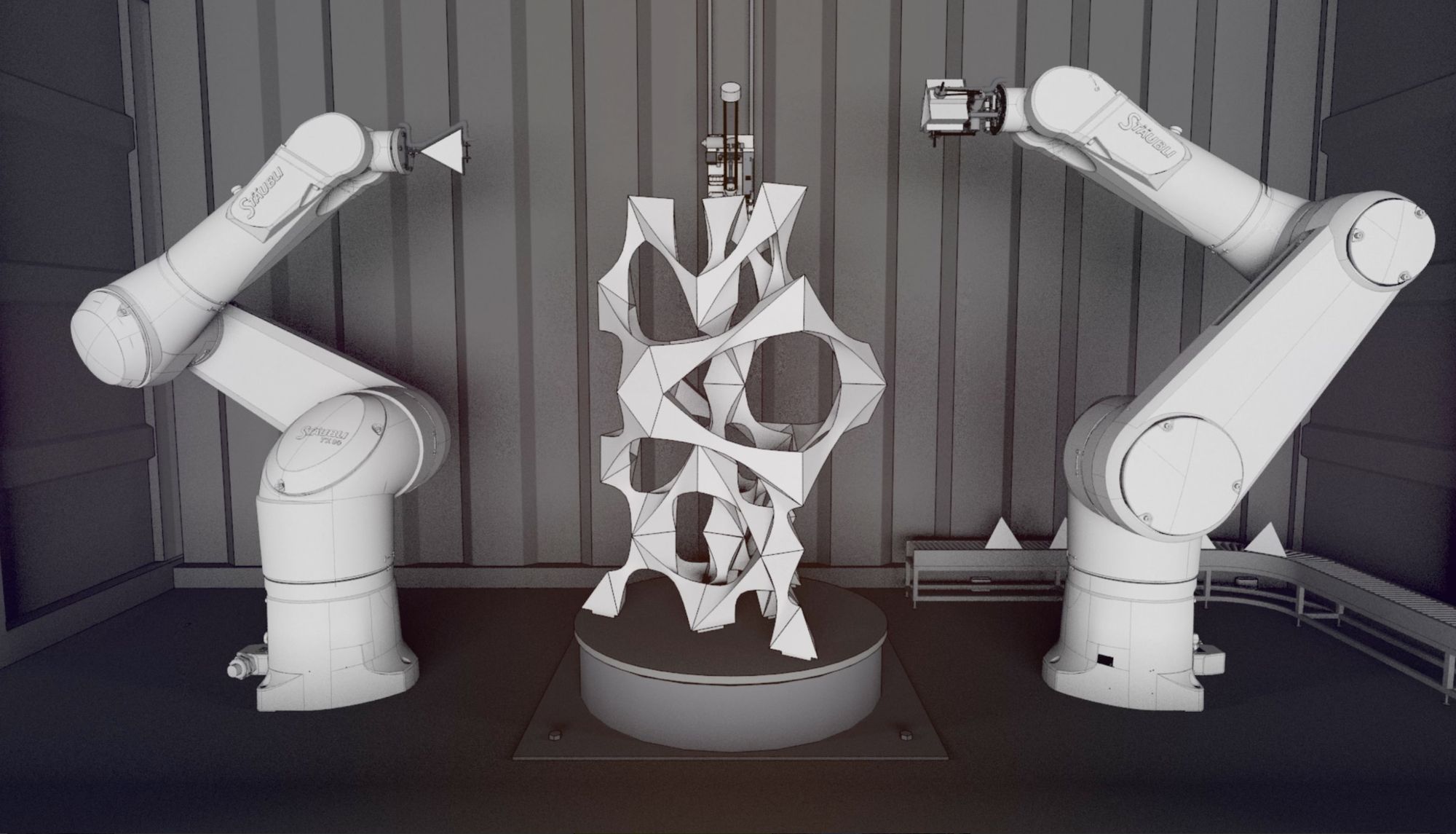
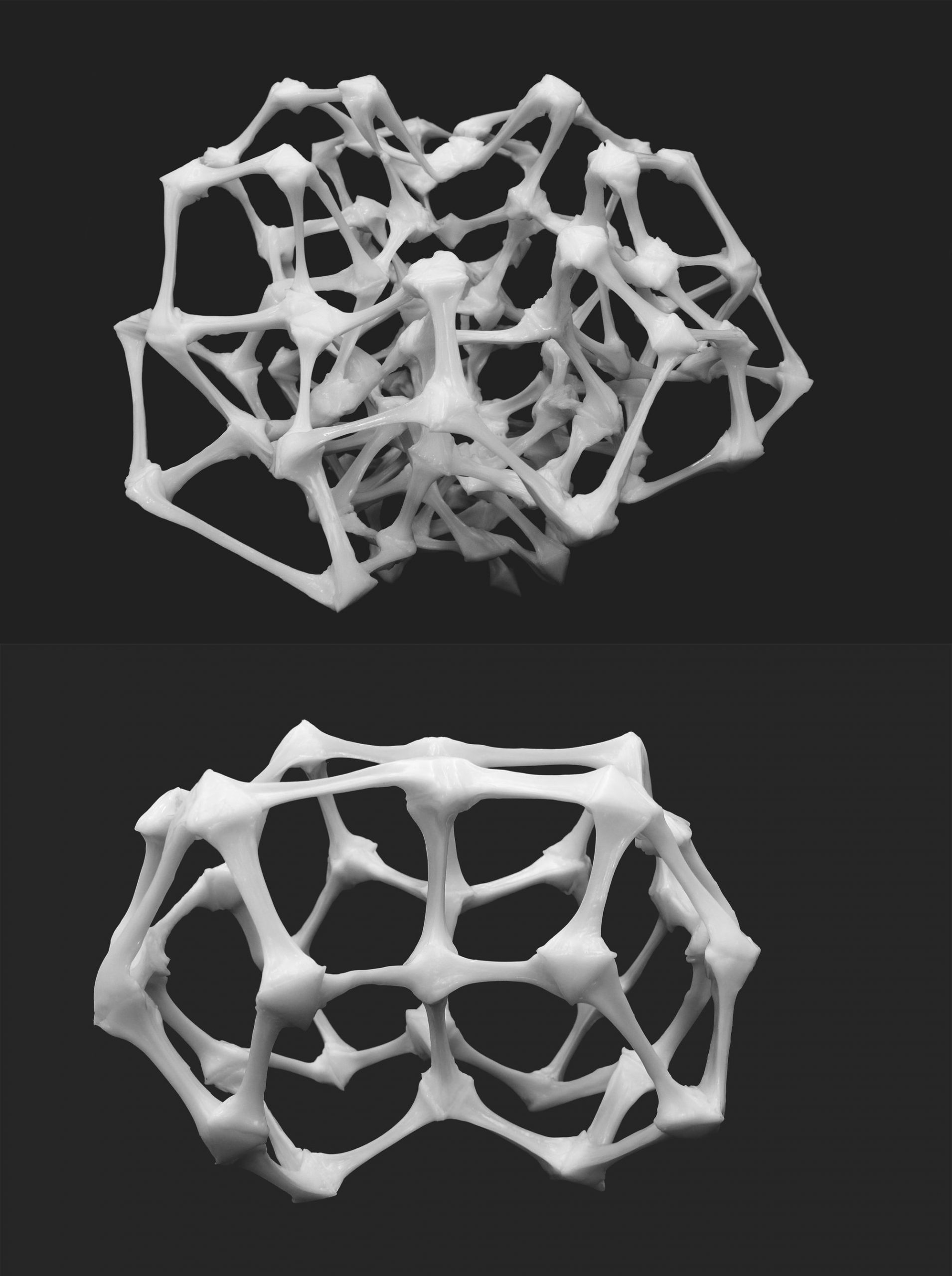

