In a world where efficiency, sustainability, and innovation are paramount, modular construction stands tall as a game-changer in the architectural and construction industries. This construction method has gained immense popularity due to its ability to revolutionize how buildings are designed, fabricated, and assembled. In this blog post, we will delve into why modular construction is the future of the built environment.
What is Modular Construction?
Modular construction involves constructing buildings in off-site manufacturing facilities, where modules or prefabricated sections are built. These modules are then transported to the site and assembled to create the final structure. This method streamlines the construction process, as various components are made simultaneously in a controlled environment. This approach is not limited to residential projects but extends to commercial, educational, healthcare, and even industrial buildings.
The Process of Modular Construction
The modular construction process begins with comprehensive planning and design, where the architect and engineers work collaboratively to create detailed blueprints. These blueprints guide the fabrication of modular units in a factory setting. Skilled workers in the controlled environment of the factory construct the modules, ensuring high-quality and consistent results.
Once the modules are ready, they are carefully transported to the construction site. Here, the assembly process connects the modules precisely to create the final structure. Combining the modules requires expertise and adherence to strict quality control measures, ensuring a seamless integration that meets safety and building code standards.
Advantages of Modular Construction
1) Reduced Construction Time
Modular construction significantly reduces the time required to complete a project. Since modules are constructed simultaneously in the factory while site preparations occur, both processes run in parallel. This overlap accelerates the overall construction timeline, allowing projects to be completed in much shorter periods than traditional construction.
2) Cost Savings
While the initial investment in setting up a modular construction facility may seem significant, the benefits in the long run far outweigh the costs. Reducing labor costs, faster project delivery, and minimized material wastage contribute to substantial cost savings. The controlled factory environment also leads to fewer weather-related delays, further optimizing expenses.
3) Enhanced Quality Control
The factory setting of modular construction ensures that each module undergoes stringent quality checks throughout the manufacturing process. Skilled workers, following precise assembly procedures, guarantee high-quality components and materials are used. As a result, the finished building demonstrates exceptional craftsmanship and durability.
4) Increased Flexibility
The modular construction method offers unparalleled flexibility in design and layout. With the ability to fabricate modules of various sizes and configurations, builders can create unique structures to meet specific project requirements. Moreover, modifications or expansions can be made more easily by adding or removing modules as needed.
5) Improved Sustainability
Sustainable practices have become a vital aspect of the construction industry. Modular construction aligns perfectly with this goal. The controlled environment in the factory reduces waste generation, and surplus materials can be efficiently recycled. Additionally, modular buildings are designed with energy efficiency in mind, contributing to lower energy consumption and a reduced carbon footprint.
6) Minimized Disruptions and Site Impact
Traditional construction can cause significant disruptions to the surrounding community and the environment. Noise, dust, and traffic congestion are common issues. In contrast, modular construction minimizes these disruptions by moving much of the construction off-site. This leads to a cleaner and quieter construction process, garnering more significant community approval.
7) Consistent Quality
The factory-controlled environment ensures that each module adheres to the same high-quality standards. This uniformity is particularly beneficial for projects involving multiple identical structures, such as affordable housing developments or schools.
8) Safer Construction Process
The factory setting of modular construction eliminates many of the safety hazards typically associated with on-site construction. Workers face fewer risks, reducing the likelihood of accidents and injuries. Moreover, heavy machinery and equipment use is limited on-site, enhancing safety for workers and the public.
Applications of Modular Construction
- Residential Buildings: Modular construction is widespread in residential projects, from single-family homes to multi-story apartment complexes. The efficiency and cost-effectiveness make it an attractive choice for home builders.
- Commercial Structures: The flexibility of modular construction allows for the creation of various commercial buildings, including offices, retail spaces, and hotels. With faster construction times, businesses can start operations sooner, generating revenue more quickly.
- Educational Facilities: Schools and educational institutions have also embraced modular construction due to its ability to meet tight schedules, especially during summer breaks. It offers a practical solution to accommodate growing student populations.
- Healthcare Facilities: Hospitals and medical centers can benefit from modular construction as they often require quick expansions or renovations. Modular units can be added seamlessly to existing facilities with minimal disruptions.
