PAV’14 was constructed as the final project in the AENG473 course -Introduction to digital design and fabrication, at The American University in Cairo. During the semester, students were introduced to principles of digital design and fabrication and provided with technical tutorials in Rhino, Grasshopper and how to manufacture their model using a 3 axis CNC machine.
The class tutors run a n internal competition between the students to select a winning design that will be manufactured. The students were divided into groups and were asked to design a pavilion within a certain volume, utilizing what they have acquired in knowledge and skills about both subjects, taking into consideration structural integrity, connections, volume limitation and material performance. In this competition, 15 proposals were presented throughout the semester. The choice of the winning proposal took into consideration -beside the previous points, aesthetics and complexity of the form as well as the ability of fabricating it using the available tools – a 3-axis CNC machine.
The winning proposal, PAV’14, was derived from a mobius strip and in order to optimize the design for fabrication sectioning was used. Sectioning is considered one of many fabrication techniques that uses a series of profiles, the edges of which follow lines of surface geometry. The modeling software (Rhino 5 + Grasshopper) can almost instantaneously cut parallel sections through objects at designated intervals.
Before settling for that output some optimization was made to the form, manually making sure to provide sufficient resting area on the ground and also automating thickness optimization for the whole structure according to calculated stresses -for this Millipede for Grasshopper was used, this helped with the structure performance of the pavilion and also minimized the amount of material used. From the optimized mesh a surface was extracted which was used then in the sectioning operation, resulting supposedly in the final pieces to be fabricated.
Because of the complicated design of the mobuis strip, and before cutting the wooden boards, the team noticed that some of the grooves in the sections were oriented each at a different direction, this would have been very problematic during the assembly. We had to check the direction of each surface to make sure they were all oriented to the same direction this was automated in Grasshopper.
