One of the most significant parametric buildings in the world is the Hangzhou Tennis Center. The building has been selected for this article due to its unique and distinctive parametric design method. The designers of this building use parametric design to model the envelope of the center for two rational reasons: first, to find suitable innovative skin, and second, to reduce the steel consumption for the structure.
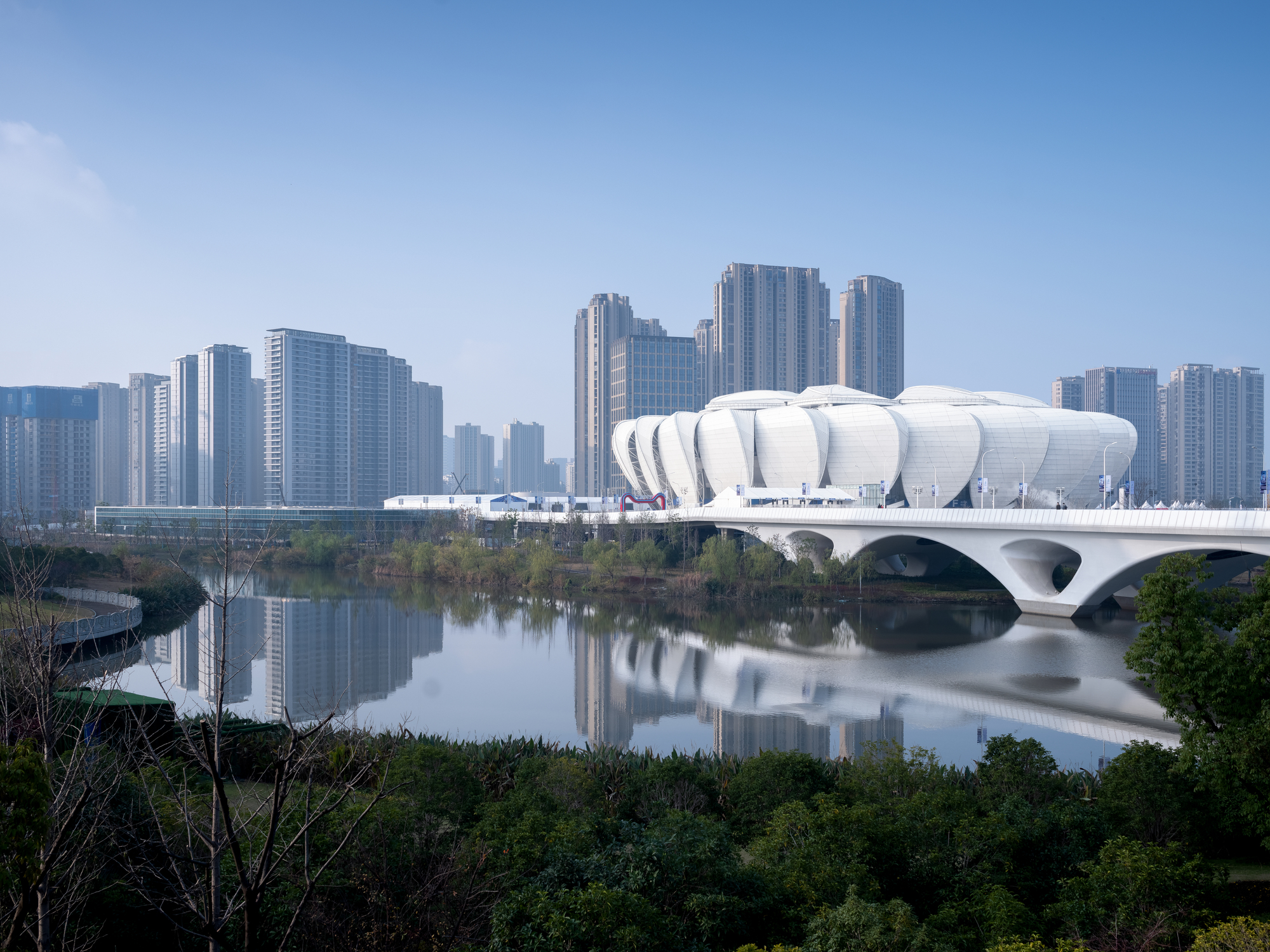
© Shao Feng
The computational design criteria of this building are based on five main tasks:
-
Translation
The design concept, the design problem, or the initial design model (according to the type of design project) is translated parametrically by programming or scripting to a parametric model. This task can be operated by the architect of the project, a parametric design expert, or an external specialized firm. In the case of collaborating with an expert or an external firm, the design team should provide the parametric team with a full description of the concept and detailed objectives of the design to accomplish a successful parametric model.
