The canopy design starts with the basic functional criteria of a canopy: to provide a shade (the site is covered with an existing canopy that stops rain water), a flat folded surface is made to fit in the volume constraint of 3M x 3M x 6M. After a series of adjustment of the form, the base surface is shaped into a dynamic appearance that offers a shaded area and a seating bench underneath.
Within the dynamic form, curvature varies across the surface; such a curvature variation provides a basic input for the propagated component to create differentiated openings. Several steps of optimization have been taken to subdivide the surface: by looking for a balanced point between the most dynamic grid which result in drastic variation in the shape/size of grid cells and the most identical grid cells’ shape that breaks the grid continuity at some high-curvature area, an orthogonal surface gird is finally chosen to generate a hexagonal array of panels. Extensive panels are automatically eliminated when they fall out of the surface domain.
In the first deployment of the hexagonal panels, panels are doubly curved in most area of the surface, and in between panels lack any openings. Considering the available panel fabrication technique and material are laser-cut plywood, it is essential to ensure that all the panels are flat, and the gradient openings should be intelligently designed while propagating the panels on curved surface.
After optimize the propagation strategy, all hexagonal panels are flattened by projection in a manner so as to keep 3 points constrained to their original location, and projecting the other 3 to a flat plane. This provides a method to constrain the hexagonal panels at 3 of its 6 vertices, while freeing up the other 3 to produce openings where the surface curvature becomes radical. A second stream of triangular holes on the panels is deployed where the panels are very large.
