Introduction
The computational bamboo installation was built in July 2018 as part of the IAAC Global Summer School in Quito, Ecuador. The structure is constructed from bending-active bamboo laths and rods and will be showcased for 3 months at the Museum of Interactive Science in Quito. The workshop, which resulted in this demonstrator, combined natural local traditional building materials with new computational methods for design combined with traditional fabrication.
IAAC Global Summer School
The demonstrator structure is one outcome of ongoing research conducted at the Institute of Building Structures and Structural Design (ITKE), under the guidance of Prof. Jan Knippers, regarding the design, analysis, and construction of bending-active structures. The workshop was led by two ITKE researchers, Evy Slabbinck and Seiichi Suzuki, and attended by 9 students who were mostly inexperienced in the use of computational tools. The two-week workshop was divided into three parts: the learning phase, design workshop, and fabrication and assembly phase. Initial lectures provided in-depth tuition on bending-active structural systems, computational tools, FEA software, and material science. This 3-day period was then followed by a 4-day intensive design session where the structure was designed in detail and the workshop ended with a 4-day fabrication period. The workshop aims to have an impact on different levels. First, the installation combines traditional materials with cutting-edge computational technology. It teaches local students to use computational design and the resulting demonstrator showcases the advantages of computational design in Quito. Second, the pavilion uses exclusively natural materials: bamboo rods and laths for the structural system, and jute cord for the joint details. In keeping with sustainable materials, the bending-active system is very materially-efficient as well. There is no need for complex formwork nor molds, nor high-end machinery. Finally, computation is opening new ways for interacting with our structures. Within this context, current architectural paradigms are shifting from designing static building models to the design of more dynamic and behavioral ones. Structures can now be designed to physically respond to stimulus coming from dynamic and unpredictable environments for improving design criteria performances. However, the problem of designing such structures relies on the unpredictability of its geometrical shape. Contrary to standard design processes where the shape can be defined in advance, the final geometrical configuration of these flexible structures relies on the integration of material behavior as the main agent driving the entire formation process. The workshop explored the non-standard dynamic articulations of bending-active elements by bridging the gap between physical and digital models with in-house made software: Elastic Space.
Bending-active bamboo structure
The completed structure is constructed using natural bamboo laths of 5mm thick and rods of 10mm diameter. It spans 7.5m across space, is 15.5m long, and reaches a height of 4m at its peak. The structure attempts to utilize the inherent properties of bamboo, i.e. lightness, flexibility, strength, and natural beauty, within a larger scale construction. The structure differs from other bending-active bamboo structures through adopting the design freedom of Japanese basket builders and implementing it at a larger scale by the introduction of computational design, easy form-finding, and a new structural typology. We move away from arches that need a foundation and are simply connected to one another. All forces are resolved internally within the structure and this pure equilibrium shape pushes the design boundary of bending-active bamboo structures beyond traditional shapes. The structure exits out of a boundary edge, made out of rods, and a syntax filling, made out of laths. All materials are made out of local bamboo canes and are processed to create a smooth consistent structural element. The joints are using traditional friction-tight rope connections with the natural jute cord. The boundary edge is designed and form found to a site-specific shape that was desired. The syntax was implemented in a second step to make the structure more stable and stiff. The syntax uses weaving and torsion to enhance the stiffness of the local very flexible elements. The structure has a spatial 3d design and moves away from 2.5D grid shell structures. Elastic space V2, working with IGUANA (in-house software), is used to simulate the intricate equilibrium of all weaving elements including all connection/coupling points. A computational and digitally fabricated bench was built to support the structure.
