Storage facility for archiving furniture, products, and artwork in Miyota-machi, Nagano Prefecture, with a Culvert Guesthouse attached. Located in a quiet and nature-rich environment where streams weave through a thick forest of red pine, the tunnel-like architecture took shape through a combination of precast and prestressed construction methods.
The tunnel-like building takes shape through a combination of precast and prestressed construction methods in a peaceful and nature-rich area where streams swirl through a thick forest of red pine. Common parts for precast construction are molded at a factory and assembled on-site. One example of its employment in infrastructure projects is the box culvert (a box-shaped concrete structure that stores subsurface waterways, paths, power lines, and communication lines). However, because the approach does not provide a leak-free composition or allow for stacking, both of which are required for this architecture, prestressing was utilized to join the sections.
Culvert Guesthouse ‘s Design Concept
The prestressing method is used in civil engineering projects such as bridges that involve aligning the parts and then tightening them using wires to join them. This produces a seamless and flawless surface finish, a tight seal, and durability. The common square-shaped sections weigh around 12 tons each, and 63 of these parts were employed in total. The size of the parts was determined by the delivery truck’s loading capacity and the weight that a crane could lift. The reinforcement at the entering corner is 45 degrees, which is also used in typical box culverts, acts as a brace, and improves earthquake resistance. A narrow, tunnel-shaped space with an internal dimension of about 2 x 2.3 m was formed by joining these pieces. Each “tunnel” was connected by fourteen wires, which were tensioned uniformly.
The wires were gradually tightened over time until a stress of 46 tons was applied to each. The structure comprises four stacked “tunnels” with a roof in the center. There are two smaller storage rooms and a long, narrow storage room with a depth of around 40 meters, but more are expected to be added to the site as the collection increases. The first story houses the