A steel cable mesh is designed as an intermediate support structure between the primary frame and the hexagonal panels. A customized a joint is designed to fix the panels on the cable meshes, while it also gives enough flexibility between panels to absorb the construction tolerance and natural deformation due to gravity.
The joint is made from using off-the-shelf parts like cable clamps and bolts and custom fabricated parts like 9mm MDF spacer and a 0.4m stainless steel plate with 3 slots. The slots cut out from the plywood panels align perpendicularly to the slot on the stainless steel plate. When combined with the flexibility of the panel itself, they provide a joint that is flexible and manipulatable in 3 axes.
A 40x40mm L-section steel frame is anchored to the wall, then a grid of laser-cut plywood sections is secured to the steel frame, to where the steel cable mesh attached. At last the overall field of hexagonal panels are fixed to the cable mesh via the customized joints.Given the flexibility from the joints, all hexagonal panels adjust themselves into final position by gravity.
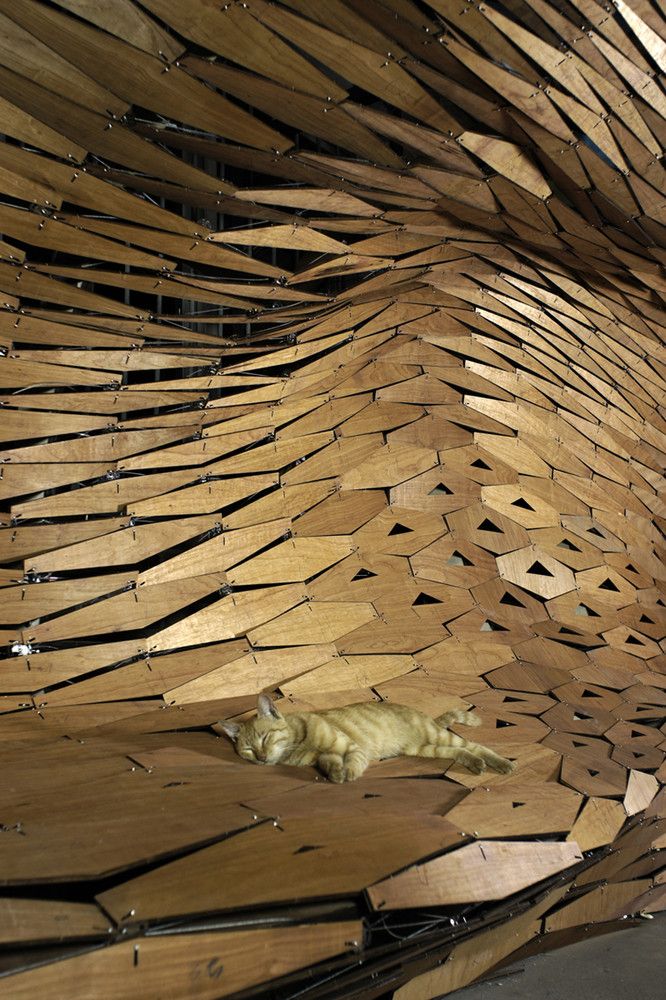
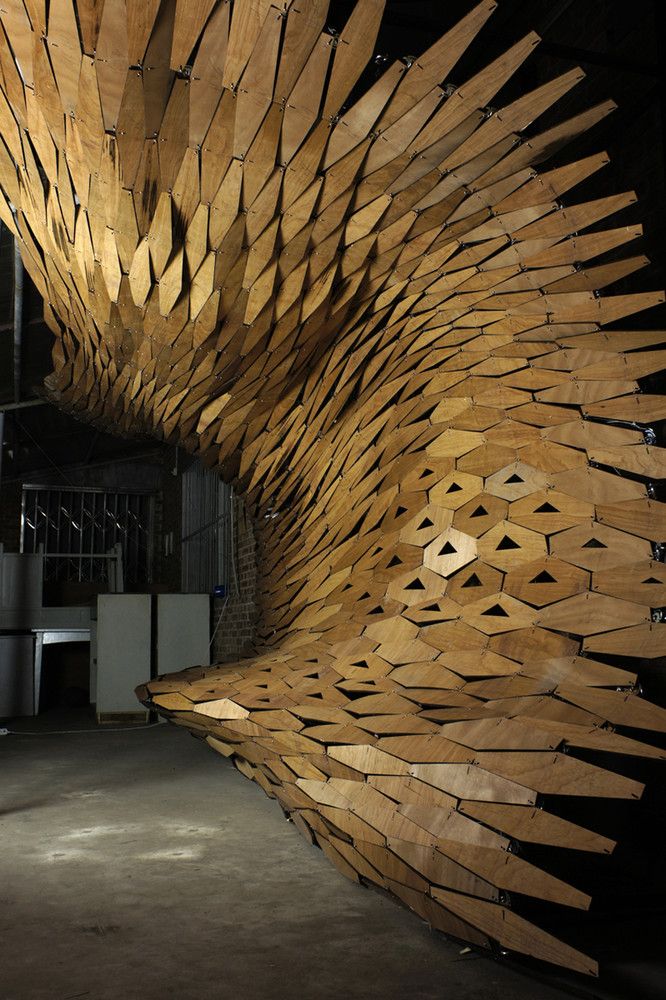
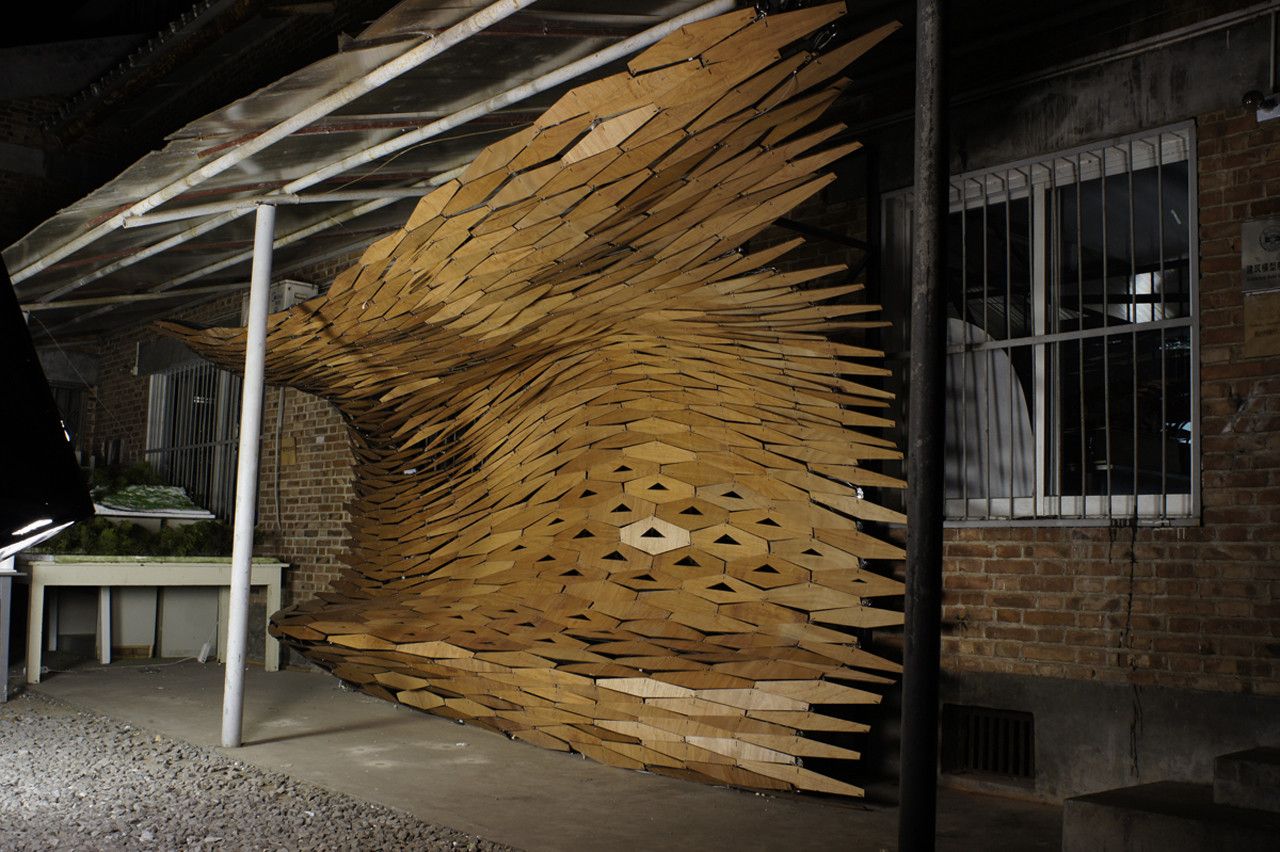
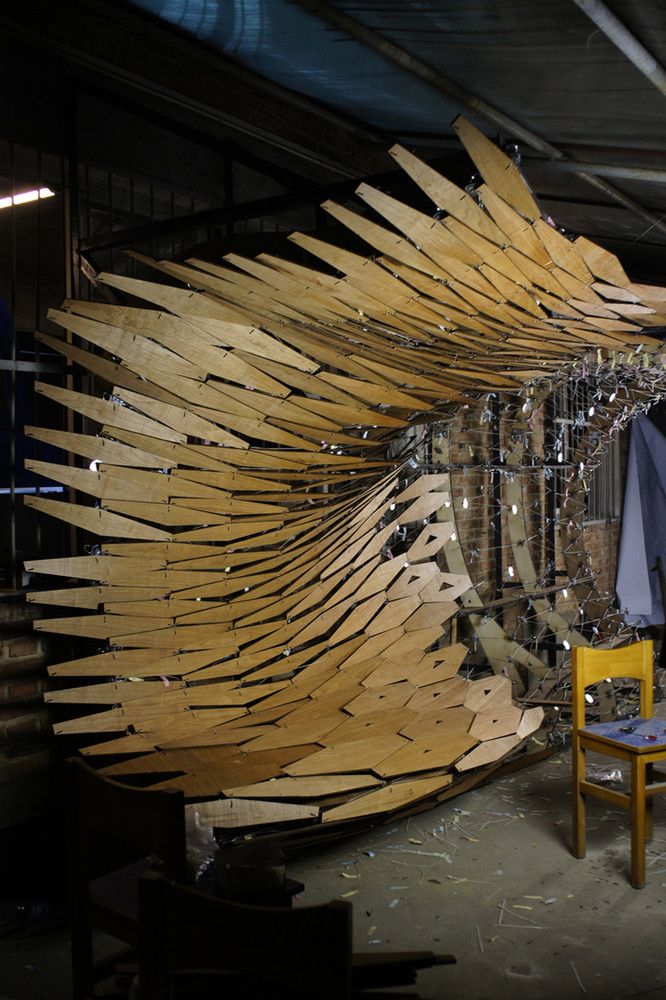
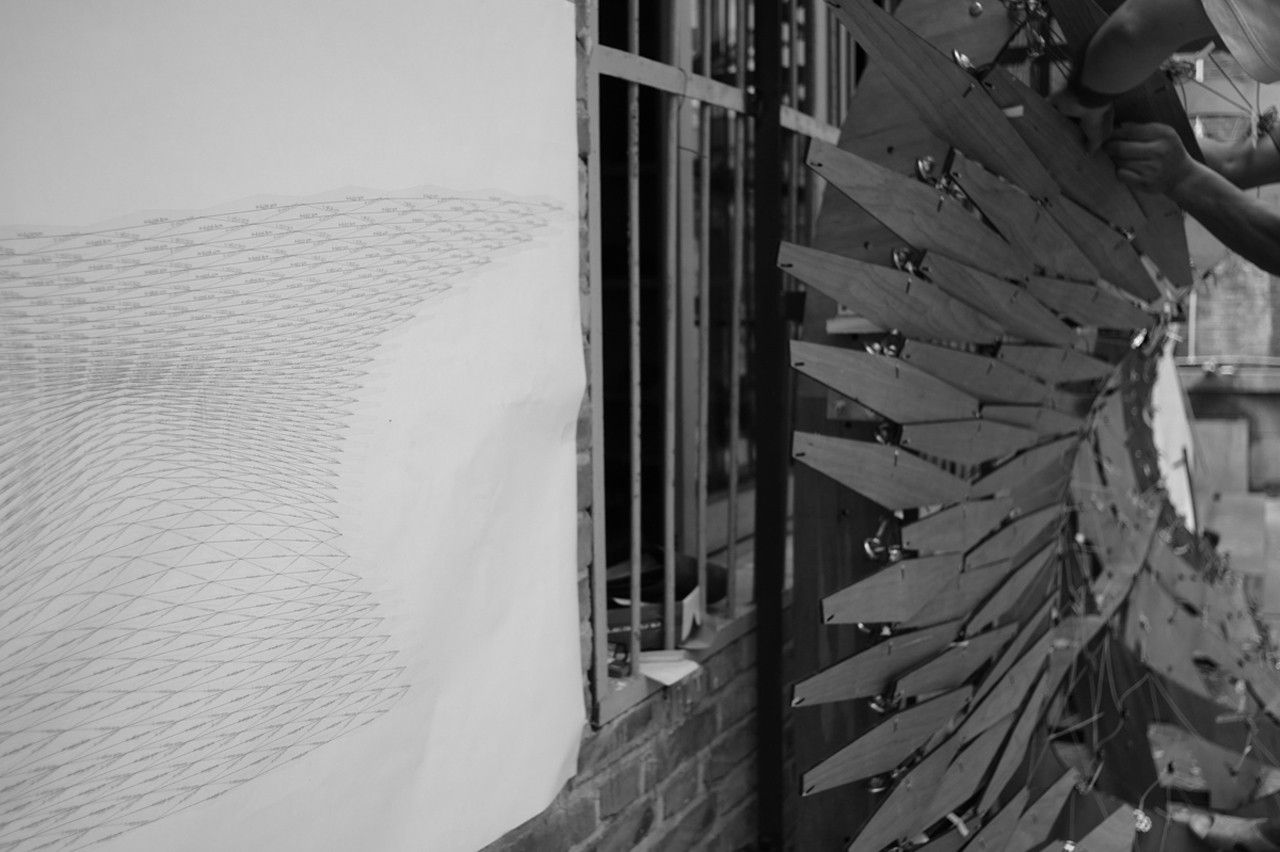
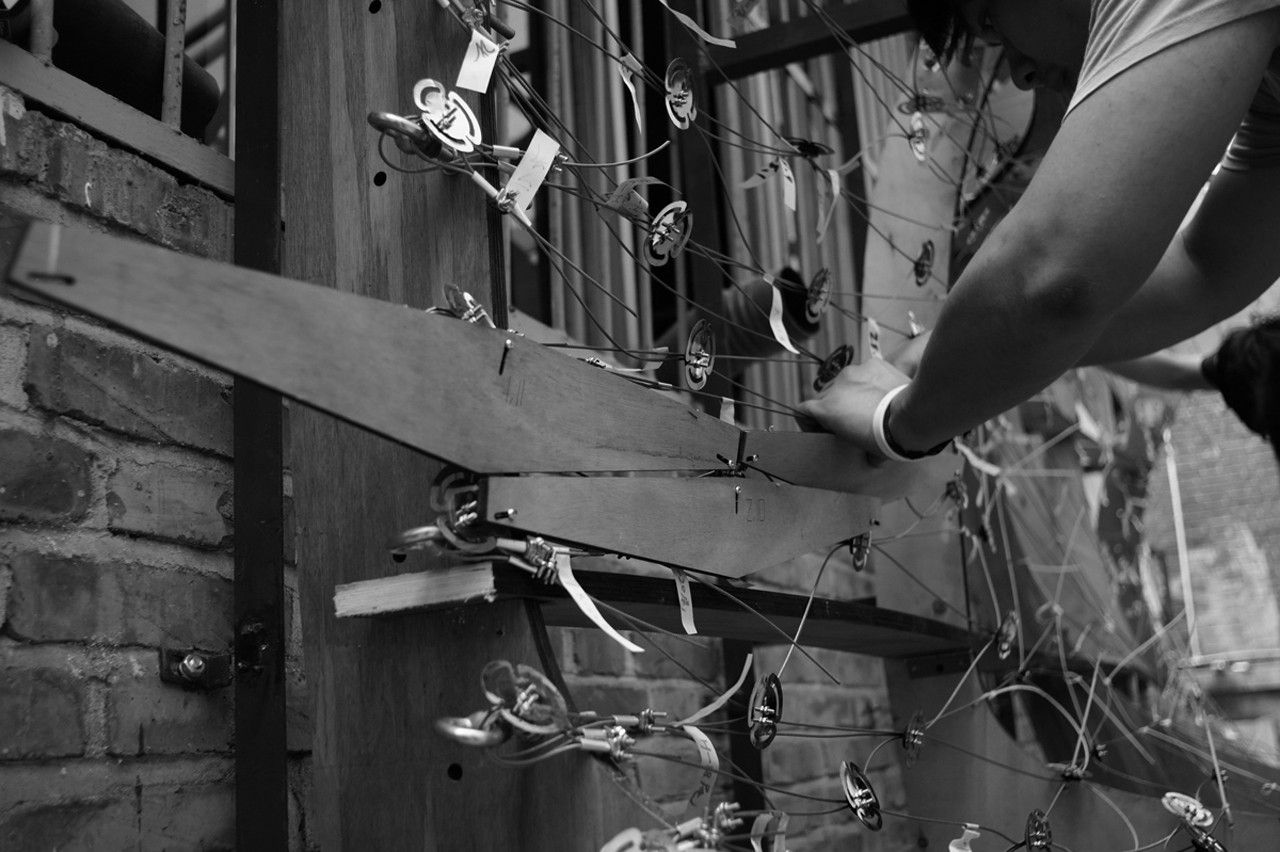
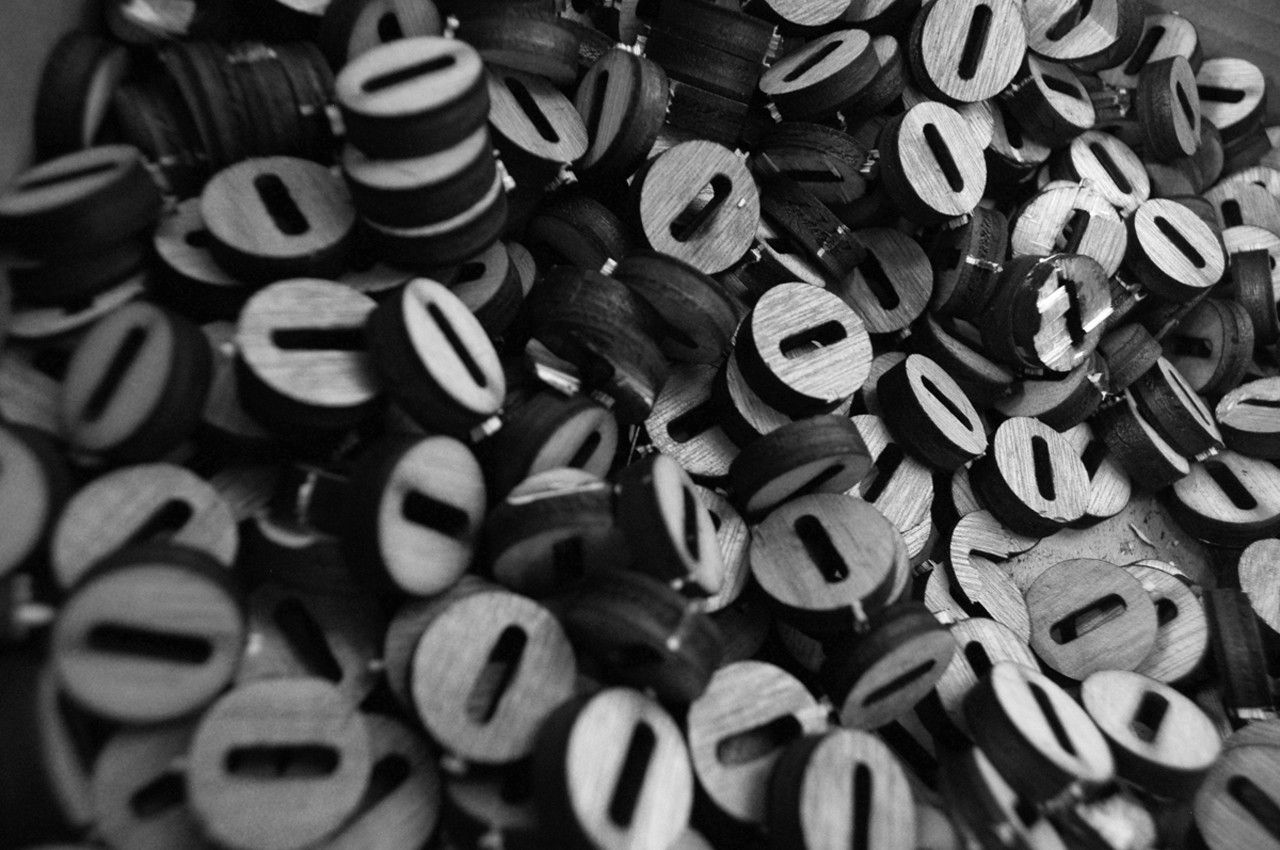
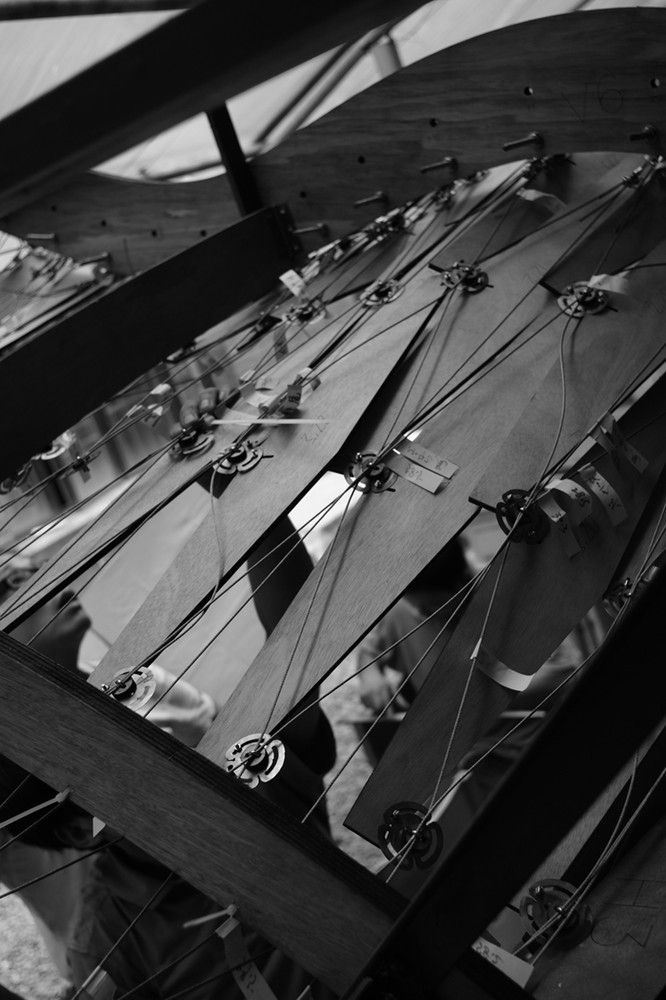