Courtesy of © The American University in Cairo (AUC)
Tutors: Dr Ibrahim Abdelhady, Dr Passaint Massoud, Mohamed Hassan, Omar Samy Roshdy, Sherif Tarabishy
Students: Abdallah El Cherbini, AbdelRahman AbdelTawab, Abdullah Soffar, Ahmed El-Desouky, Ahmed Nour, Allaa Elamrousy, Aya Afify, Caroline Makary, Caroline El-Sibai, Dina El Husseiny, Ghada Ismail, Hania Ghazal, Hemmat Fouad, Mai Mohamed, Mariam Abdel Dayem, Mariam Amer, Marwan Mostafa, Nada Osman, Nadin Mahgoub, Nadine Mekawy, Noha Eissa, Nouran El Begermy, Nouran Mostafa, Nourhan Mohamed, Omar Abdel Kader, Omar Al-Qathab, Omar Othman, Rana El Badawy, Rana Soliman, Saleh Amina, Samar Samir, Sara Wissa, Serageldin Elshatty, Tarek Amr and Toya Afify.
Material: 30*14mm mdf boards
Machining time: 20 hours
Assembly time: 10 hours
Number of elements: 145 unique pieces
Cost: 1400 USD
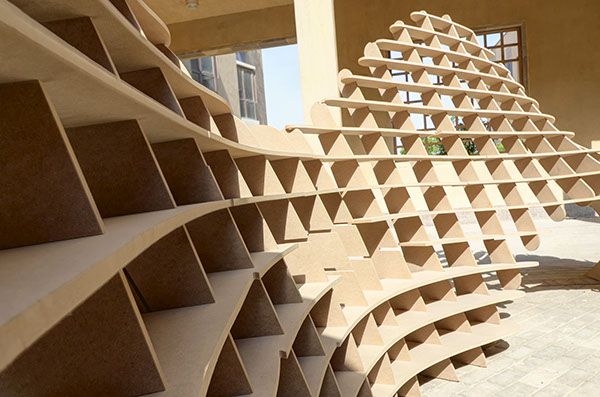
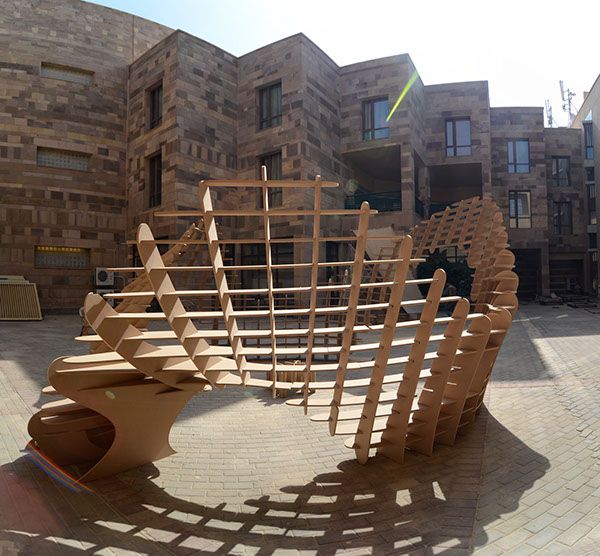
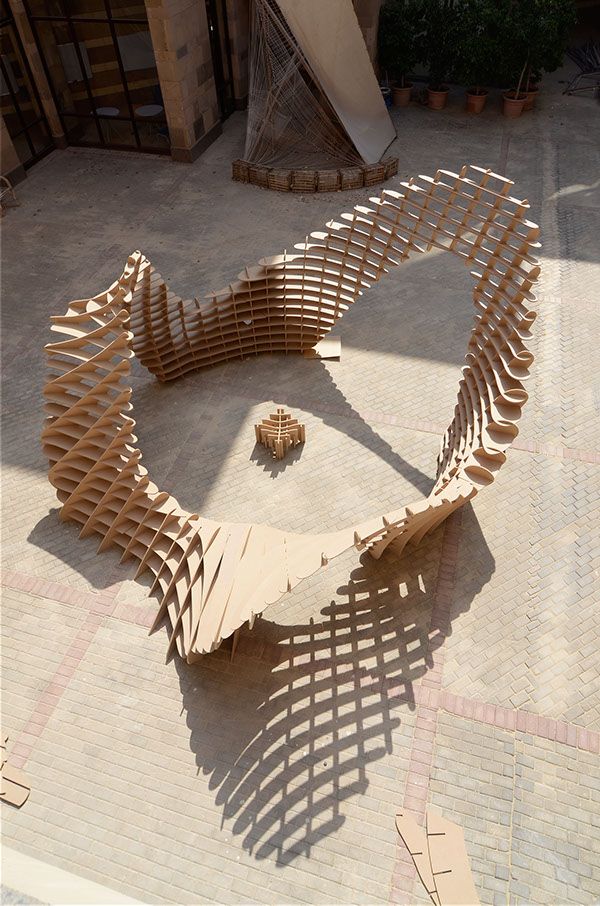
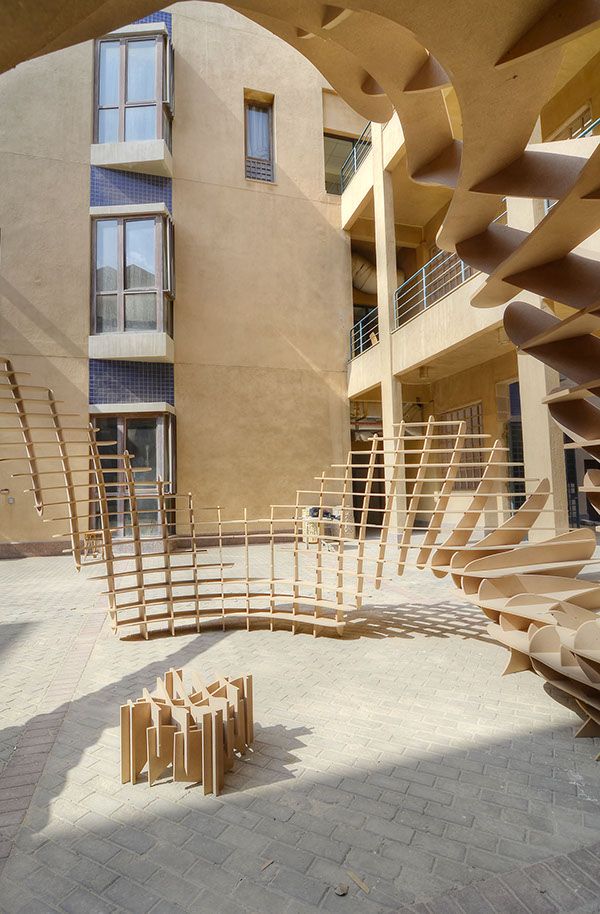
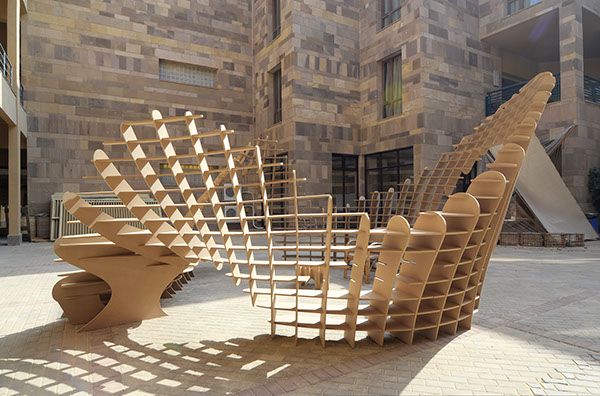

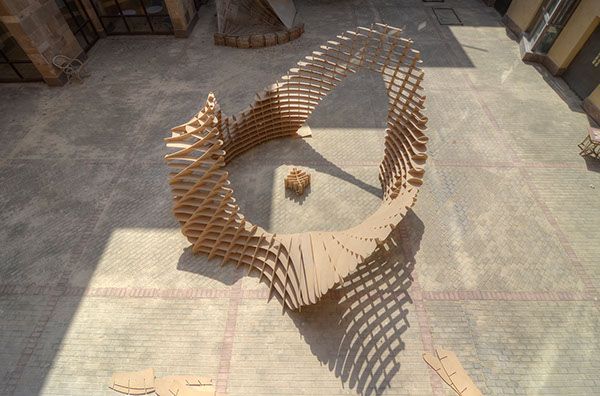

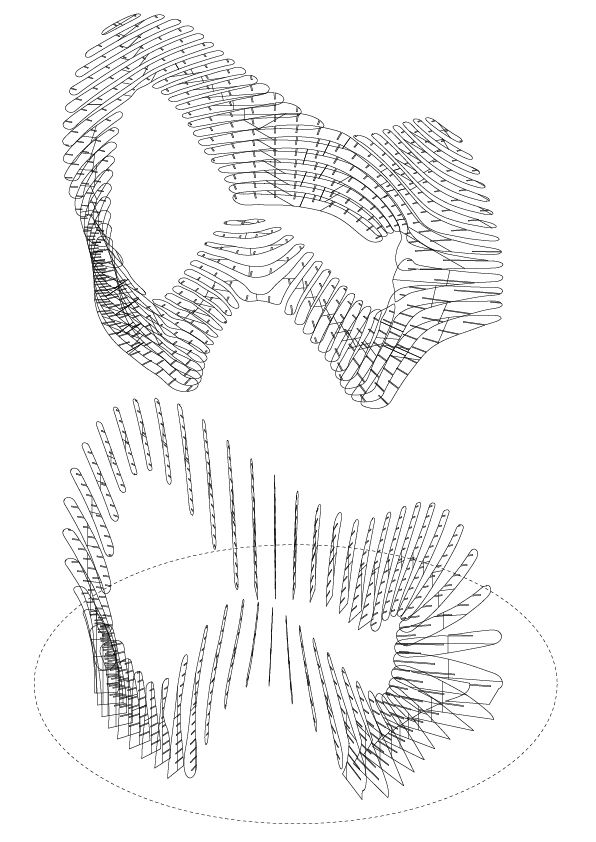
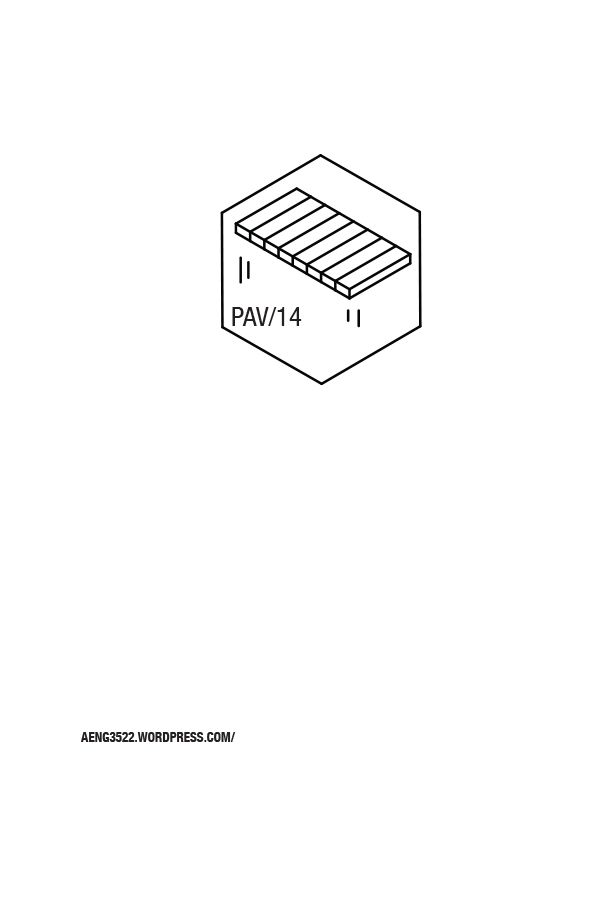












