AA Summer DLAB experiments with the integration of advanced computational design, analysis, and large-scale prototyping techniques. Now in its 14th year, Summer DLAB continues to build on its expertise in complex architectural design and fabrication processes, relying heavily on materiality and performance.
The program brings together a range of experts – tutors and lecturers – from internationally acclaimed academic institutions and practices, including AA Emergent Technologies & Design (EmTech) Graduate Programme staff. The research generated at Summer DLAB has been published in international media and peer-reviewed conference papers, including SimAUD (Simulation in Architecture and Urban Design), eCAADe (Education and research in Computer Aided Architectural Design in Europe).
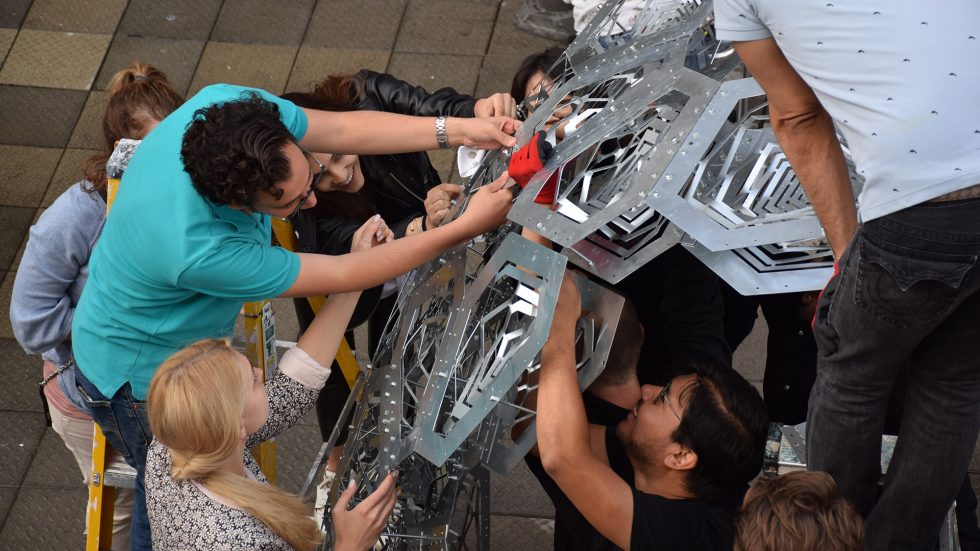
Courtesy of Summer DLAB
In 2018, the program focused on devising a novel approach for the creation of metal light-weight self-supporting structures through the employment of metal kerfing and robotic sheet panel expansion. Research objectives have focused on the synthesis of material behavior on a local scale and the structural performance on a global scale via advanced computational and robotic methods.
Traditional sheet forming techniques employ incremental deformations to a sheet until it is formed into its final shape, and the forming tool can be attached to a CNC machine or a robotic arm. Robotic metal sheet forming opens up new opportunities in the design and fabrication of component-based aggregations that can be facilitated for cladding purposes or spatial enclosures.
The versatility, multi-axis freedom, precision, and adaptable programmability of a generic robotic arm introduce new approaches and techniques to the metal sheet forming process. By the careful correlation of form-finding techniques and various analysis methods, structural, environmental, and other critical performative properties can be articulated via robotic metal sheet forming. The investigation of performance facilitates the consideration of pattern that moves away from sole ornamentation towards processes that trigger pattern formation in natural systems.
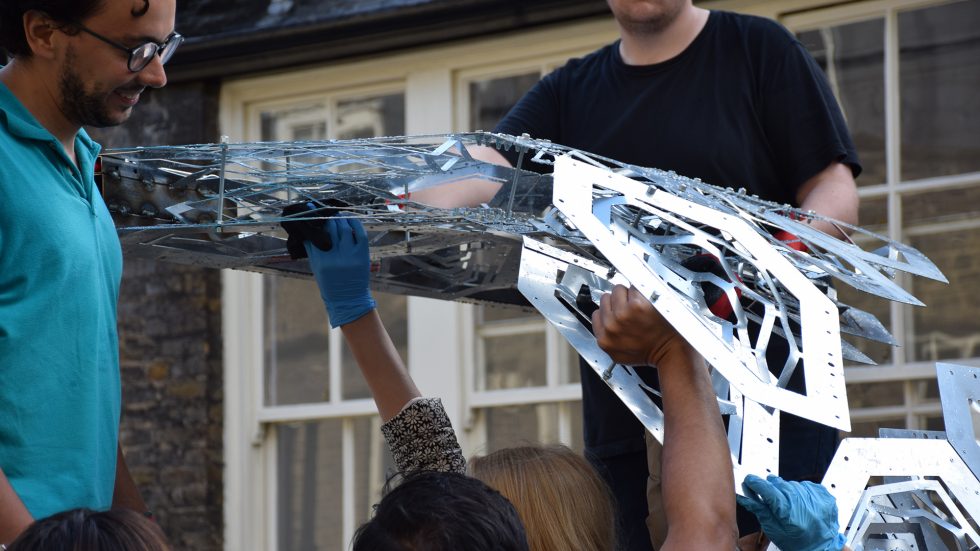
Courtesy of Summer DLAB
The research generated in Summer DLAB 2018 has focused on the geometrical, structural, and material properties within the agency of robotic sheet metal expansion. In engineering, there is a need for light materials able to withstand different load conditions. Expanded metal sheets have been employed in the construction industry mainly as furniture, safety fences, and sidewalks among other uses. The structural behavior of expanded metal sheets has the potential to yield architecturally interesting and materially efficient assemblies. The research agenda aims to link the notions of complexity and simplicity throughout the design and fabrication processes. While complexity is generated throughout computational form-finding and analysis techniques, simplicity lies in how architectural information relating to geometry, analysis, and fabrication can be seamlessly transferred between various digital and physical platforms.