- Remote and Challenging Locations: Modular construction has proven ideal for projects in remote or challenging locations, where on-site construction can be logistically tricky. Modules can be fabricated elsewhere and transported to such sites with relative ease.
- Disaster Relief Housing: In the aftermath of natural disasters, modular construction can provide temporary housing for displaced individuals. Its quick deployment and customization capabilities are invaluable in emergencies.
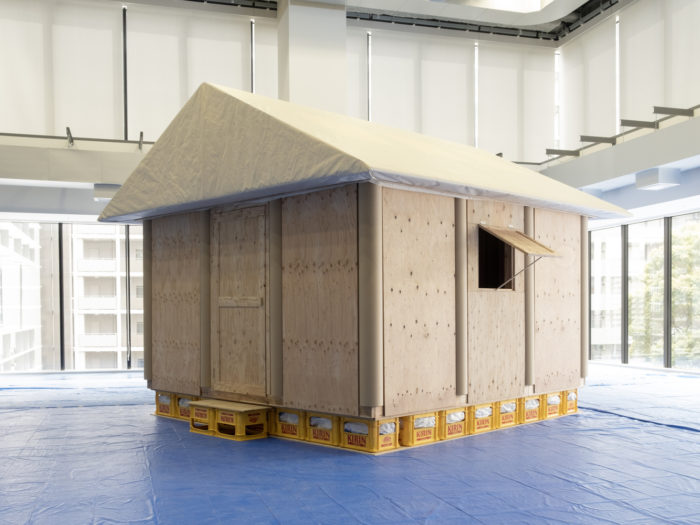
Prototype for Temporary Housing in Response to the Turkey-Syria Earthquake. © Shigeru Ban Architects
Challenges of Modular Construction
While modular construction offers numerous advantages, it is essential to acknowledge some of the challenges associated with this approach:
- Transportation and Logistics: Transporting large modules to the construction site requires careful planning and coordination. Issues such as traffic, road restrictions, and weather conditions can impact delivery schedules.
- Design Limitations: While modular construction is flexible in many ways, specific complex architectural designs may be challenging to achieve with modular units. Designers need to strike a balance between innovative aesthetics and practicality.
- Initial Investment: Establishing a modular construction facility demands a significant upfront investment. This can be a barrier for smaller construction firms or those with limited financial resources.
- Skilled Workforce: The success of modular construction relies on a skilled workforce with expertise in manufacturing and on-site assembly. Ensuring a competent team of workers is crucial for optimal results.
Final Thoughts
Modular construction represents a transformative advancement in the building industry. Its time-saving, cost-effective, and sustainable attributes have made it an attractive option for various projects, from residential and commercial buildings to educational facilities and disaster relief housing. The ability to prefabricate components in a controlled environment, reduce on-site disruptions, and provide consistent quality are driving the widespread adoption of this method.
As the construction industry continues to evolve, modular construction is expected to play an increasingly vital role in shaping the future of building projects worldwide. Embracing this innovative approach opens new possibilities for more efficient, eco-friendly, and adaptable construction solutions that meet the needs of the modern world.