kitchen, bathroom, toilet, and other water utilities, while the second floor houses a small bedroom and a study. The windows were created with as few metal frames as possible, and high-transparency glass up to 10 meters long was fastened into the slots like shoji screens. The gravel and plantings utilized on the façade were also employed on the interior to bring in the outdoor atmosphere.
The gravel was partially cemented with glue to make it easier to walk on. Instead of just pouring resin over the gravel, as is generally done, the resin was applied to the base first, followed by the gravel, to prevent the surface from becoming shiny. Furthermore, the door handles would have looked jarring if they had been fitted as-is. Therefore, an original handle was built to hide in the small gap between the door and the wall. The bathtub is carved into the floor such that the water surface lines with the floor, giving the illusion of a continuous tunnel shape. The final environment is more of a project that mixes civil engineering concepts with product design features than an architectural space.
Project Info:
Year: 2022
Photographs: Takumi Ota, Daici Ano
Collaborators: Noritaka Ishibayashi, Ryota Maruyama, Daisuke Maeda
Filming And Editing: Toru Shiomi
Filming: Takahisa Araki, Masaya Yoshimura
Country: Japan
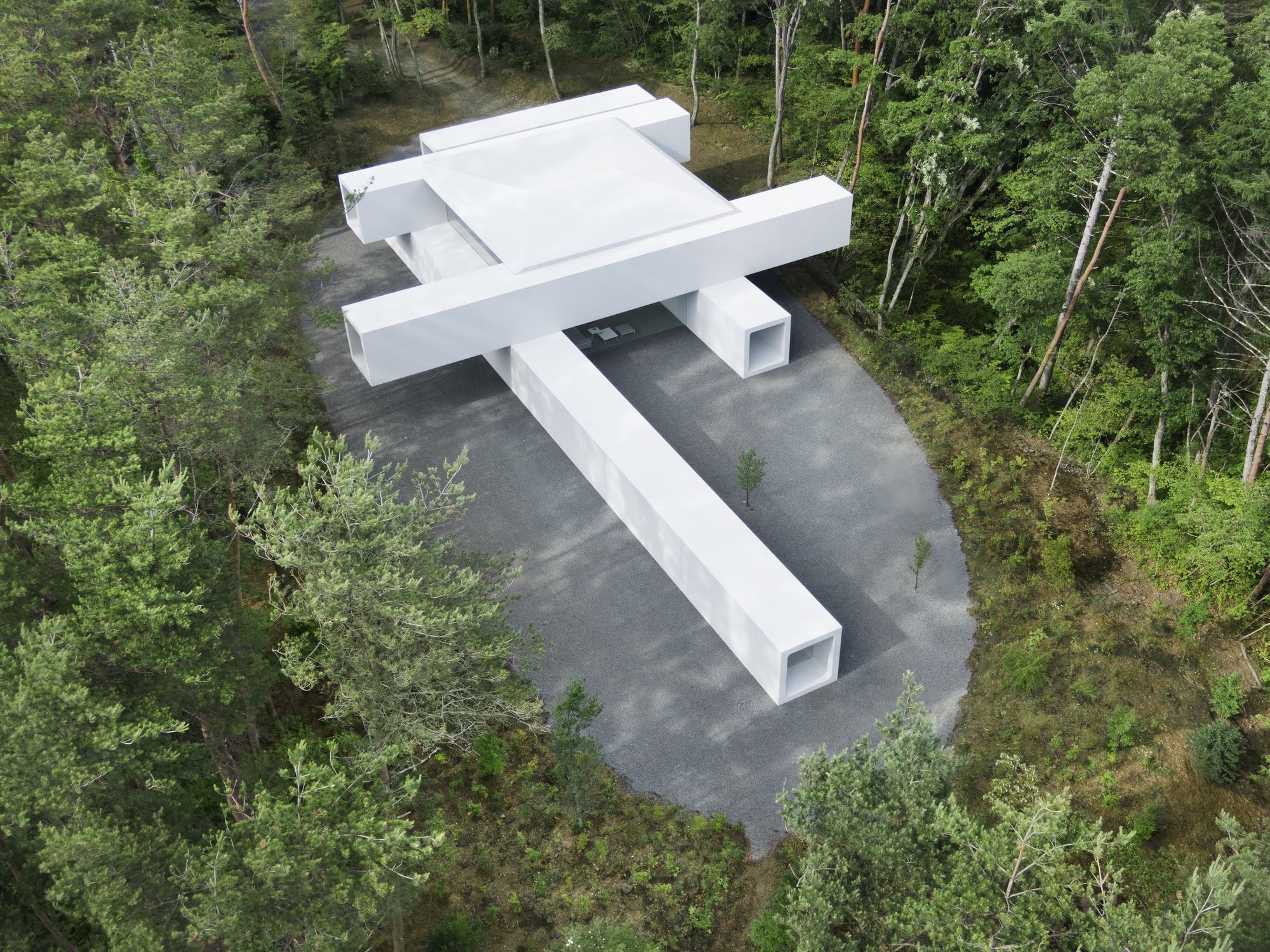
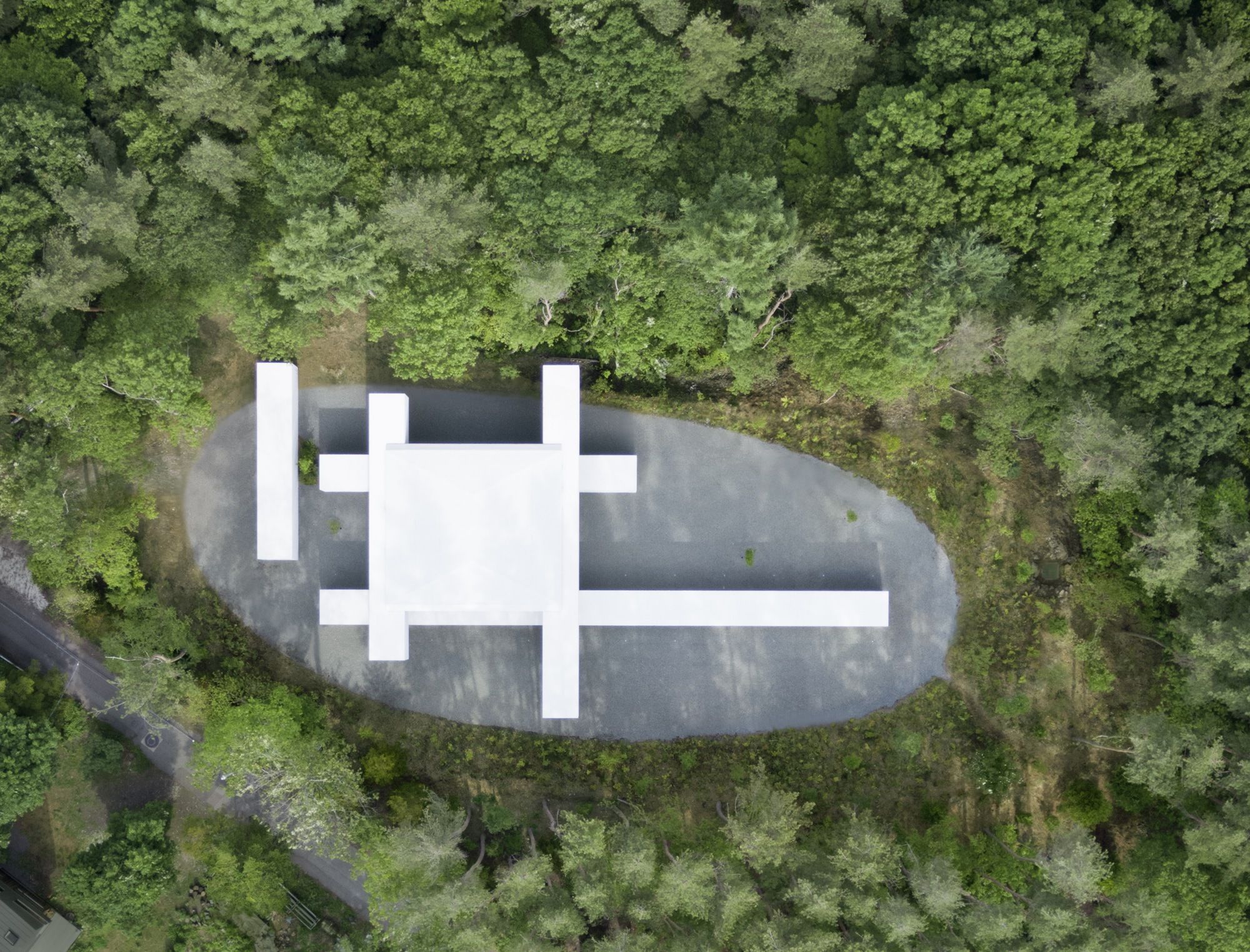
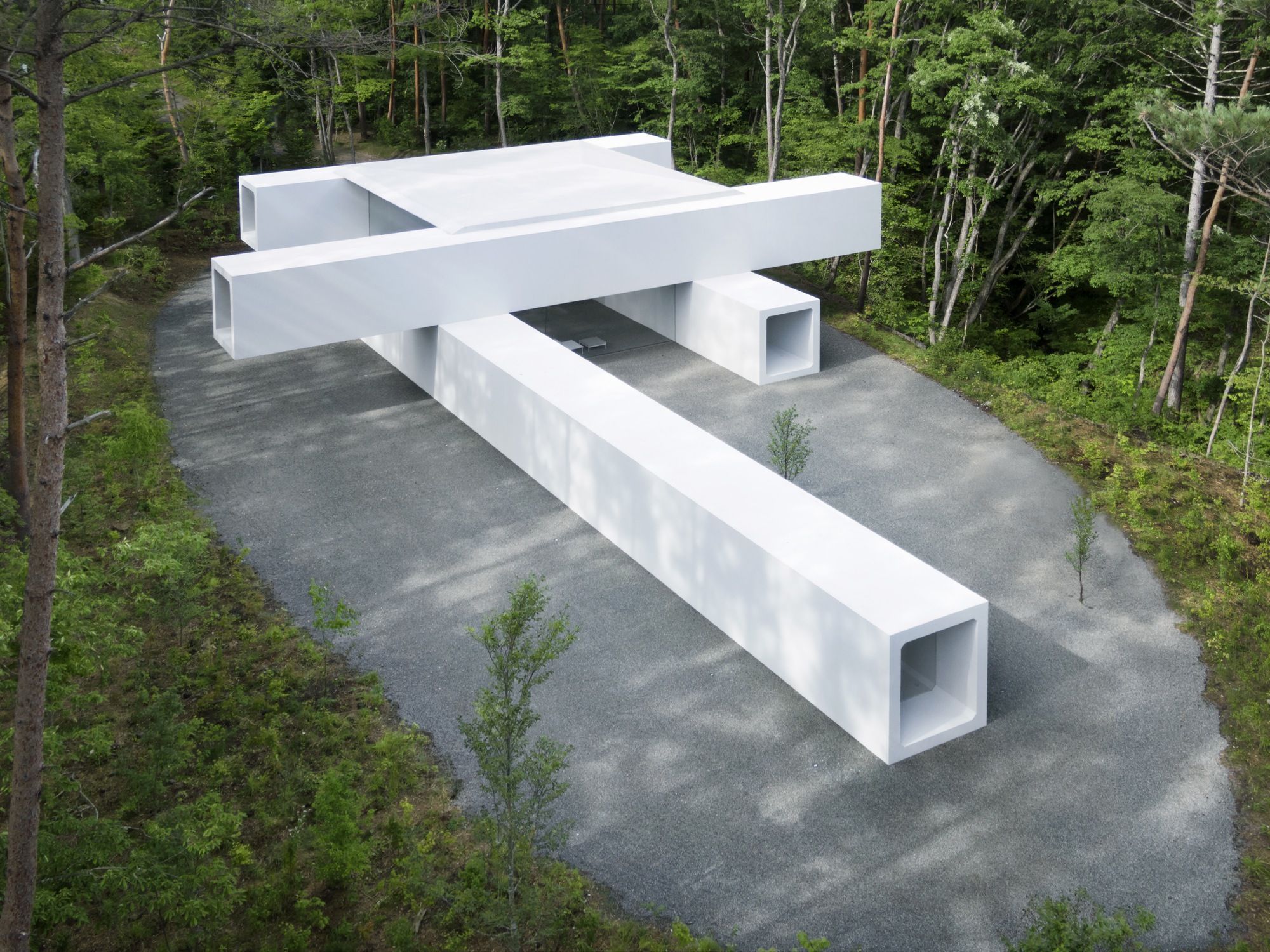
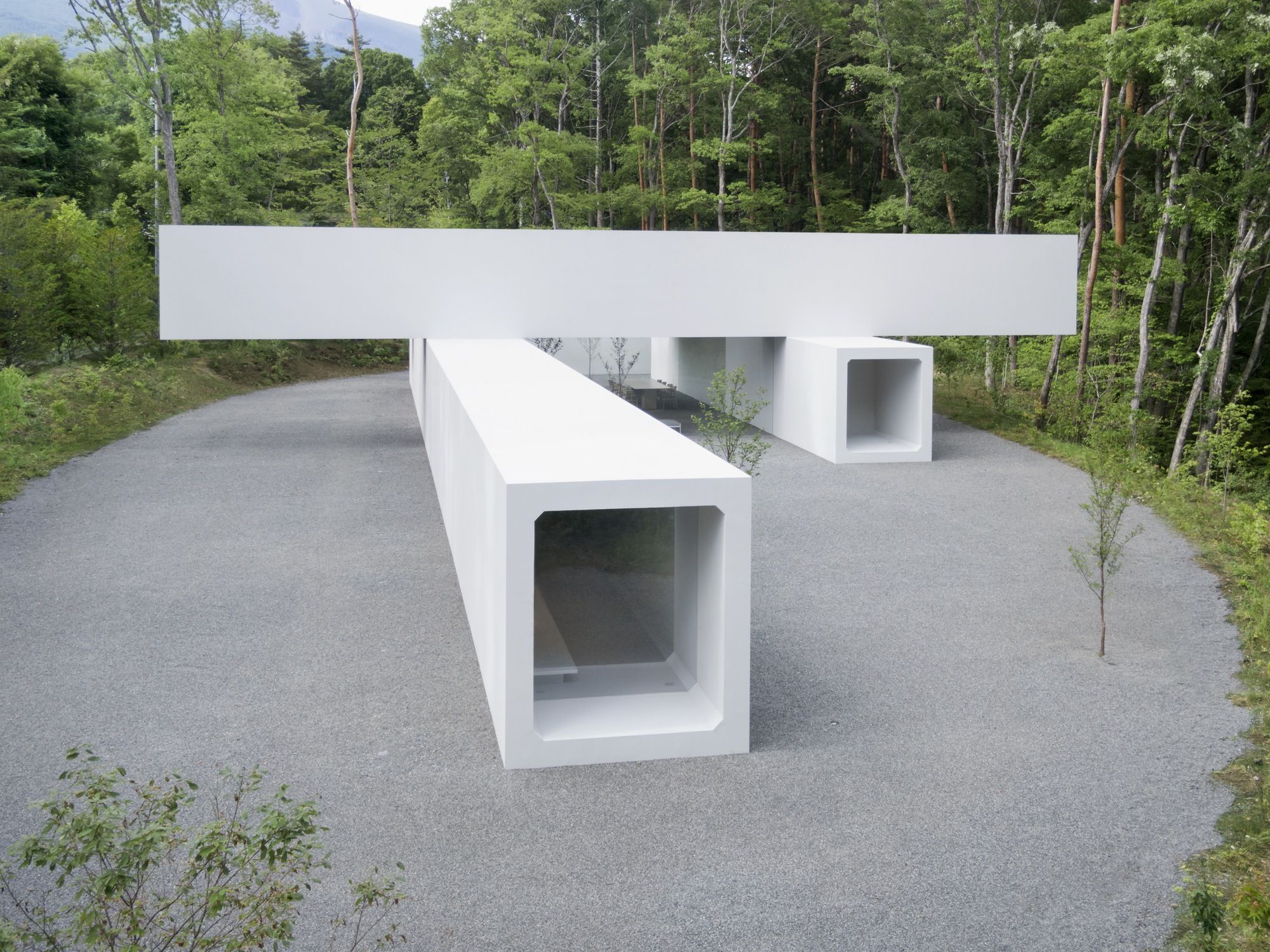