Project Info:
Architects: ITKE
Scientific Development: Evy Slabbinck and Seiichi Suzuki Erazo
Technical support: Yaner Luis Cangá Chavez, Anders Obregon, and Juan Edison Columba Paucar
IAAC GSS Students (Design and Fabrication): Juan Francisco Mayorga Jaramillo, Valeria Latorre, Gordon Leibowitz, Valeria León, Veronica Sofia Molina, Maria Gabriela Chacon Palacios, Gisella Parra, Fausto Andres Davila Pazmiño, and Juan David Barona Trujillo
Volunteers (Fabrication): Byron Esteban Cadena Campos, Sophia Natalia Gualán Chacón, Gustavo Francisco Abdo Hernández, Santiago Dario Guevara Hidalgo, and Karen Elizabeth Landazuri Proaño
Documentation: Rafael Fernando Suárez Molina, Santiago Gabriel Miño Paz, and Nestor Emmanuel Mendoza Zambrano
In collaboration with: Institute for Advanced Architecture of Catalonia (IAAC), Institute of Building Structures and Structural Design (itke) University of Stuttgart, and Pontificia Universidad Católica del Ecuador (PUCE)
With the support of: Red Internacional del Bambú y el Ratán (INBAR), Sustainable Forest Management Corporation (Comafors), Fablab Zoi, Museum of Interactive Science (MIC), CODESA, Fibrobambu, and Pelikano Plywood
Project Name: Computational Bamboo IAAC
All Images Courtesy Of ITKE
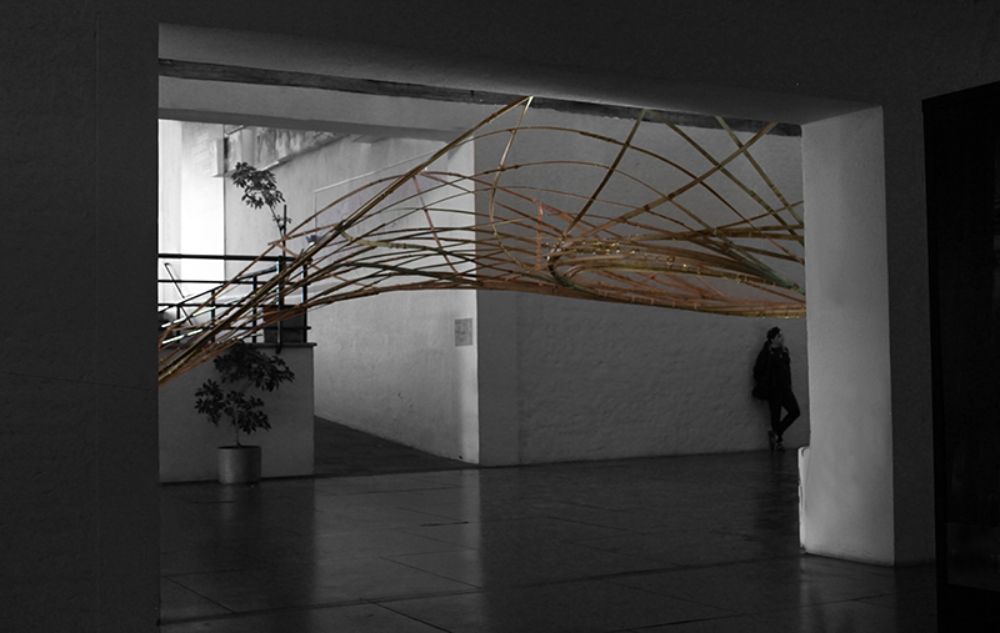
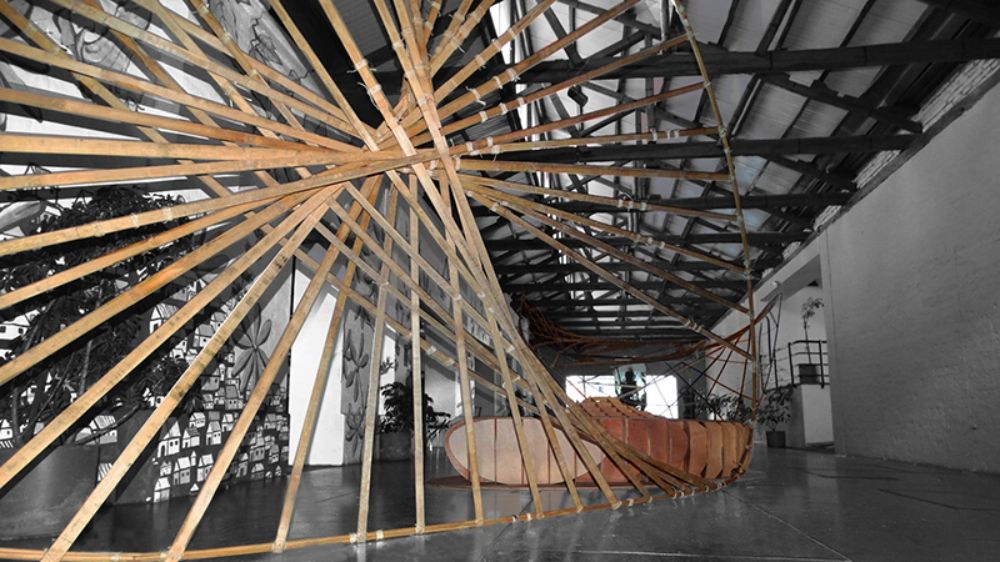
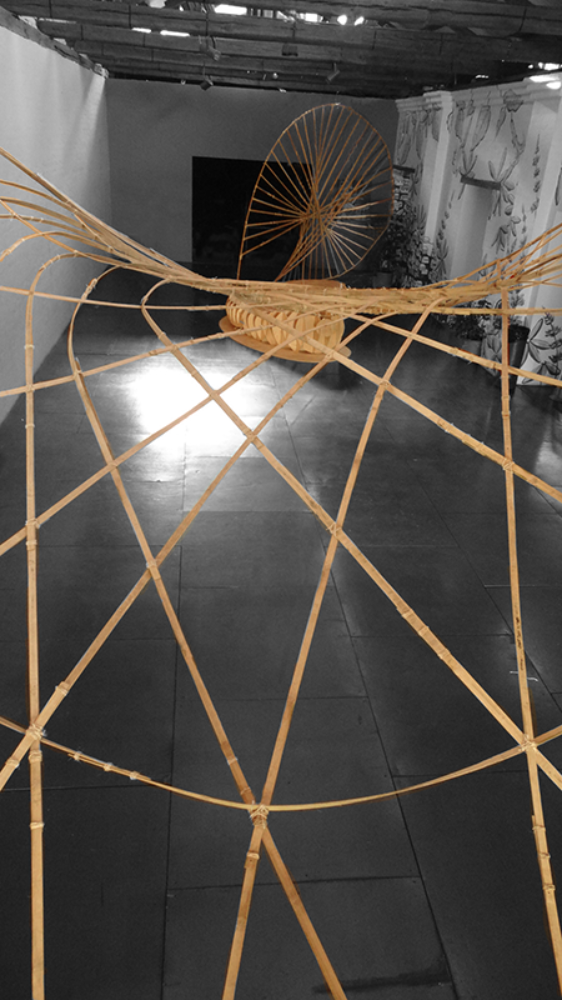
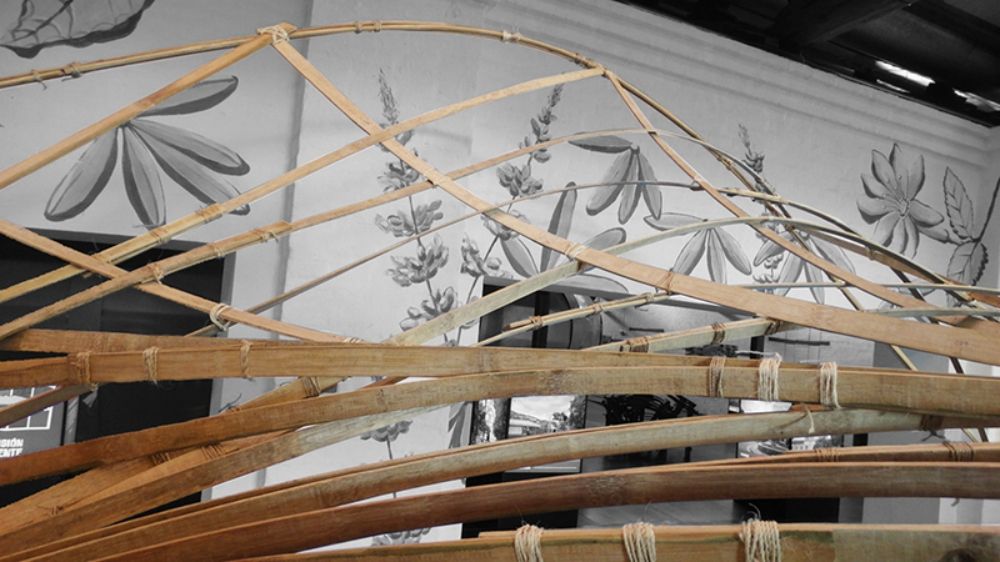
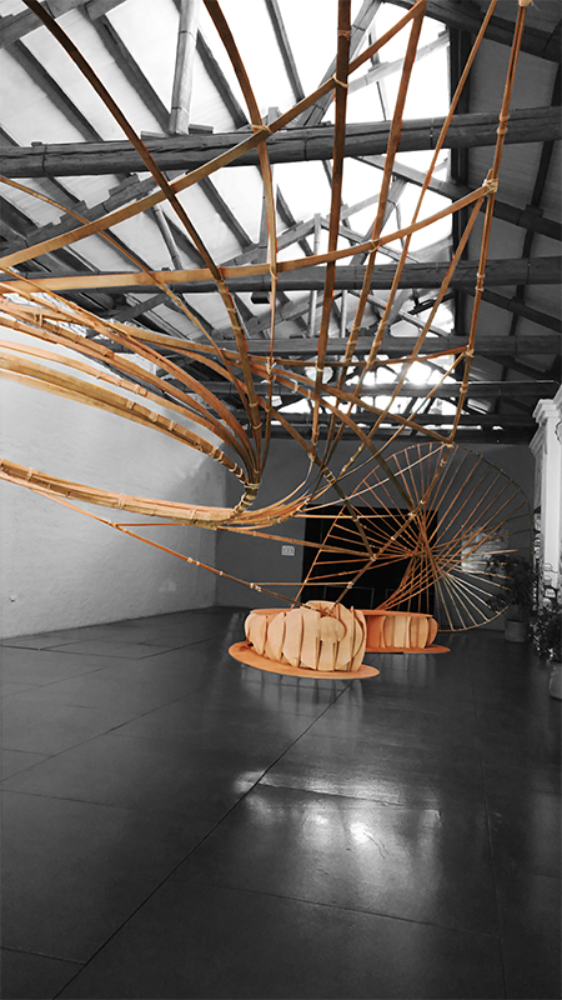
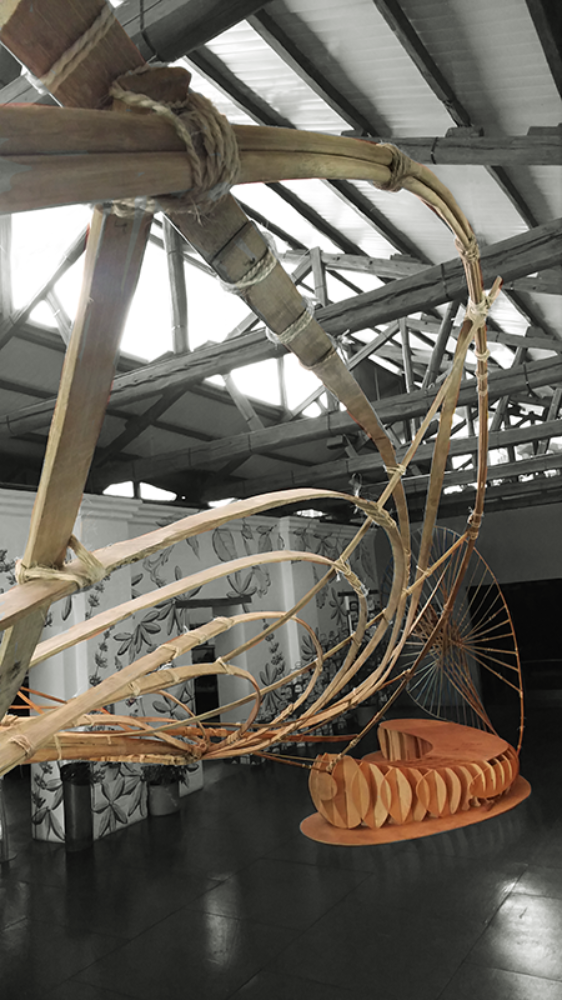
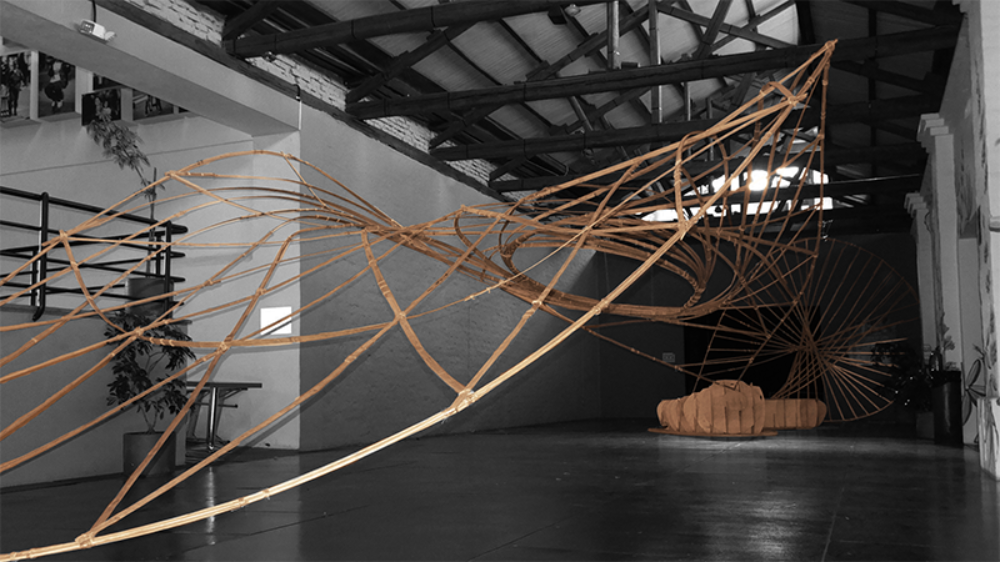