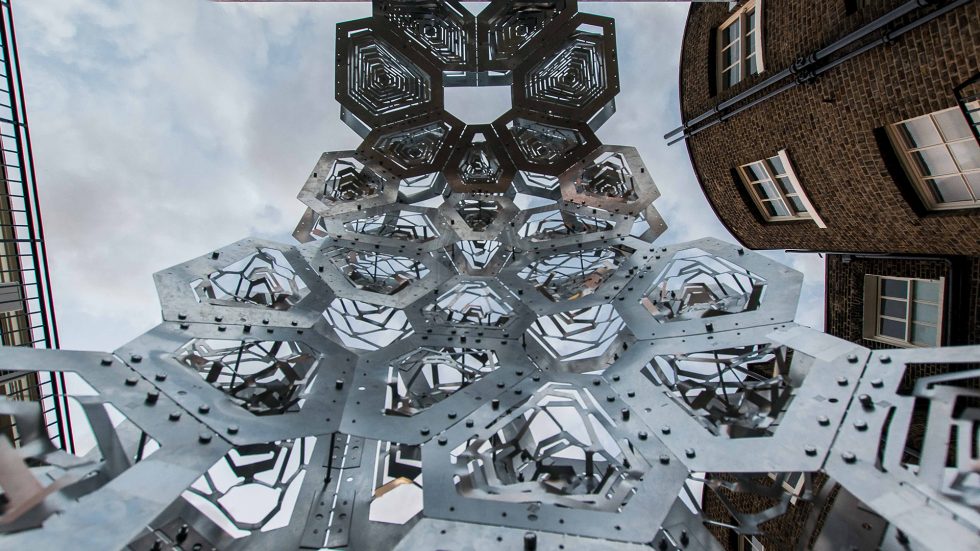
Courtesy of Summer DLAB
Sheet metal expansion methods in traditional manufacturing industries are well-documented and established for their effectiveness and precision. This process sets up a set of constraints that have direct feedback on the computational form-finding process. Initial experimentation has concentrated on investigating the relationships between metal kerfing and metal expansion on a component scale.
A computational algorithm in Grasshopper modulates pattern density, pattern distribution and symmetry, opening width, and the overlap amount of consecutive rows for metal kerfing. The computational setup is then applied on a range of panels of varying sizes and forms with a robotic framework that comprises a 6-axis robot (KUKA KR 60), a custom pushing tool as an end effector, and a custom jig for securing the panels. These experiments establish the correlation between the amount and distribution of material removal, plastic deformation through metal expansion, and spring-back.
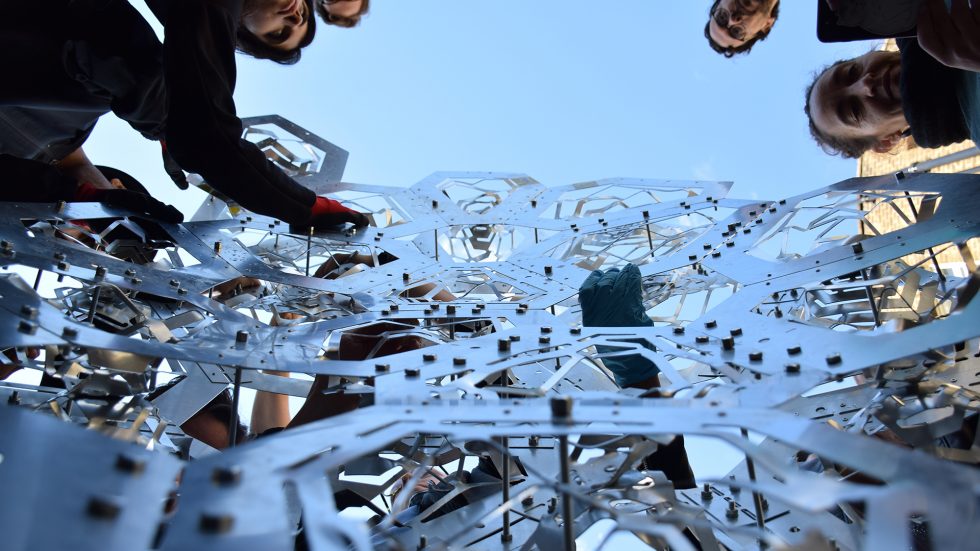
Courtesy of Summer DLAB
Computational form-finding workflow concentrates on the integration of component behavior with the structural performance of the global configuration. A custom-built script in Grasshopper initially evaluates global geometry options via Finite Element Analysis (FEA) with the Grasshopper add-on Karamba. The compressive stress values obtained through FEA are then implemented for an unequal mesh triangulation of the global form, simultaneously establishing planarization of the panels. This mesh is further optimized in order to estimate equilateral triangulation. Finally, within each triangular face of the mesh, hexagonal panels are generated for further openings.