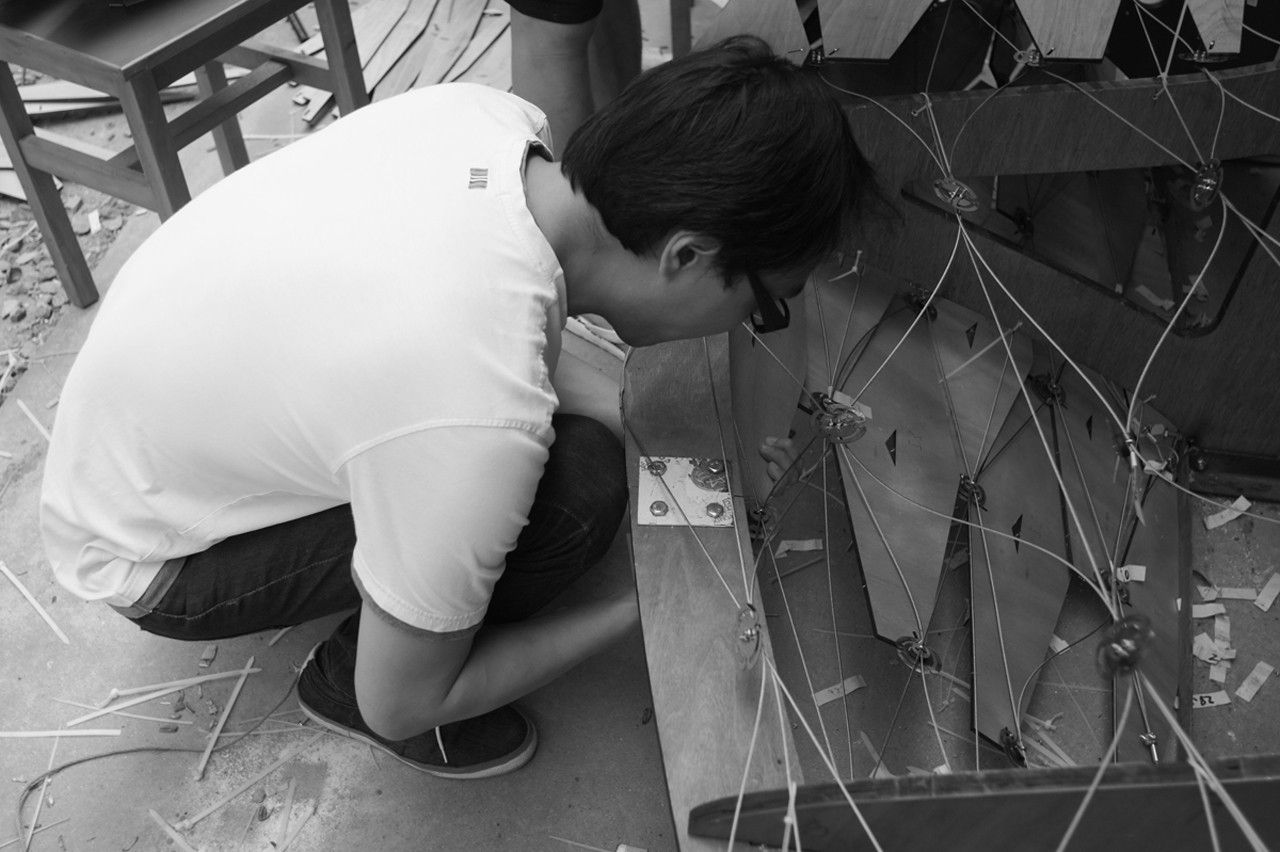
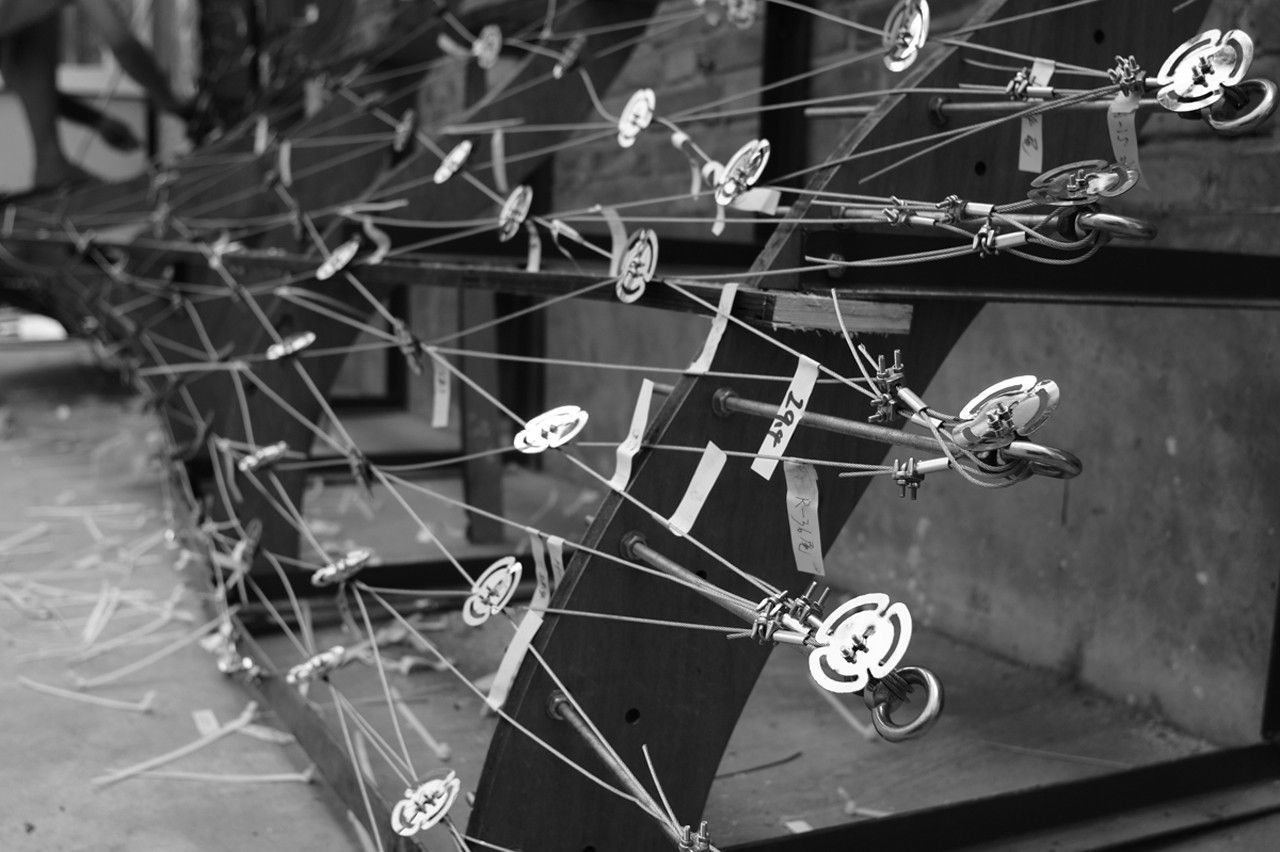

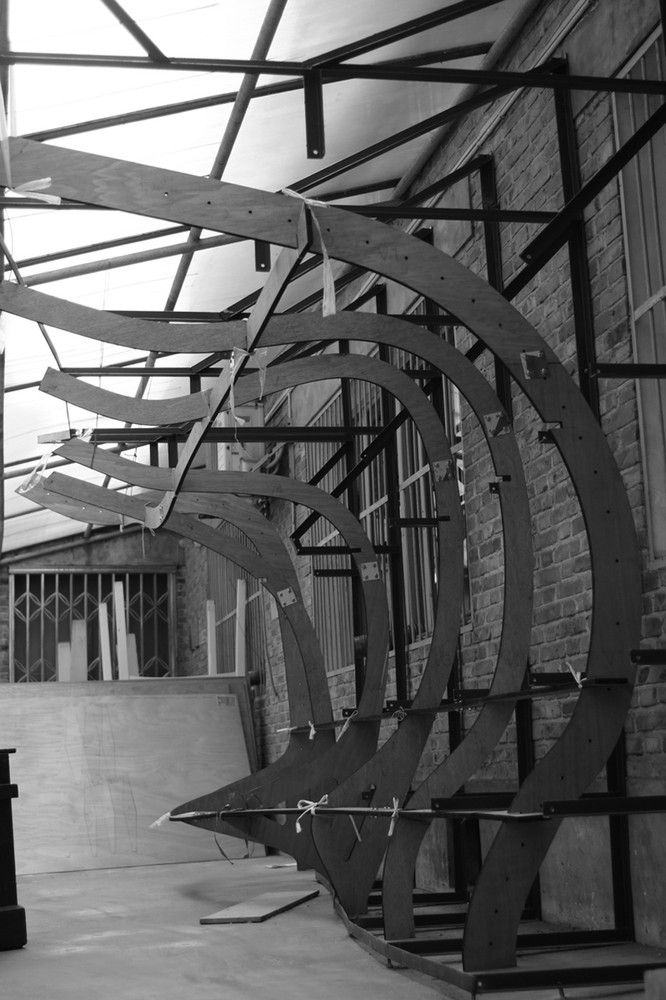
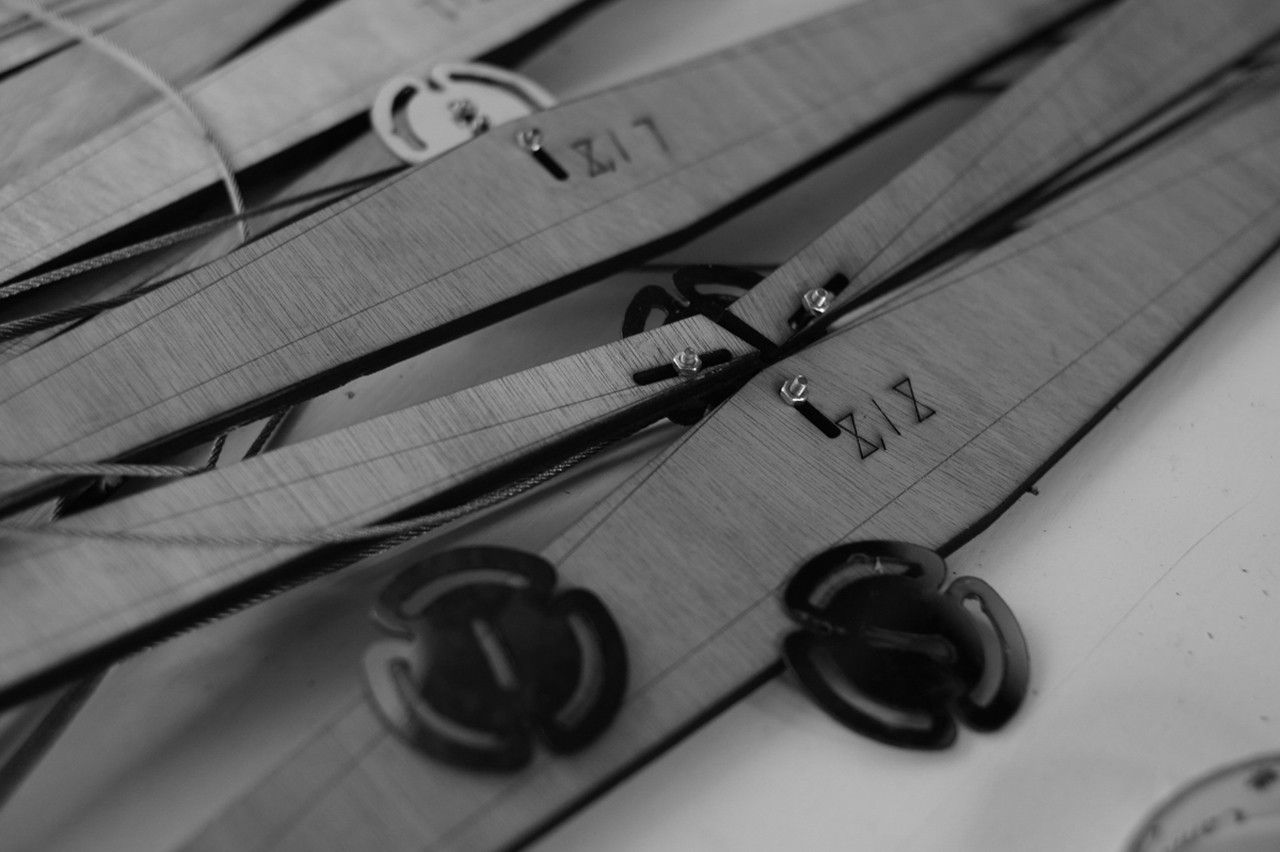

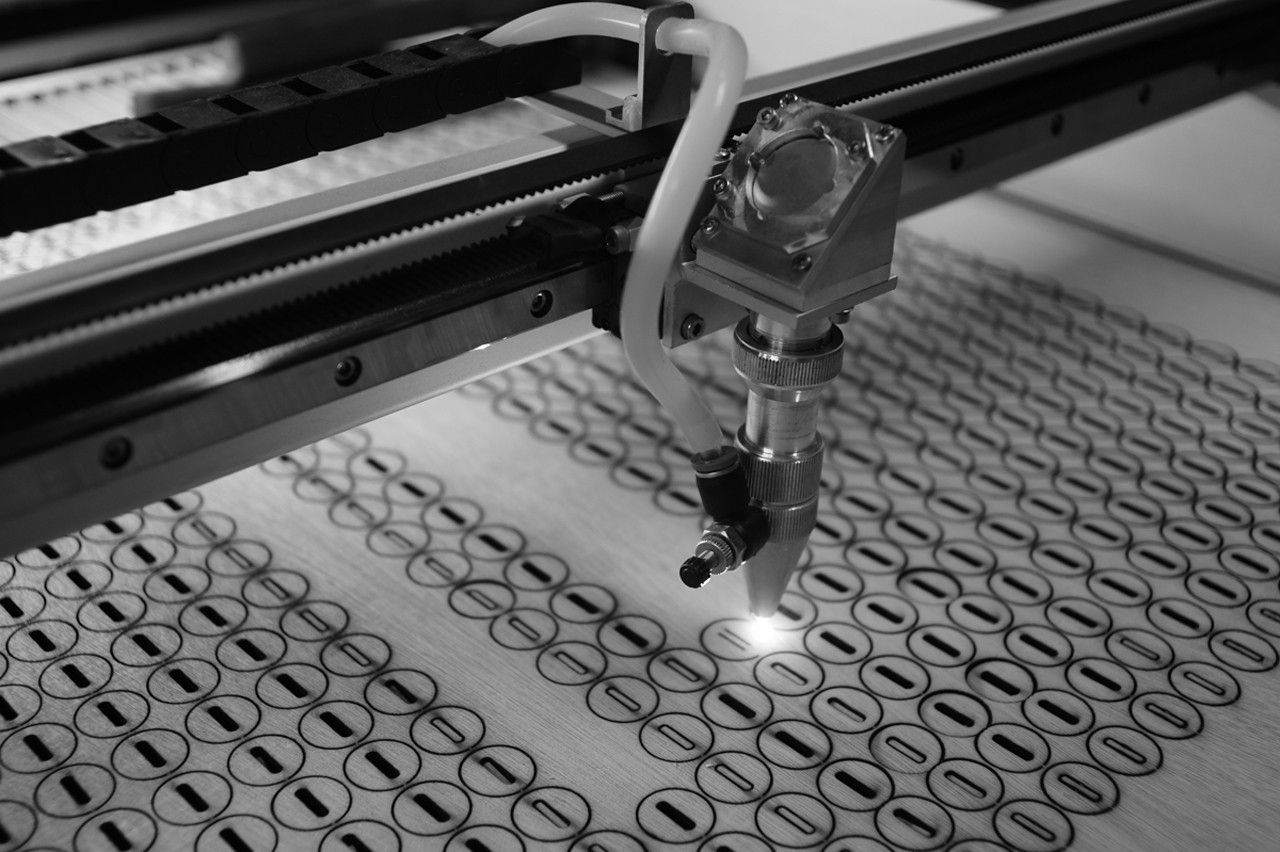

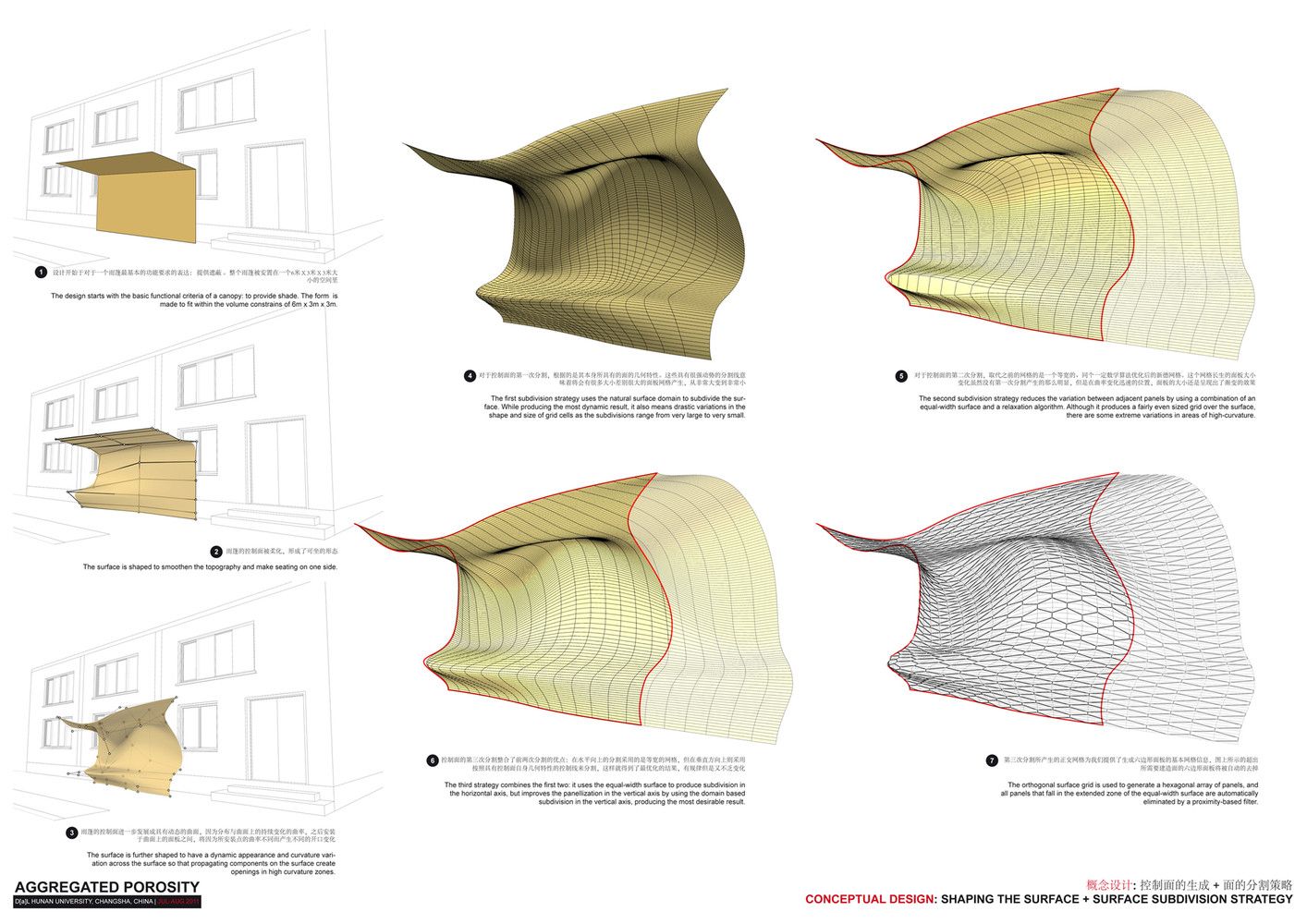
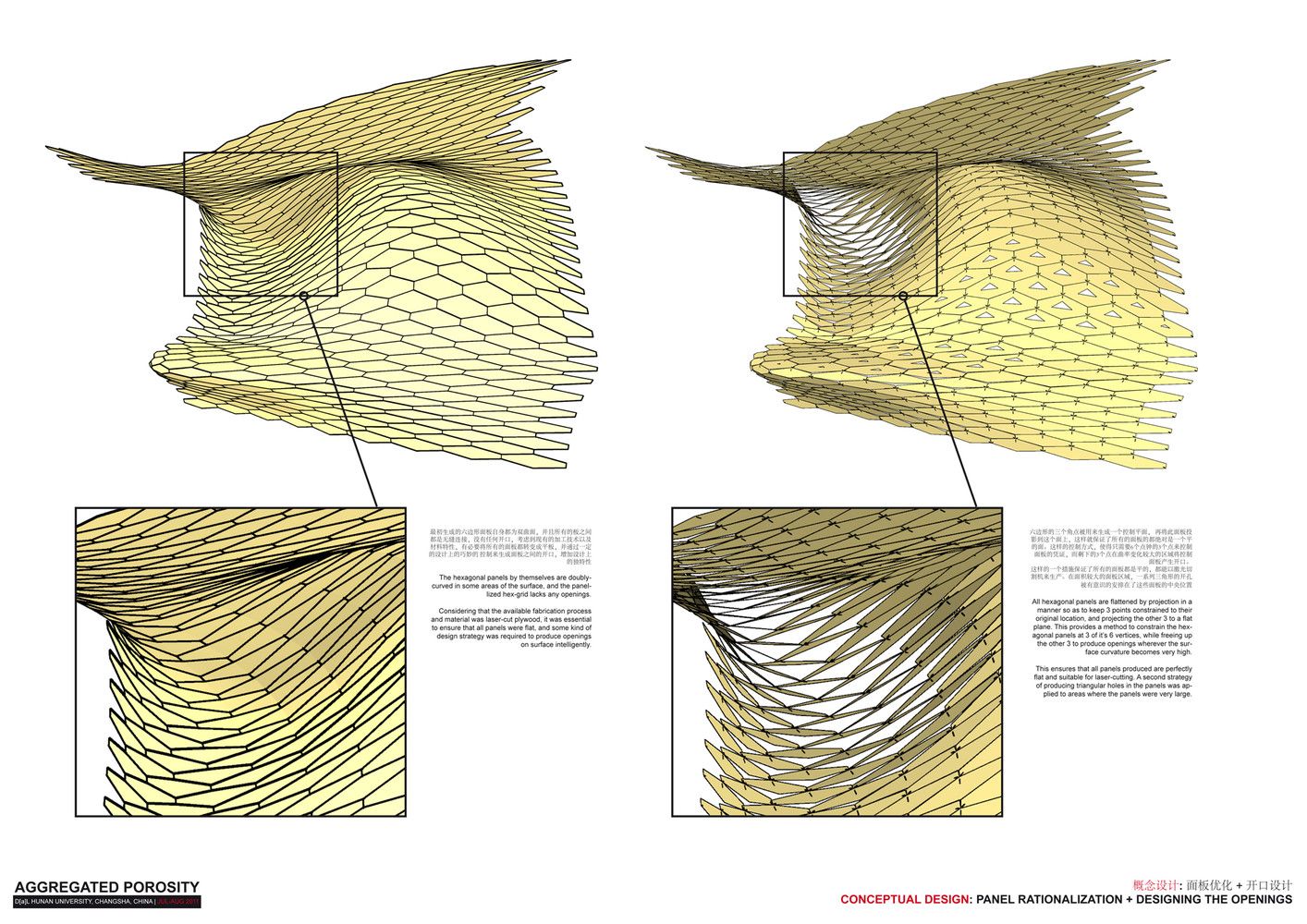
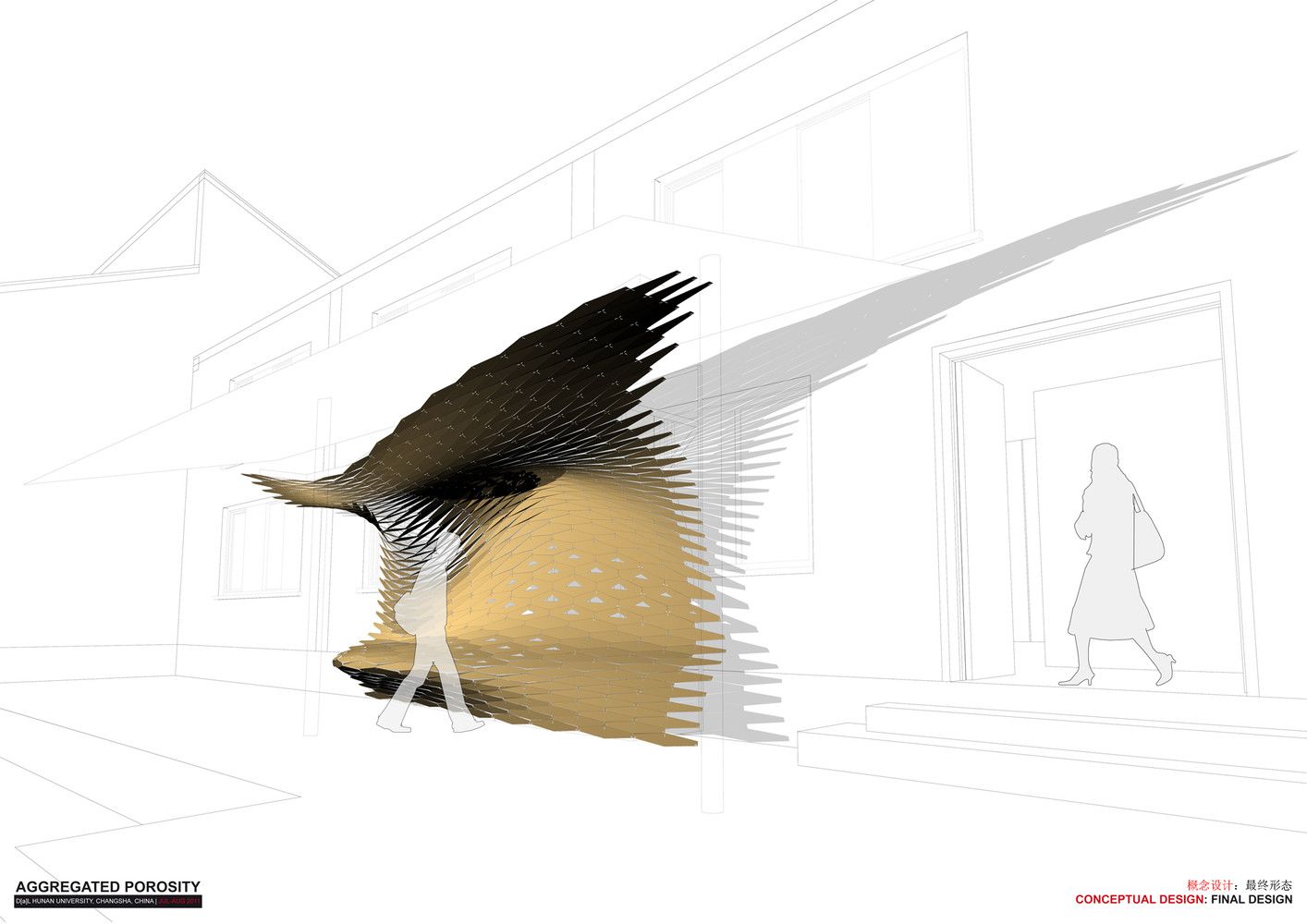


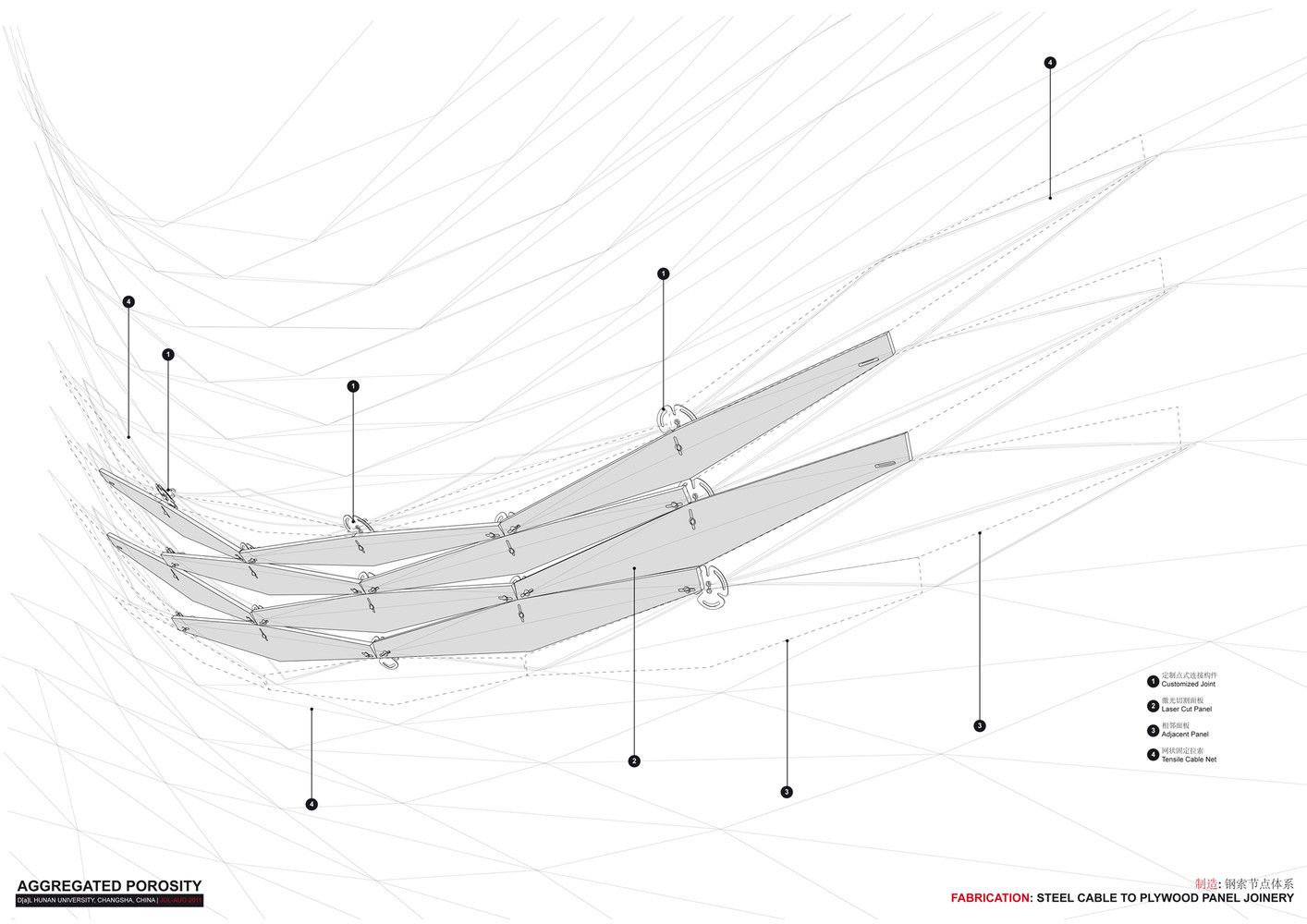
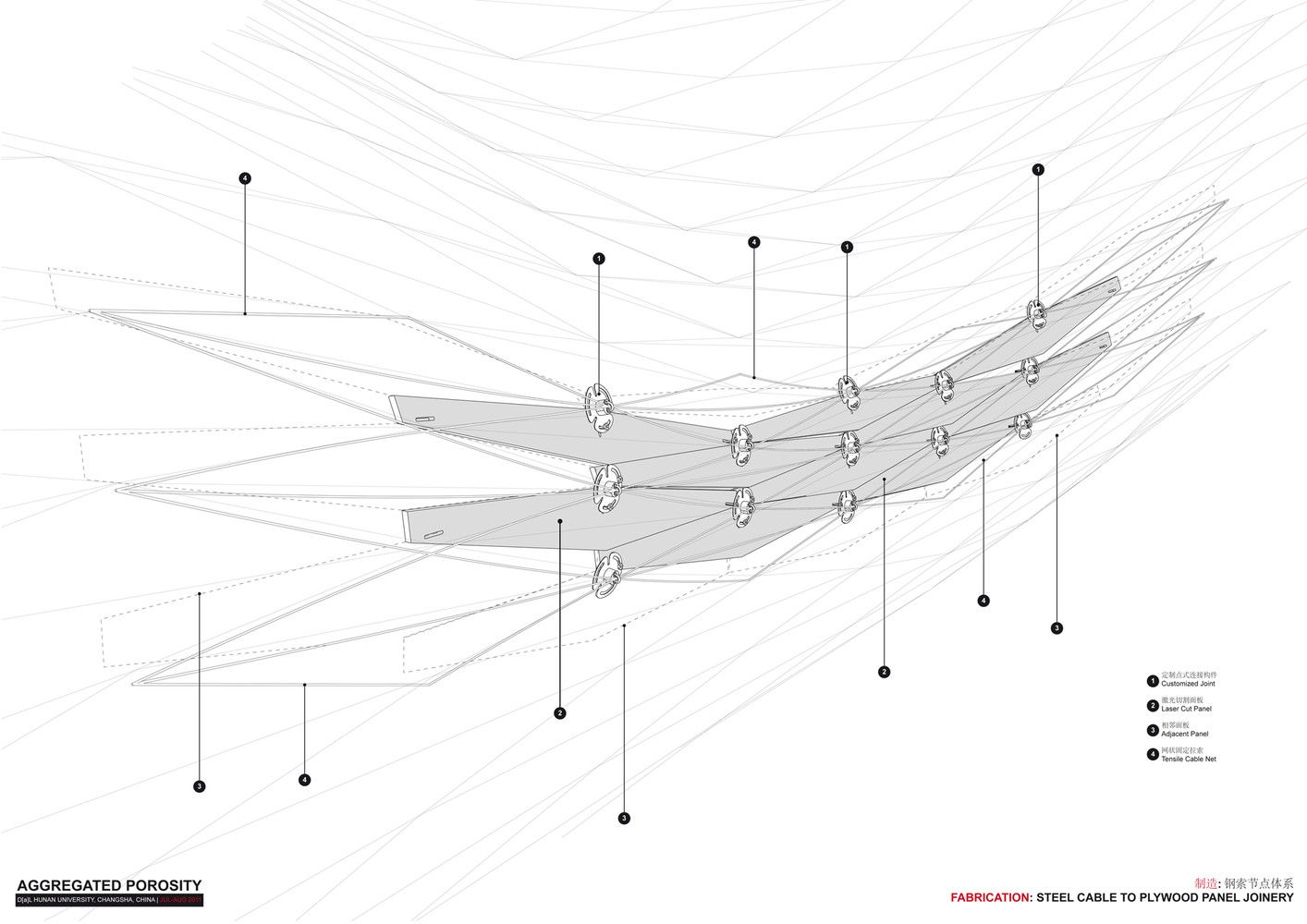
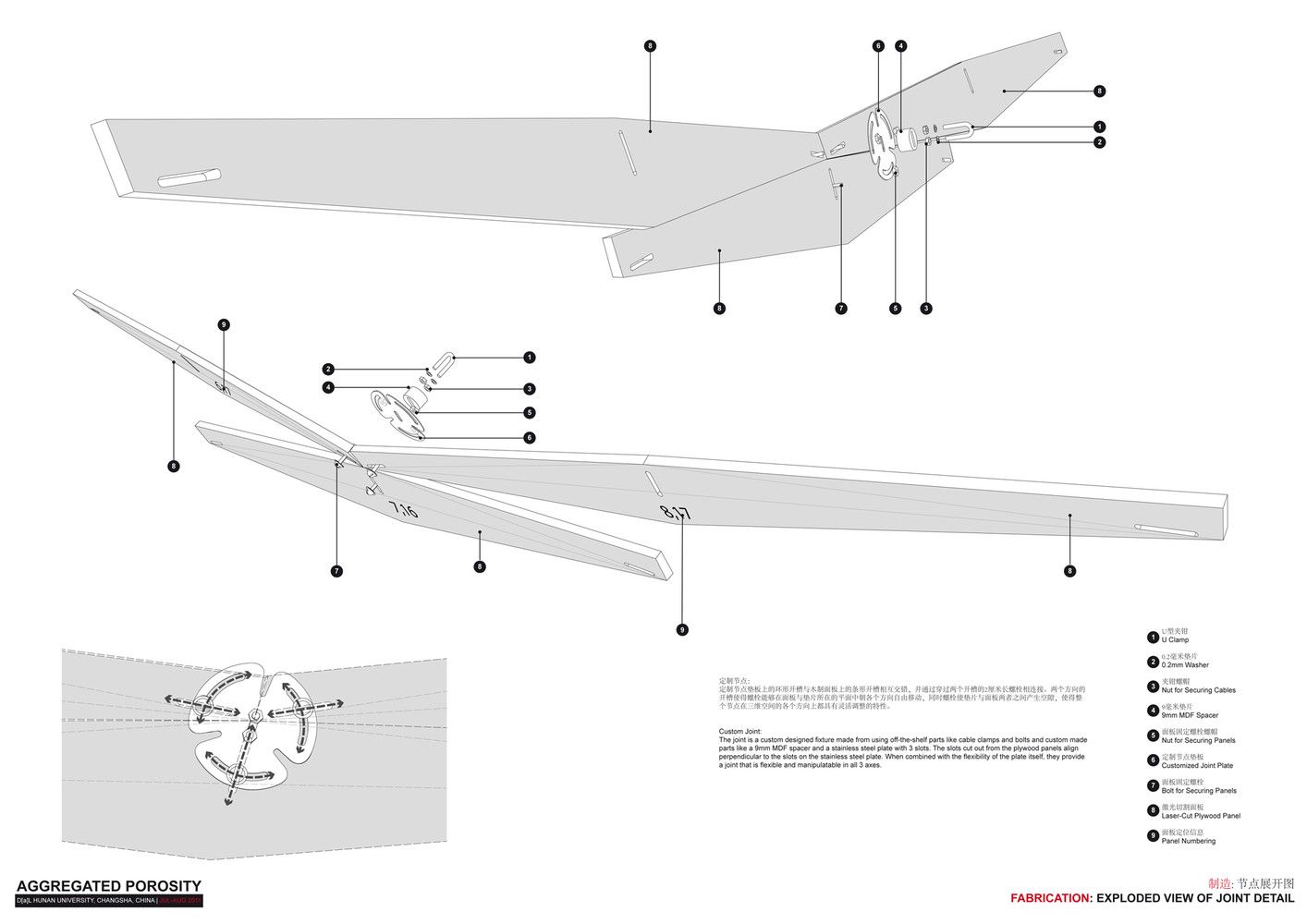
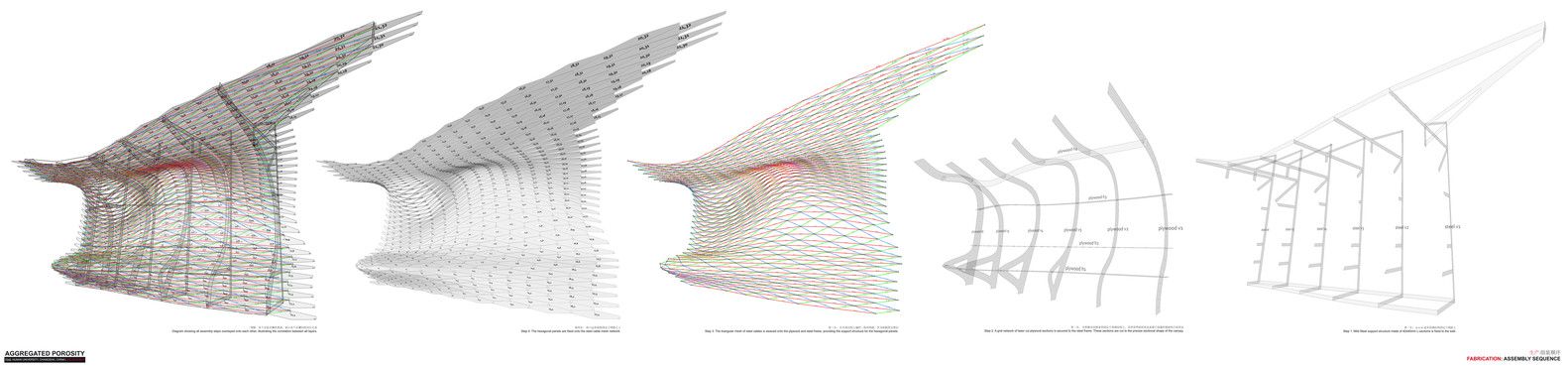