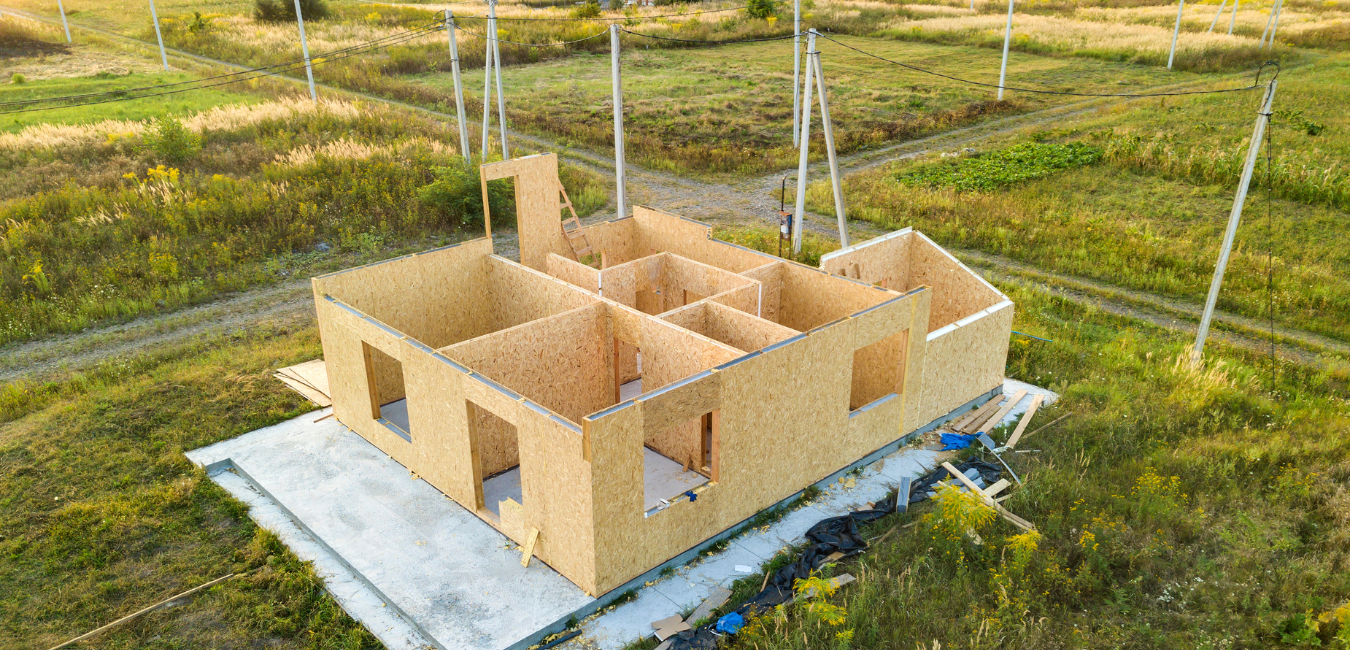