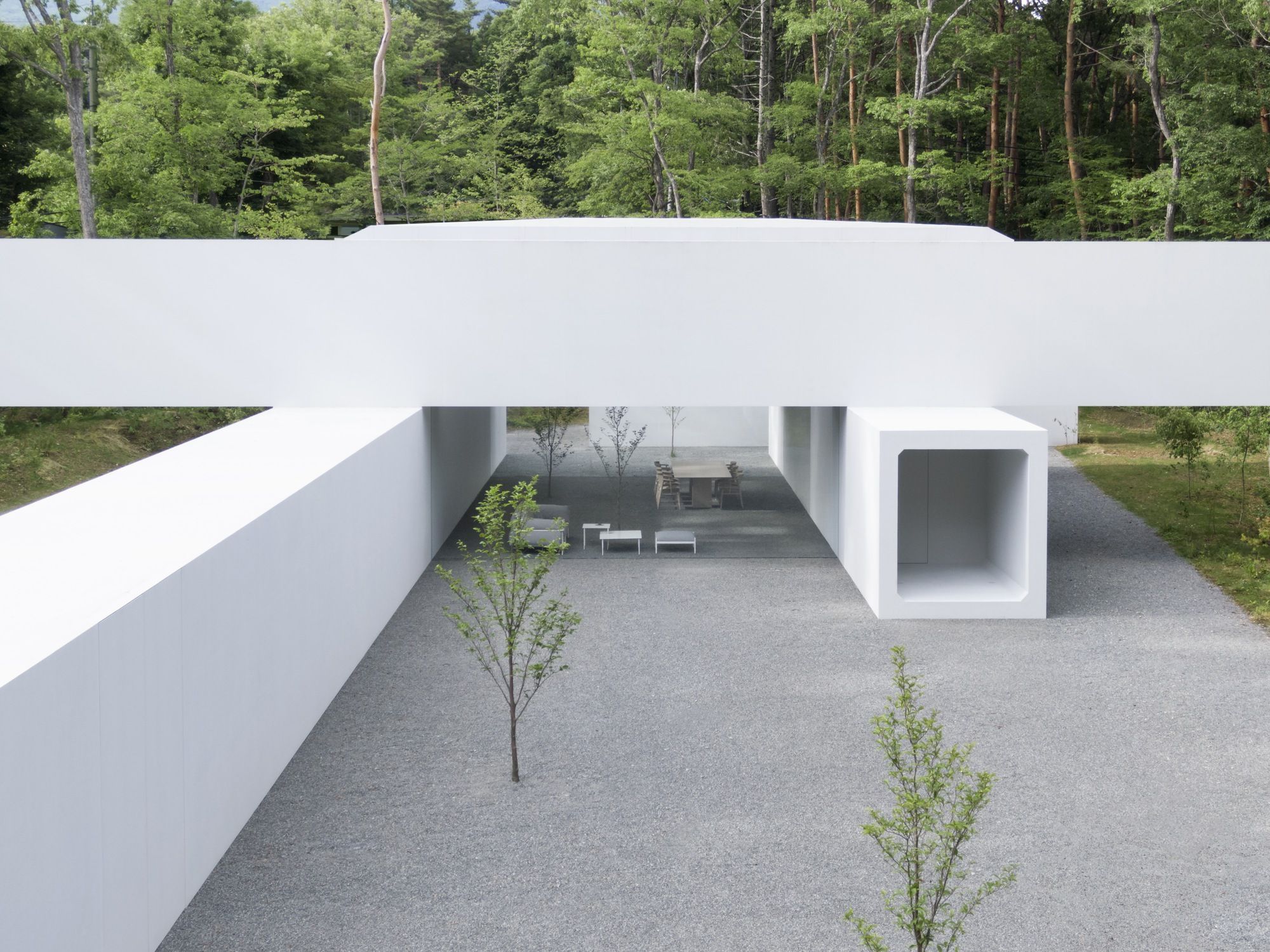
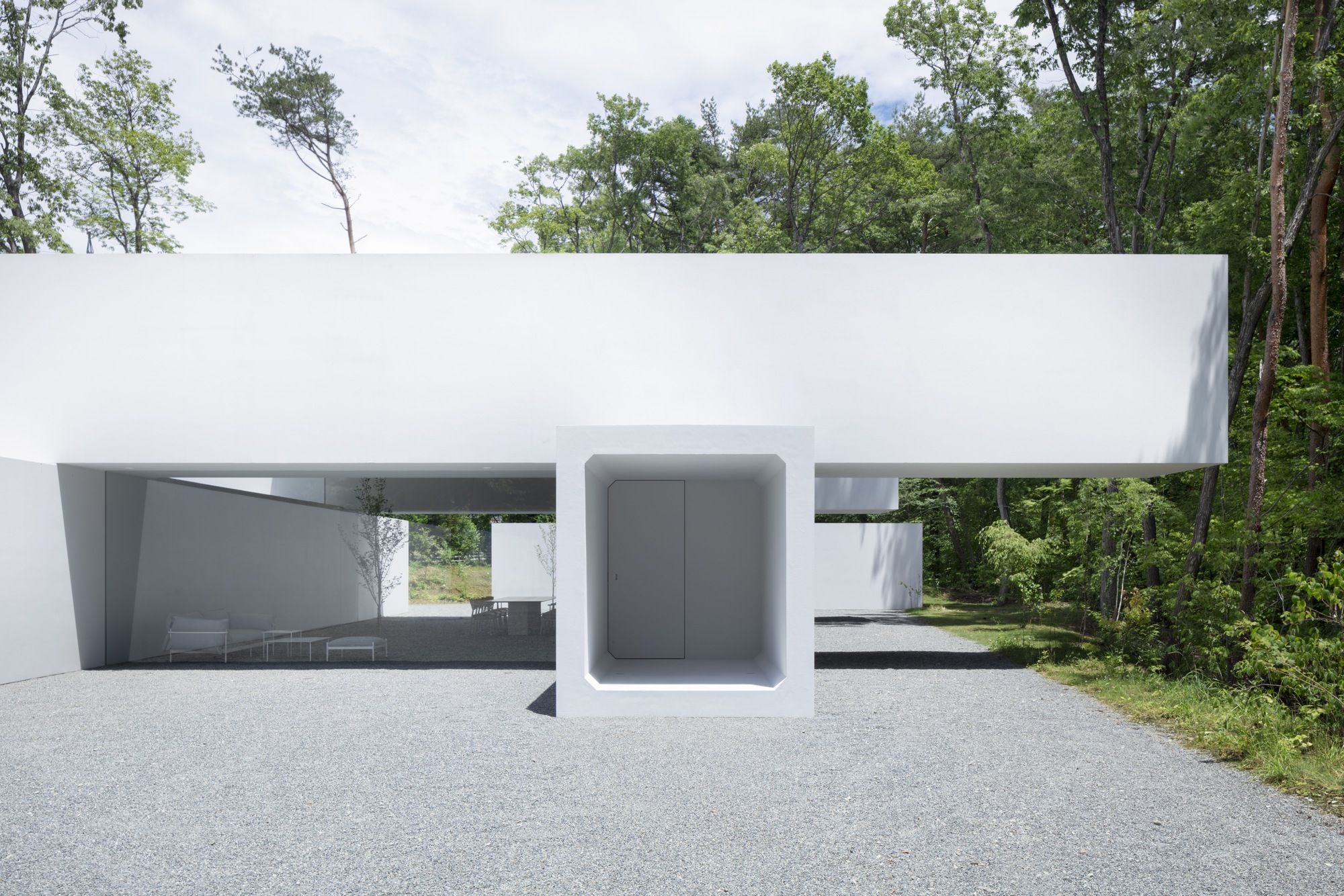
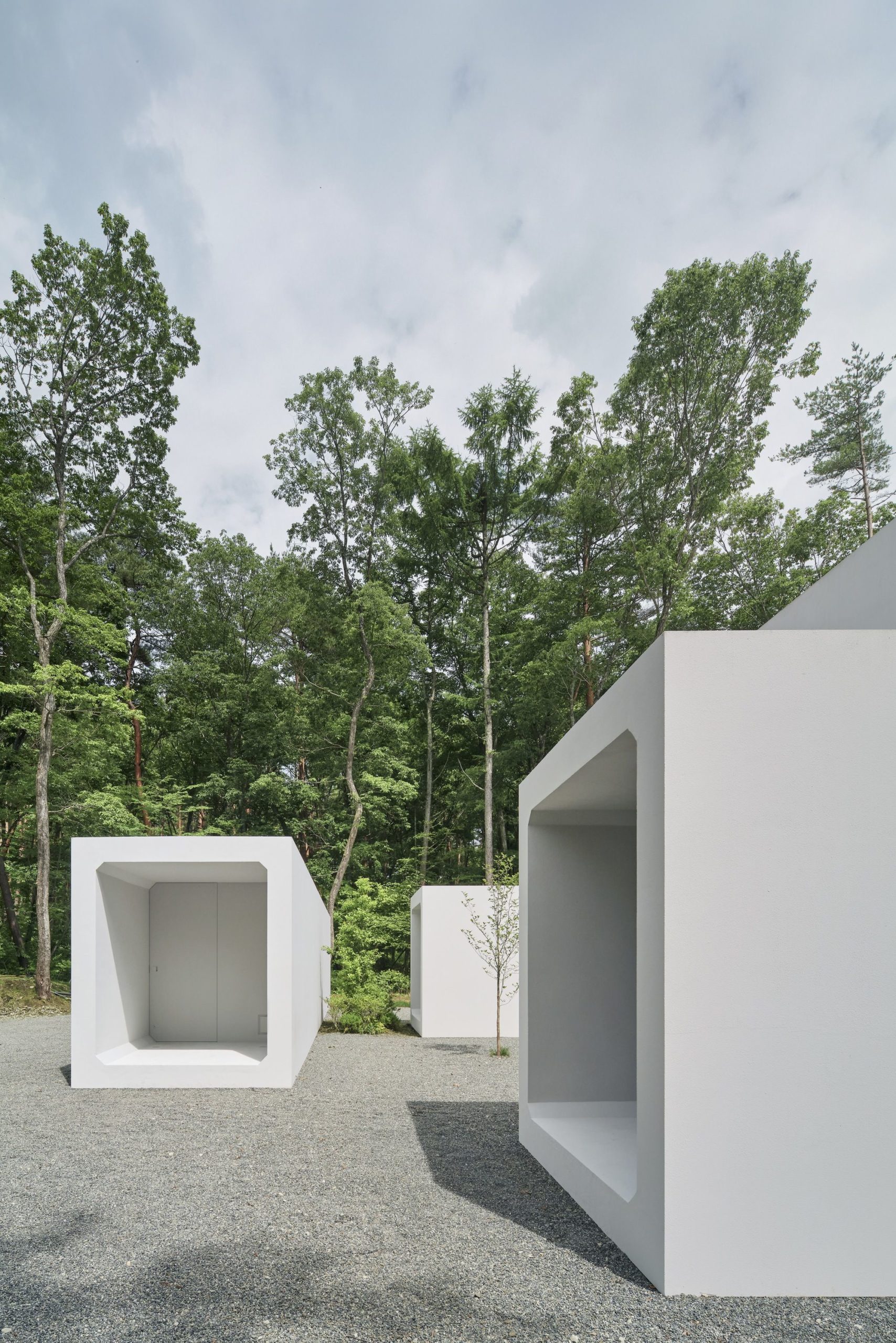
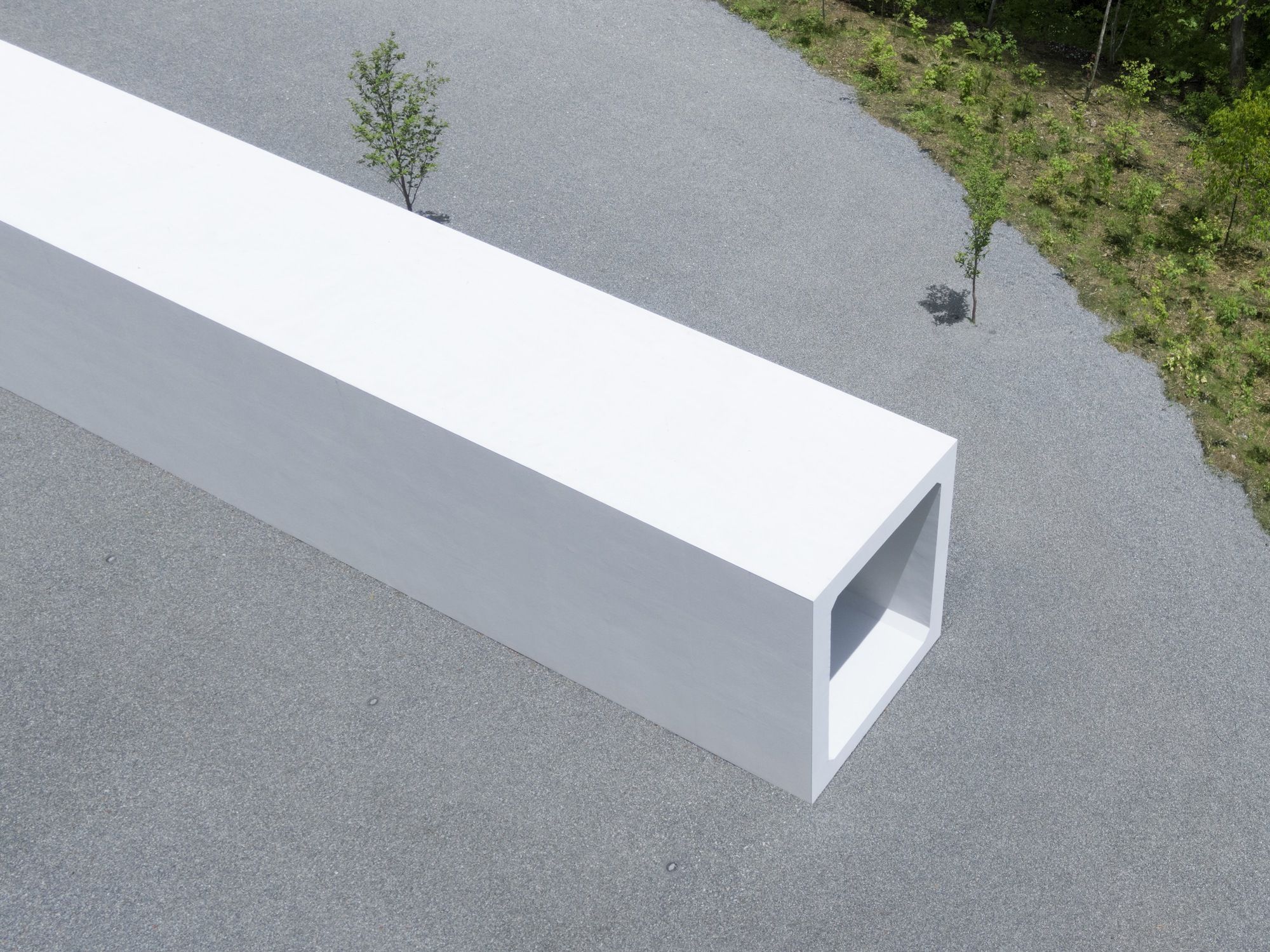
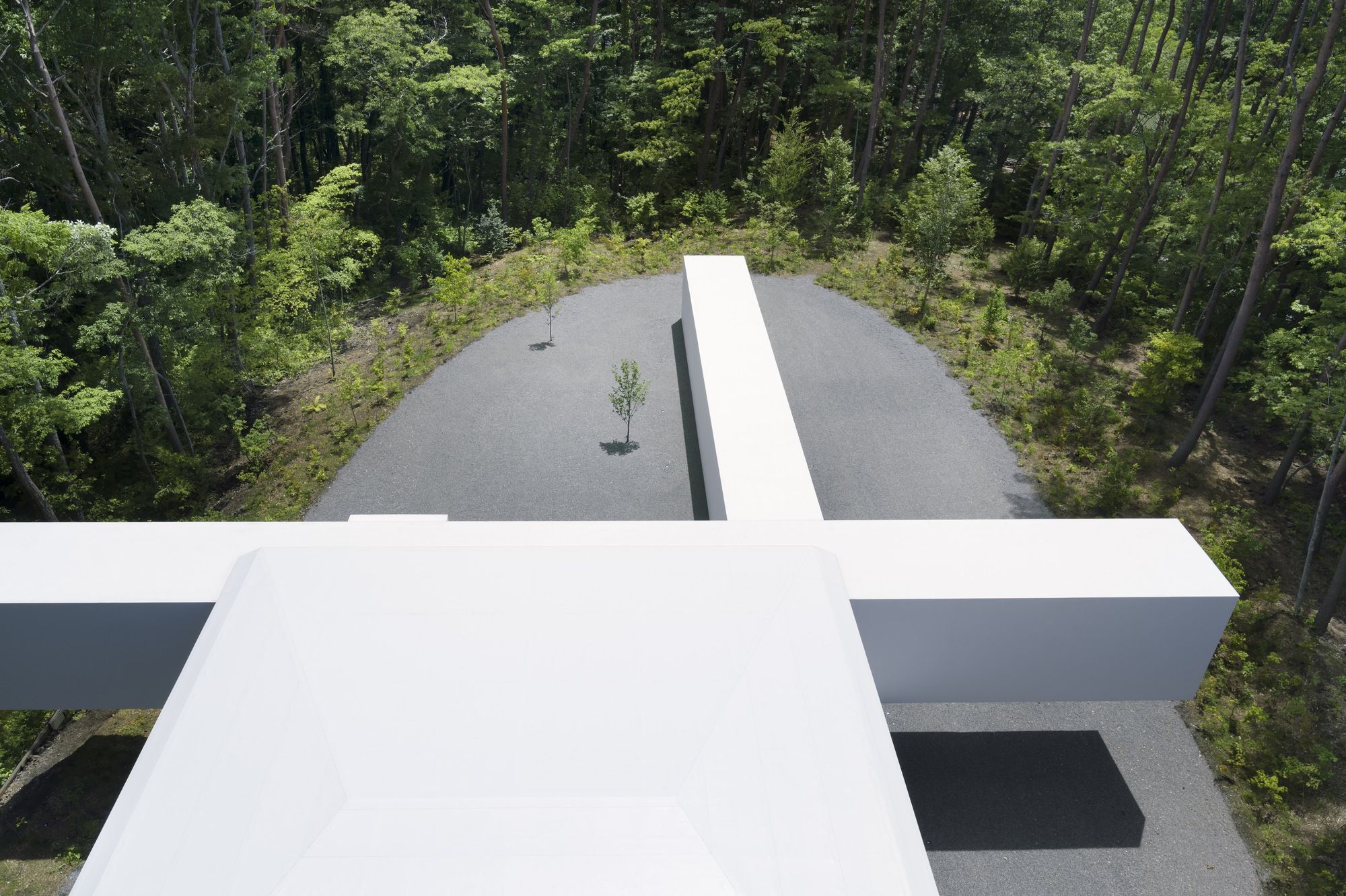
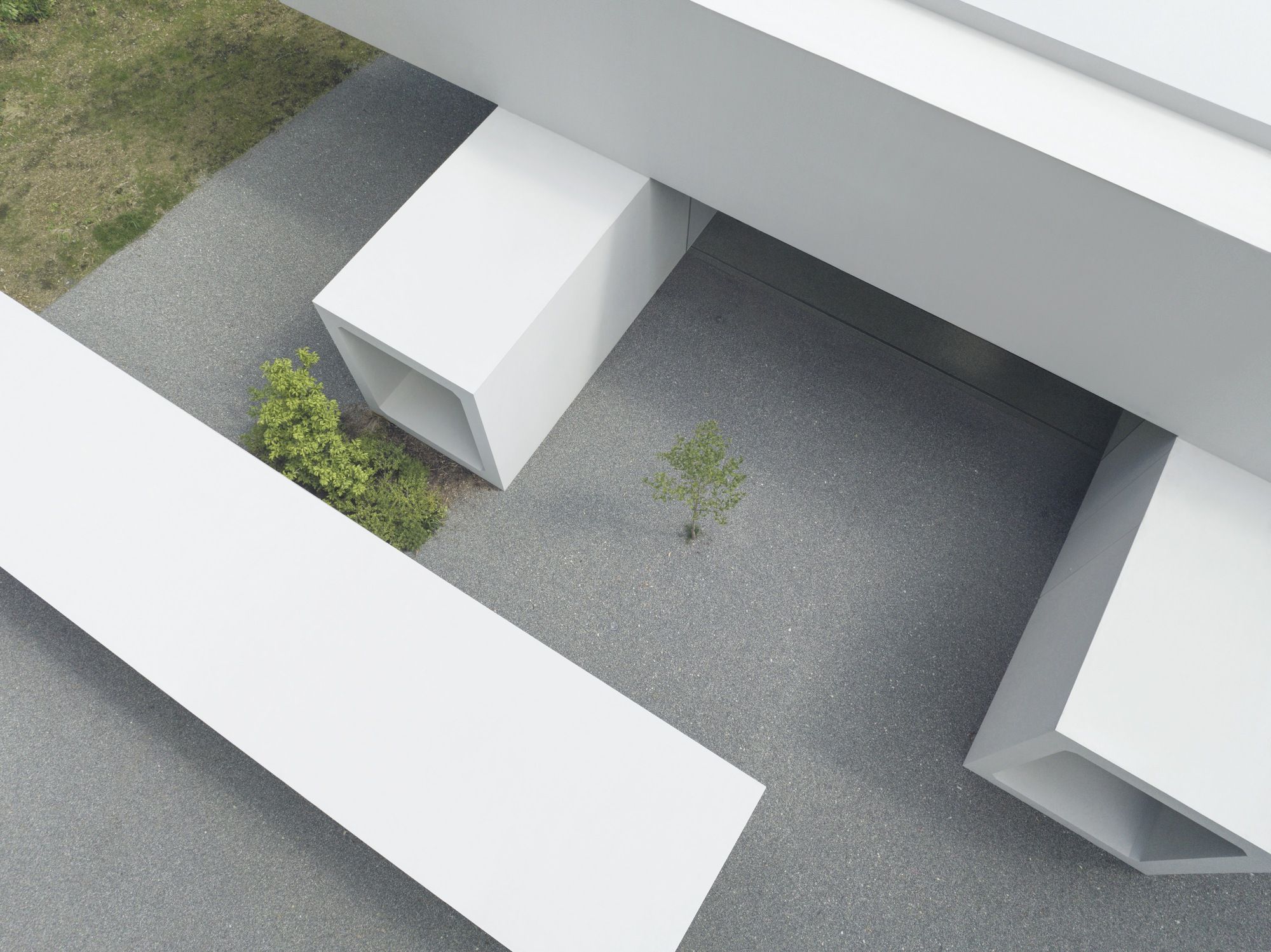
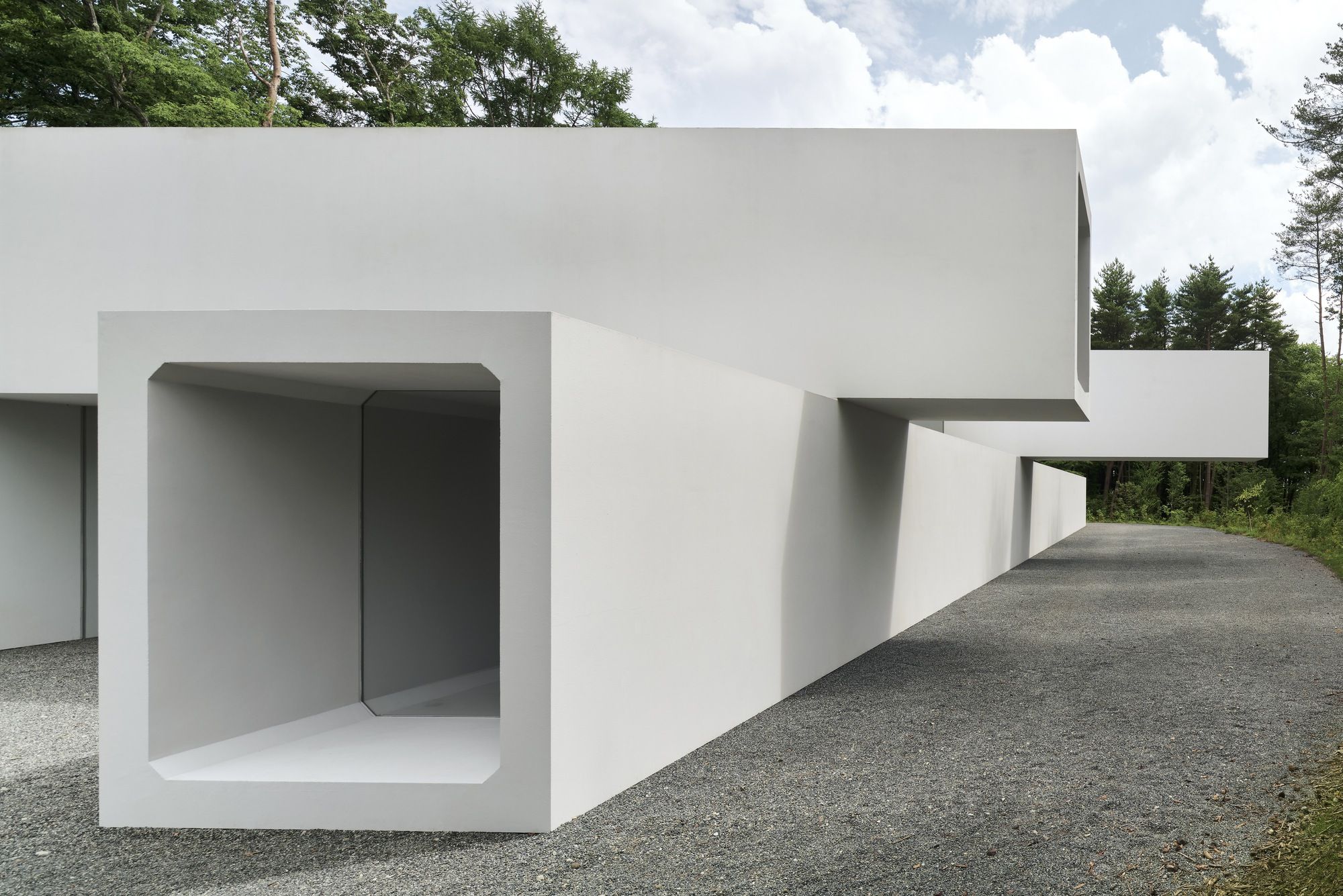
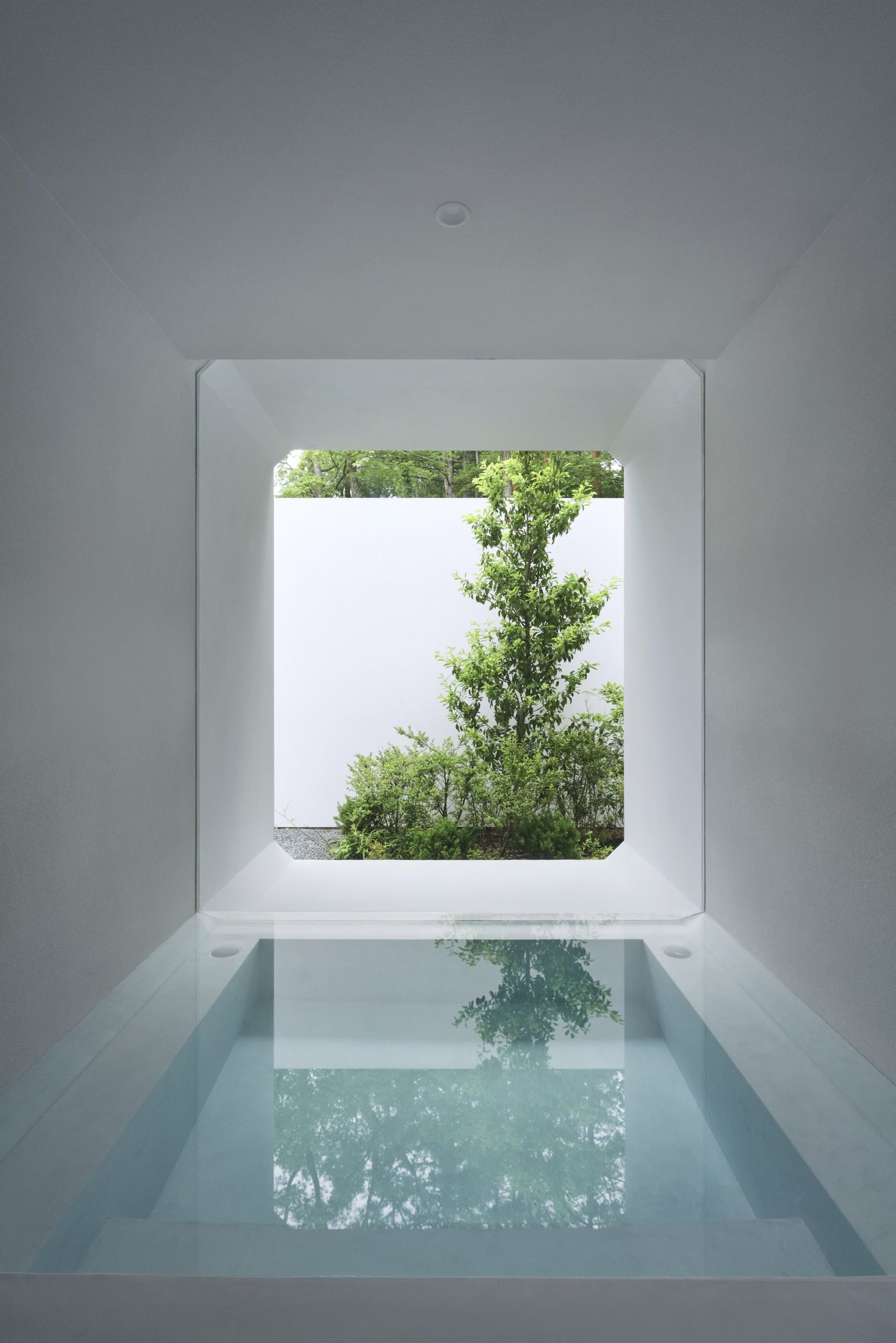
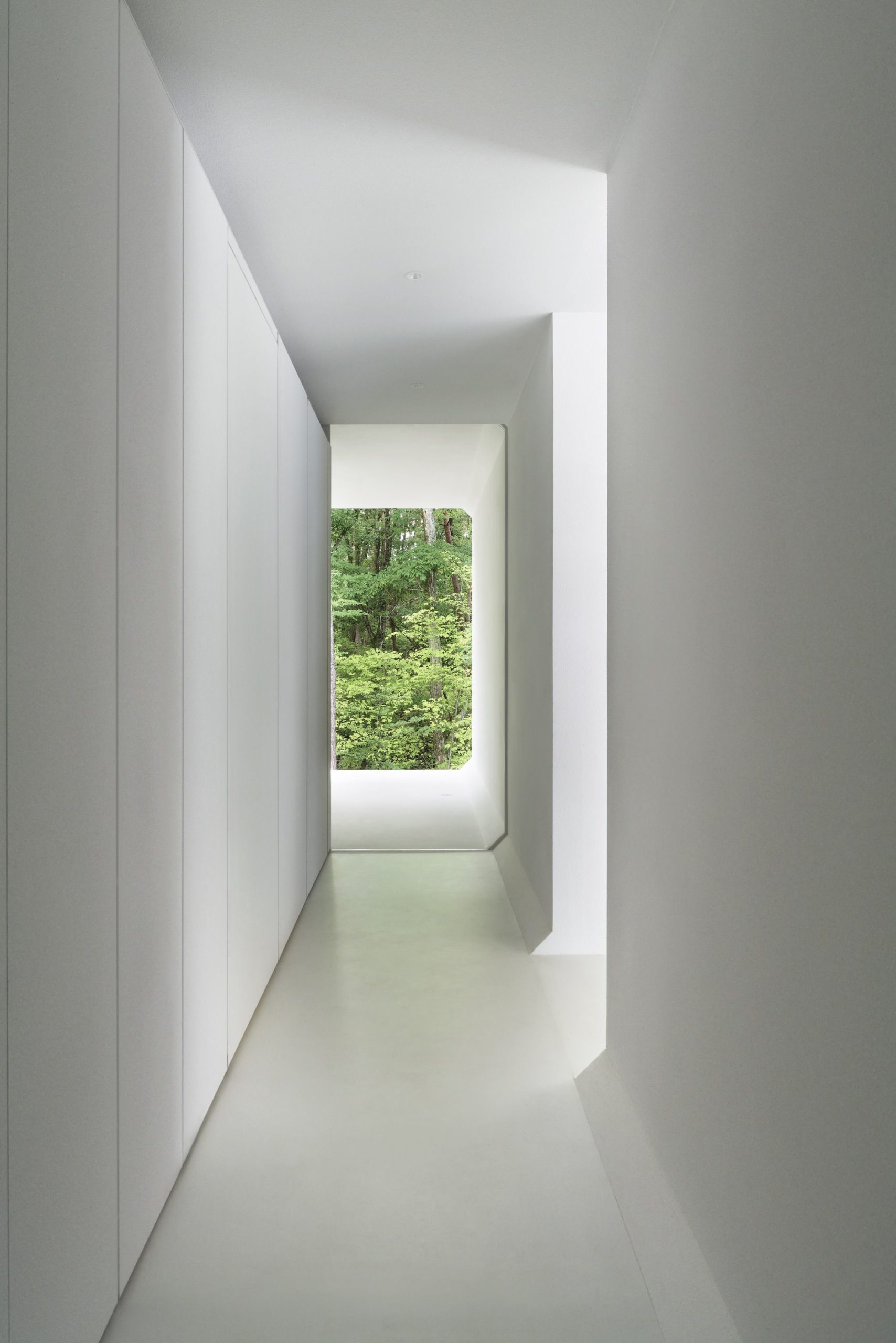
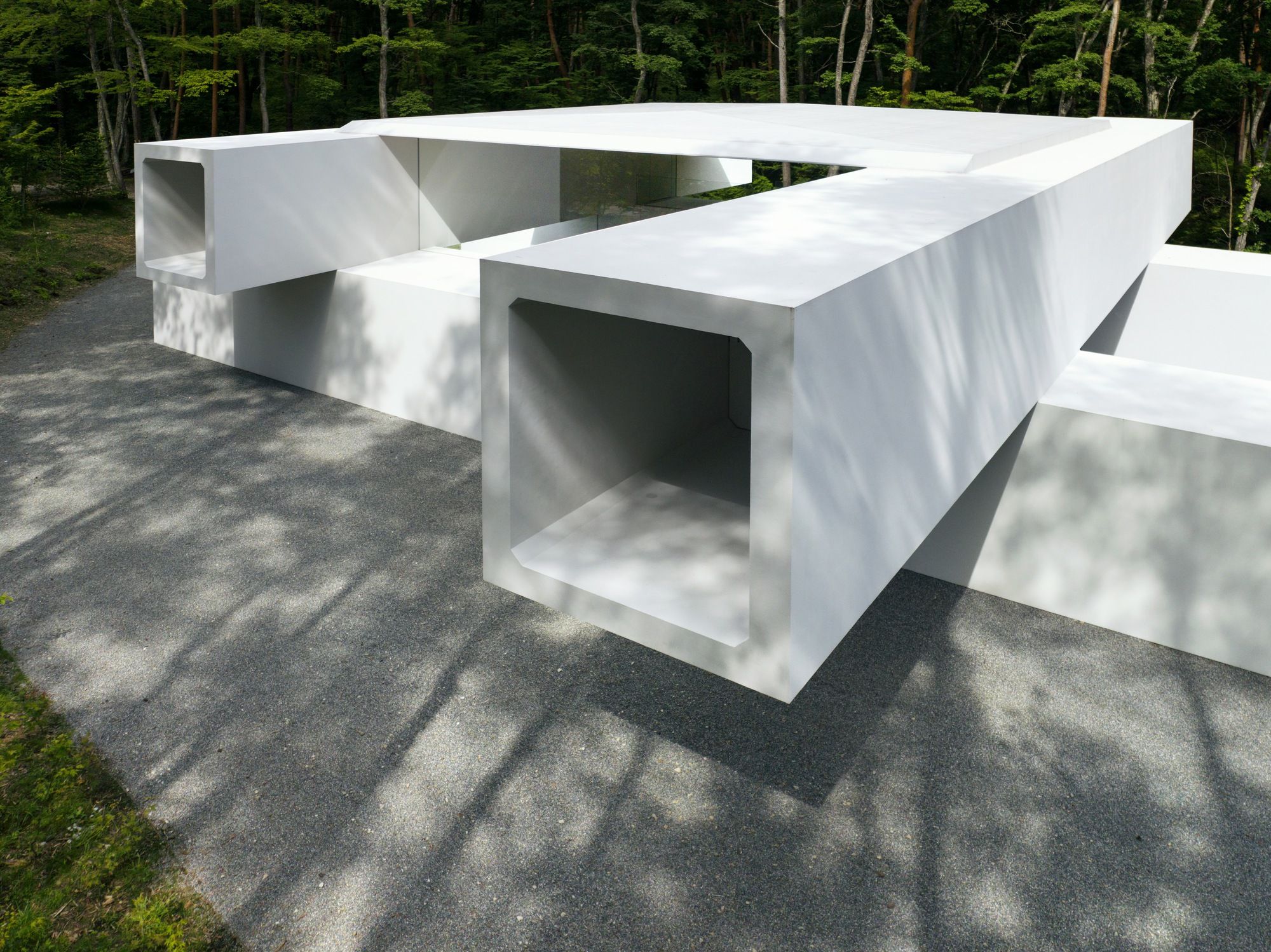
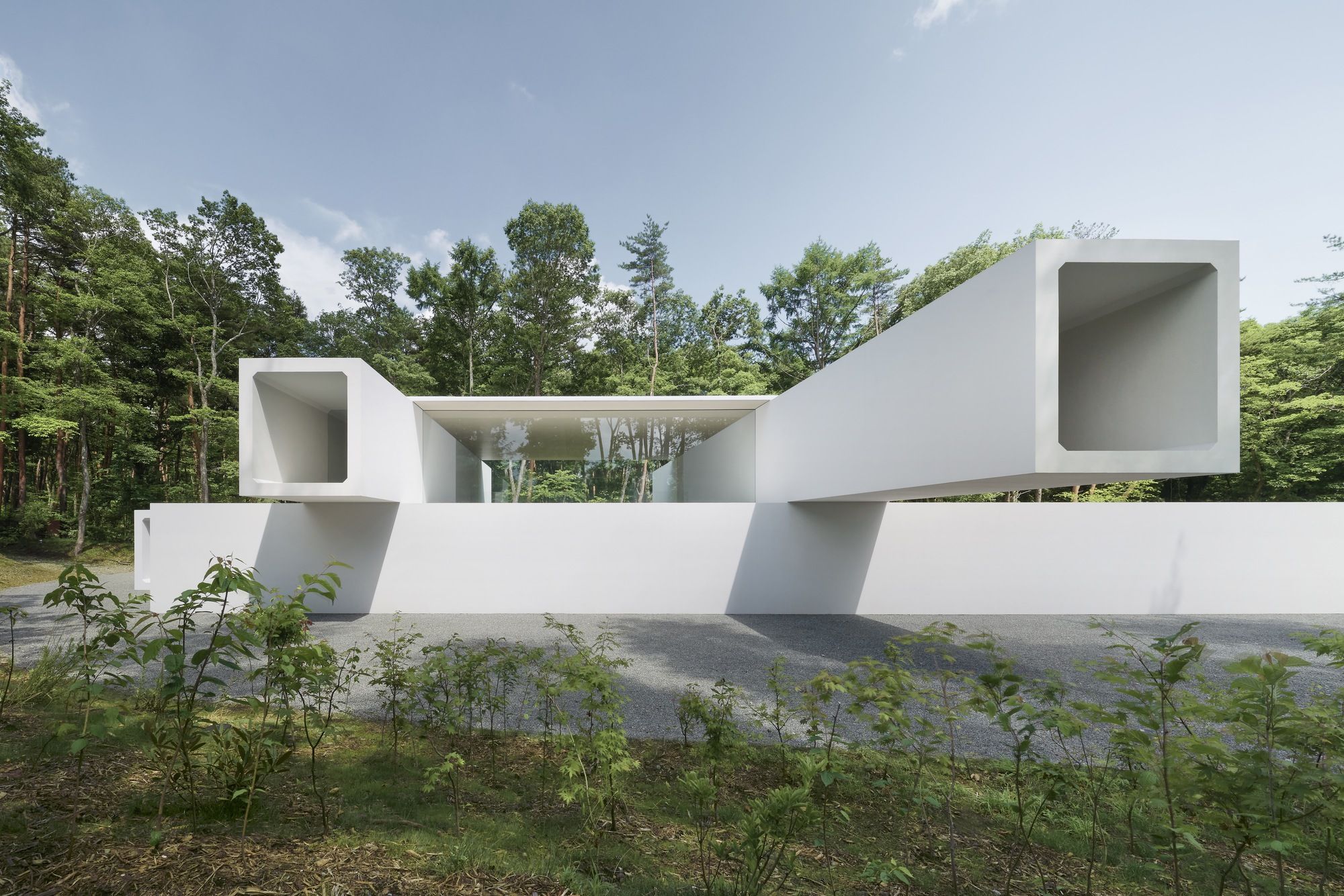
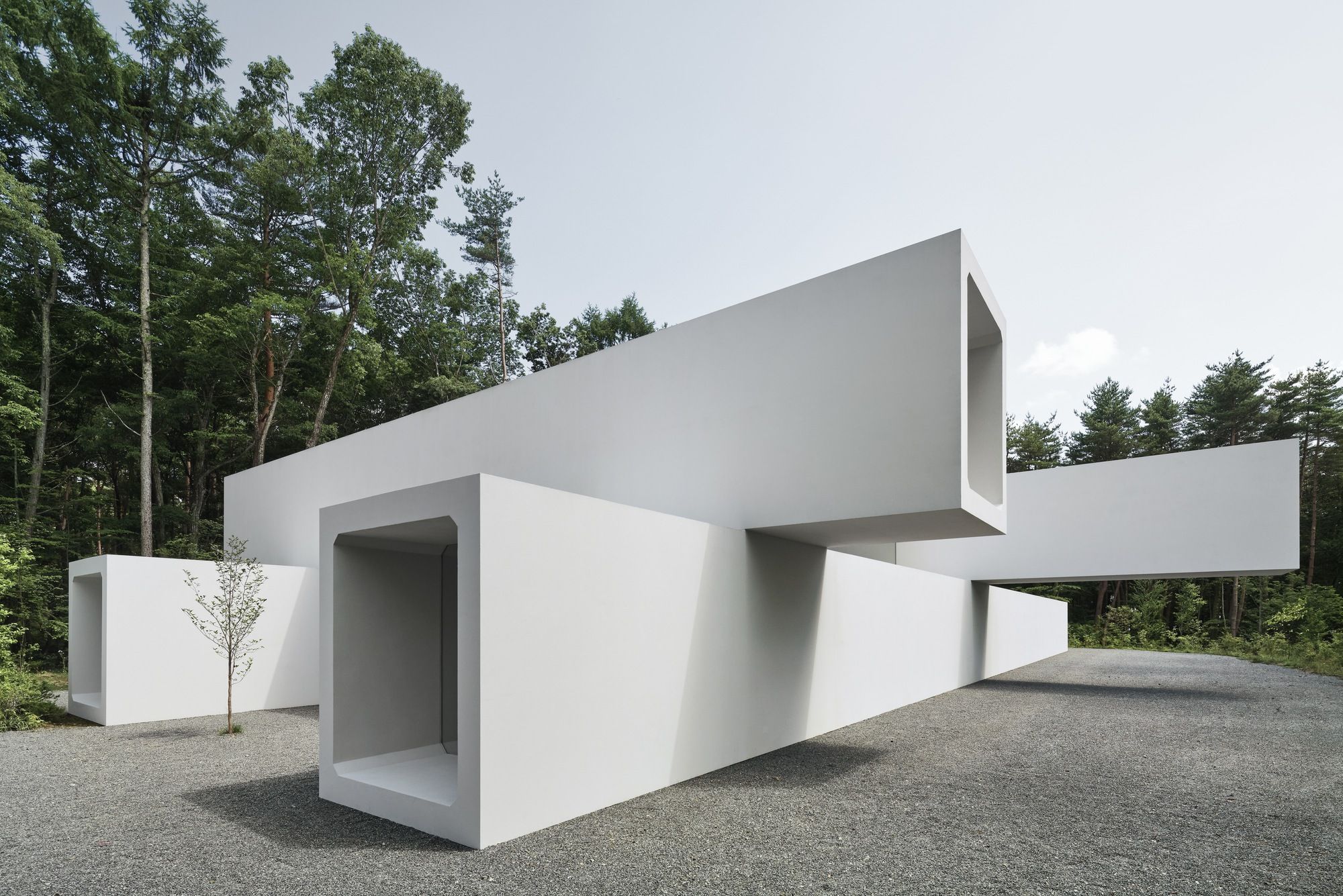
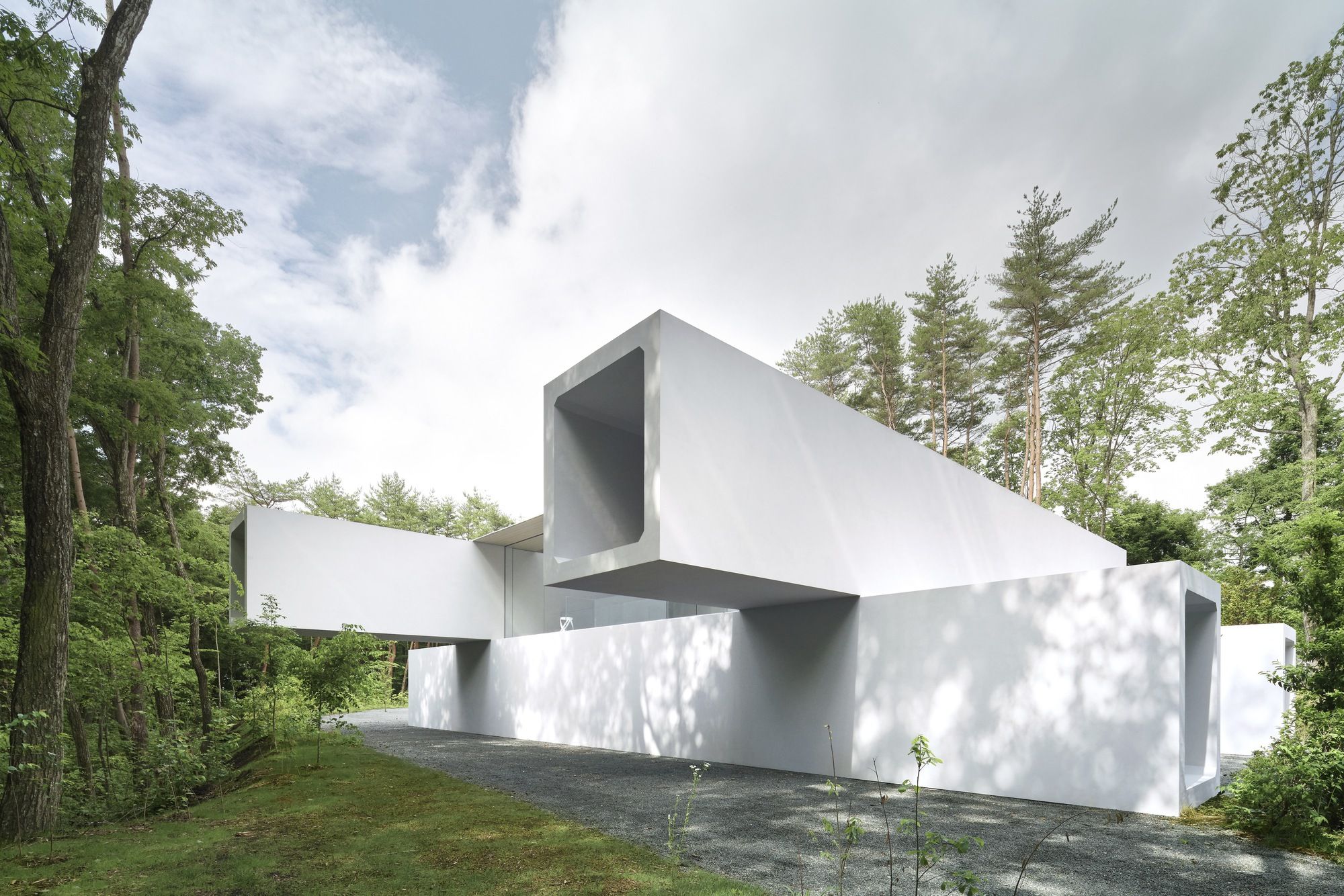
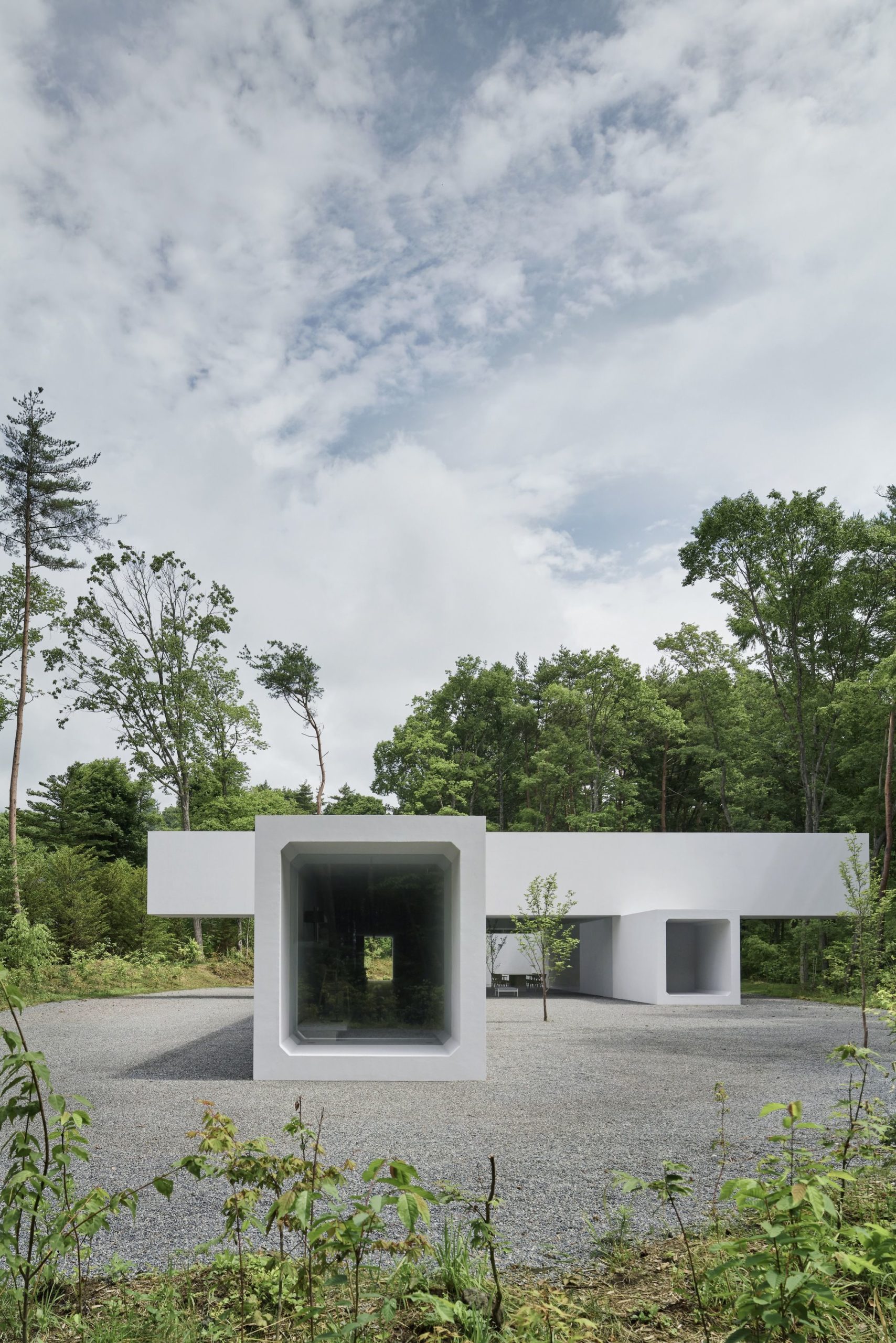
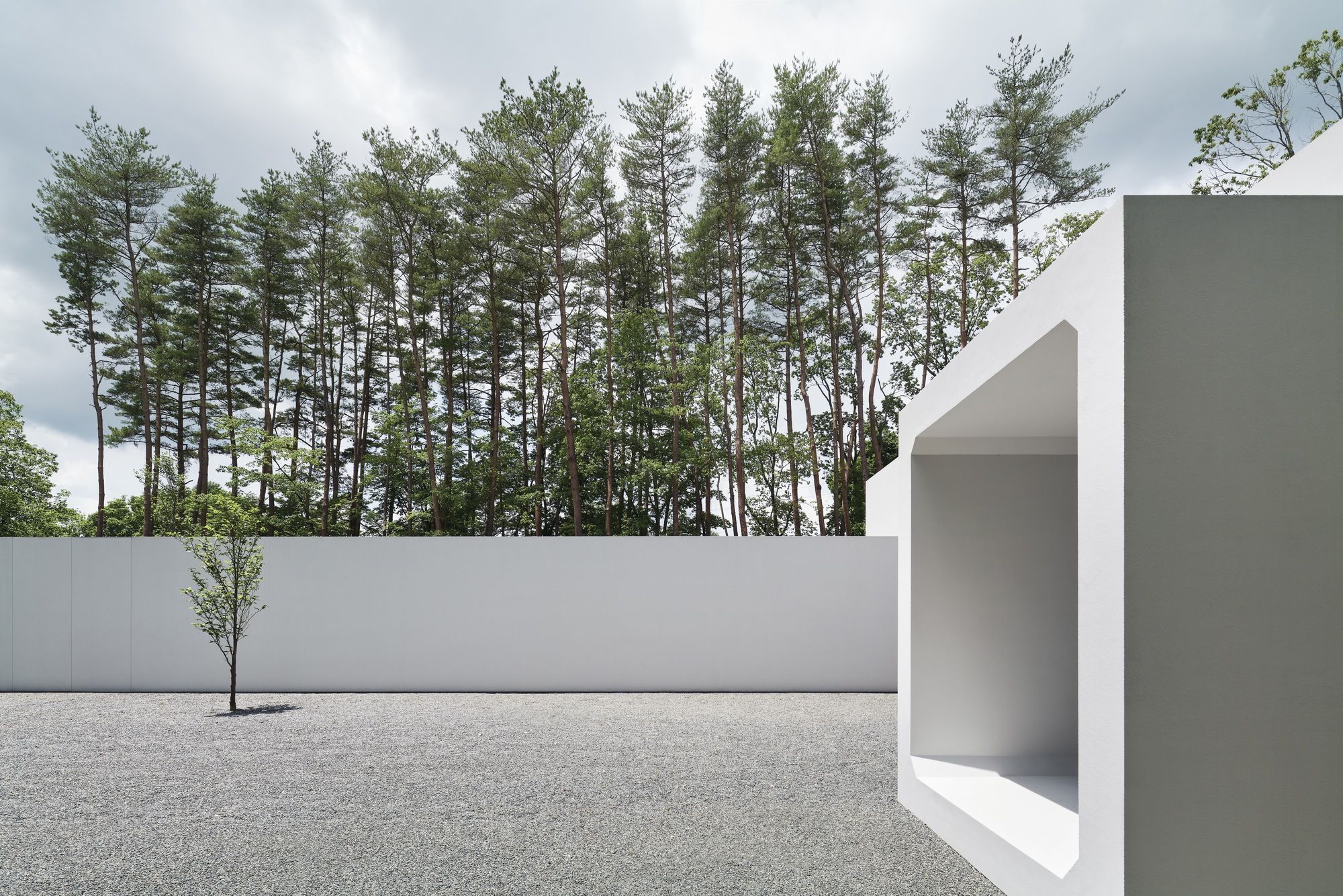
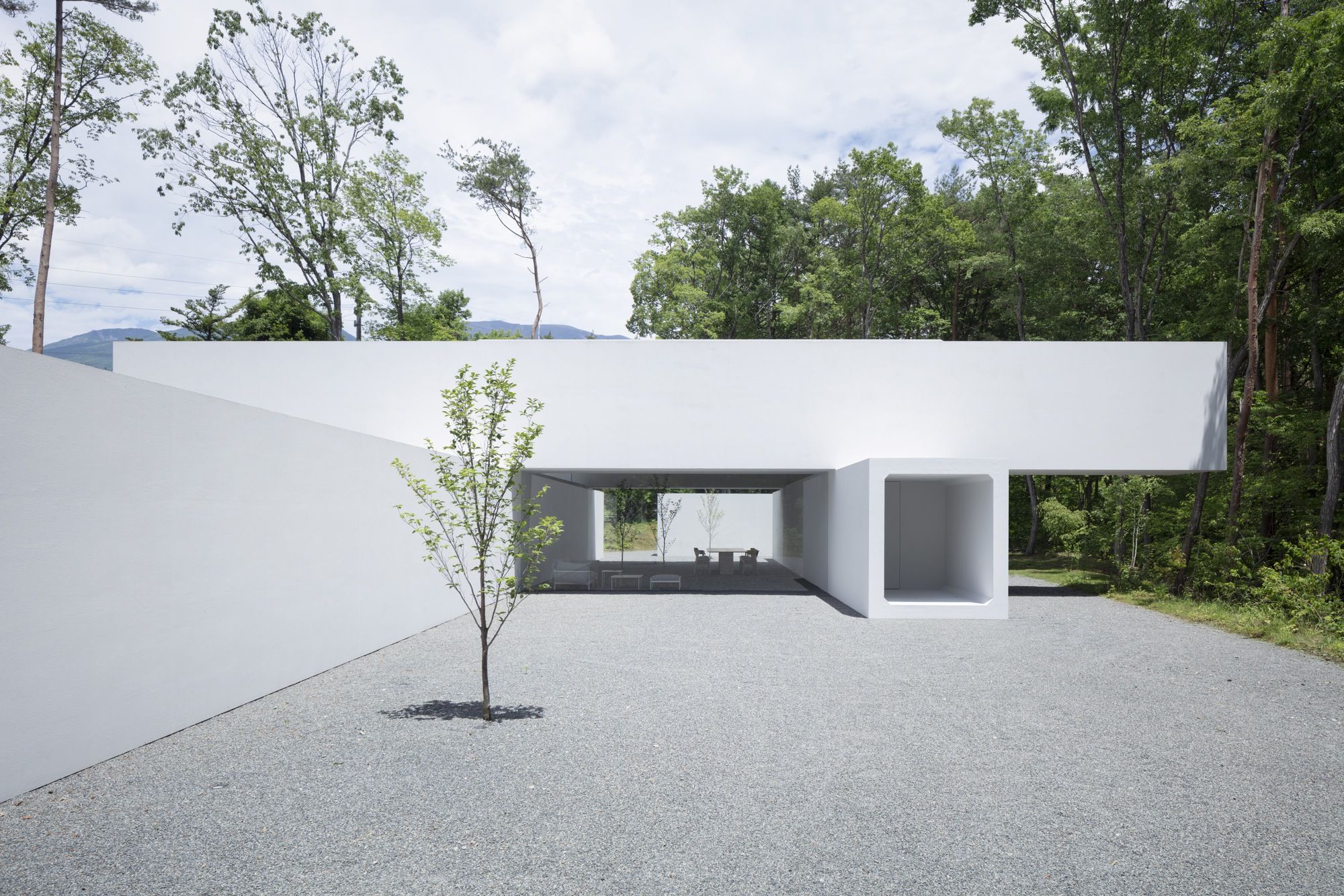
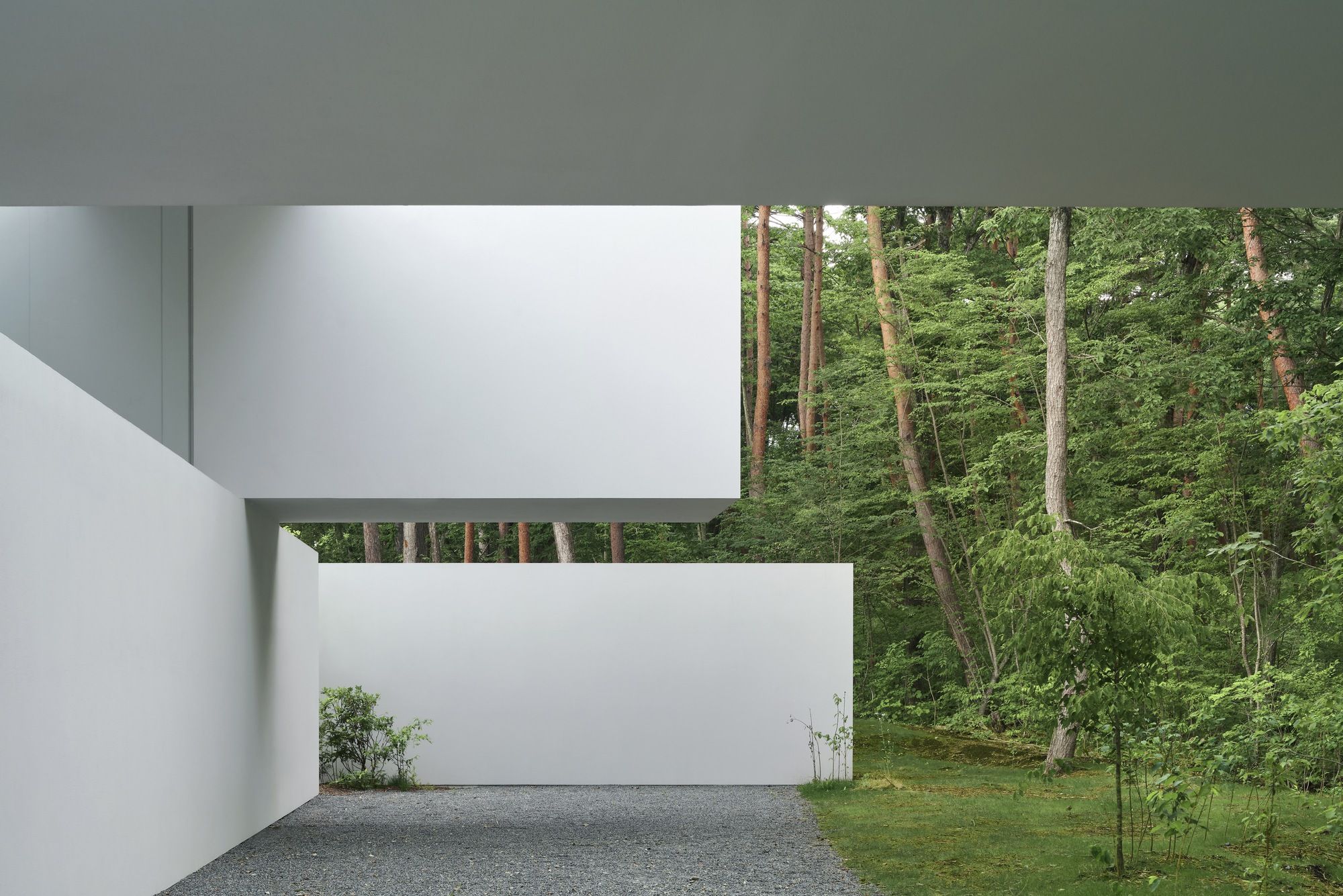
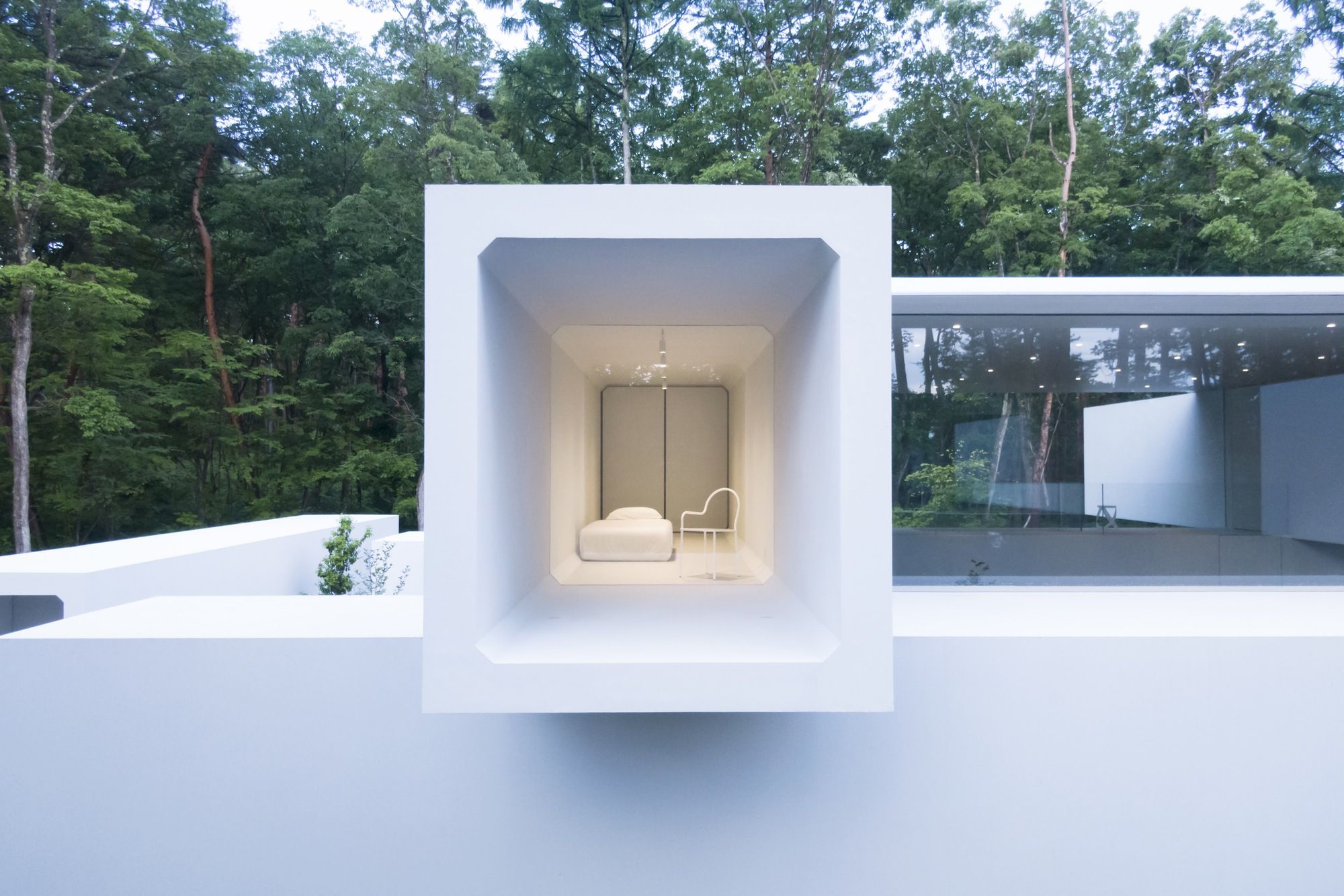
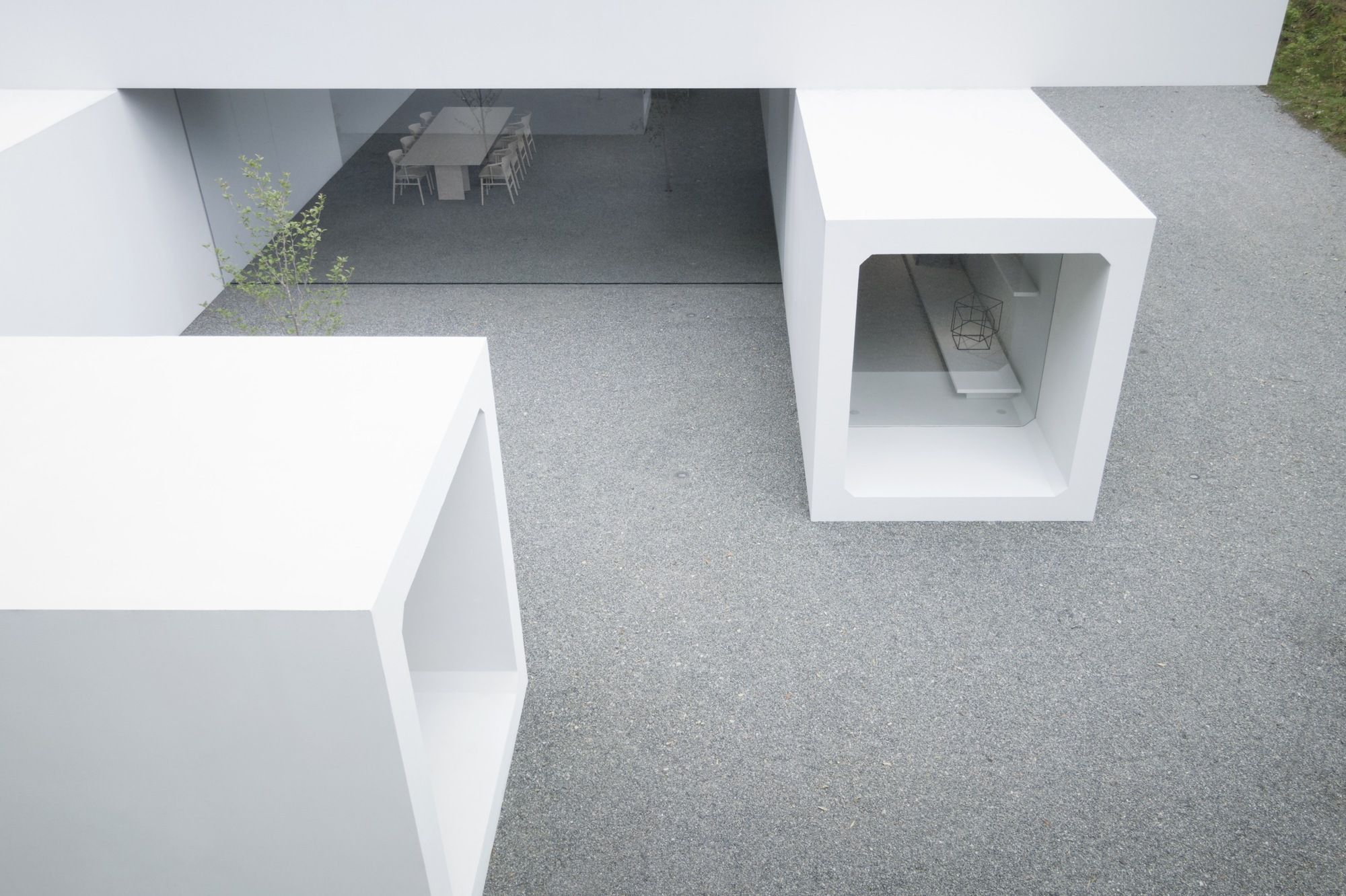