-
Rationalization
In this task, the parametric designer converts the basic concept, the sketch, or non-rational geometry into a rational logical model. This task is necessary only if the design team did not supply the parametric team with a rational 3D model that presents the concept or the design problem.
-
Control
The lead parametric designer has to find an appropriate mechanism to control the parametric model. At first, the designer should figure out the fundamental geometry, which usually called the “Design Surface”. Afterward, he/she has to assign the pre-defined parameters on his surface as the generator of the alternatives.
-
Generate and Test
This is the main task in the parametric design process. Design alternatives are generated through the pre-defined parameters that were assigned on the design surface. These alternatives are evaluated carefully and accurately by the designers throughout a criterion that depends on specified factors that differ from one project to another. However, the factors are typically related to four areas: structure, construction, aesthetics, and the environment.
-
Sharing Information
In the sharing information task, the final design model will be translated to a clear language for the construction phase. Scripting can be used to convert the model to data, drawings, schedules, or files for other applications that are suitable for contractors.
Building Background:
The Hangzhou Tennis Center is located in the city of Hangzhou in China. The center is one of the buildings the Olympic Park projects. The Olympic Park occupies 400,000 square meters on the west bank of the Qiantang River, whereas the building utilizes 220,000 square meters to accommodate 10,000 seats. The Park and the Center were designed both by the same company NBBJ in collaboration with the CCDI firm for structural design. The construction of the center was launched in 2011 and it is completed in 2015.
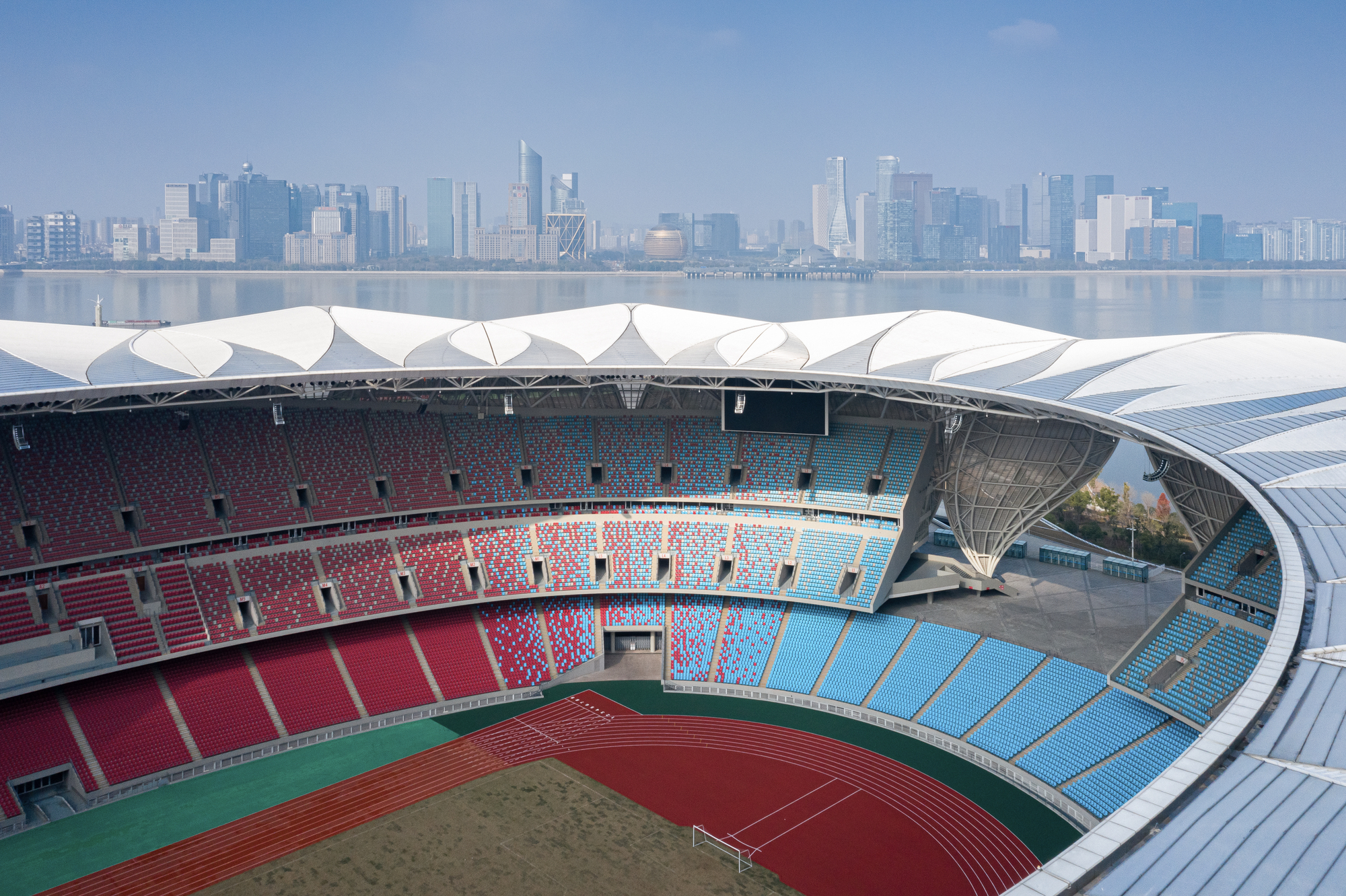
© Shao Feng
The parametric design process of the Hangzhou Center started immediately after determining the geometry of the envelope. NBBJ intends to reduce the amount of steel that will be used for the envelope structure in order to model an efficient shell that provides the spectators with a clear field of vision. Consequently, the resultant shell successfully achieves the previous goals with 24 steel trusses that bond with the concrete bowl, and reduces the steel consumption by 67% of the intended amount. This achievement truly demonstrates successful parametric design.