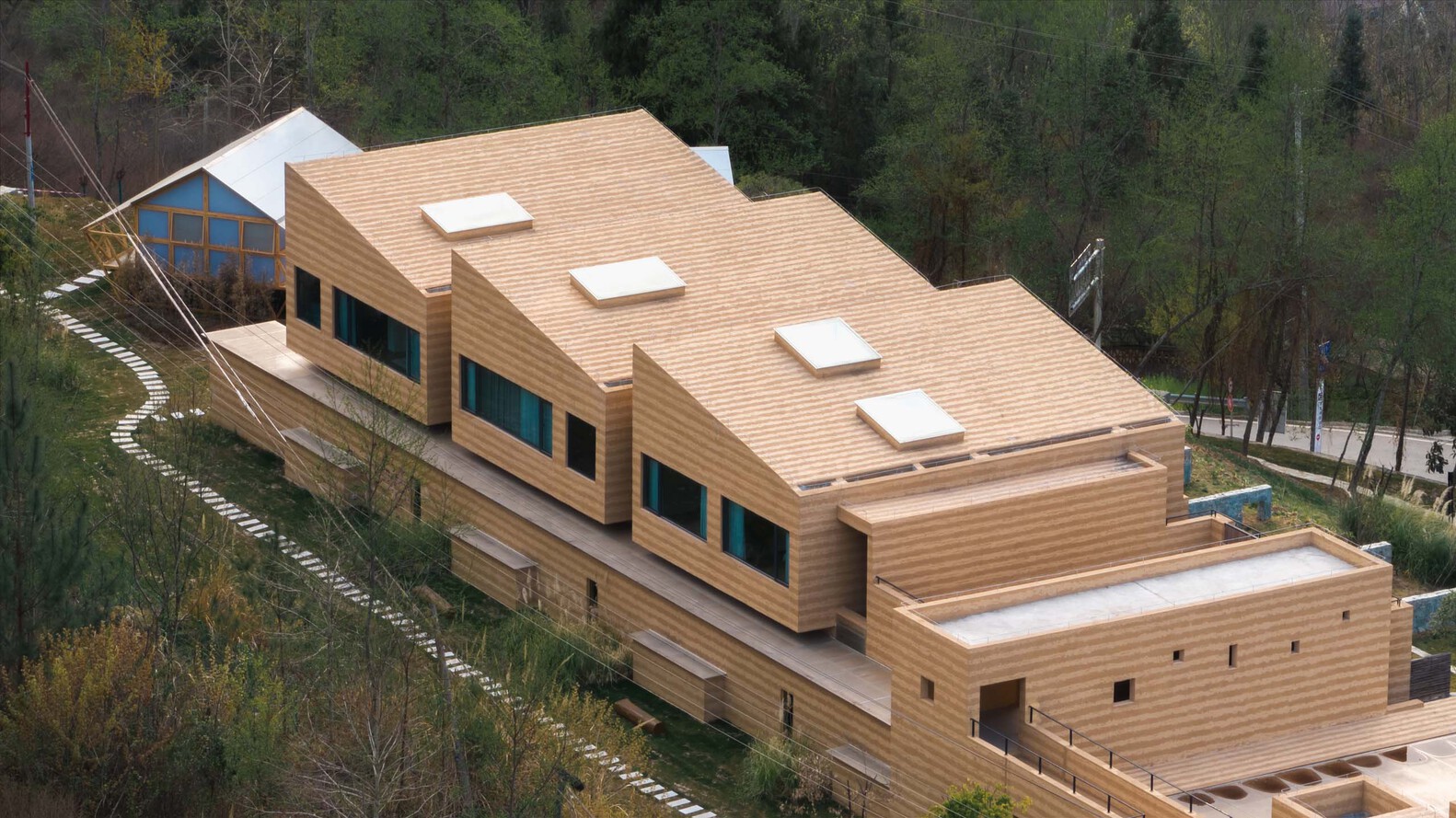
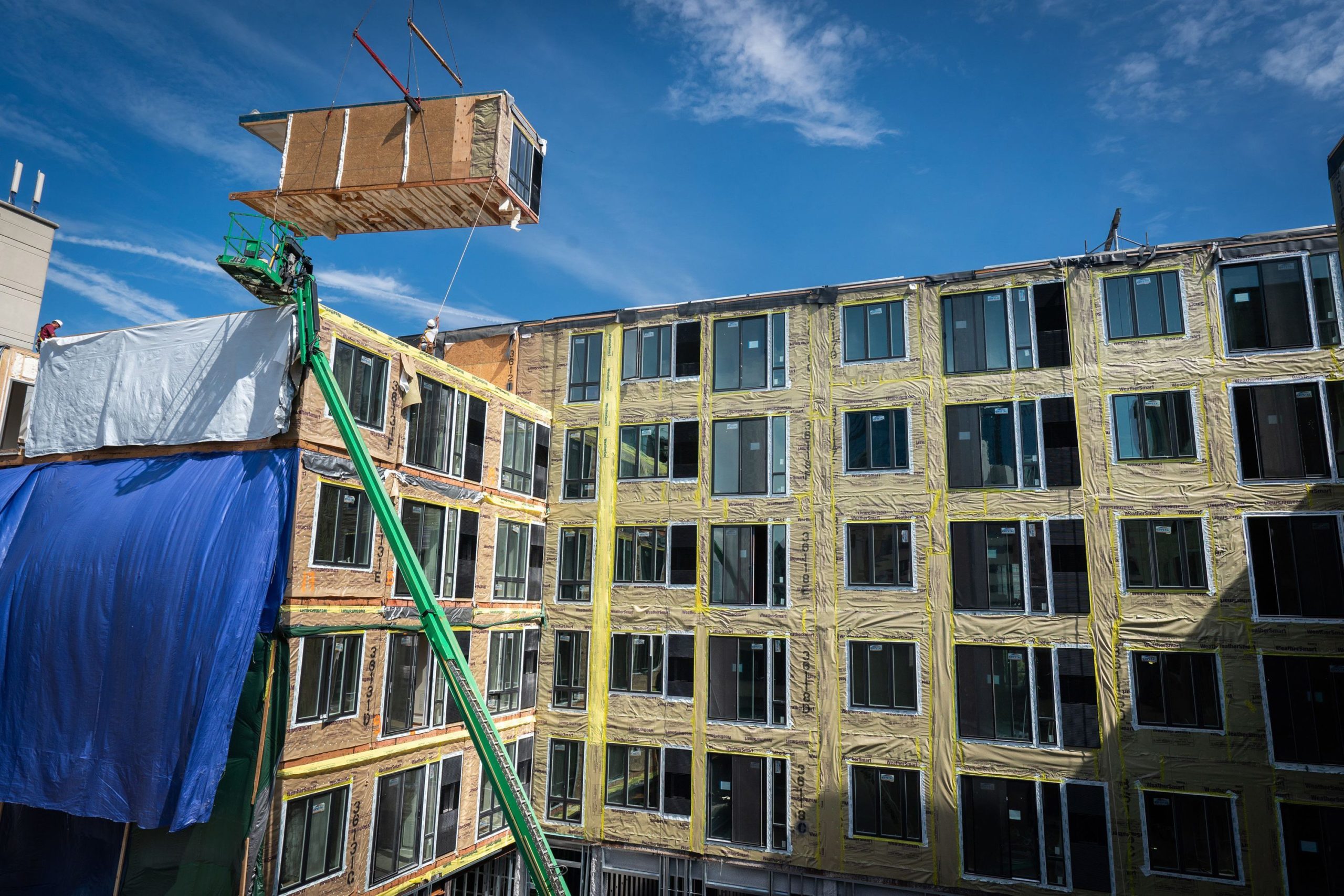