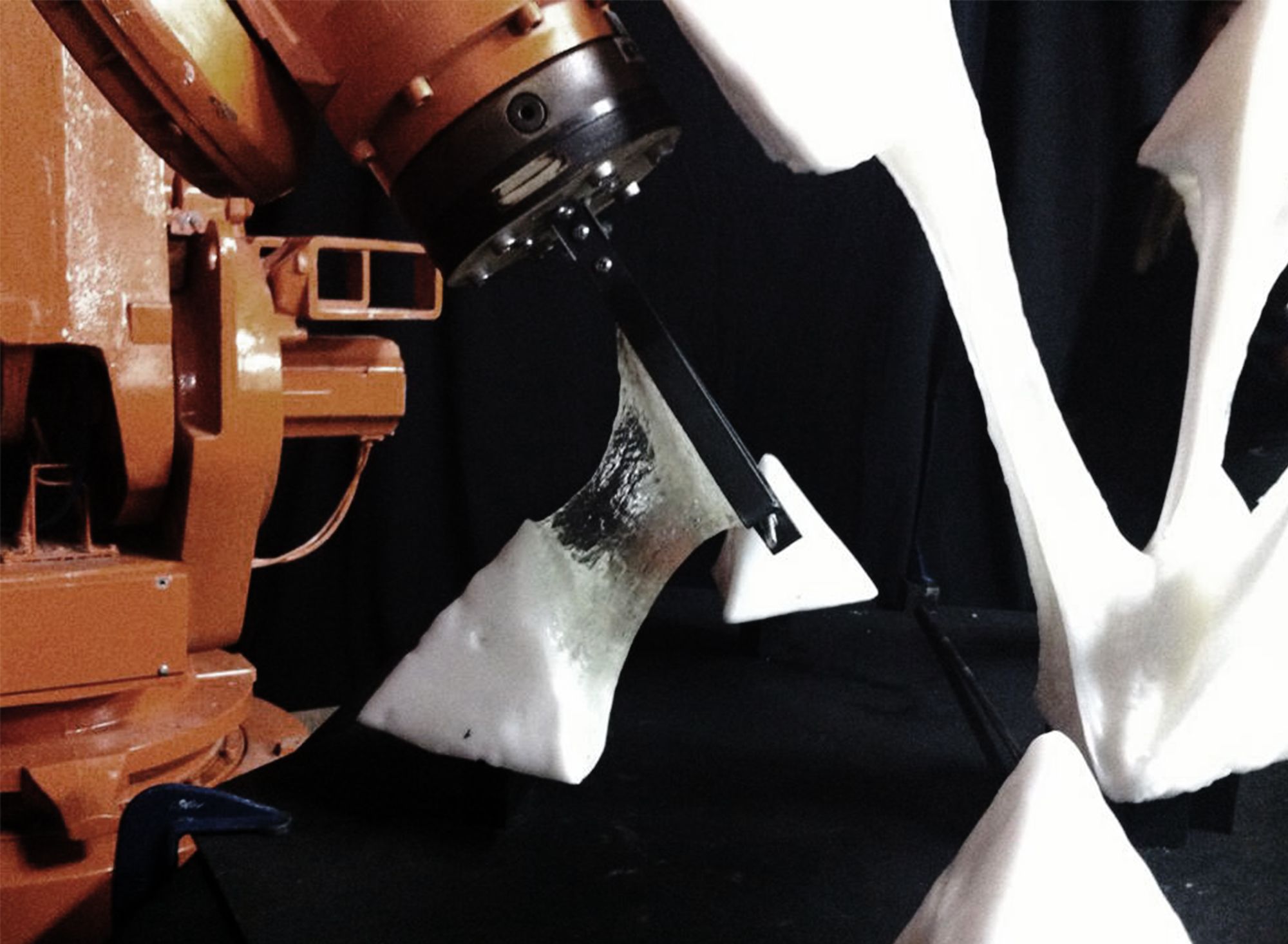