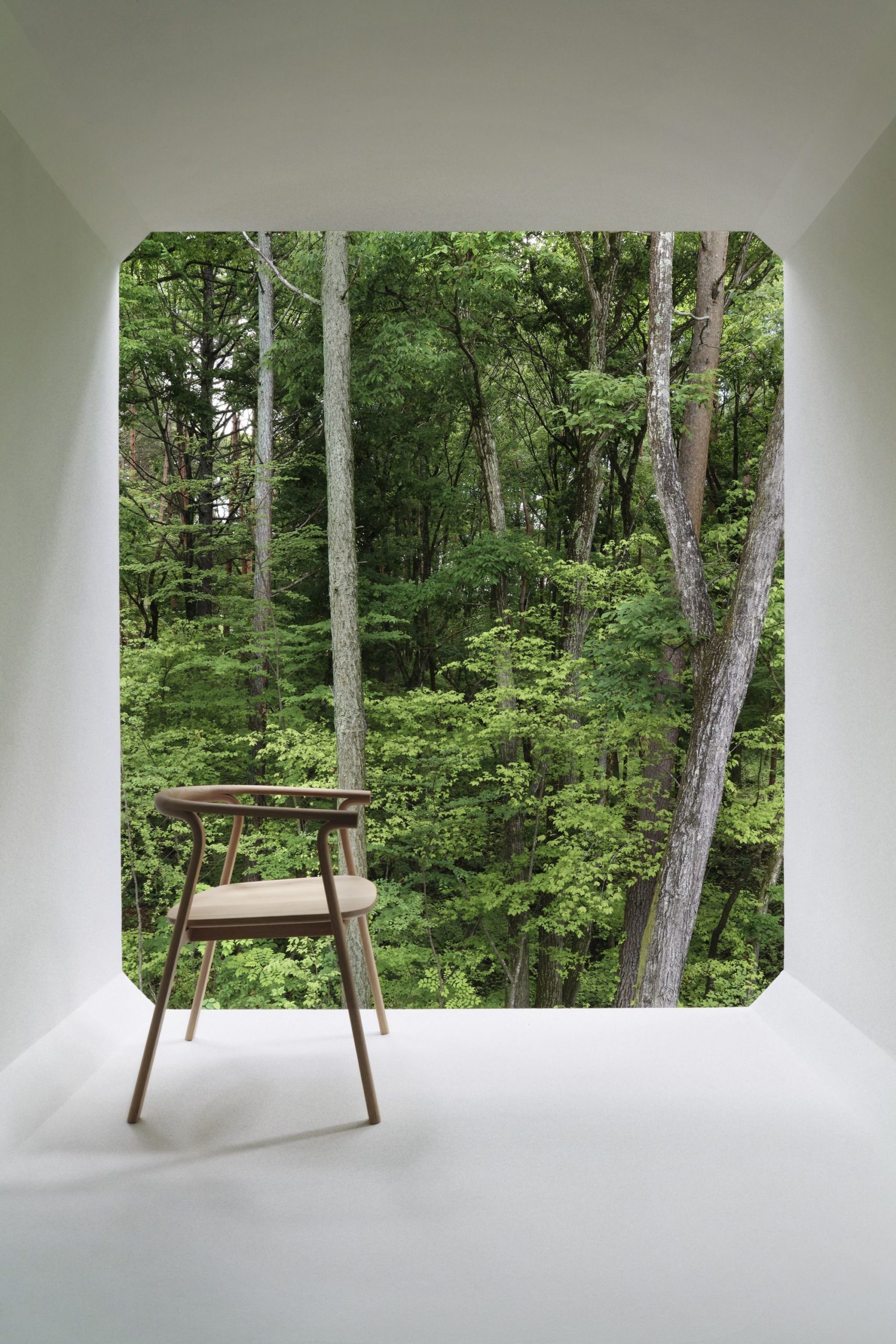
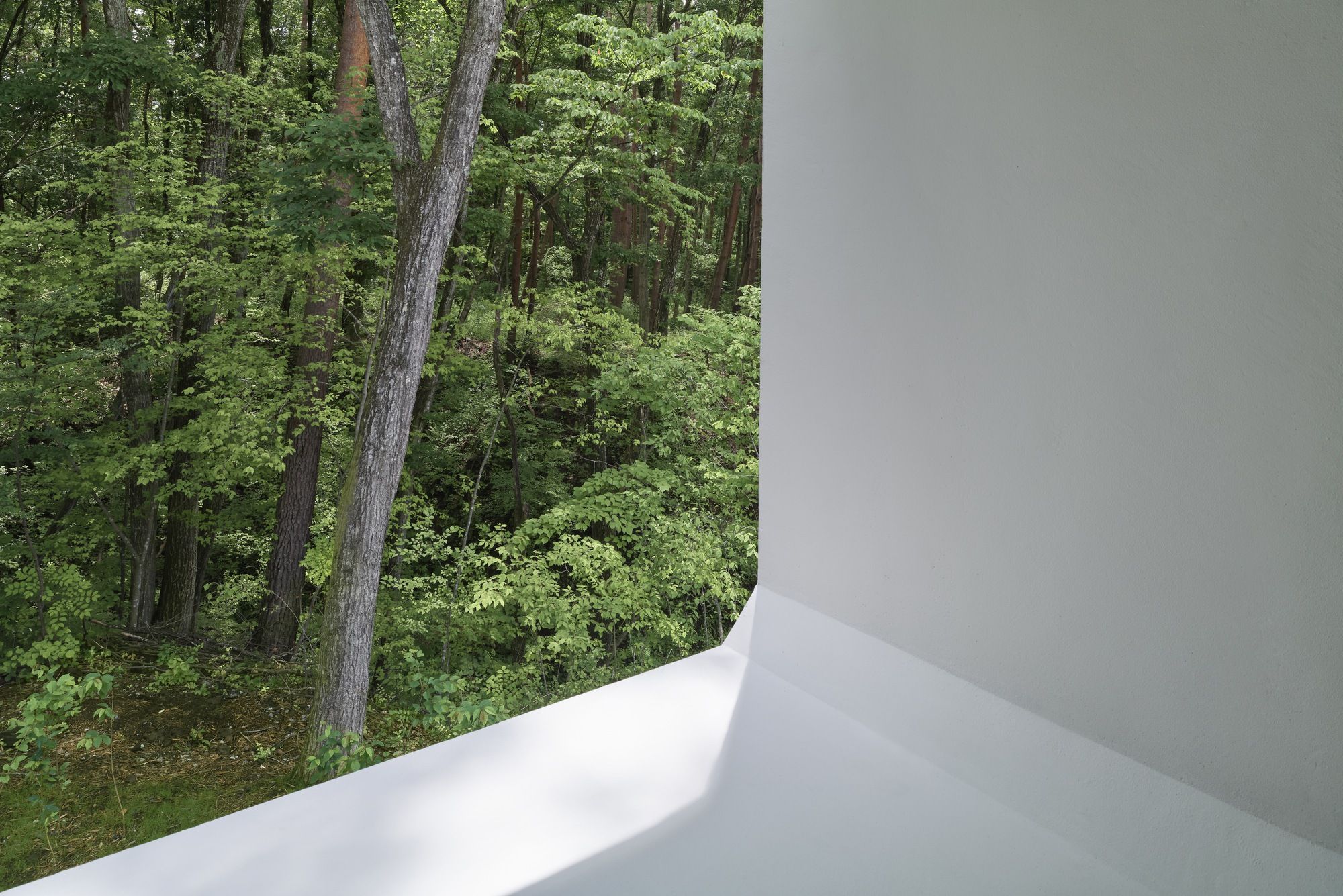
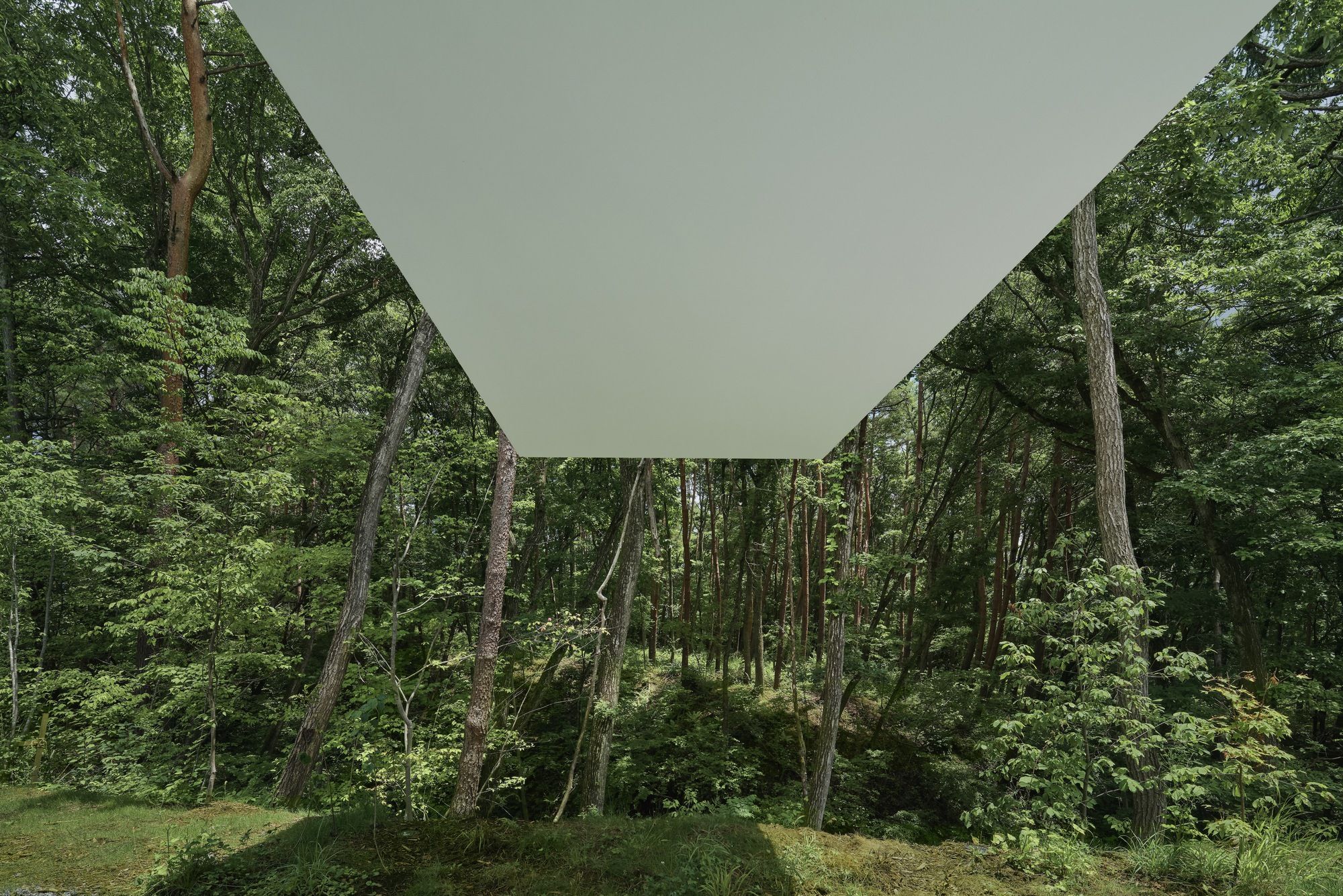
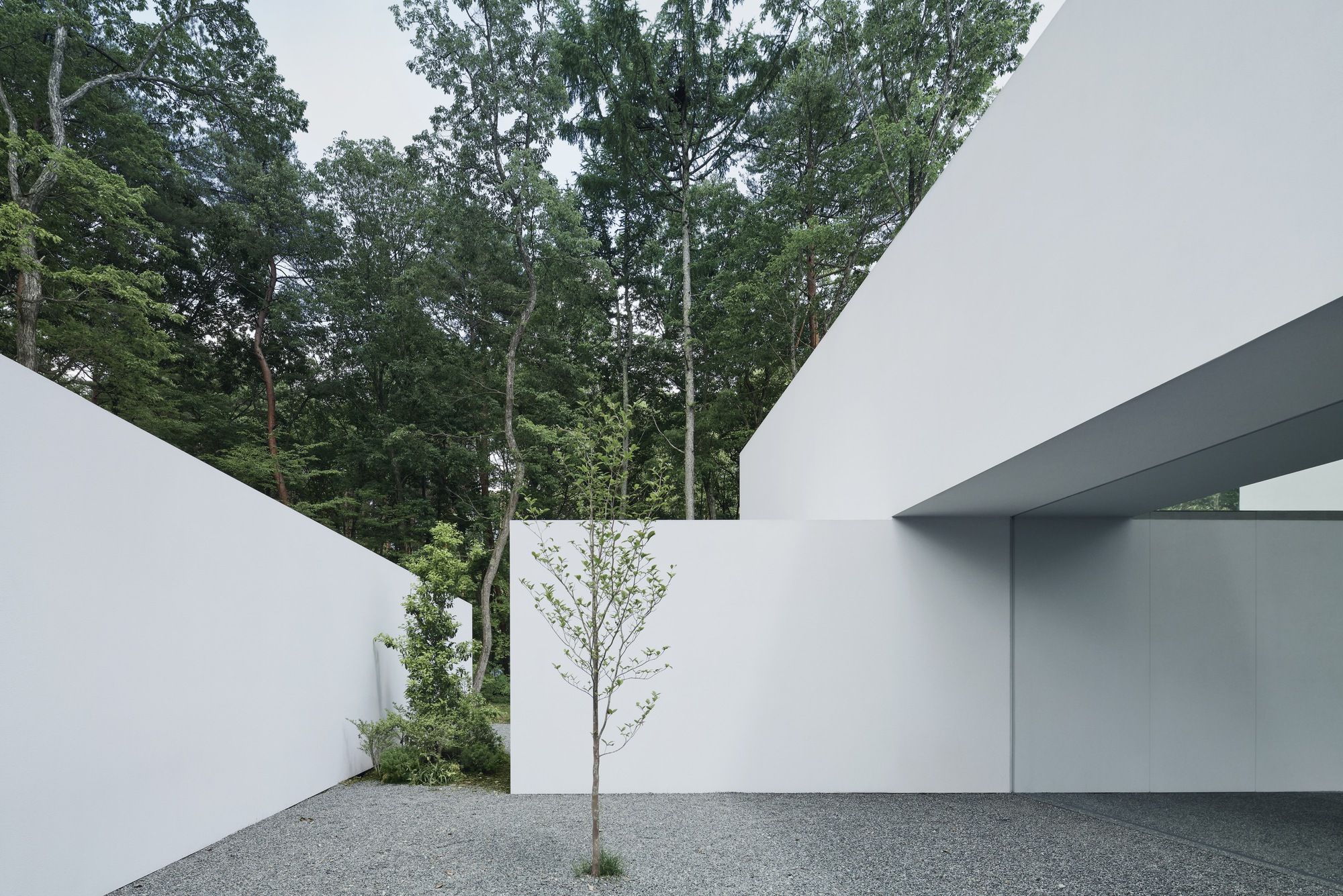
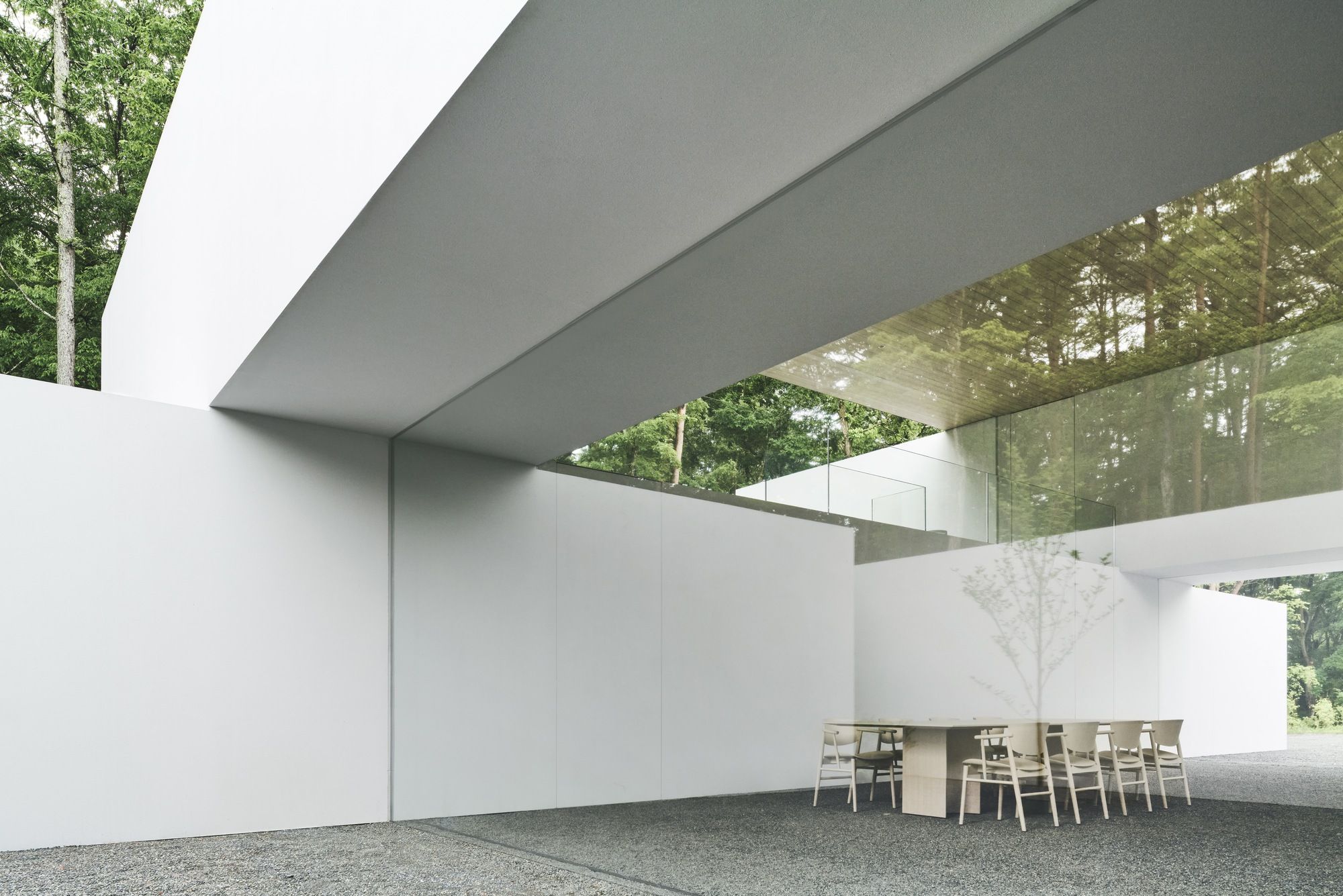
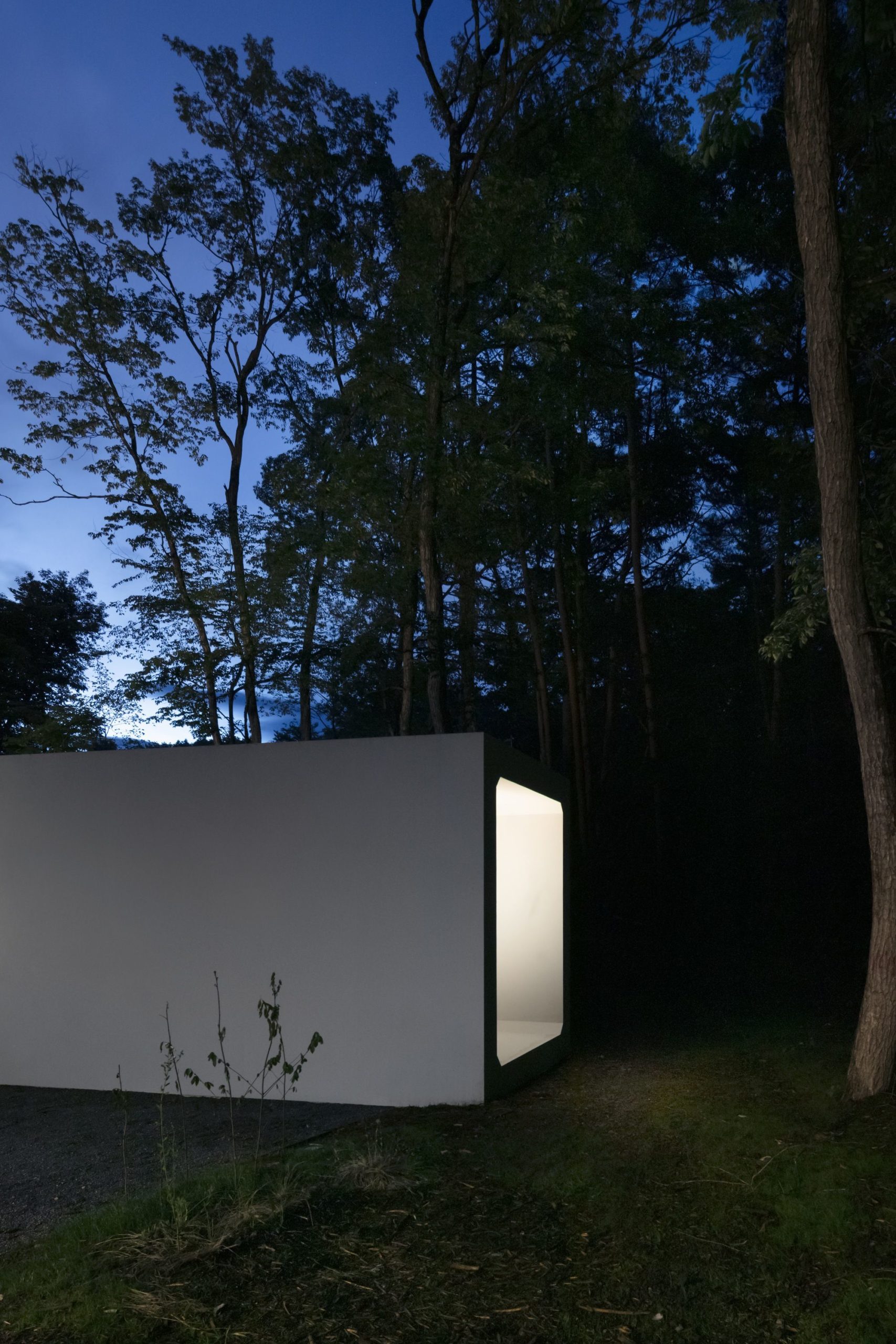
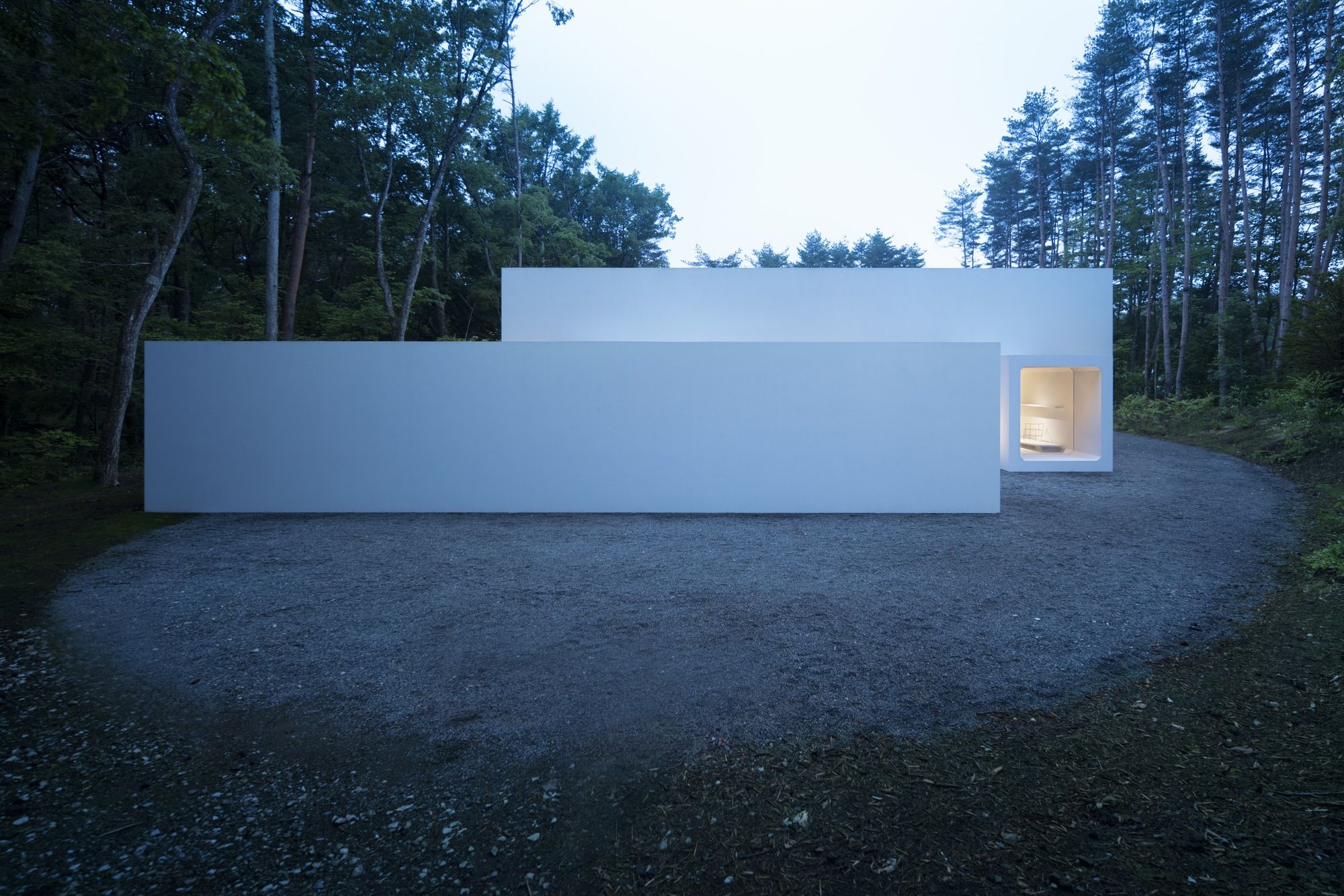
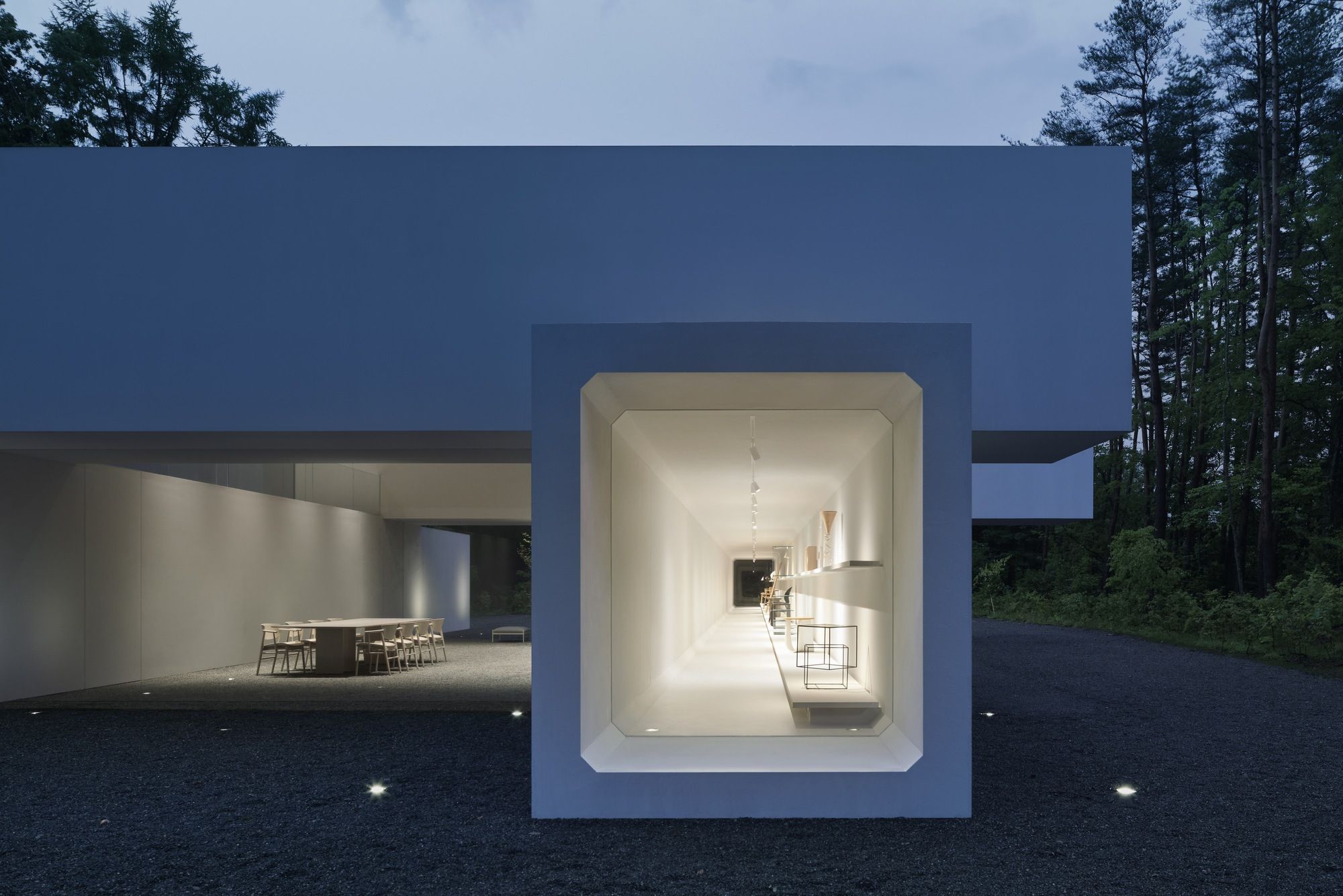
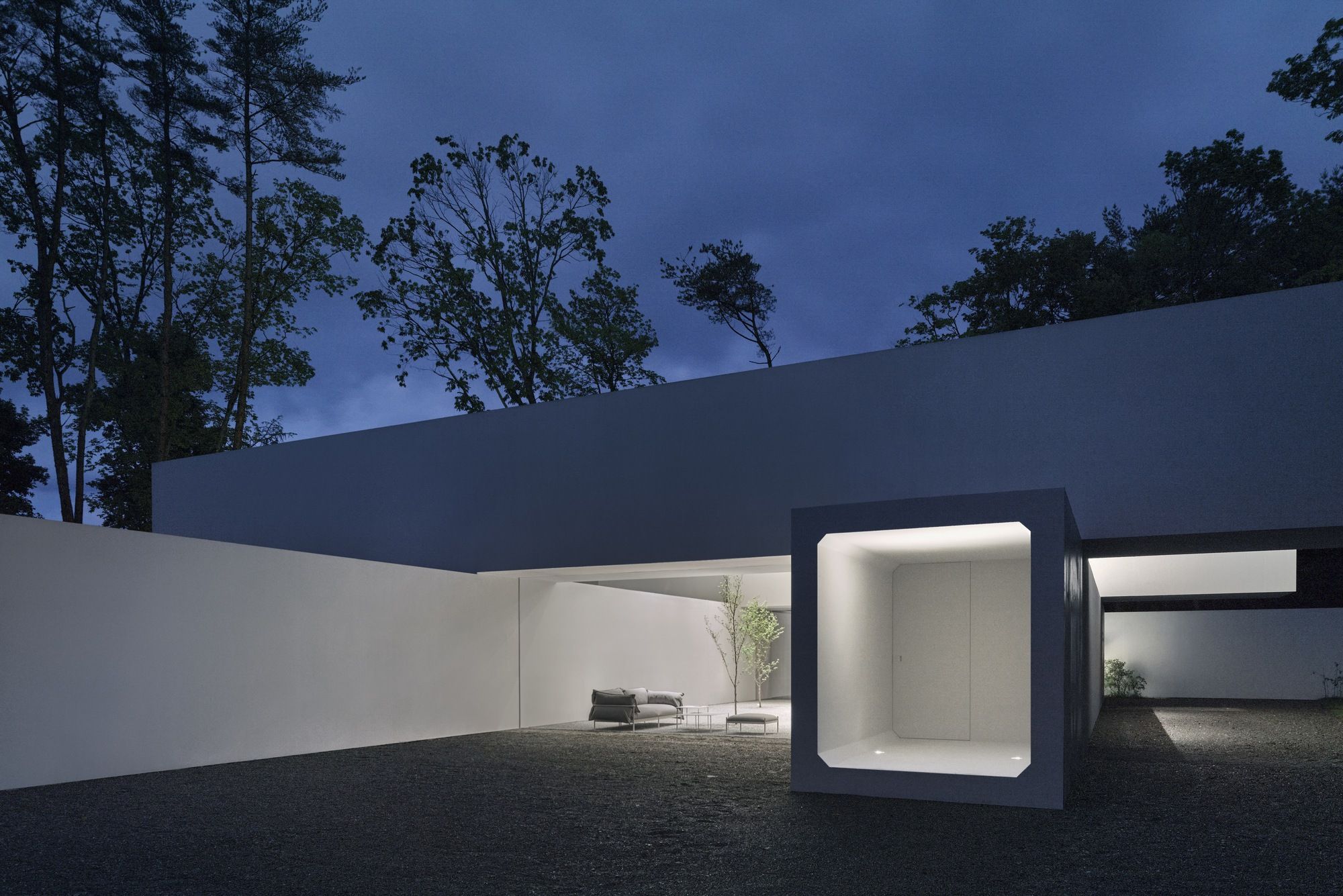
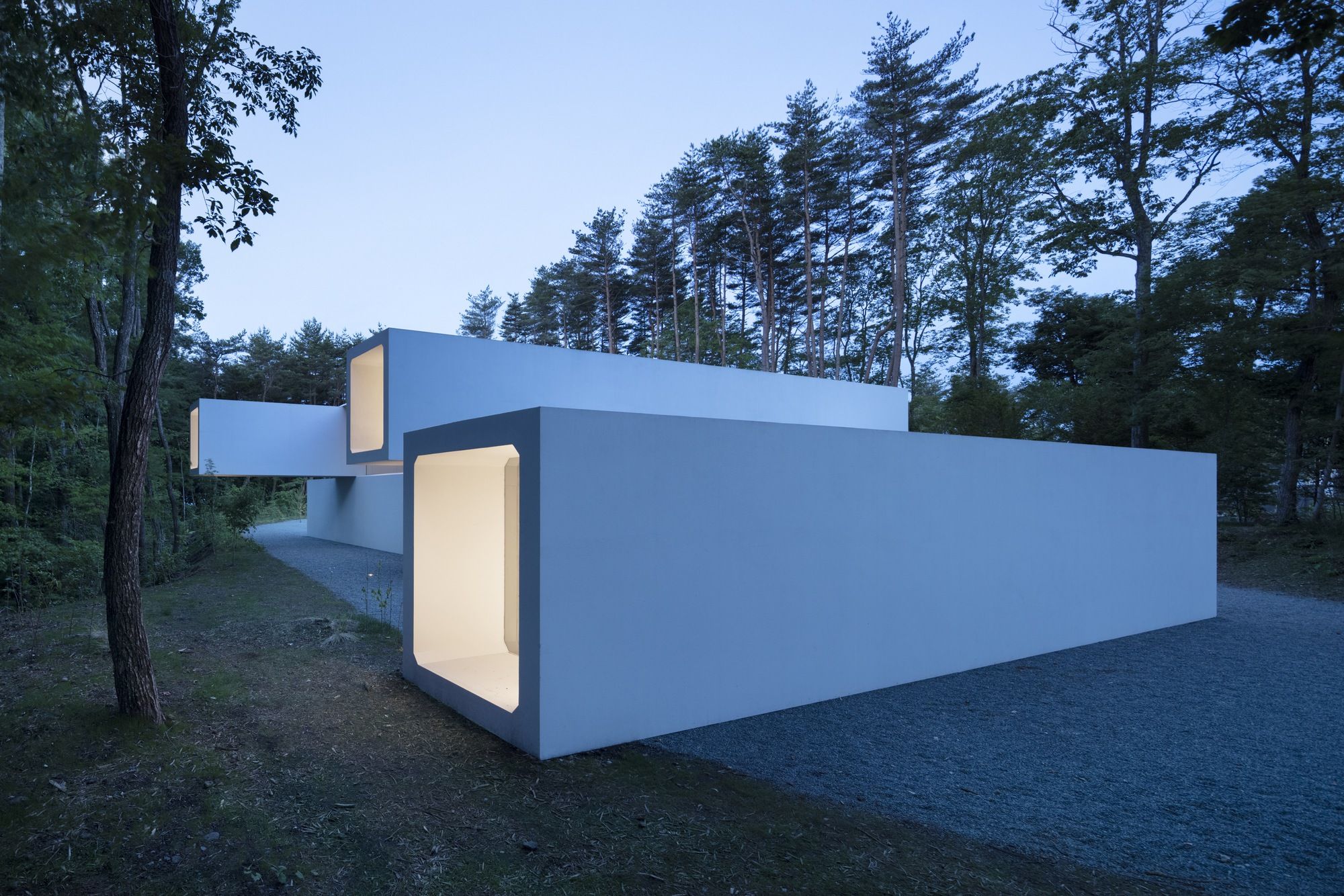
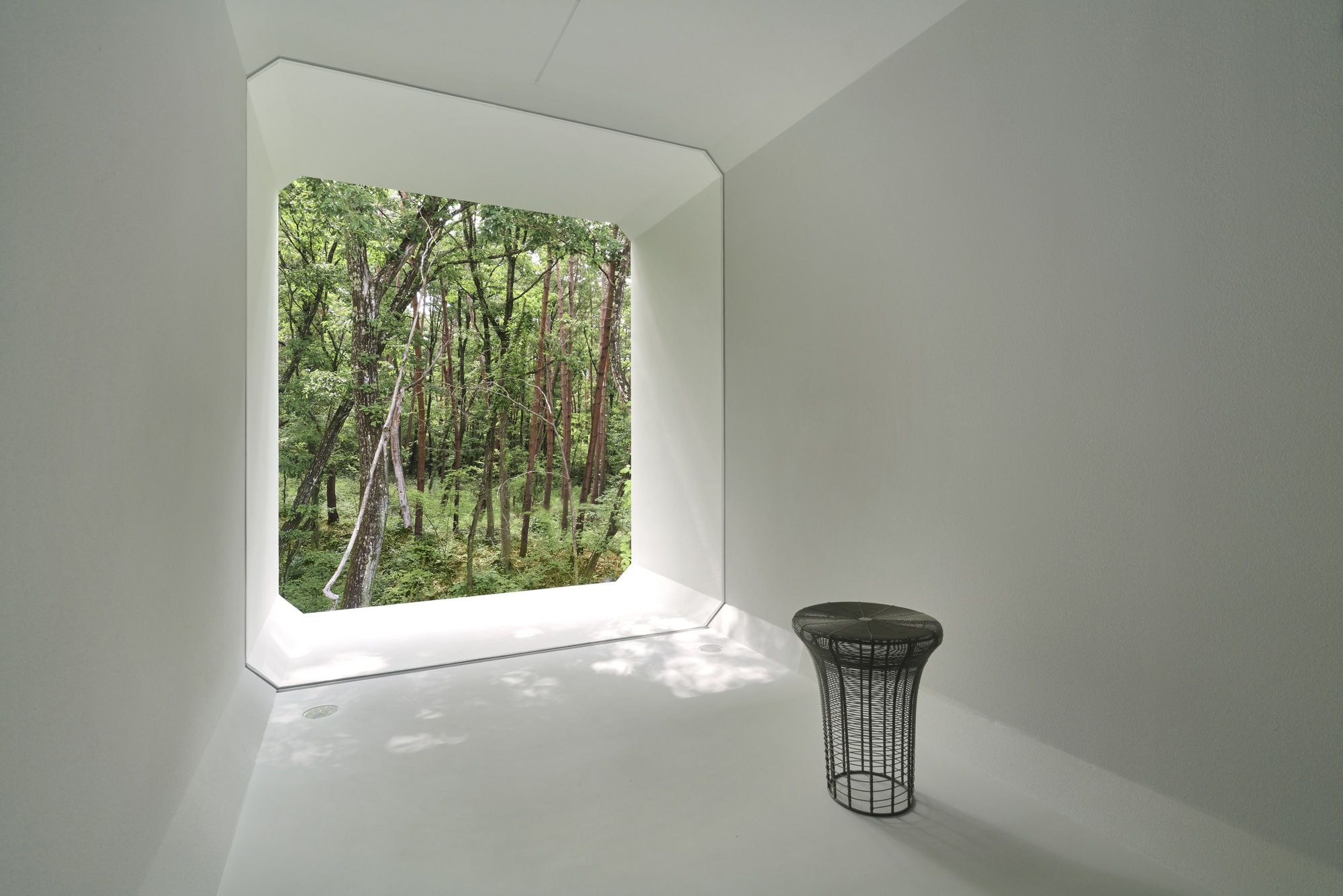
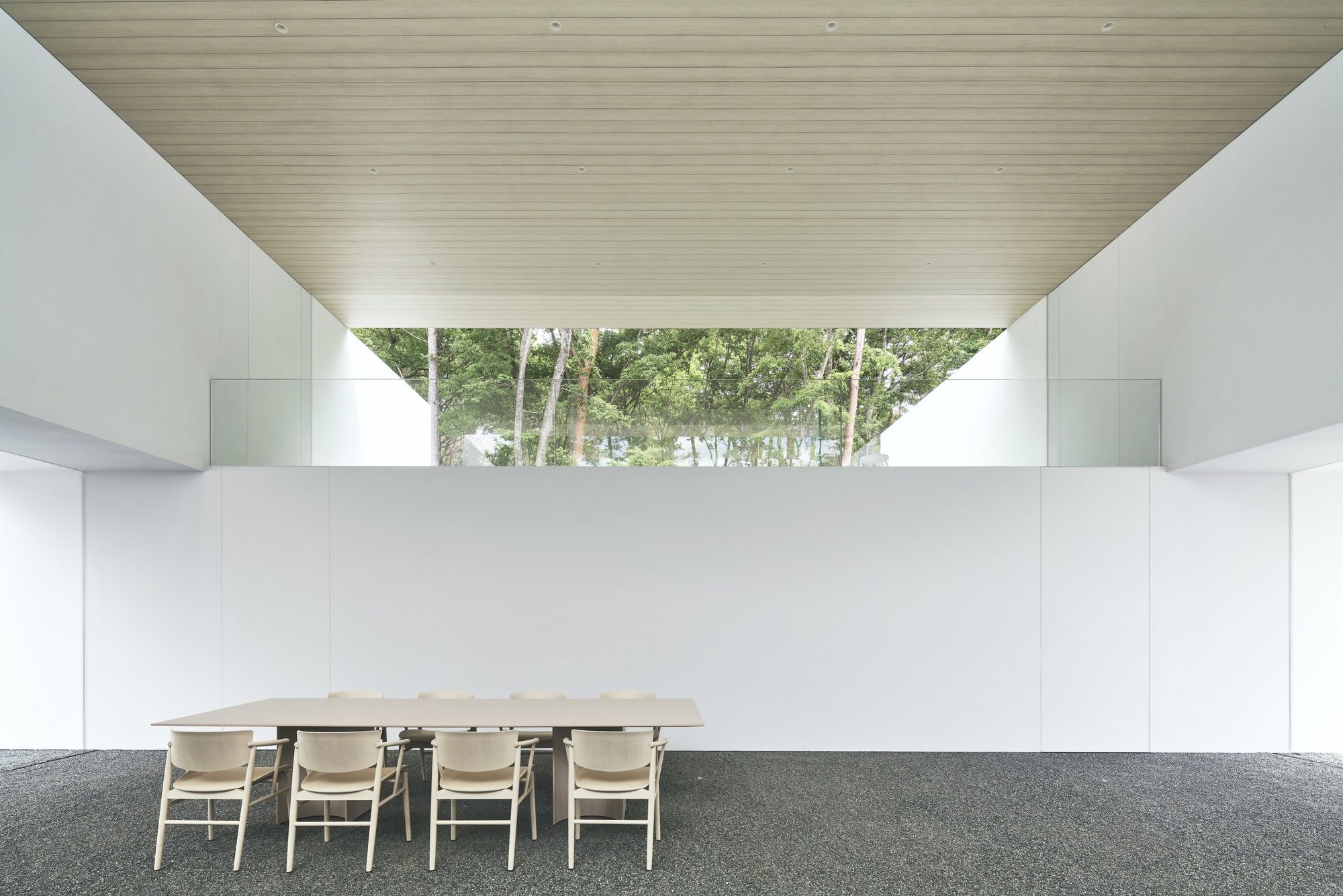
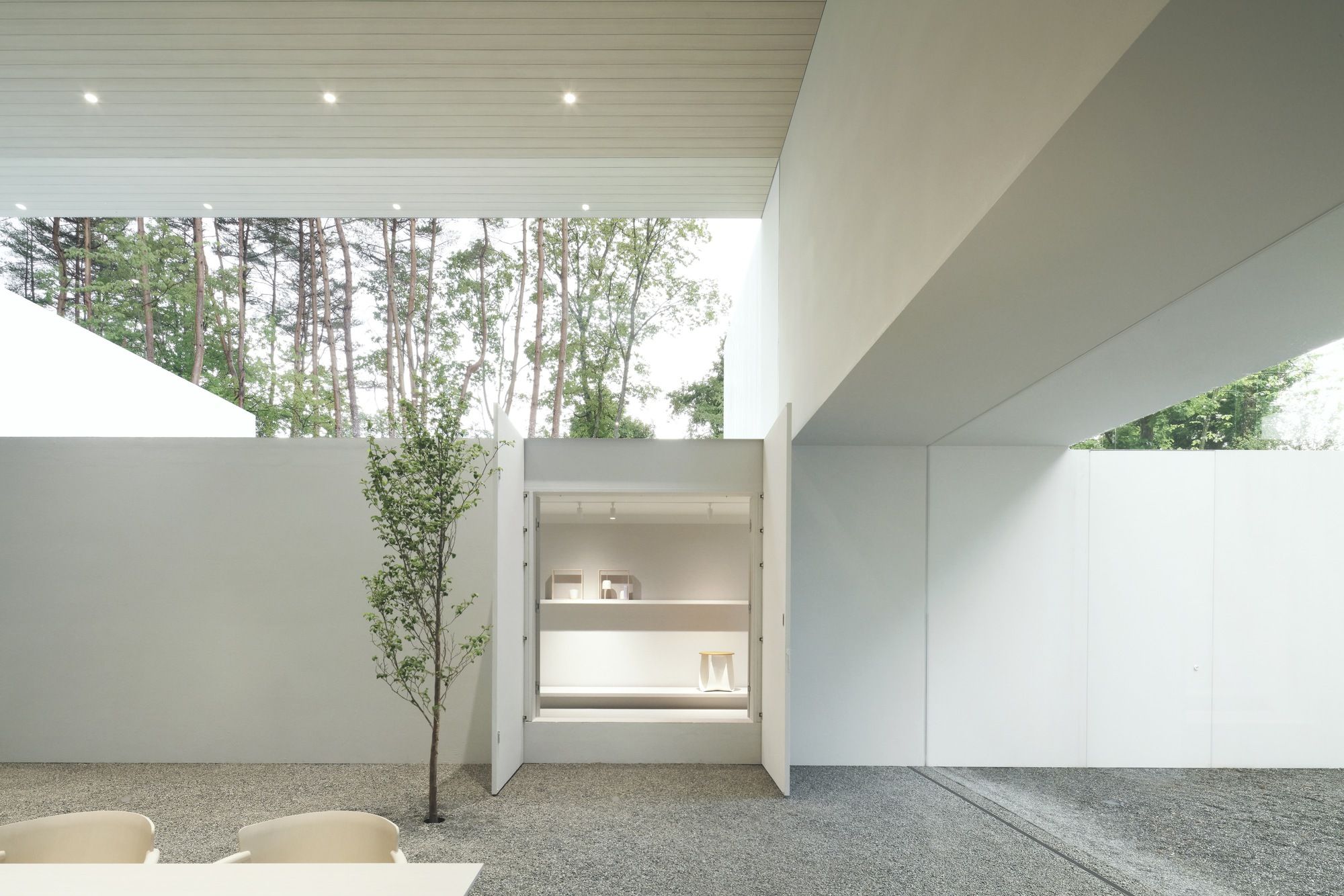

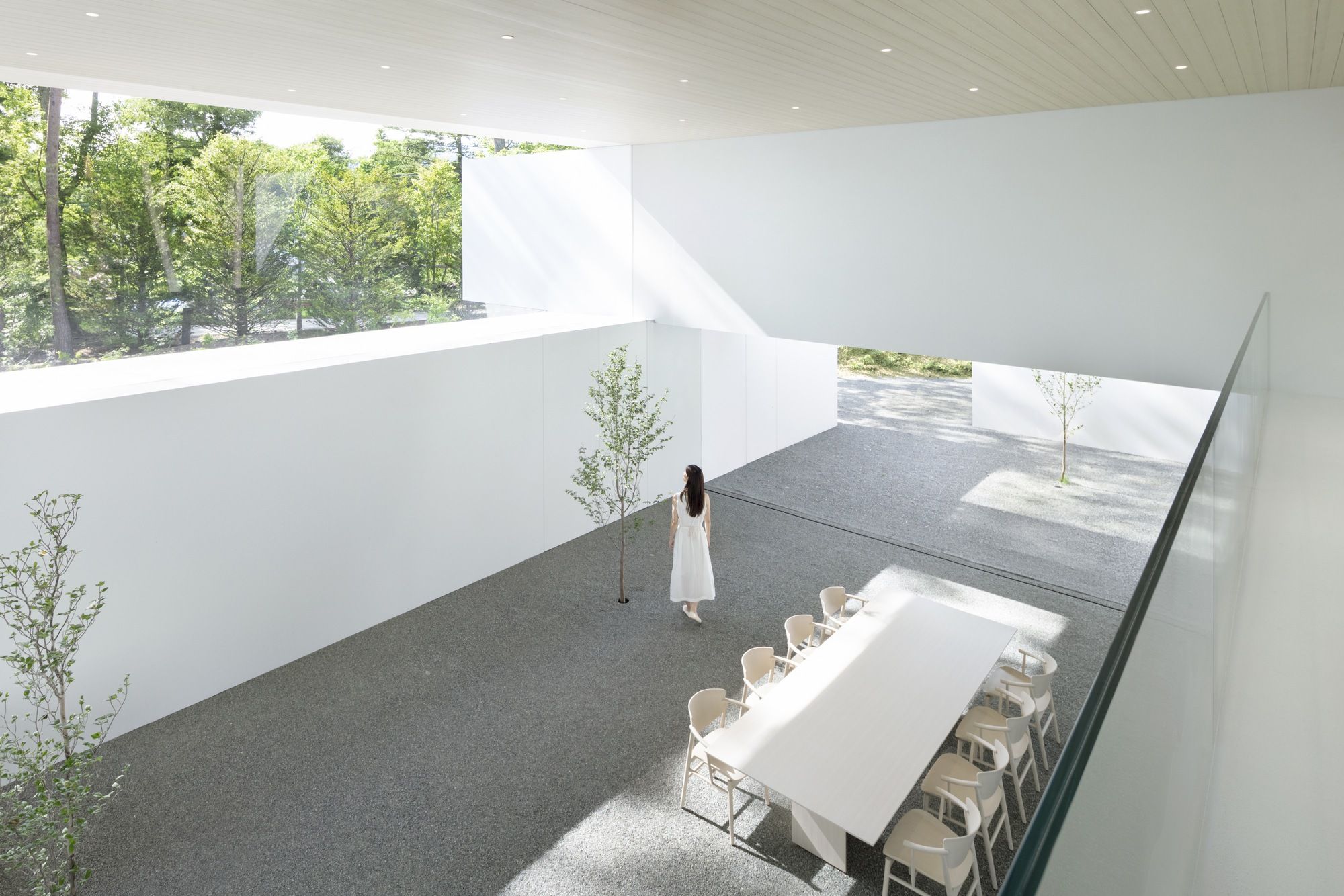
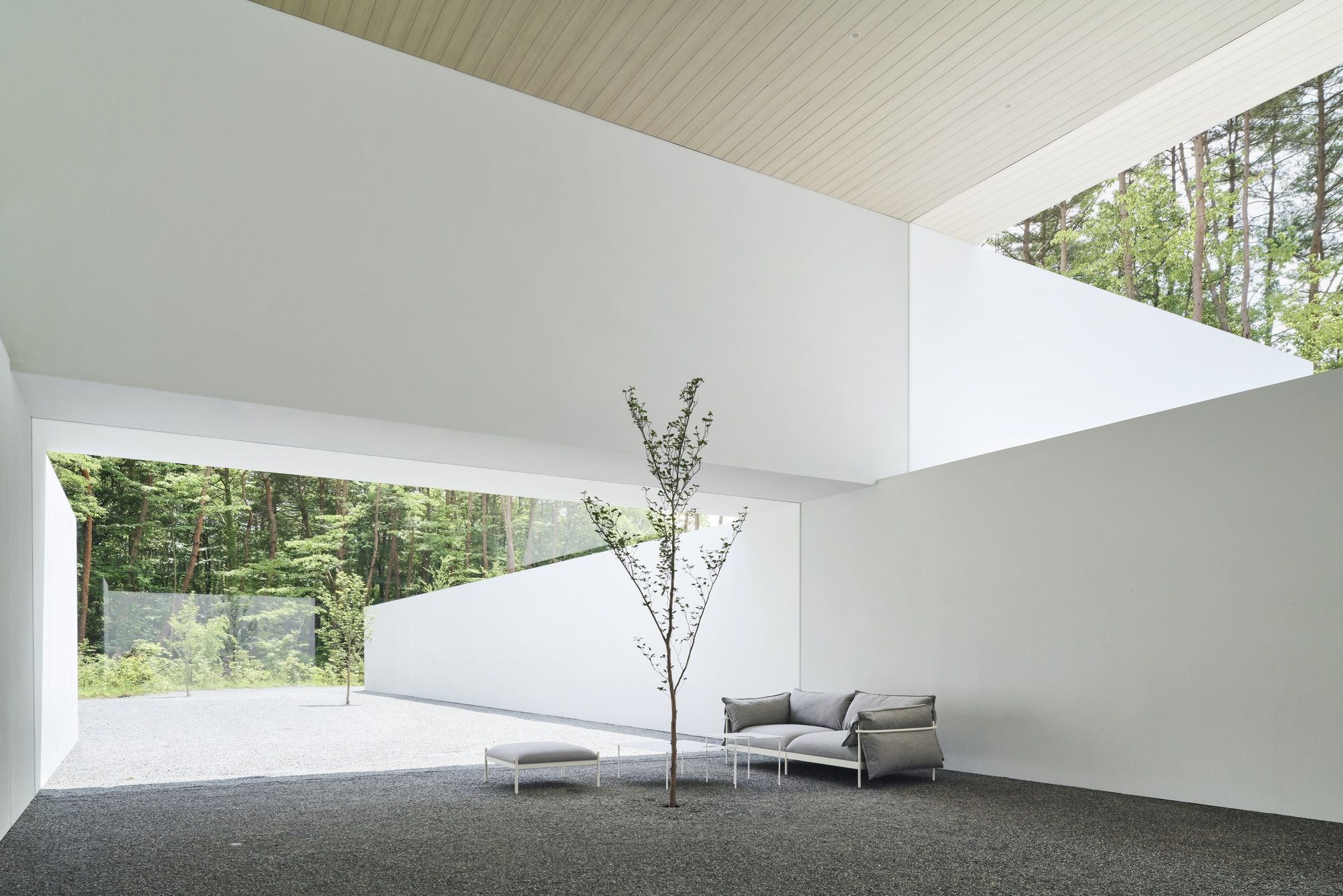
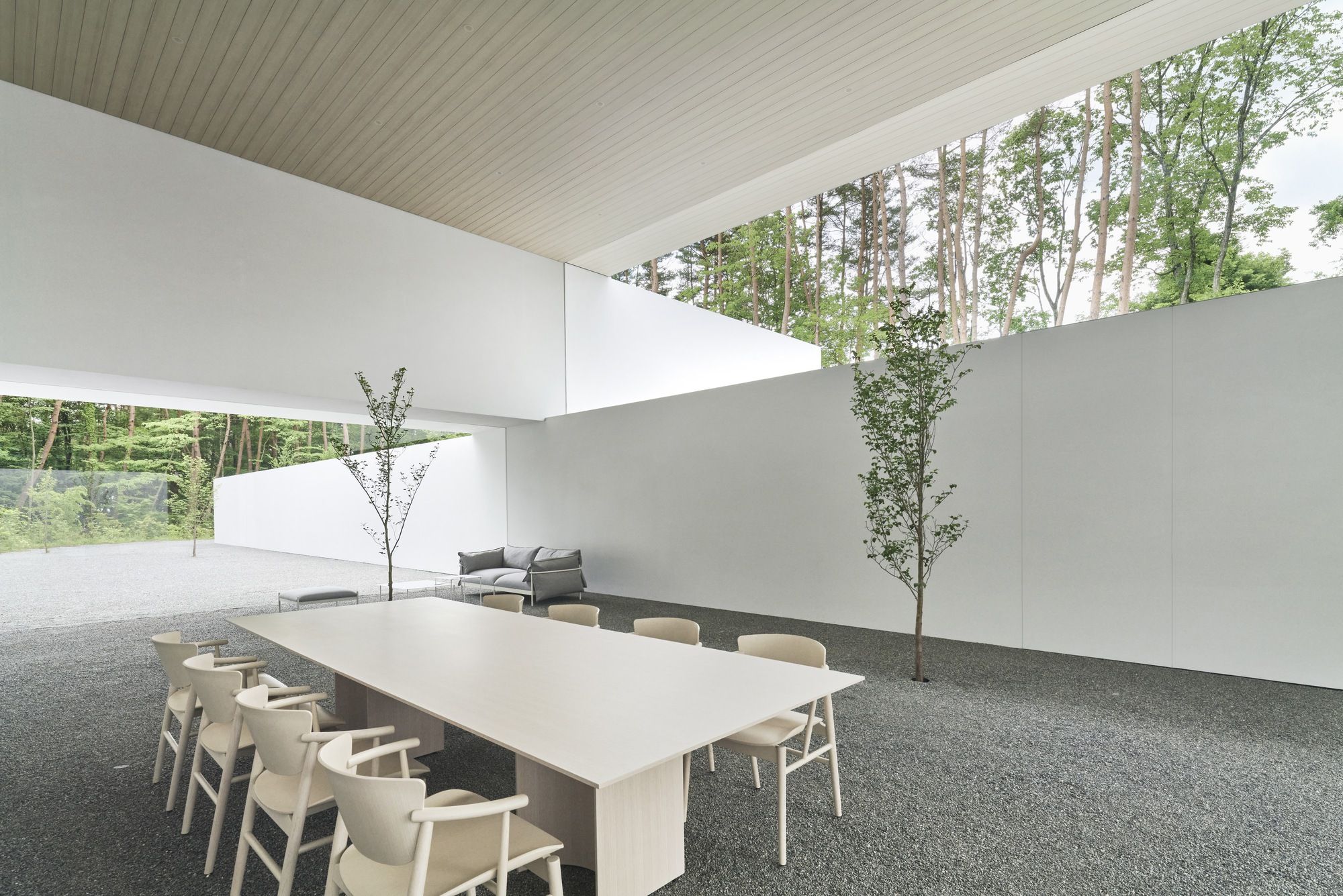
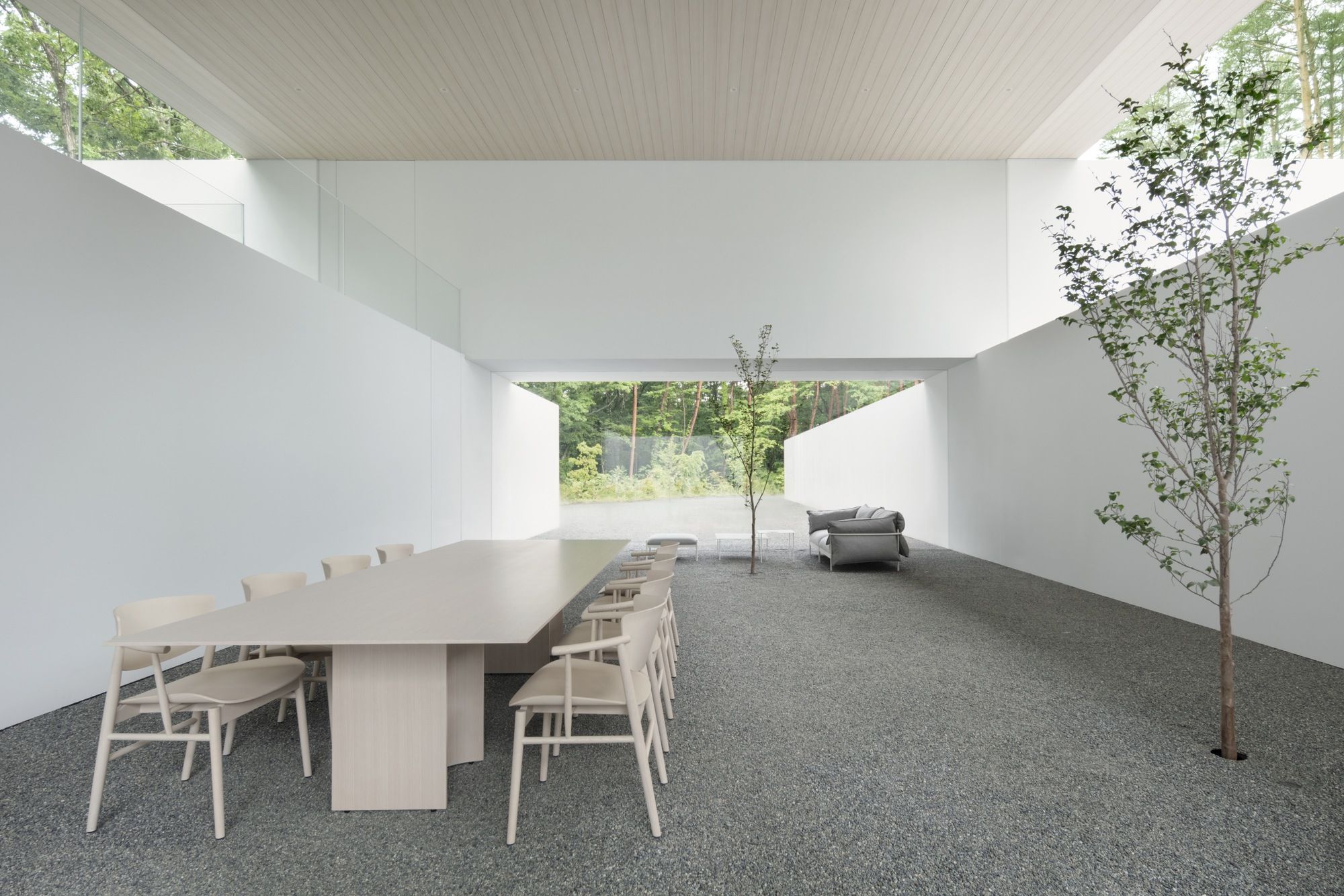
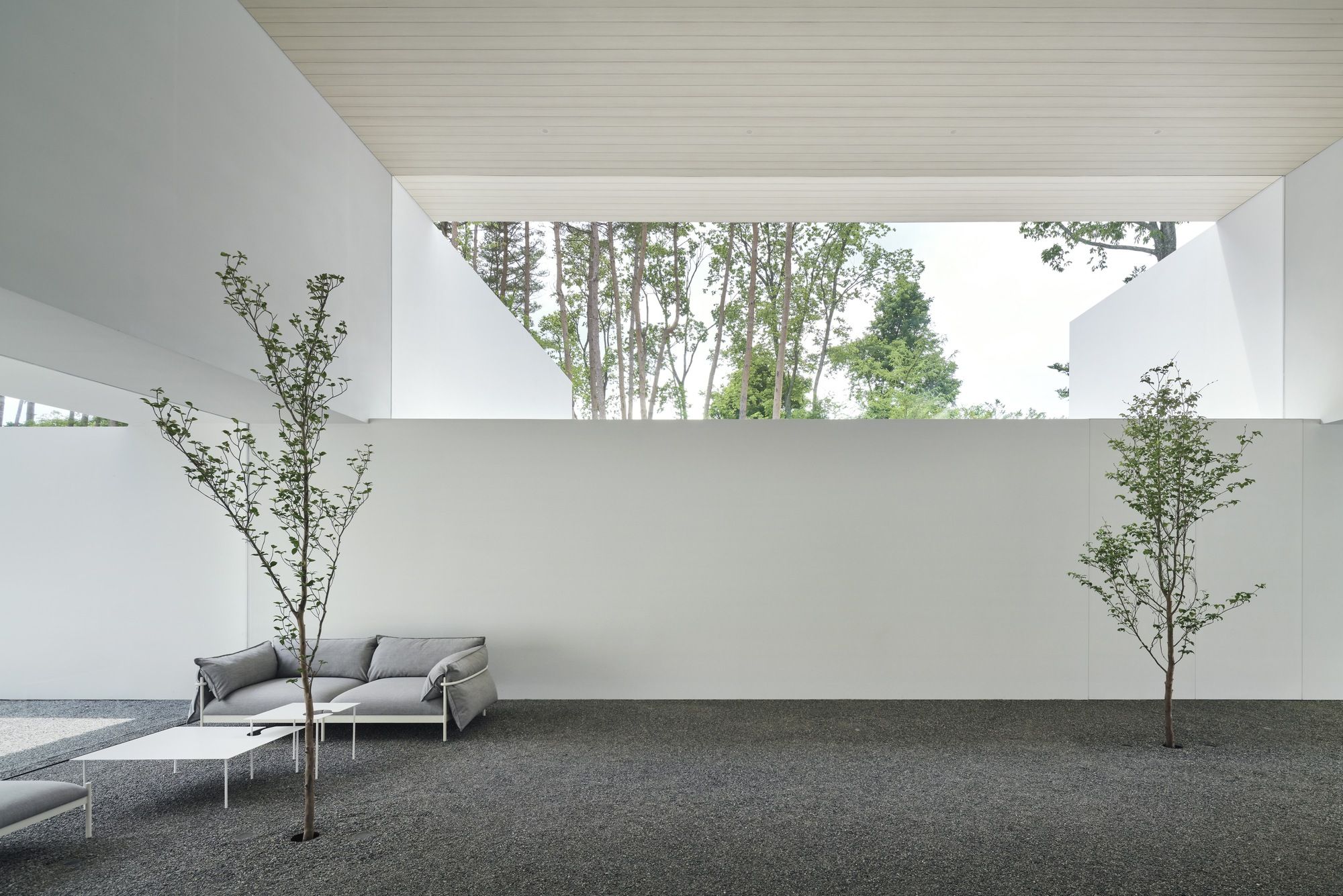