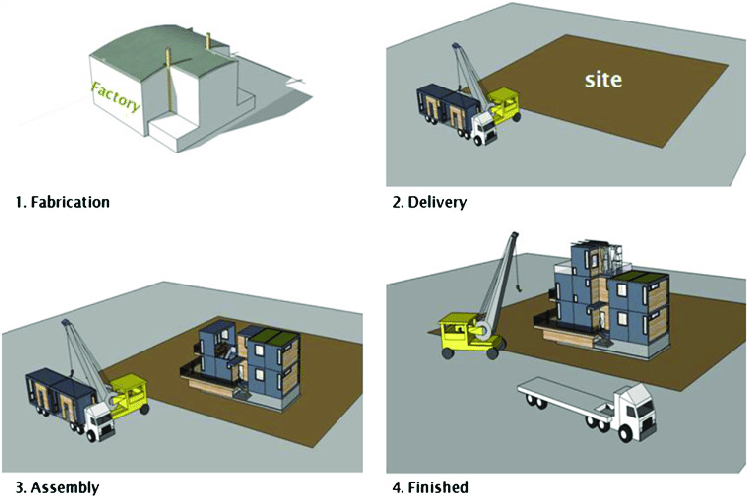
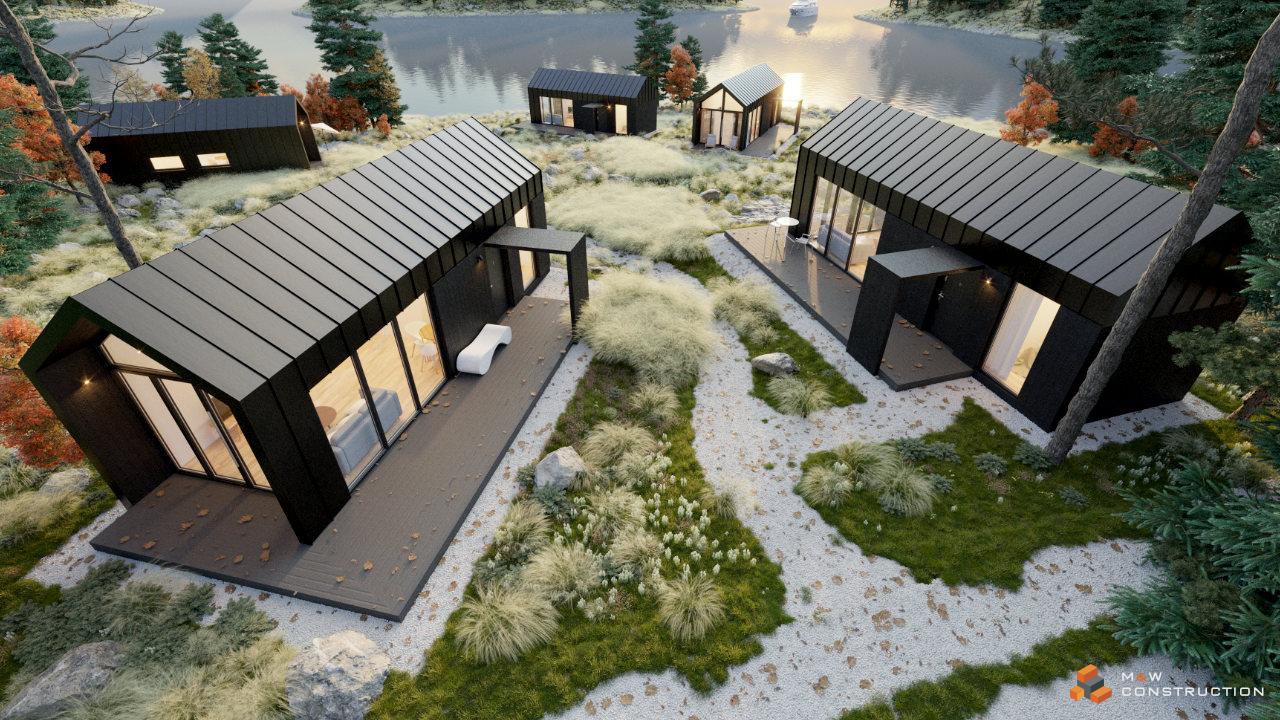