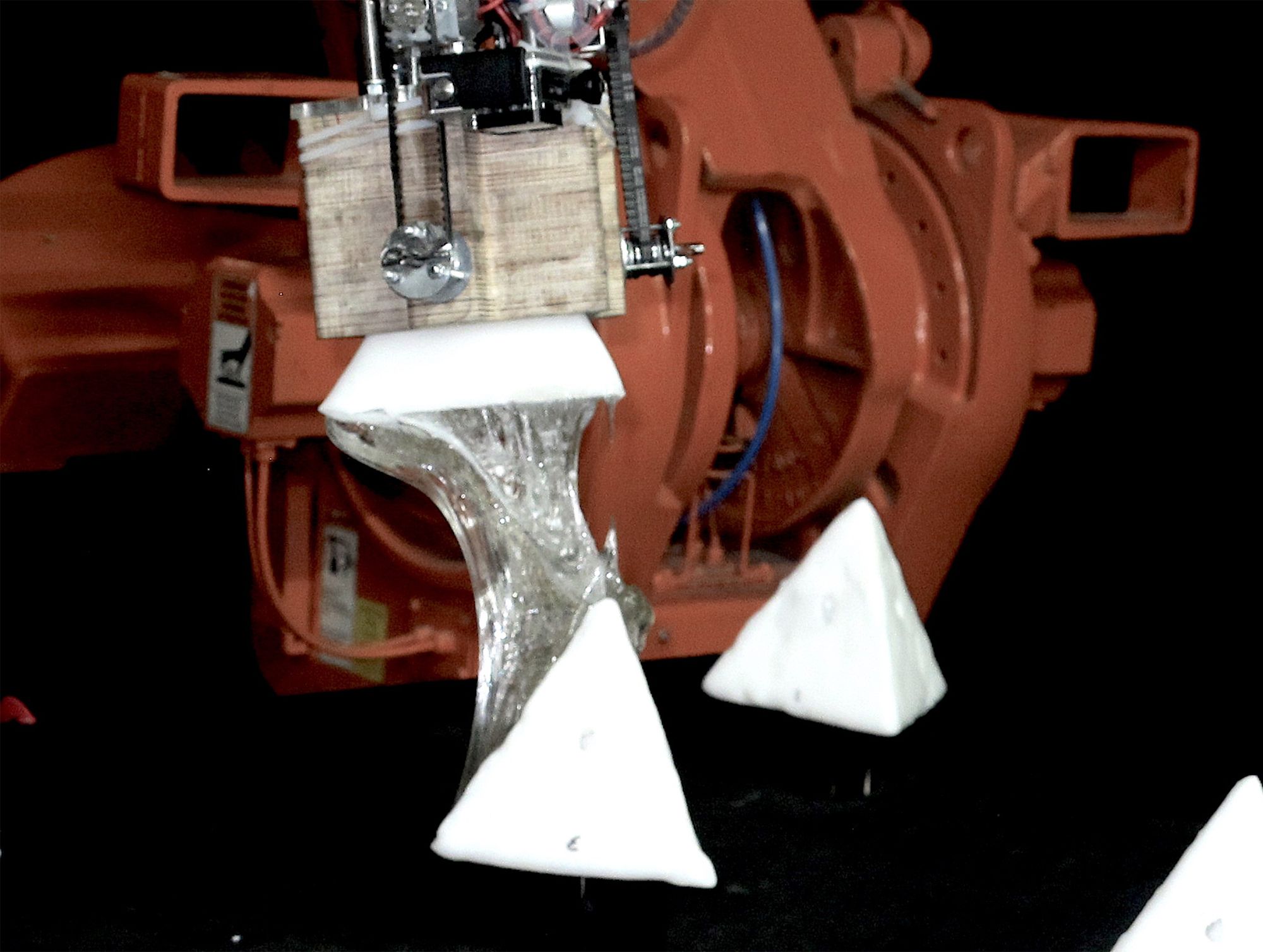

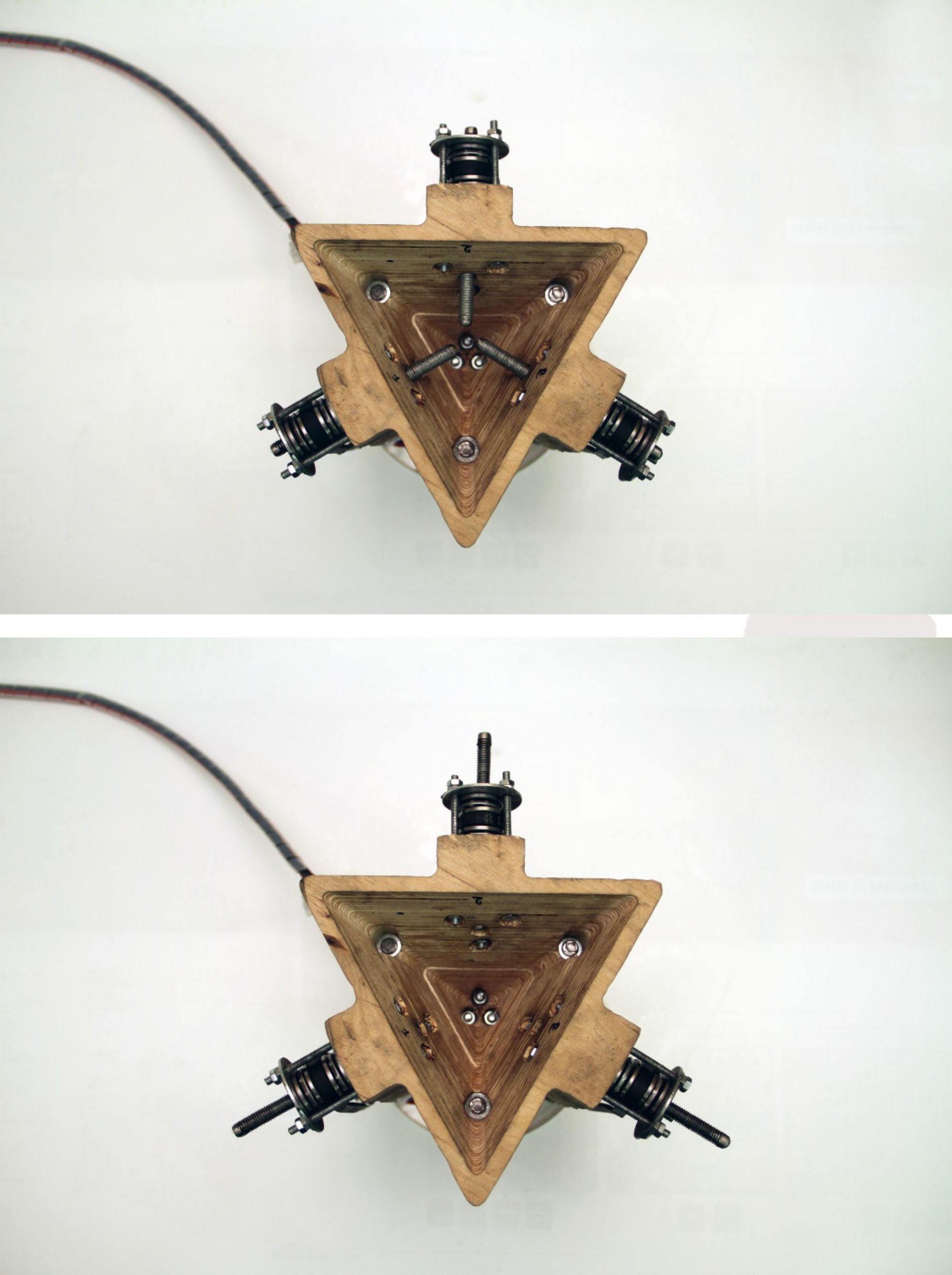