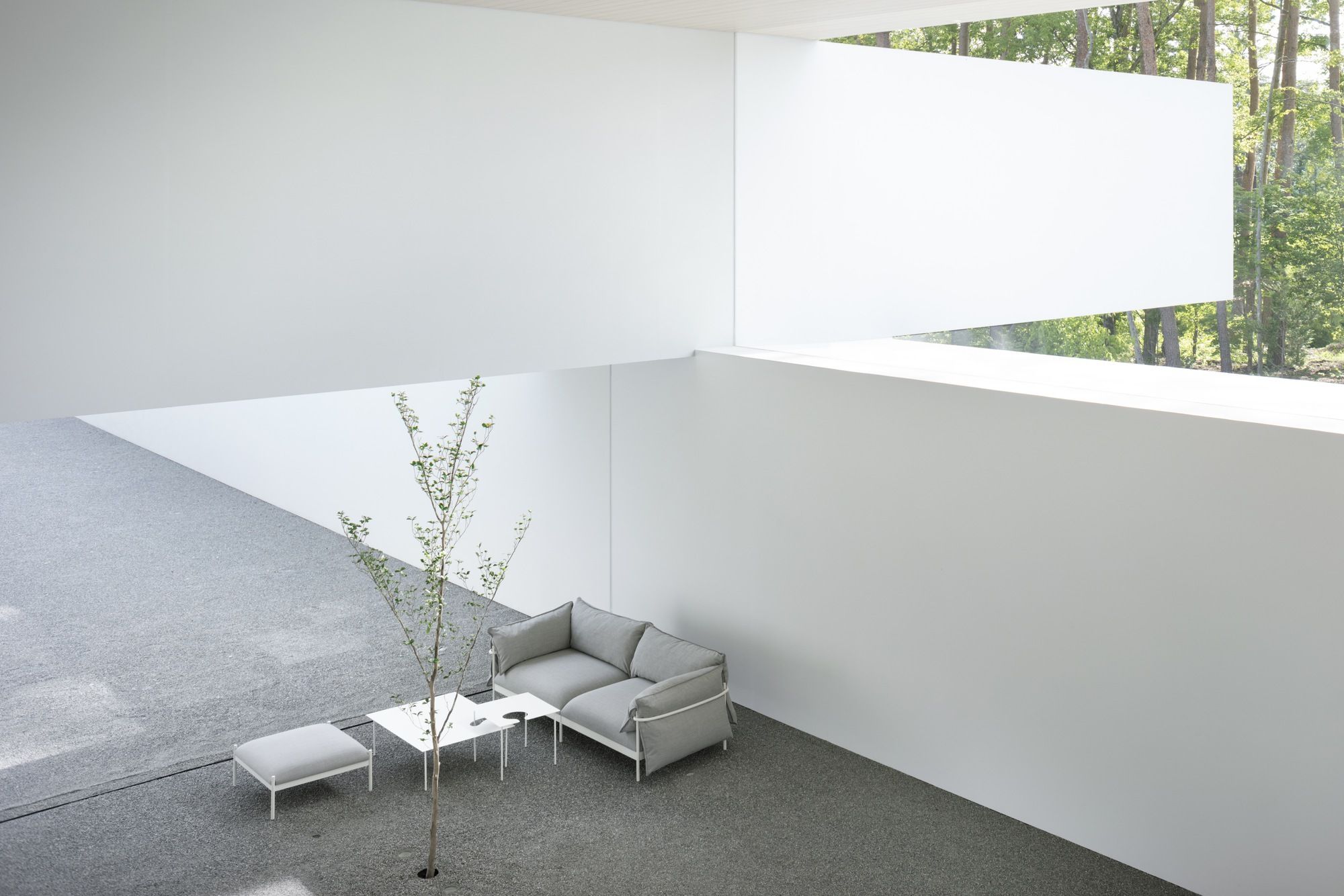
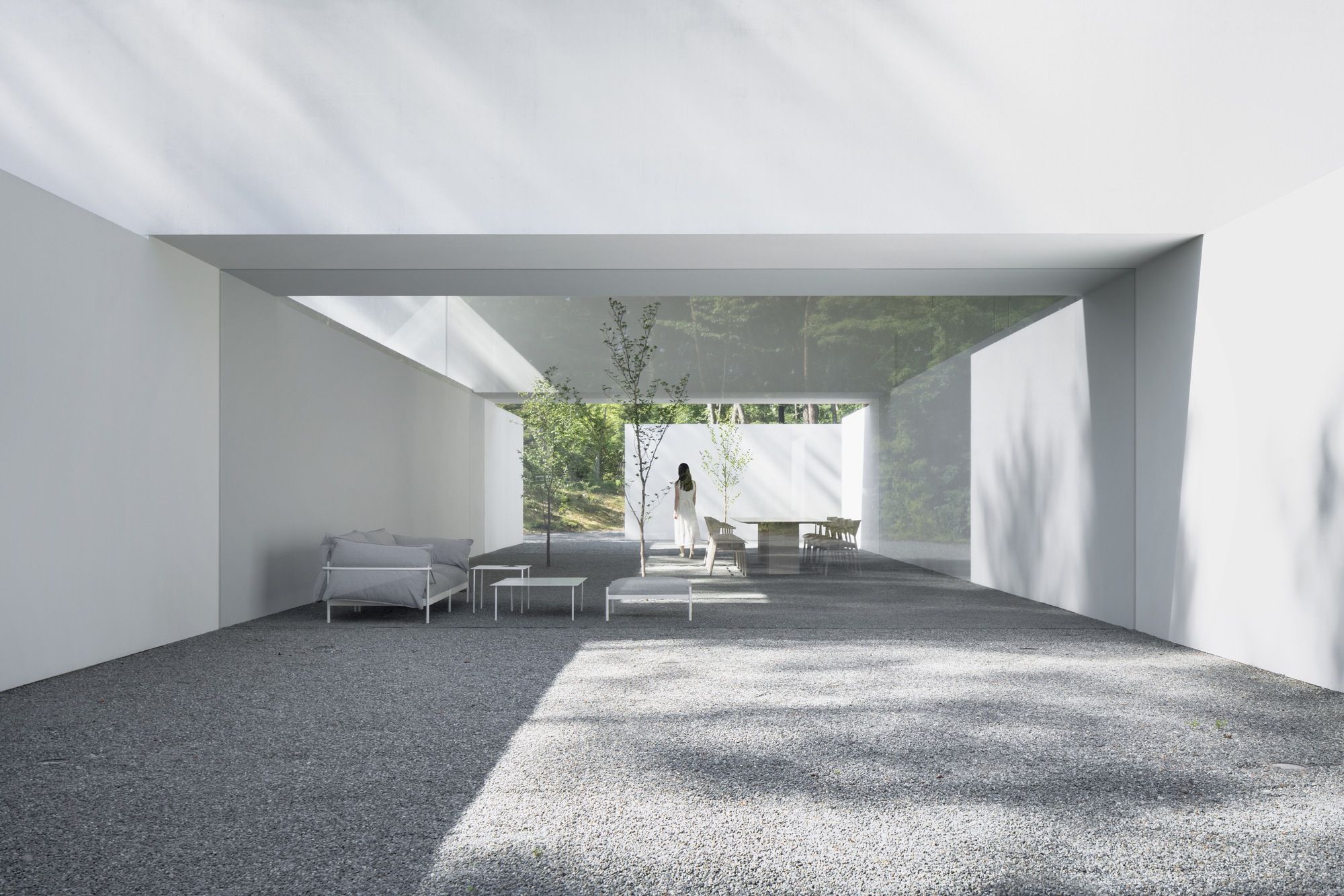
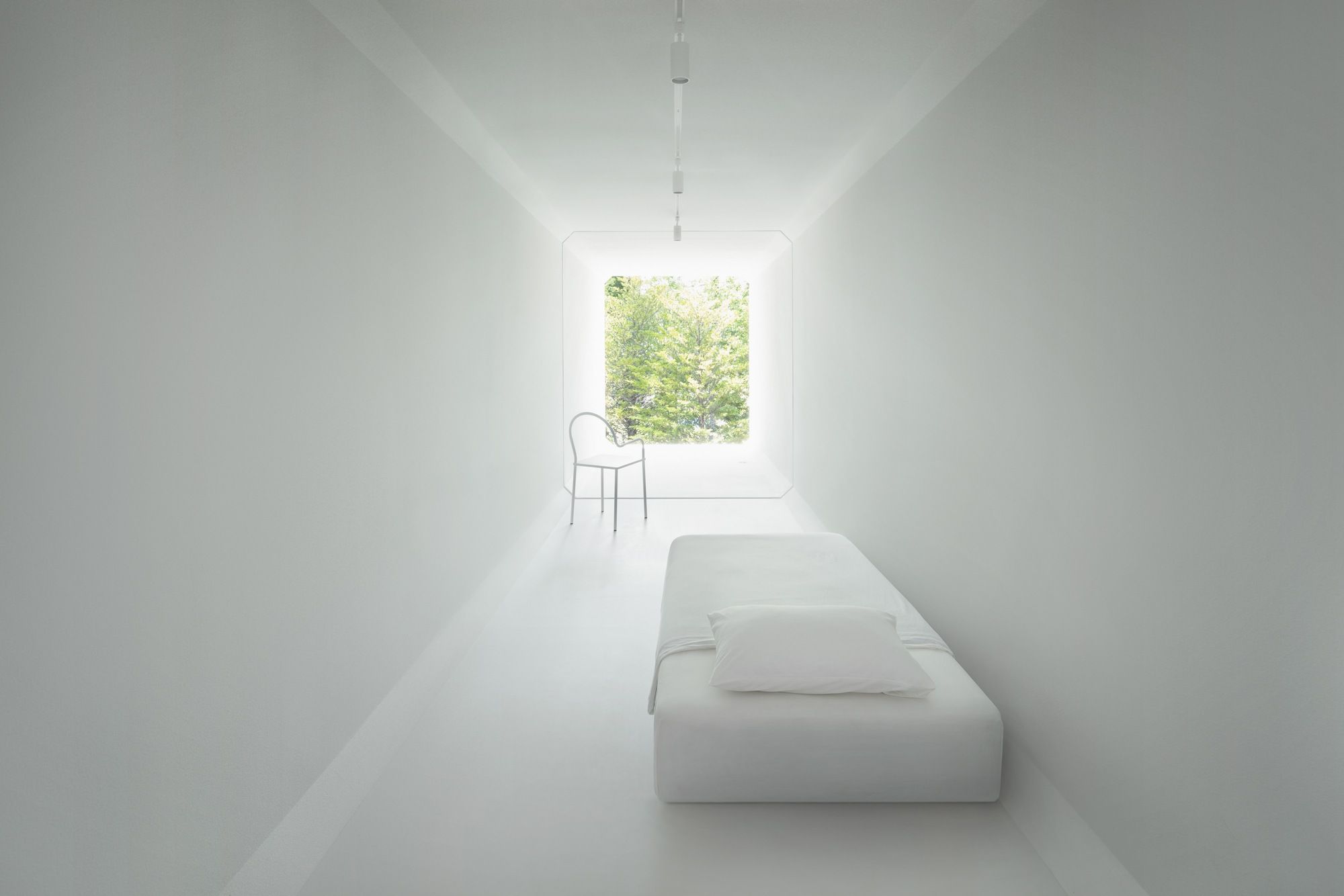
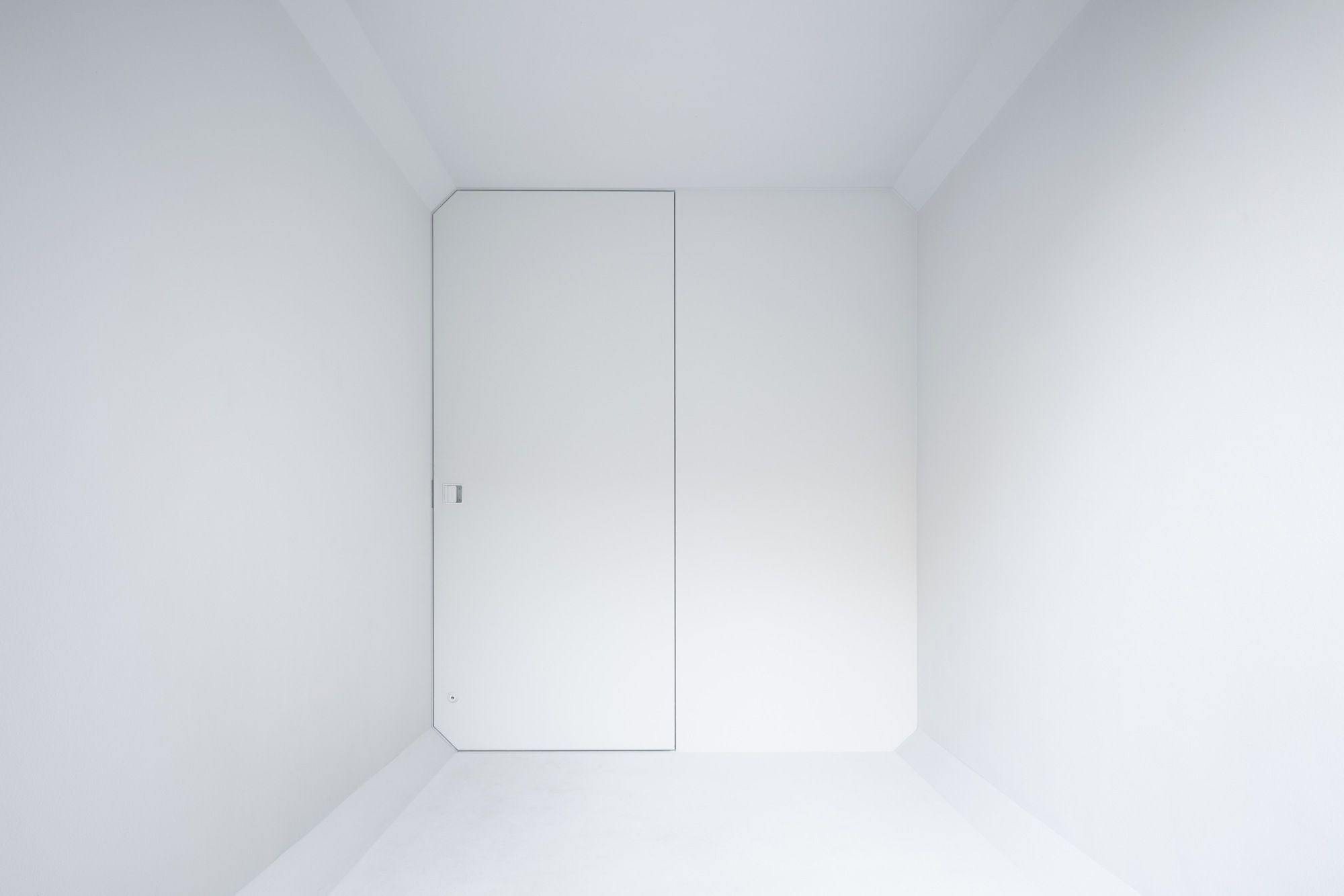
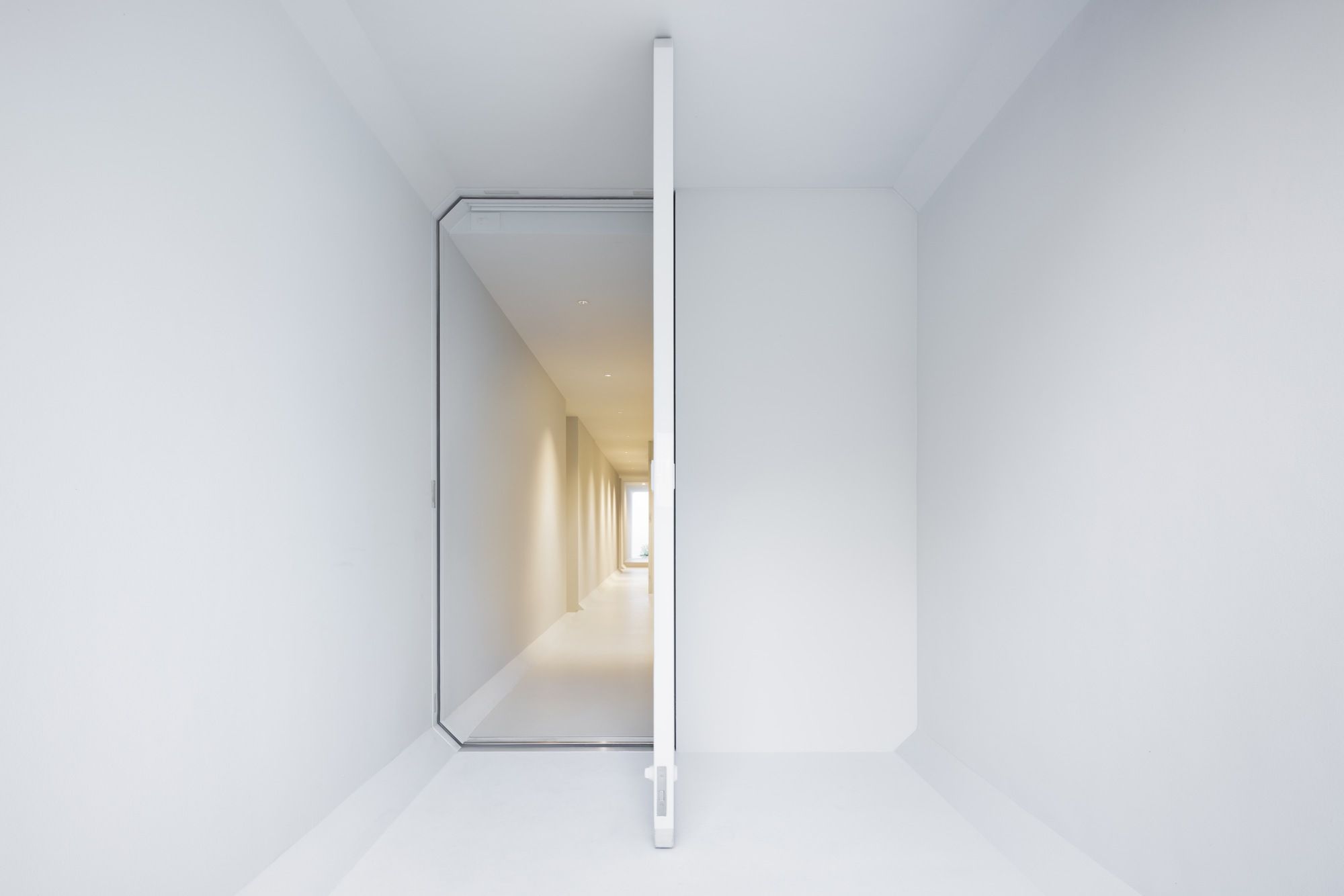
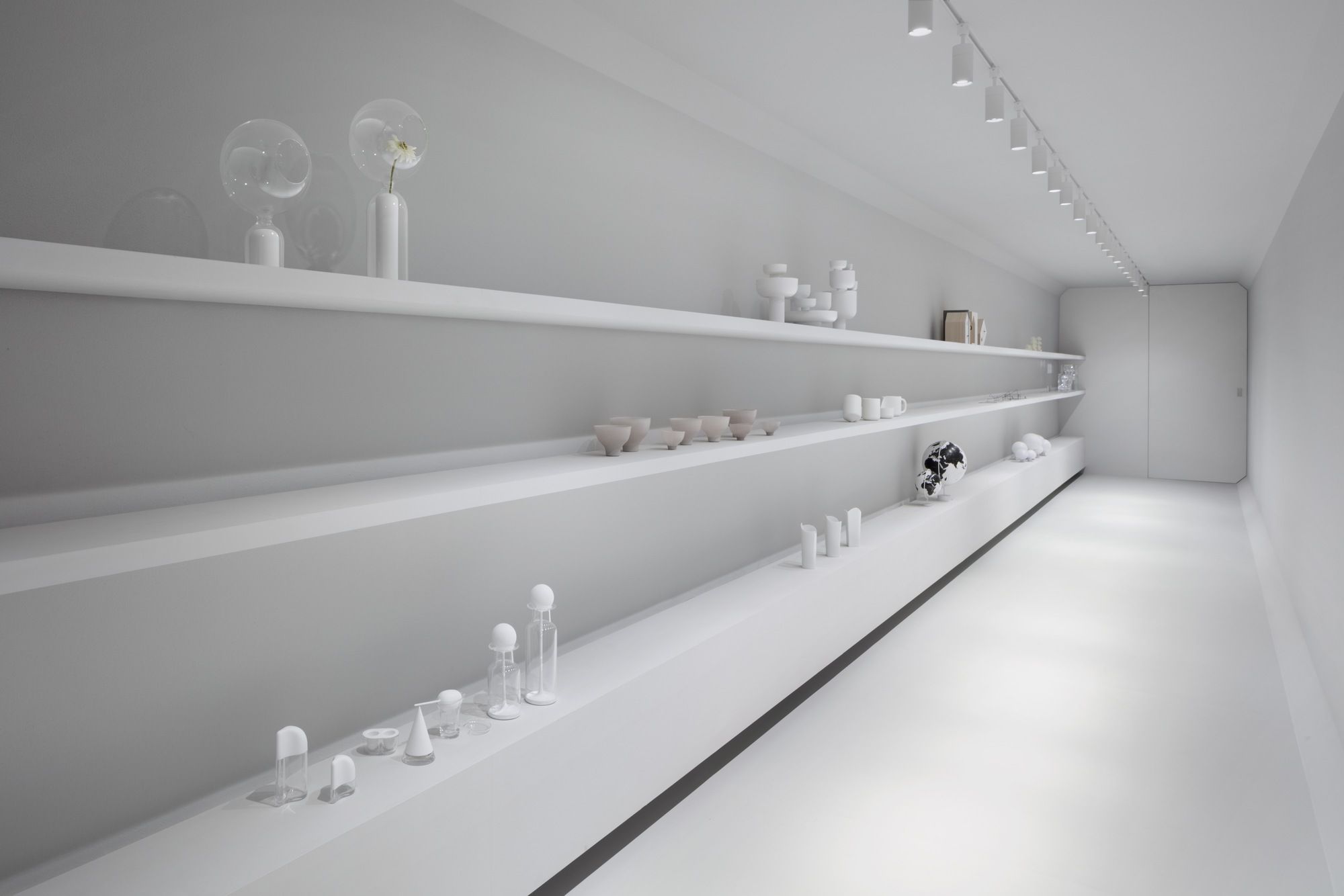
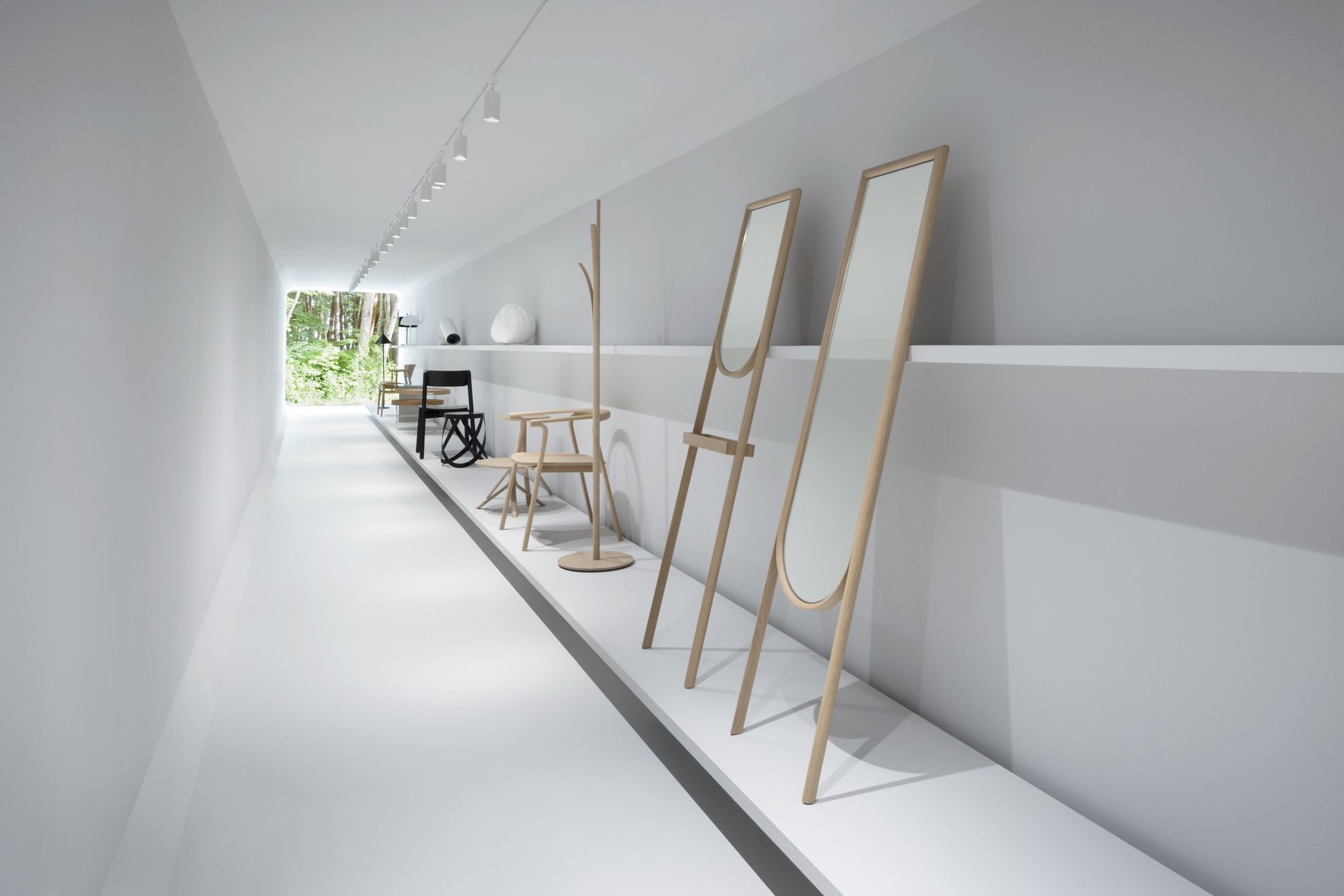
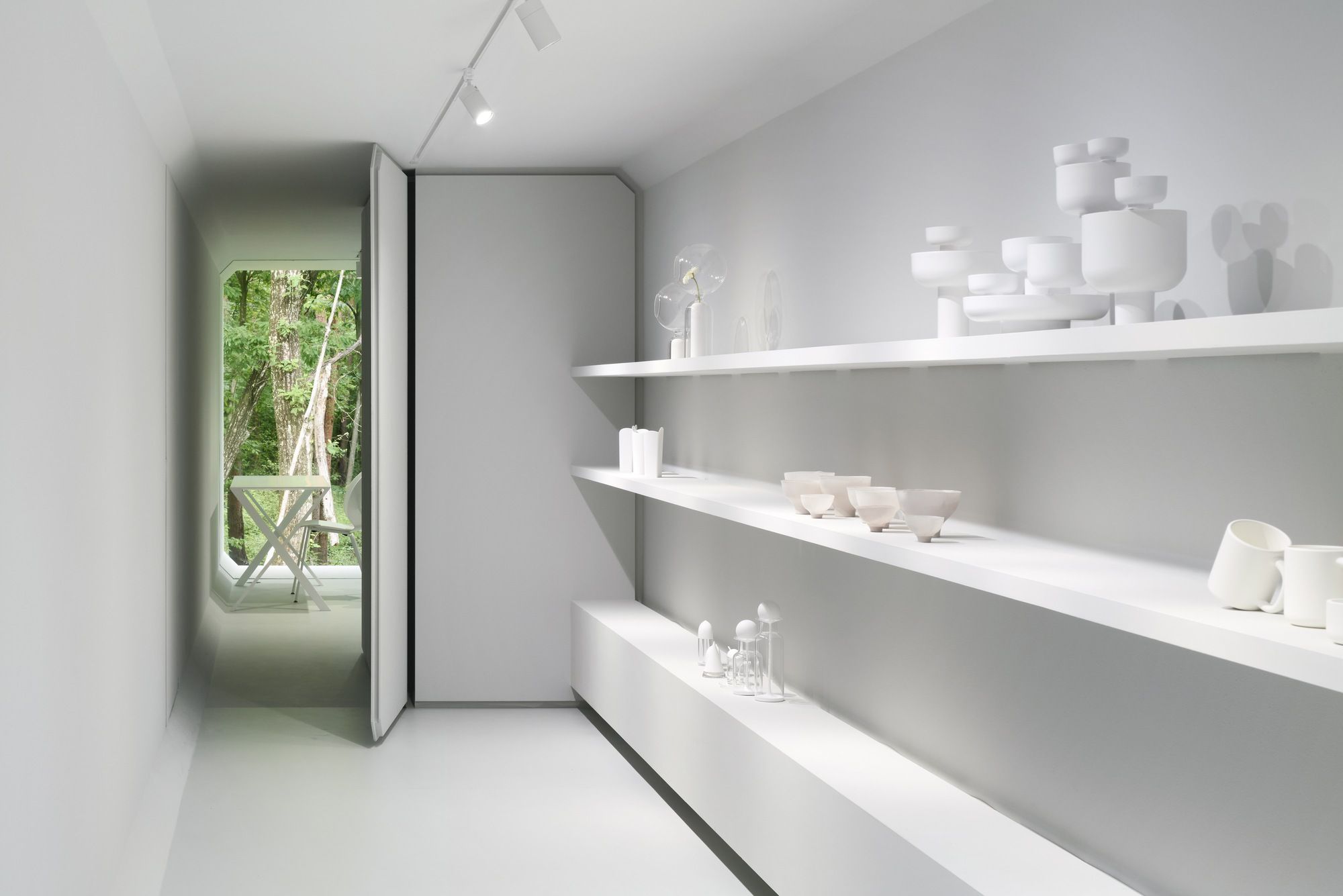
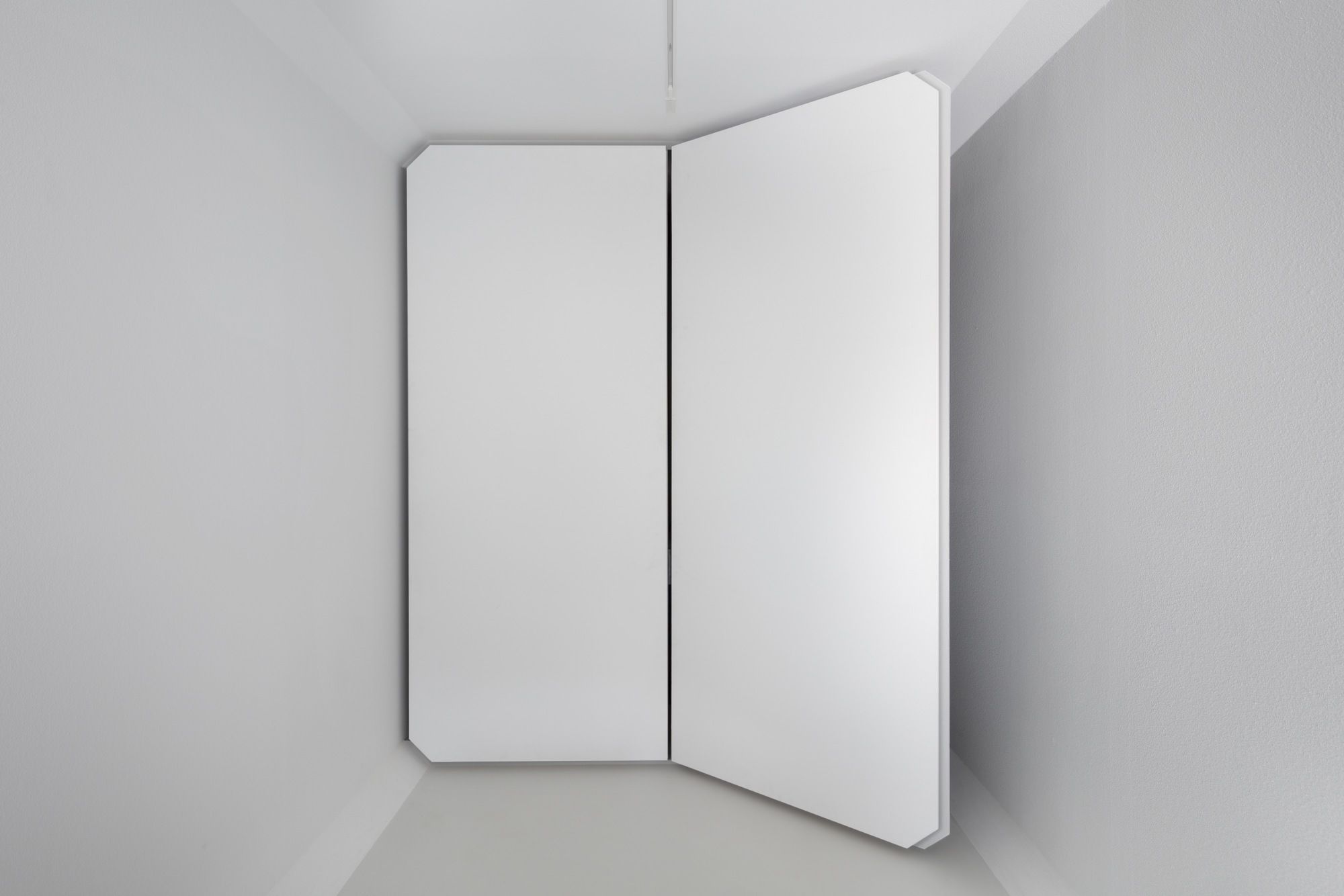
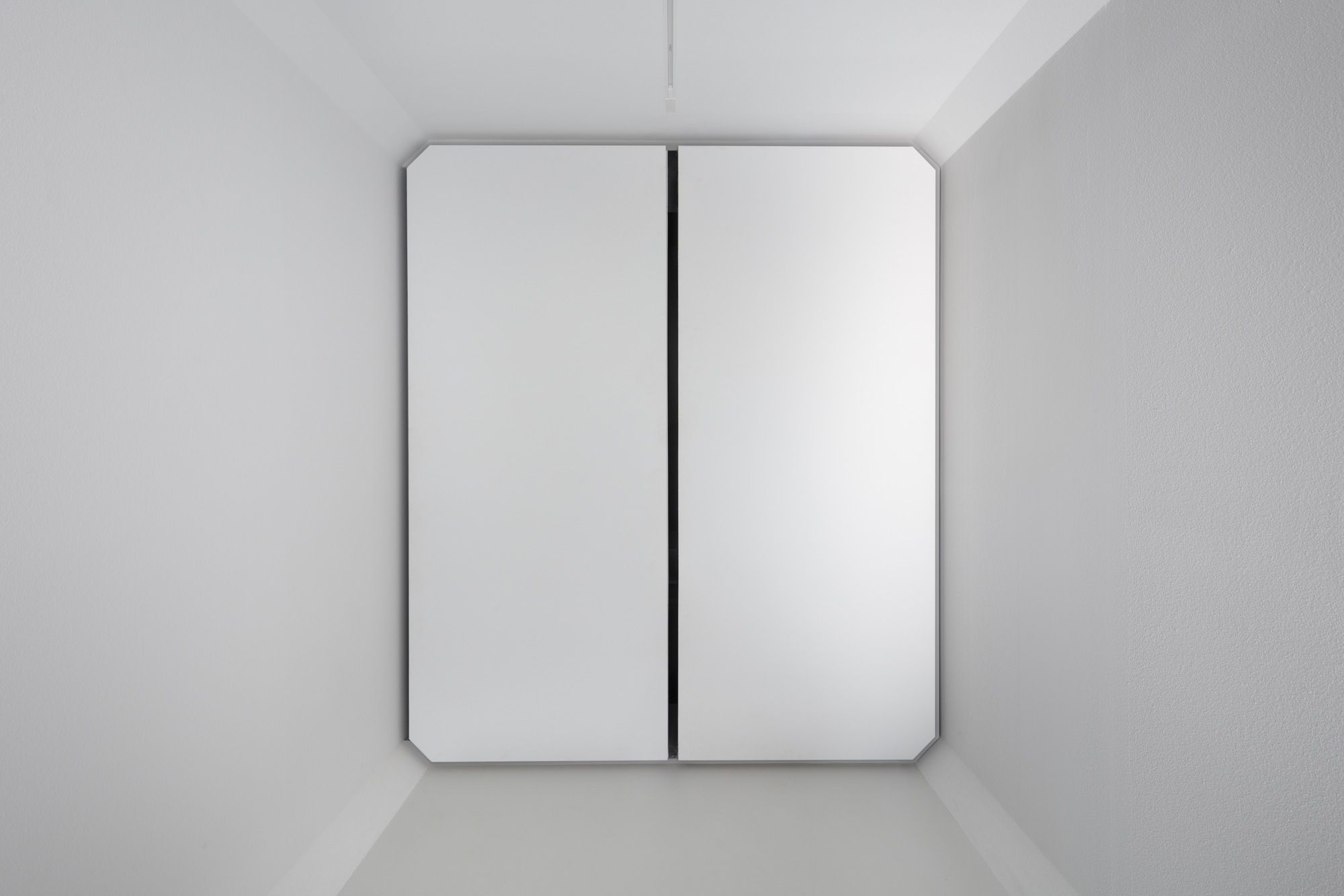

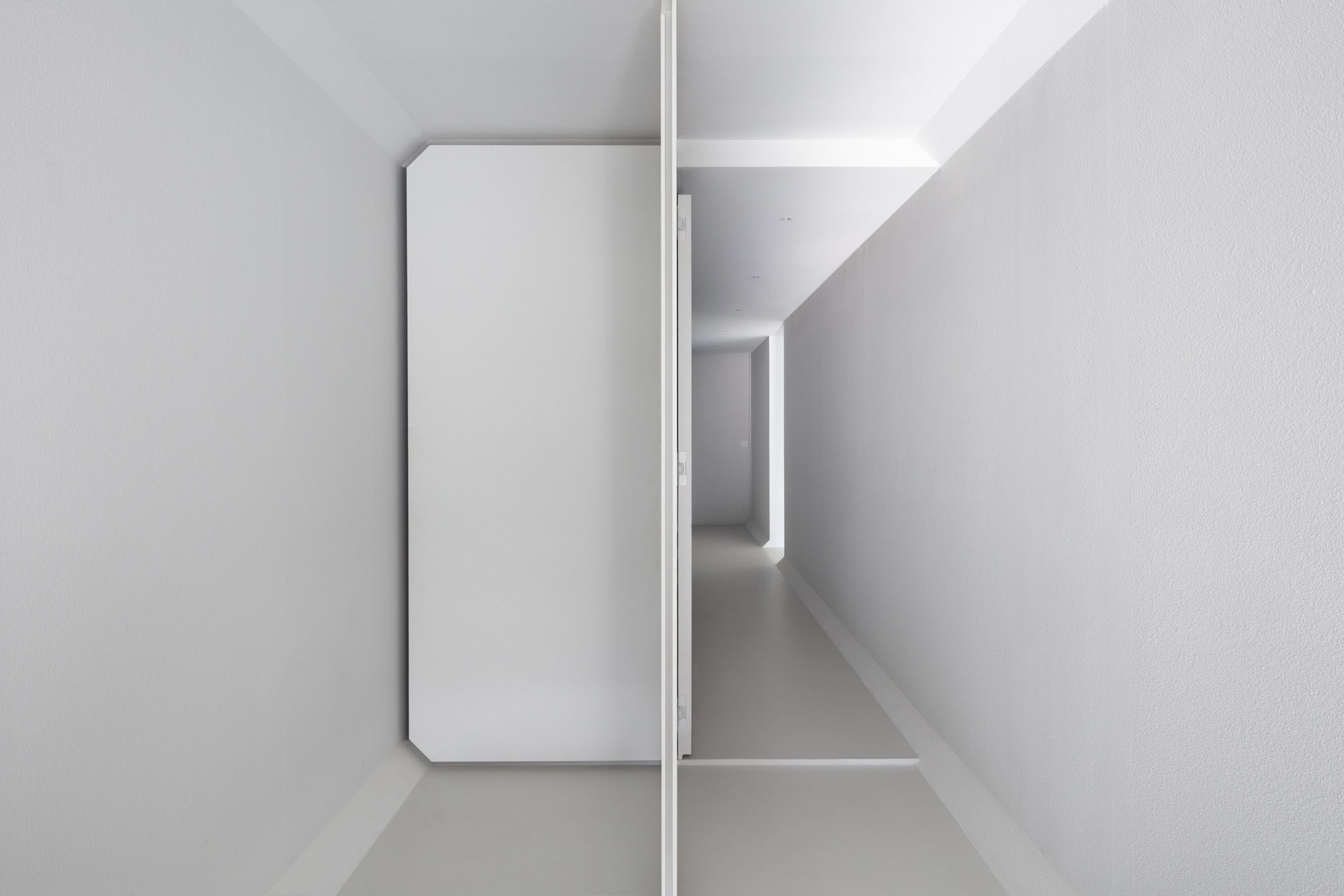
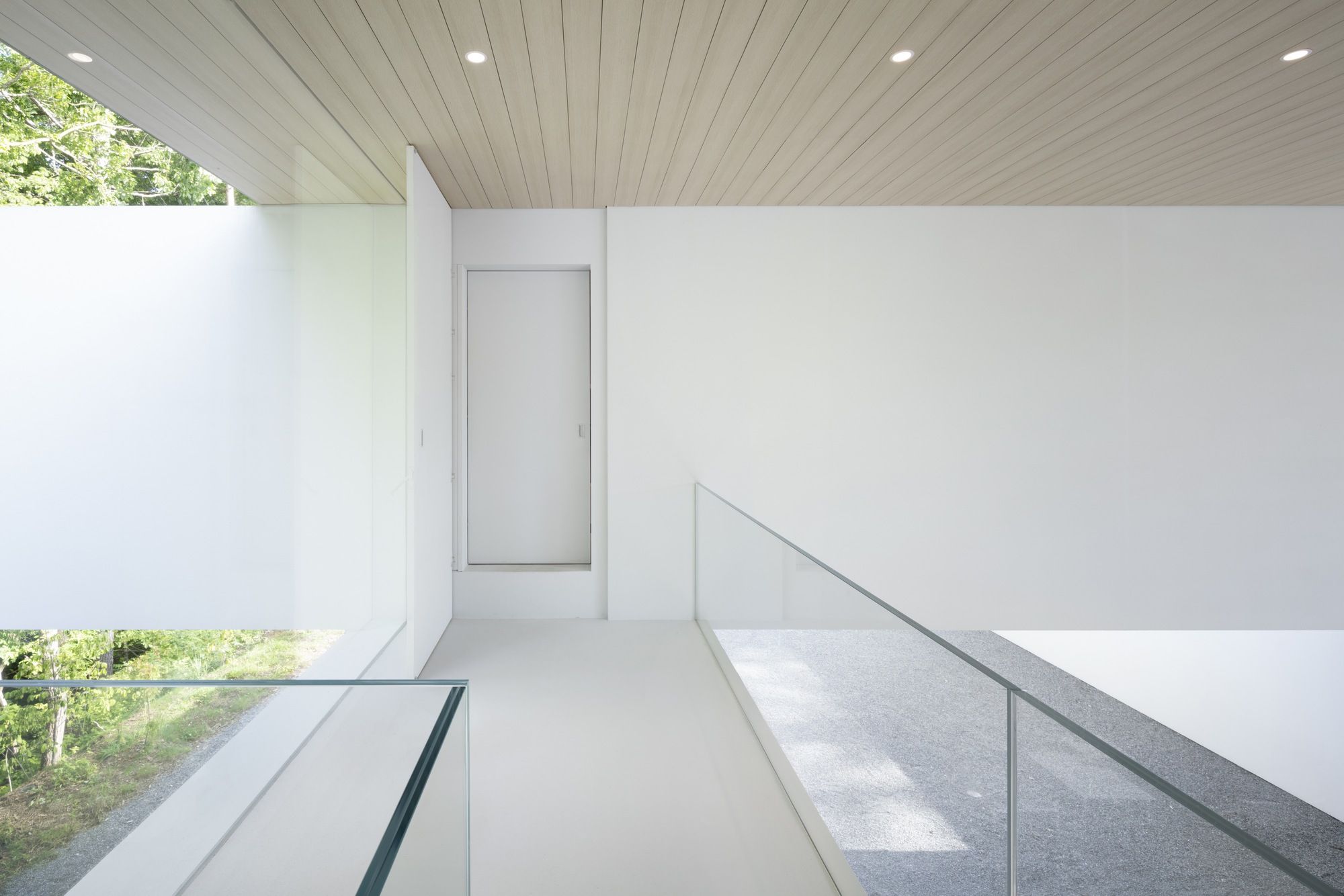
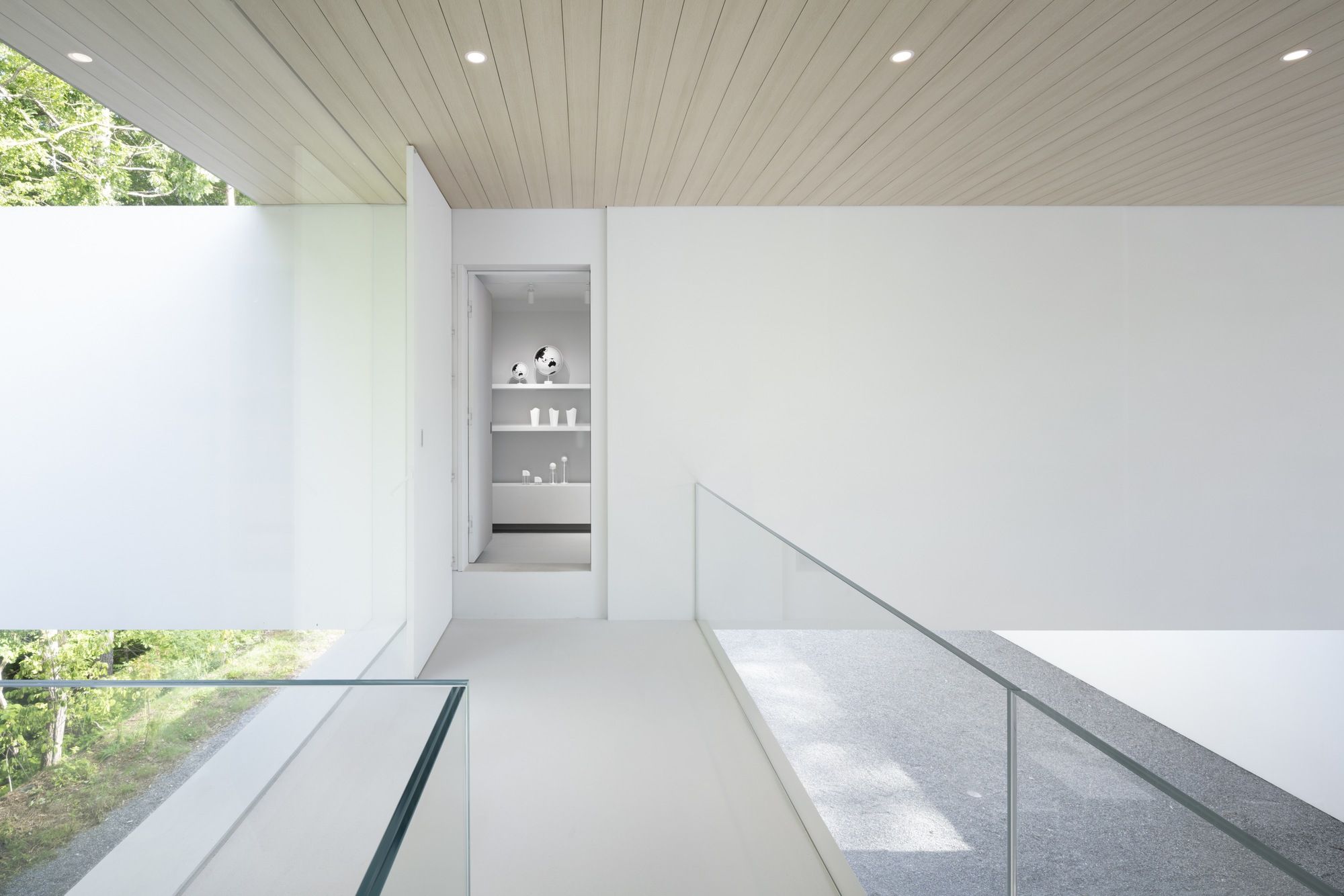
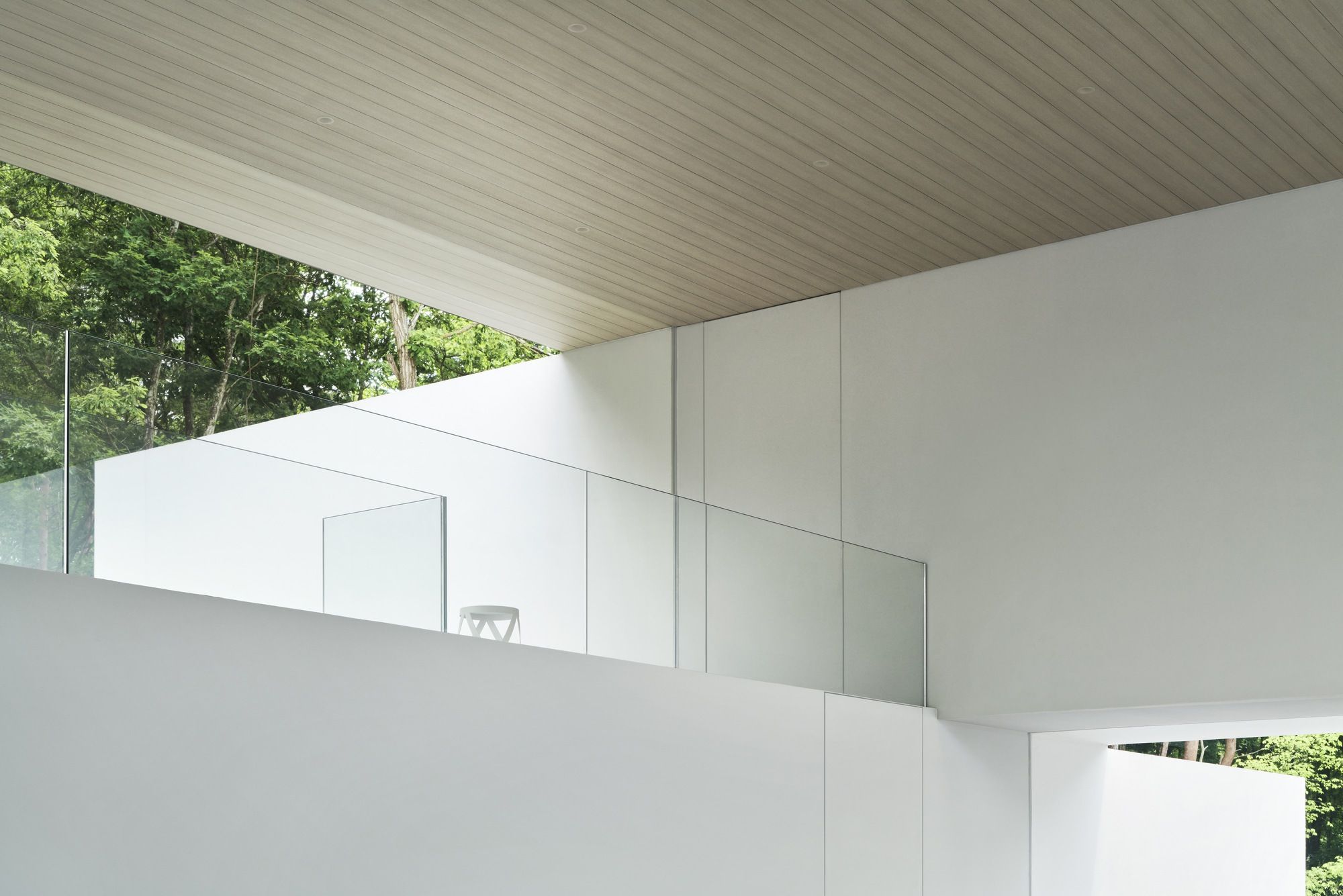
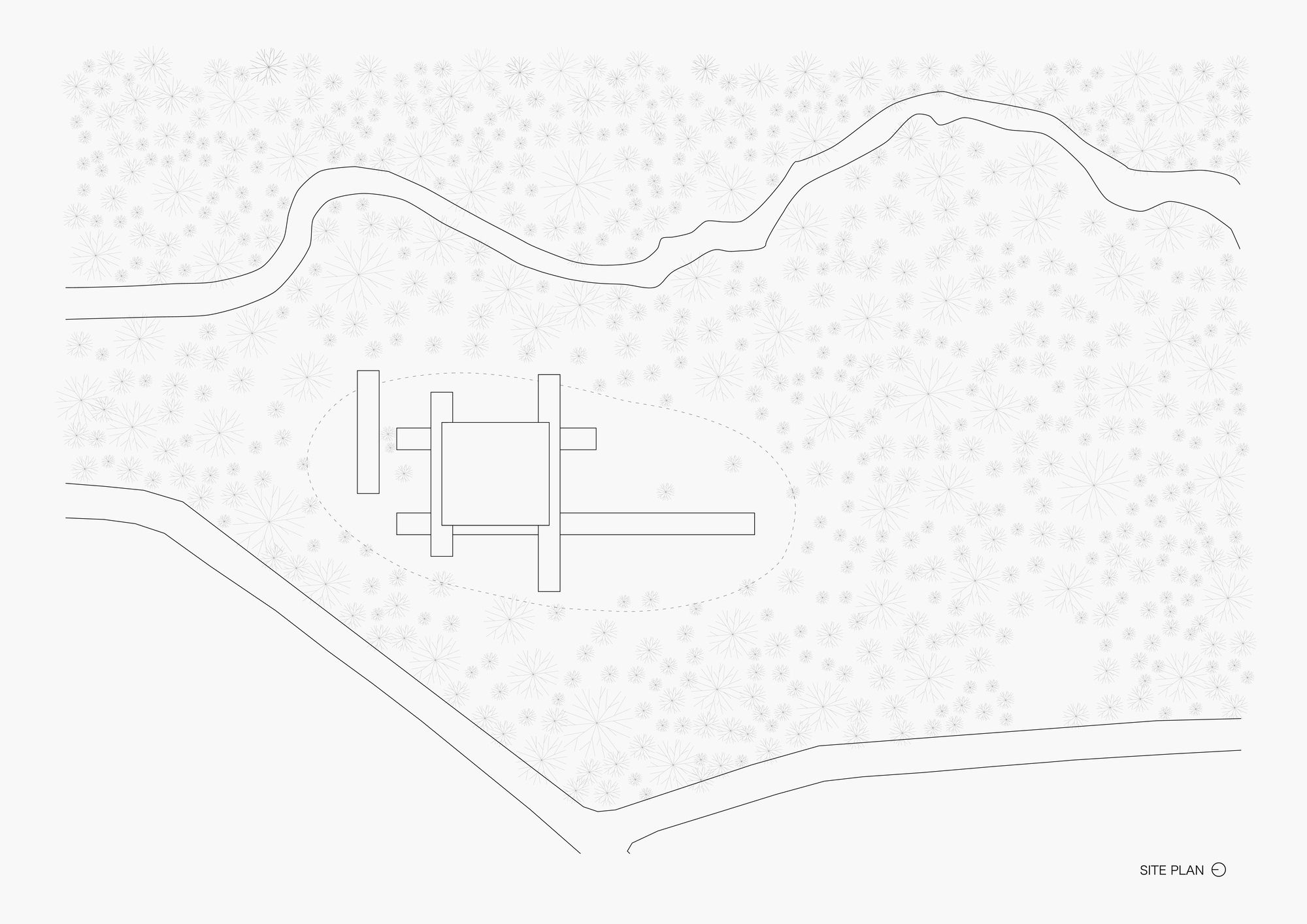
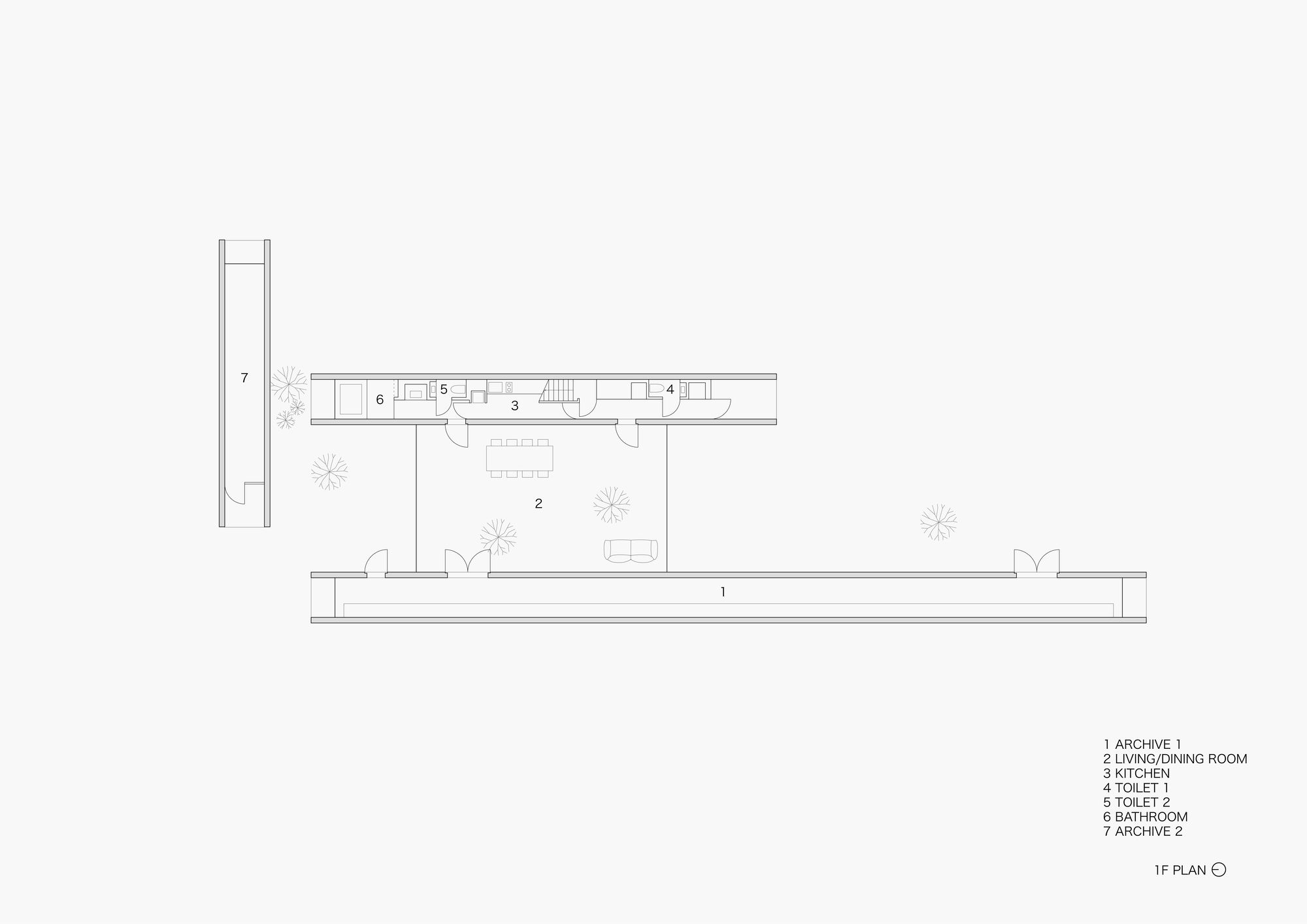
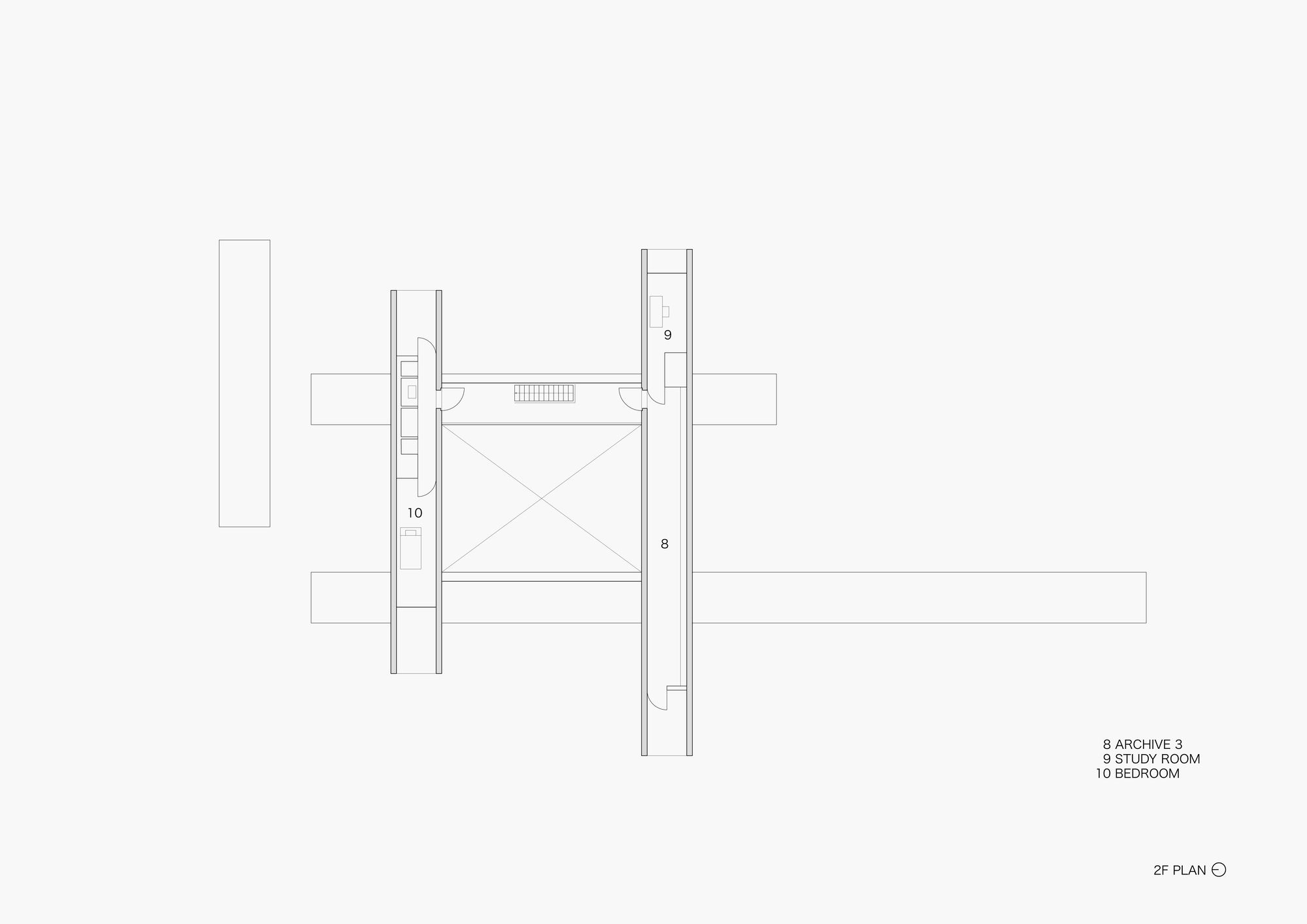
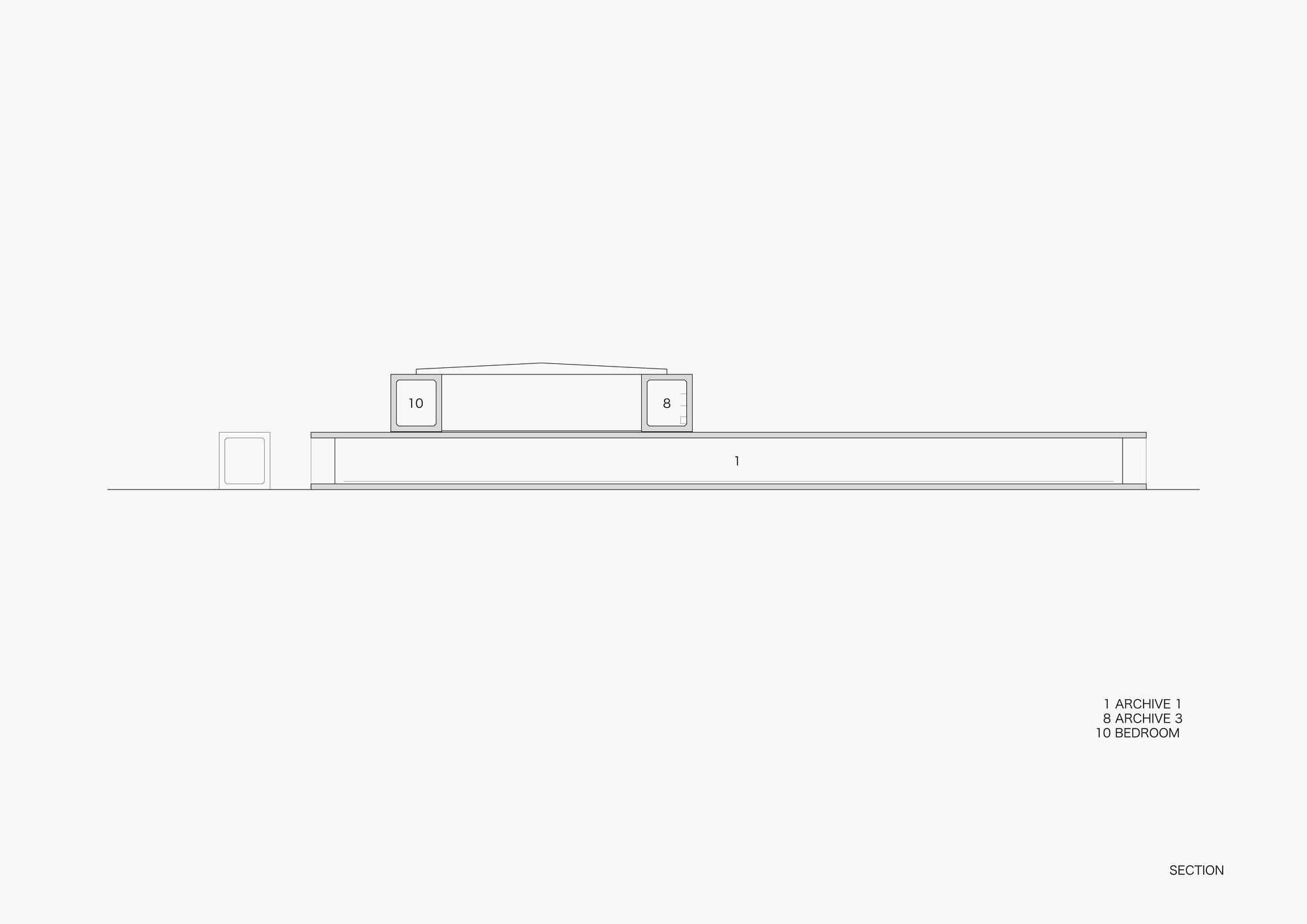