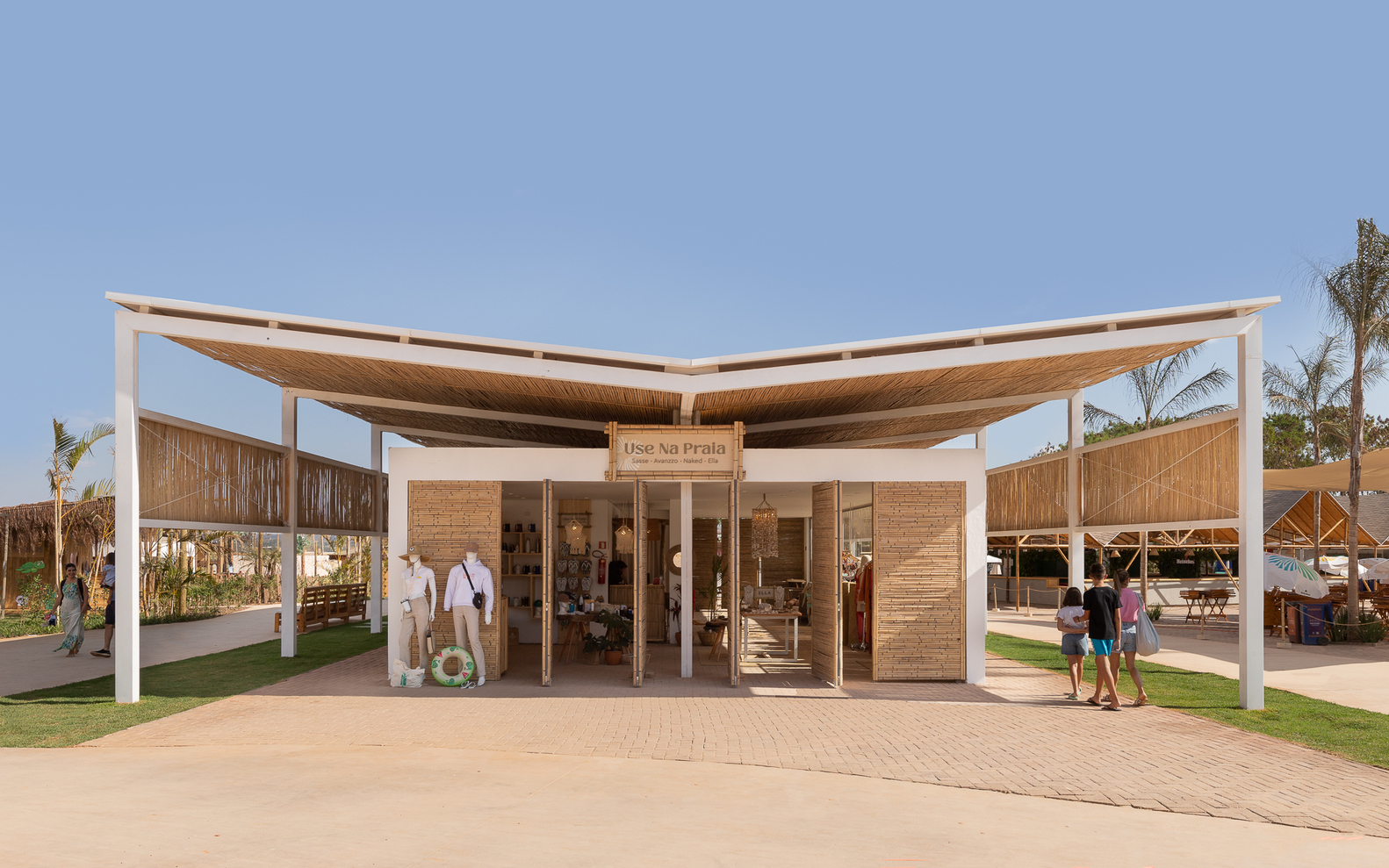
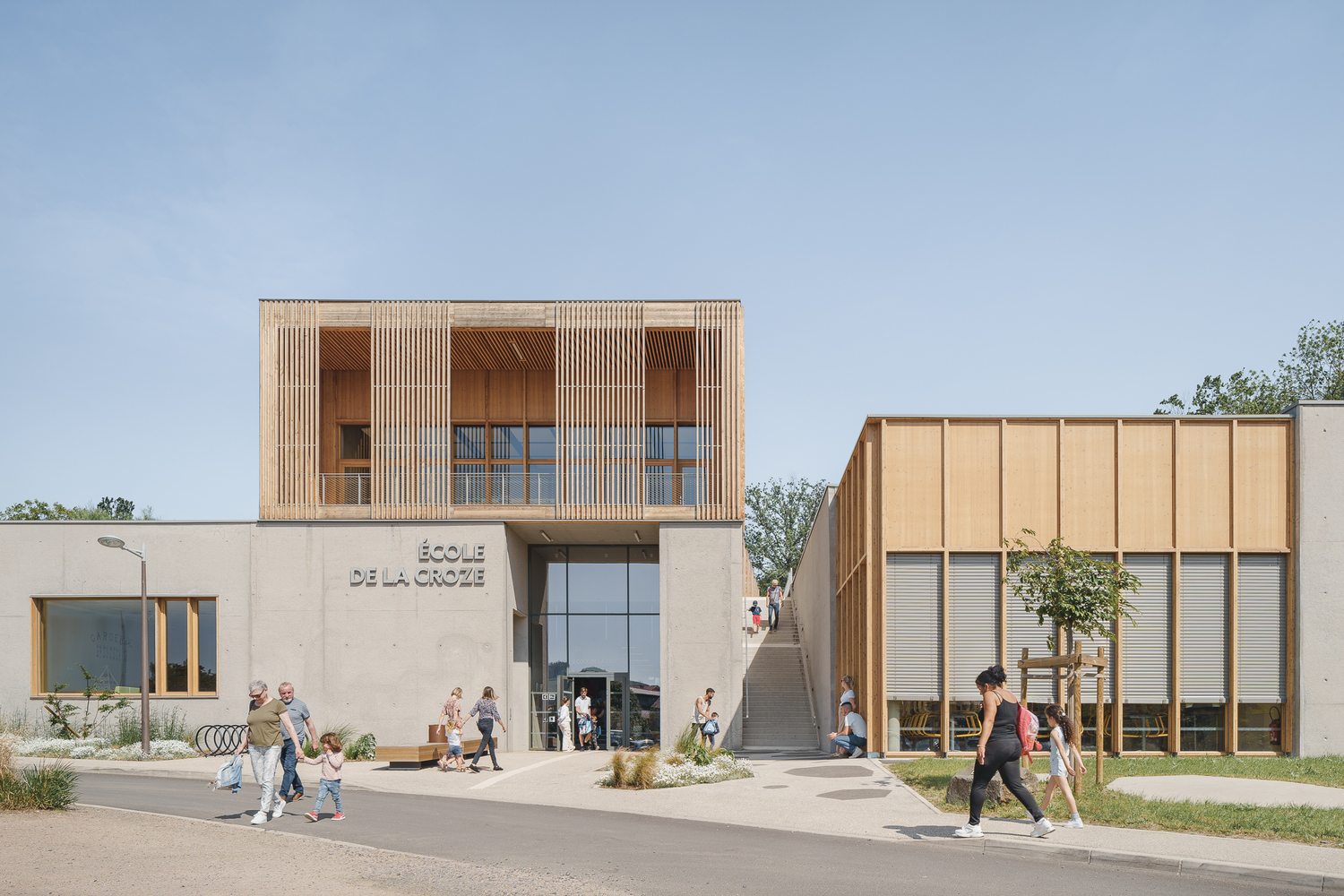