Initial experimentation conducted on the local scale sets the amount of metal expansion required for each panel. This information is employed to generate the robotic tool path for pushing distance and direction is generated. Data on assembly sequence and panel connection detailing is generated within the custom-built script, aiding in the fabrication and assembly processes. The incorporation of robotic sheet expansion constraints as a driver starting from the initial stages of design development has contributed to a strong correlation between design and fabrication phases, moving away from a direct design-to-production approach.
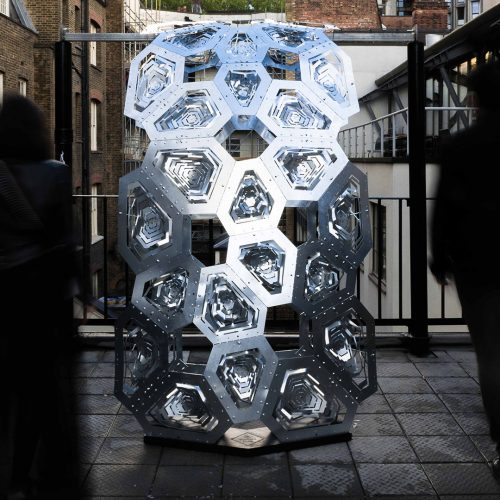
Final prototype.
Future research directions include the development of kerfing patterns that are directly informed by the structural behavior of local panels through the application of different loading conditions. This ambition has the potential to associate the distribution of differentiated kerfing patterns with the global form and forces. While the final prototype has proven to yield high structural performance values, further investigations on the elaboration of this system for variable complex global configurations are going to be carried out. AA Summer DLAB continues to explore generative design algorithms as a means to design a structure that can perform on a multitude of levels and functionalities and to understand material computation via facilitating the simulation of material organization and differentiation by taking into account real-world constraints.
Acknowledgments.
We would like to thank the faculty and students of AA Summer DLAB 2018 for their great efforts.
- Head of AA Visiting School: Christopher Pierce
- Head of AA Summer DLAB: Elif Erdine
- Faculty: Elif Erdine, Giulio Gianni, Angel Lara Moreira, Alvaro Lopez Rodriguez, Yutao Song, Alican Sungur.
- Students: Laura de la Torre, Montei di Matteo, Bryan Edward, Angelina Garipova, Vanda Hajizadeh, Jill Hartley Yokota, Ahmed Hassan, Hsin-Ying Huang, Harun Ishak, Maciej Kanarkowski, Kseniia Kondratovich, Roberto Marin, Sahil Mohan, Elena Nuñez Segura, Rajiv Parekh, In Pun, Francesca Savanco, Hugh Taylor, Ziqing Xu, Fan Yang, Masashi Yaushira.
Applications for Summer DLAB 2019 are open. Please find more information on the eligibility and application process below:
Eligibility
The workshop is open to current architecture and design students, Ph.D. candidates, and young professionals. Software Requirements: Adobe Creative Suite, Rhino 5 (SR7 or later). No prior knowledge of software tools is required for eligibility.
Applications
The AA Visiting School requires a fee of £1950 per participant, which includes a £60 Visiting Membership fee. A non-refundable deposit of £350 is required when registering with the online form – with the remaining balance due to be paid by the deadline of 8 July 2019.
Fees do not include flights or accommodation, but accommodation options can be advised. Students need to bring their own laptops, digital equipment, and model-making tools. Please ensure this equipment is covered by your own insurance as the AA takes no responsibility for items lost or stolen at the workshop.
1) You can make an application by completing the online application found under ‘Links and Downloads’ on the AA Visiting School page. If you are not able to make an online application, email visitingschool@aaschool.ac.uk for instructions to pay by bank transfer.
2) Once you complete the online application and make a full payment, you are registered to the program. A CV or a portfolio is not required.
The deadline for applications is 8 July 2019.
All participants traveling from abroad are responsible for securing any visa required and are advised to contact their home embassy early. After payment of fees, the AA School can provide a letter confirming participation in the workshop.
For more information, please visit Summer DLAB
Contact details: Elif Erdine (Programme Head, AA Summer DLAB)