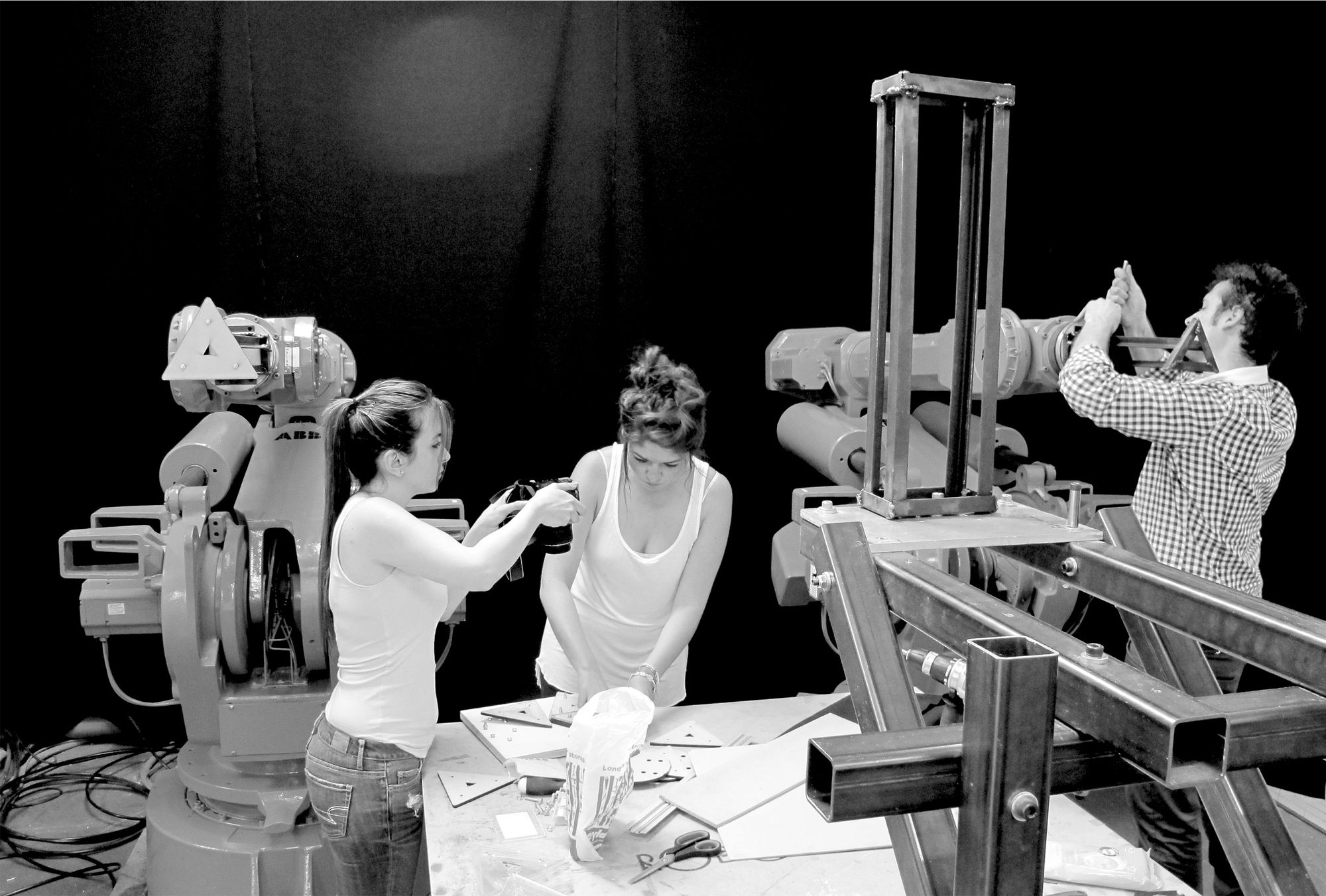
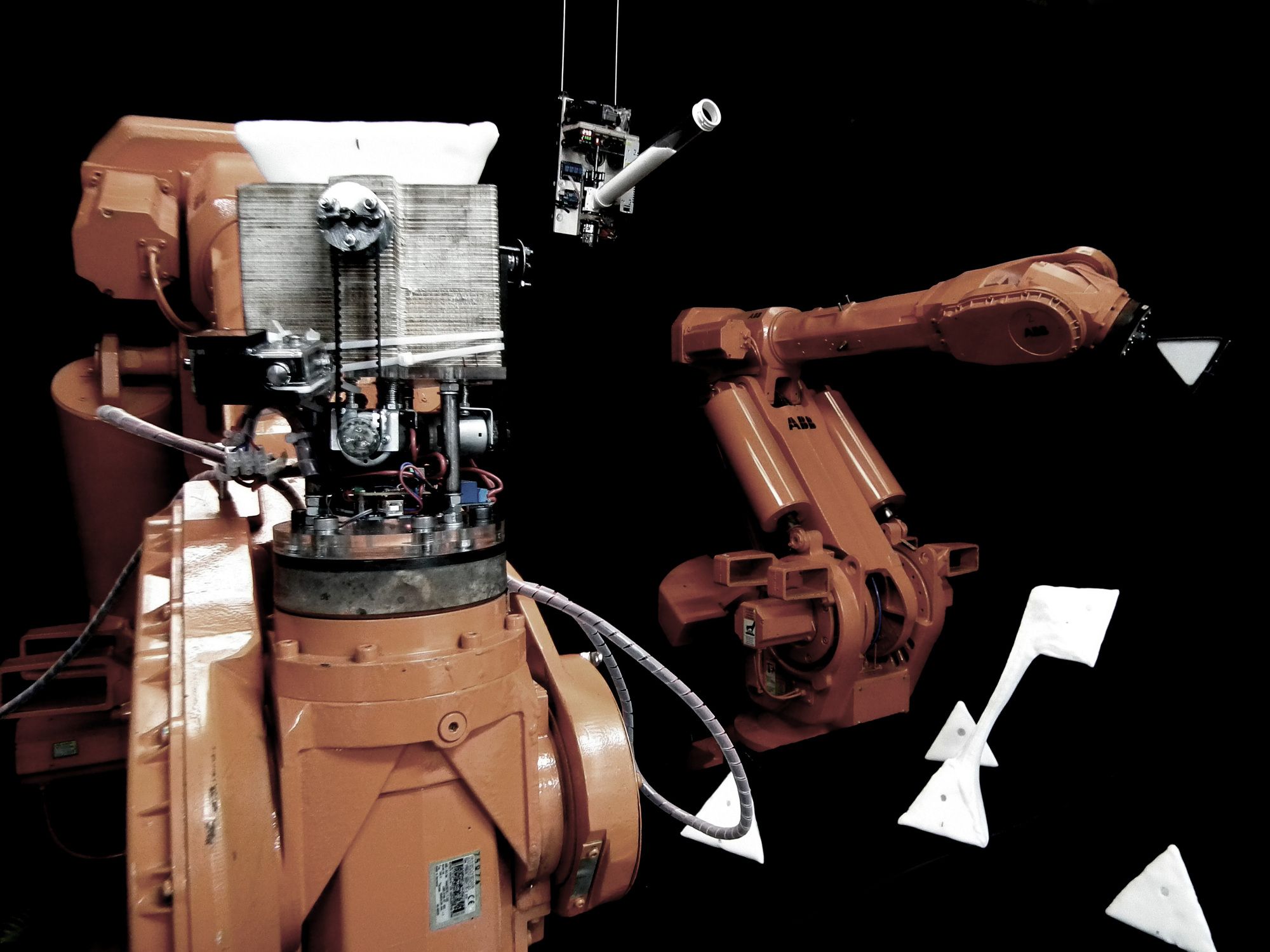