Overview of Parametric Design
NBBJ Company supervised the parametric modeling process of the Center during the schematic design phase. The main goal of this process was to produce a model that is economical in steel quantity and sufficient in energy consumption. Grasshopper application was first used to generate an accurate logarithmic design for the shell and then it was used to generate the transfer of the design information to other disciplines and achieve efficient collaboration. Furthermore, the parametric design was also applied to other tasks in this project for the first time:
- Geometry Design
- Form Variations
- Structural Collaboration
- Conceptual Simulation
- Surface Analysis and Cladding
- Coordination
- Documentation
Envelope Geometry:
The main design concept of the envelope was based on a double curve surface that was developed from a circular arc. The objective of the concept was to model an envelope that provides enough shadow on the bowl, protects spectators from the rain, and affords covered space for mechanical equipment and lighting devices. The surface was transformed parametrically to a point cloud of NURBS control points. These points were generated to produce repetitive double curve surfaces that were arrayed along the circular arc. The generated double curve surfaces took a form of a petal.
Generate Architectural Alternatives:
After defining the envelope geometry, the resultant petals were parametrically generated to gain a number of alternatives for their design and arrangement. The process depended on two operations: sorting and transforming. The design alternatives were evaluated and compared by the design team according to pre-defined factors: aesthetic judgment, parameters for shade, drainage, structural performance, and sports technology systems.
Generate Structural Elements:
To convert the petals to structural elements, NBBJ collaborated with CCDI Company to transform the double curve surfaces of the petals to a typical truss centerline model. This model was produced by Grasshopper and is applicable for structural design software. Hence, the efficient collaboration between NBBJ and CCDI had designed a convenient sufficient truss for the envelope.
The parametric design was also used for the structural analysis of the project. Kangaroo Physics plug-In for Grasshopper was employed to simulate the effect of the gravity force on the truss elements. This simulation illustrates the tensile and compression forces, which made it easy for the designers to make the appropriate structural adjustments on the trusses. This process contributed effectively in identifying the structural problems at early phases in the design process. This has great benefits for the time schedule of the project.
Cladding Design:
The parametric design was employed to facilitate the calculation process of the number and quantity of aluminum panels. Rhinoceros and Grasshopper have the tools to determine the areas of the double curve surfaces and to penalize the aluminum on these surfaces accurately. In addition, this software helped in the manufacturing of the panels by unrolling the ruled surfaces to flatten plates and cutting them with CNC machines.
Construction Documentation:
It is outstanding that the documents of Hangzhou Center were also algorithmically prepared. Grasshopper has the ability to make the export process of the parametric model to other applications within reach. Custom scripts were developed for automatic export of the data as 3D DWGs files. The files were used in Autodesk Revit to generate the orthographical drawings, whereas a special Grasshopper script was used to unroll the ruled surfaces and to document the details of aluminum plates in special drawings with quantity spreadsheets.
Written by Arch2O Internship Team
- CCDI official website. “Design and Innovations of Steel Structure as Sports Venues in China.” (2012). http://www.ccdi.com.cn/
- Miller, Nathan. “The Hangzhou Tennis Center: A Case Study in Integrated Parametric Design.” ACADIA Regional Conference 2011: Parametricism SPC, Lincoln, Nebraska, (2011).
- NBBJ official website. “ A City Blossoms.” (2015). http://www.nbbj.com/work/hangzhou-stadium/
- Hudson, Ronald. “Strategies for parametric design in architecture: An application of practice-led the research.” Ph.D. Dissertation, University of Bath, (2010).
- Wang, Tsung- Hsien. “Parametric Modeling.” School of Architecture, University of Sheffield. (November 2012).