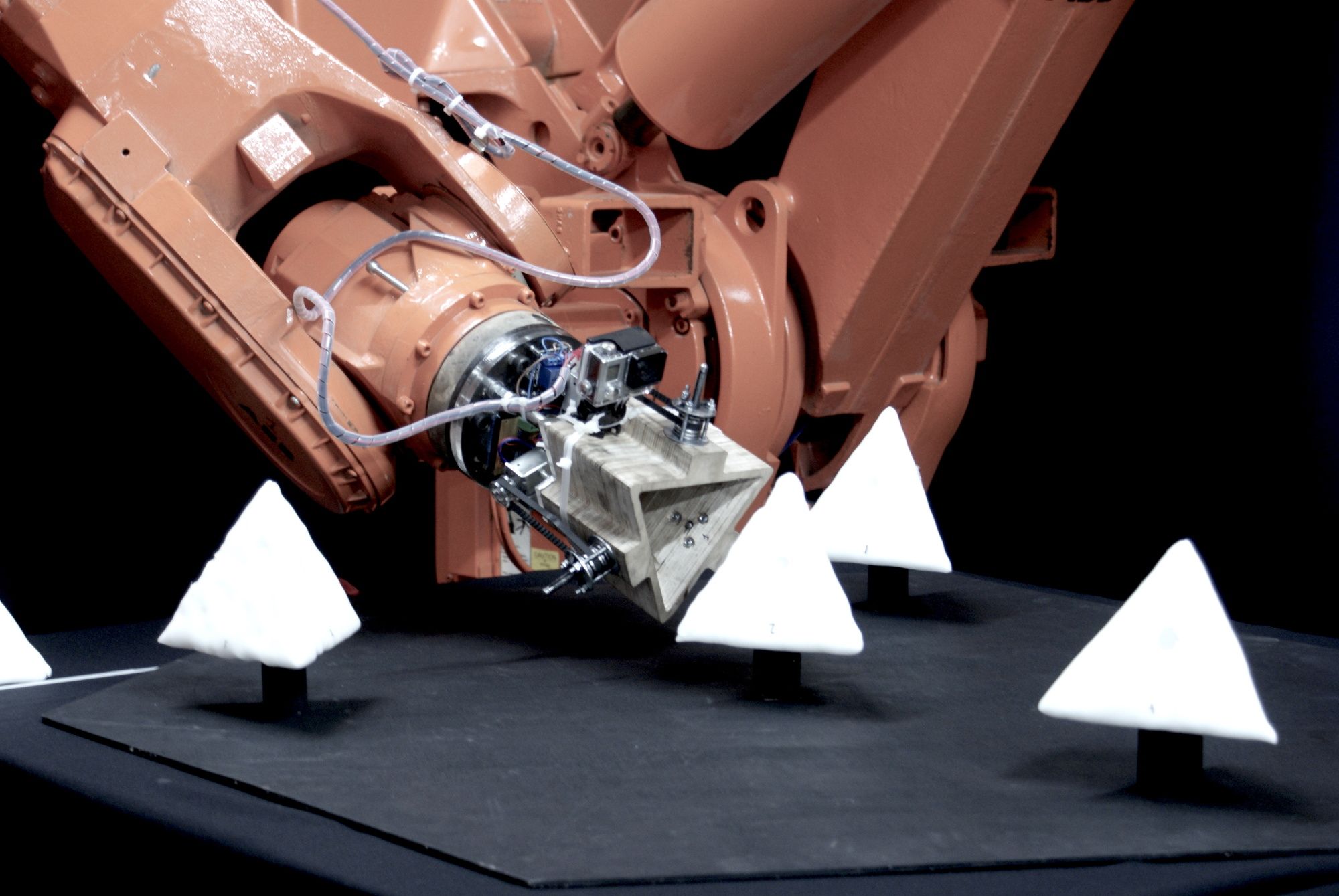
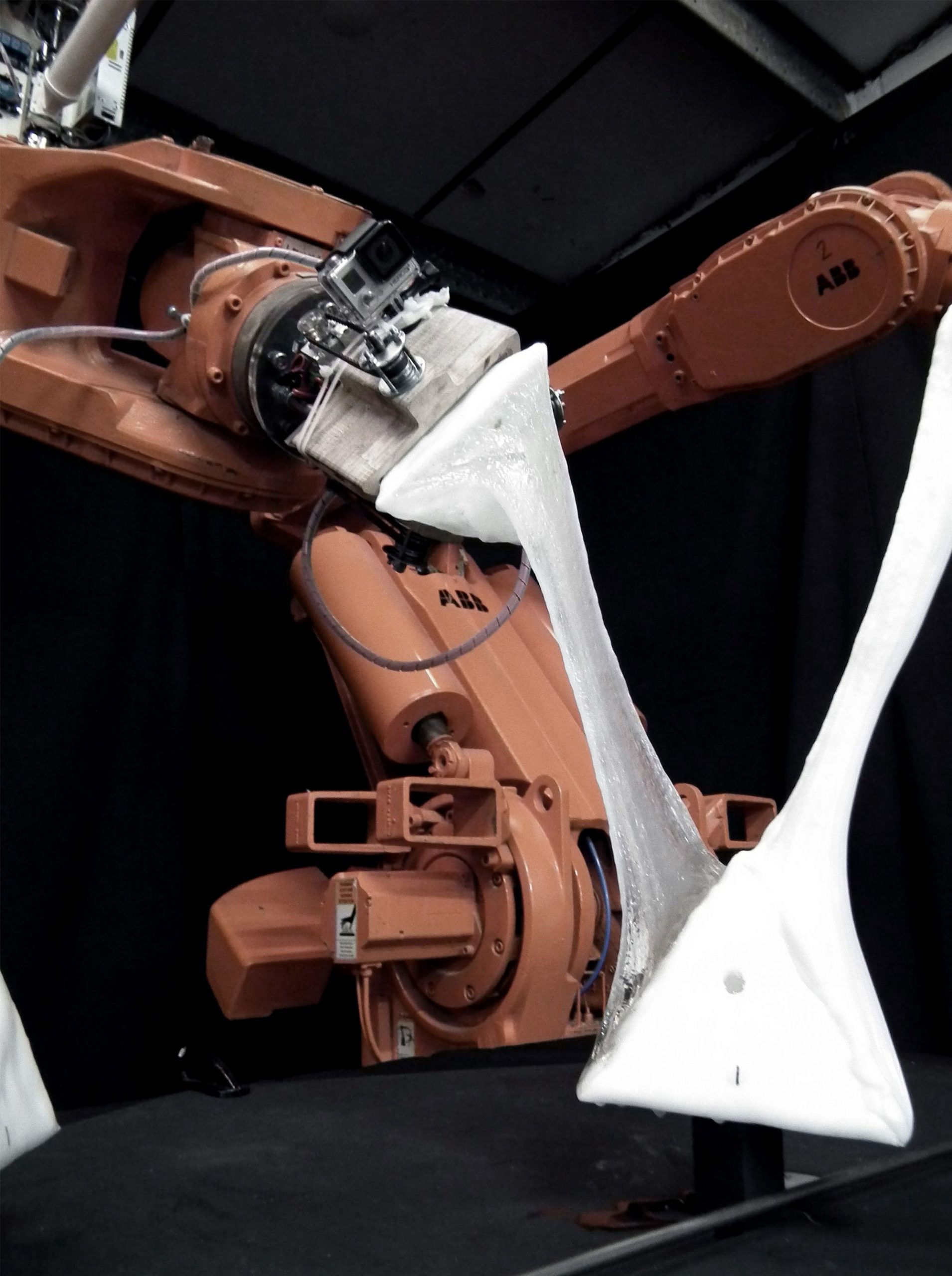
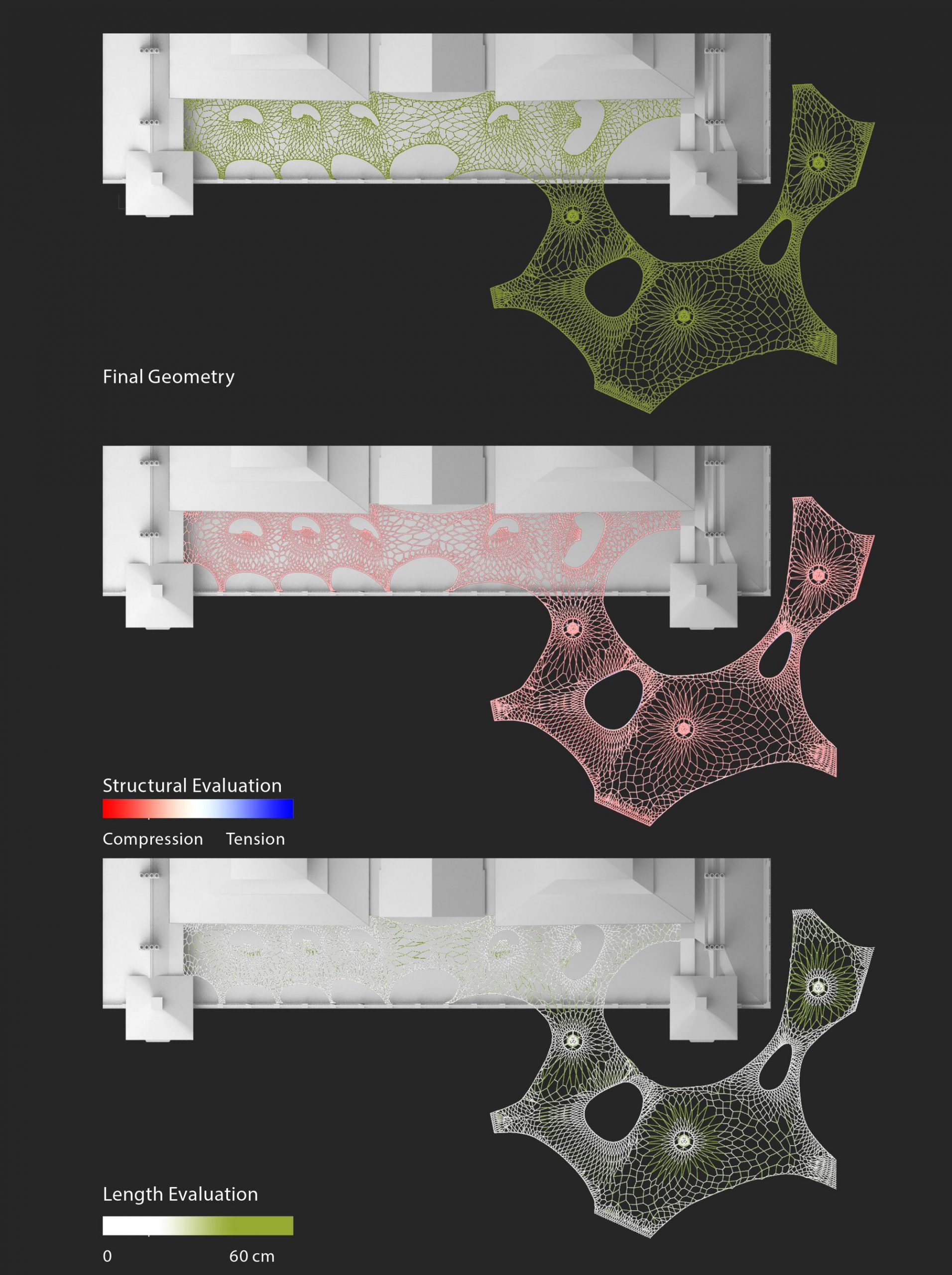
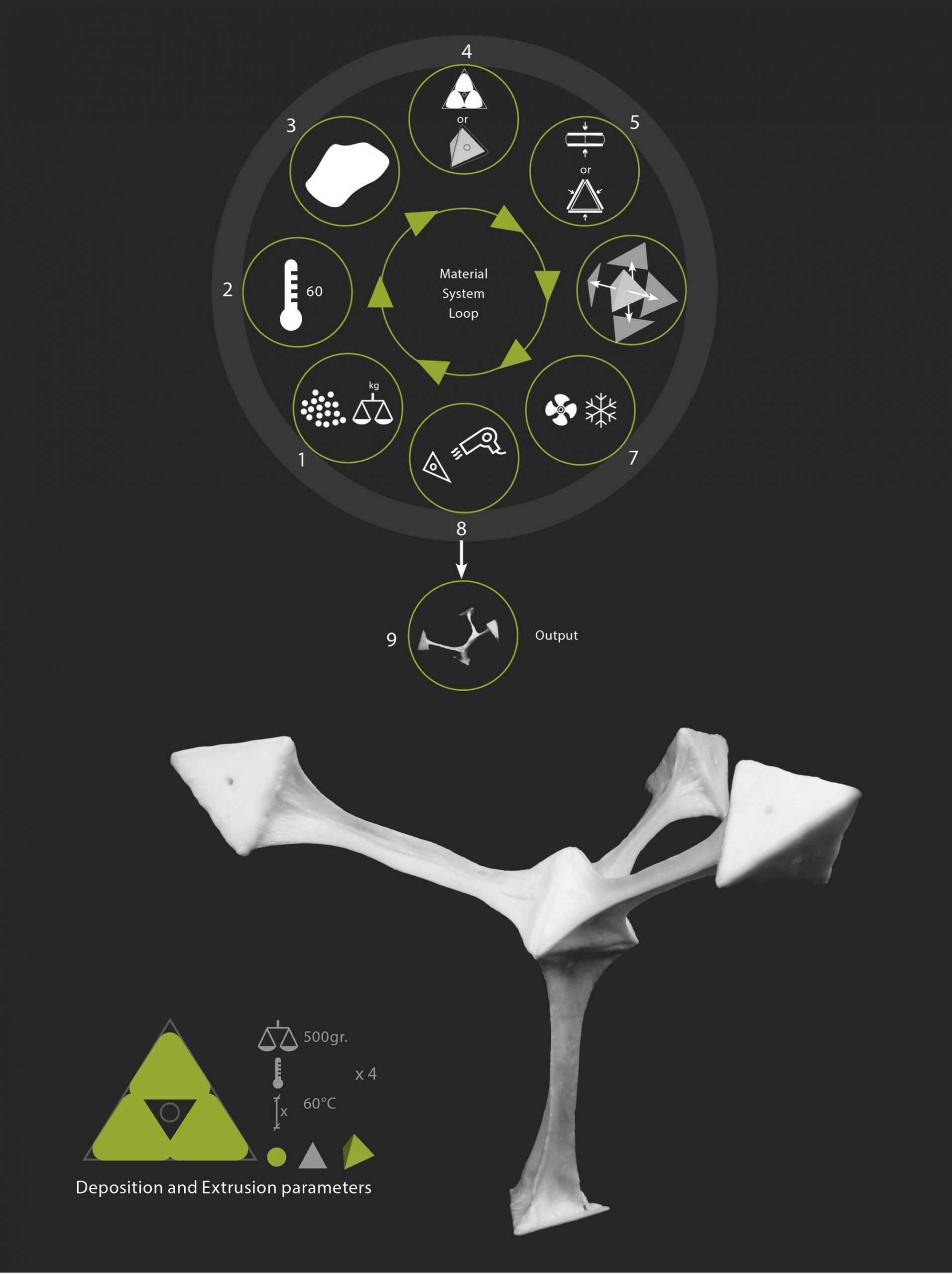
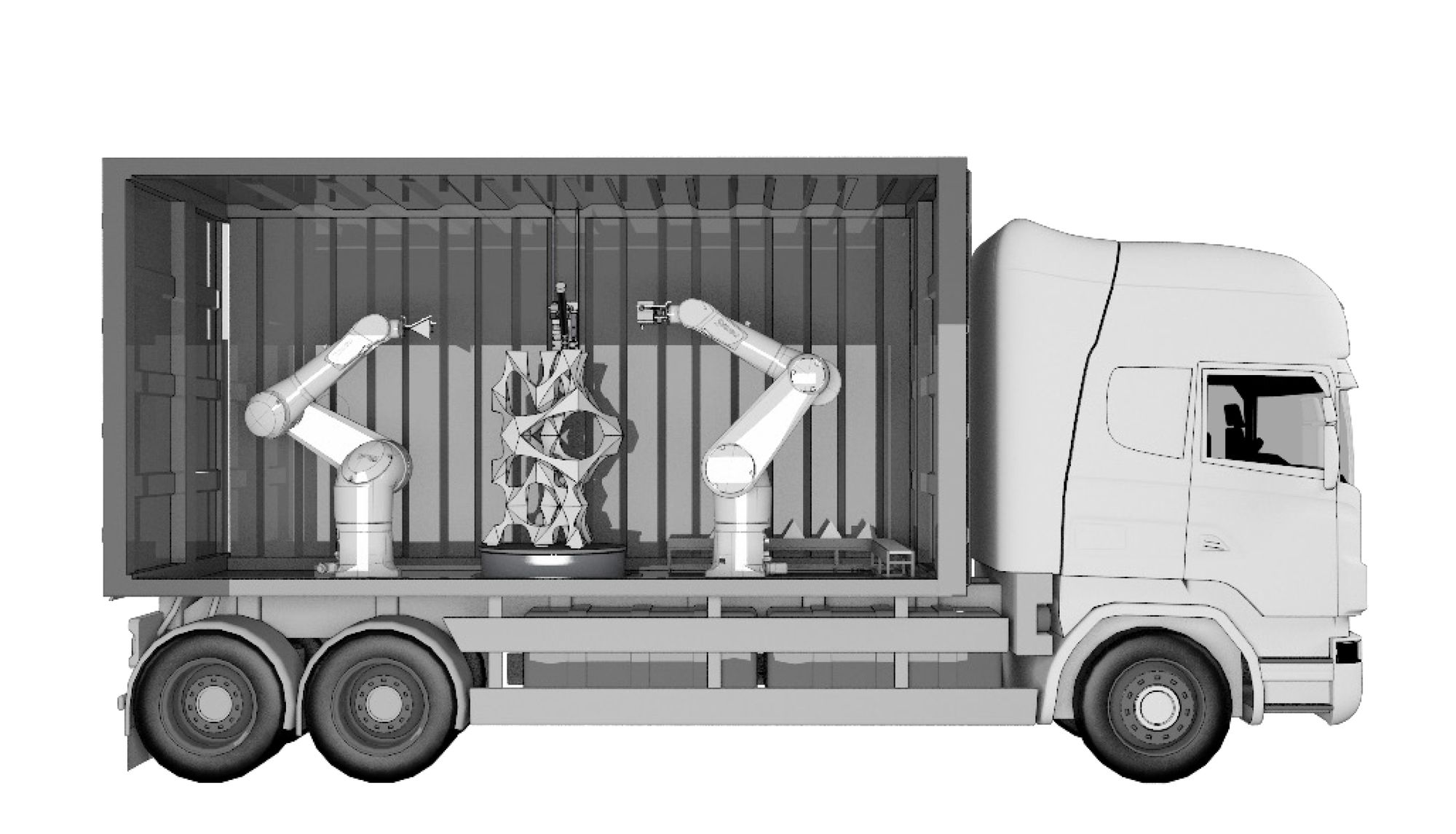
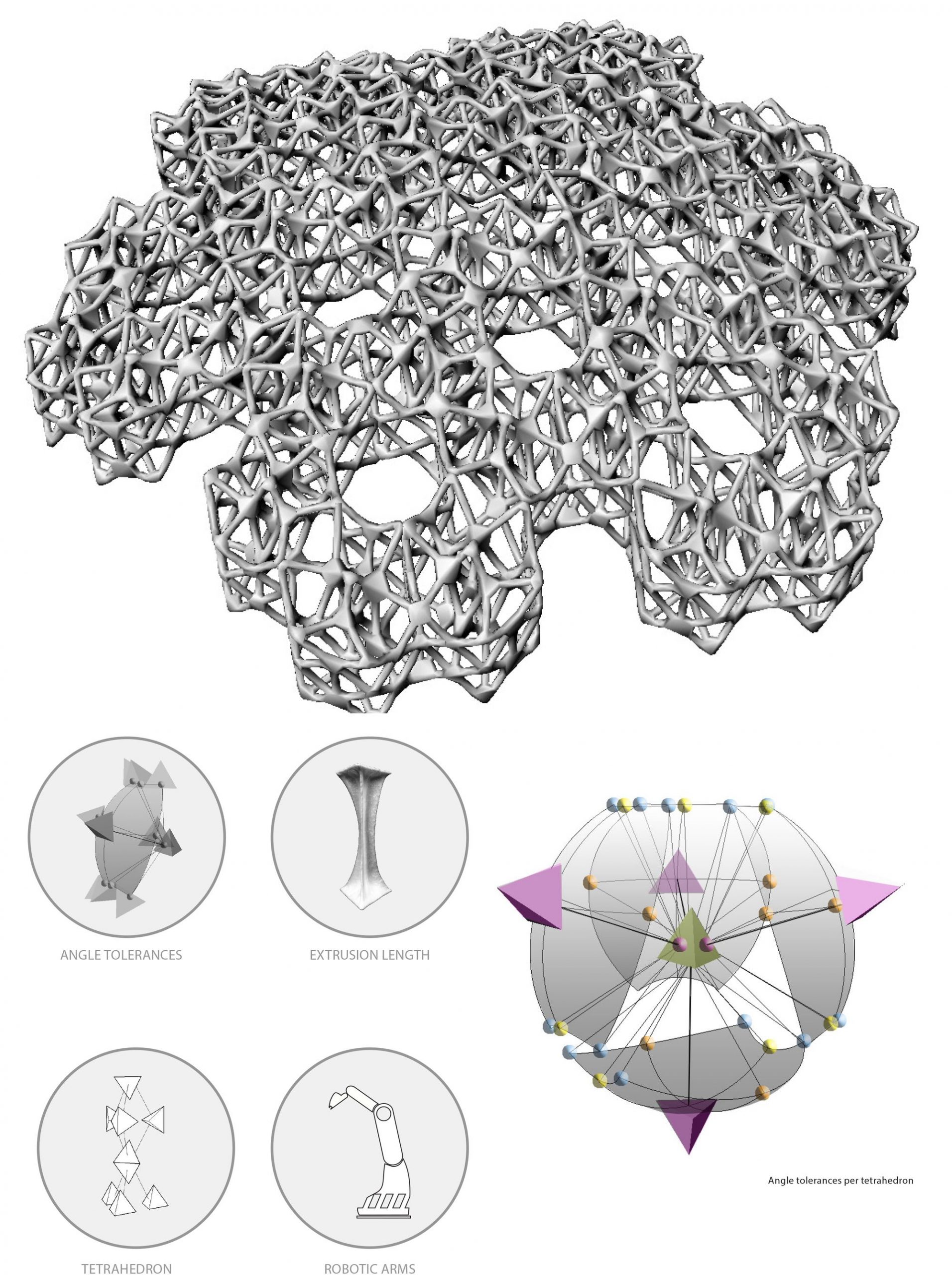
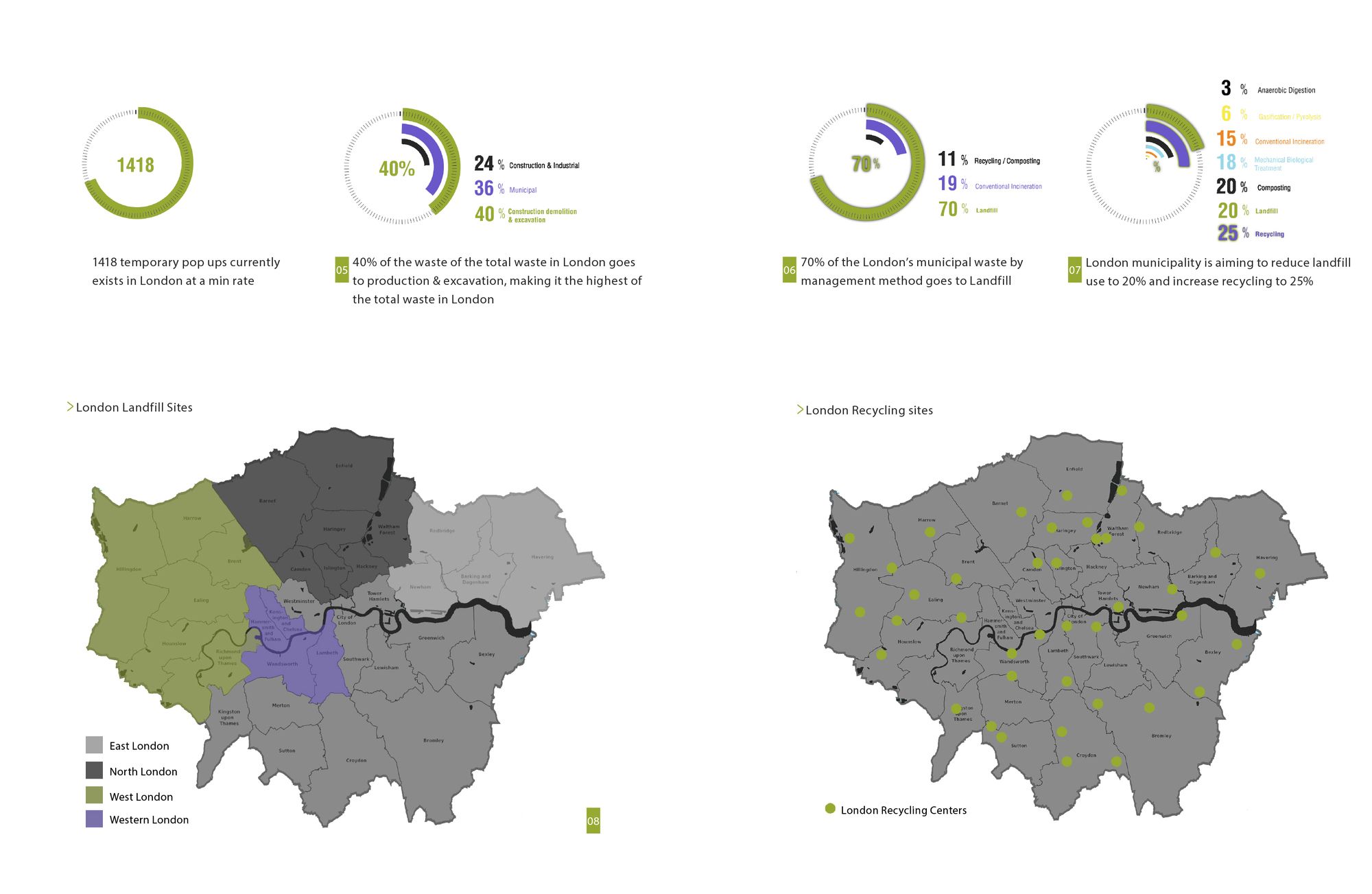