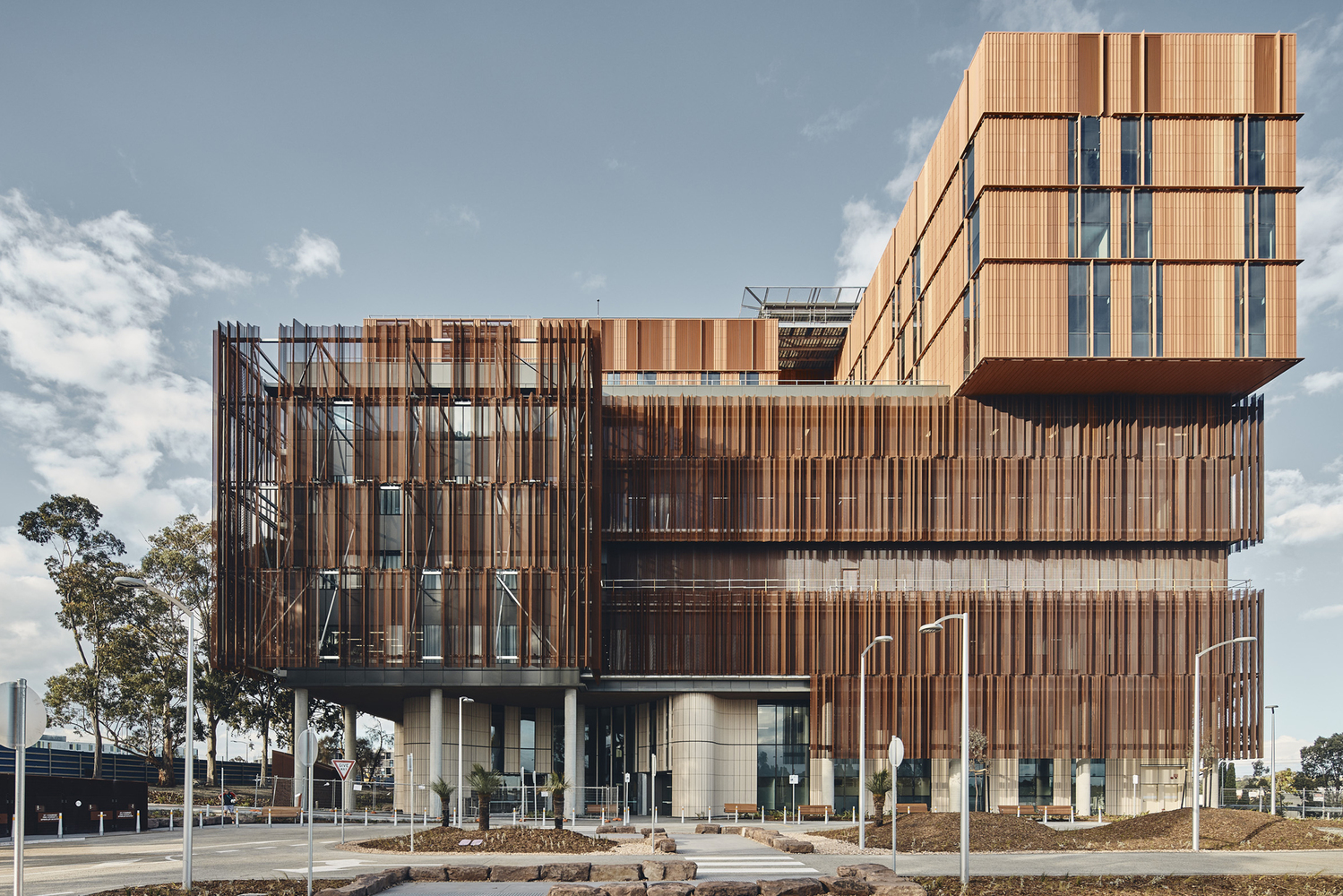
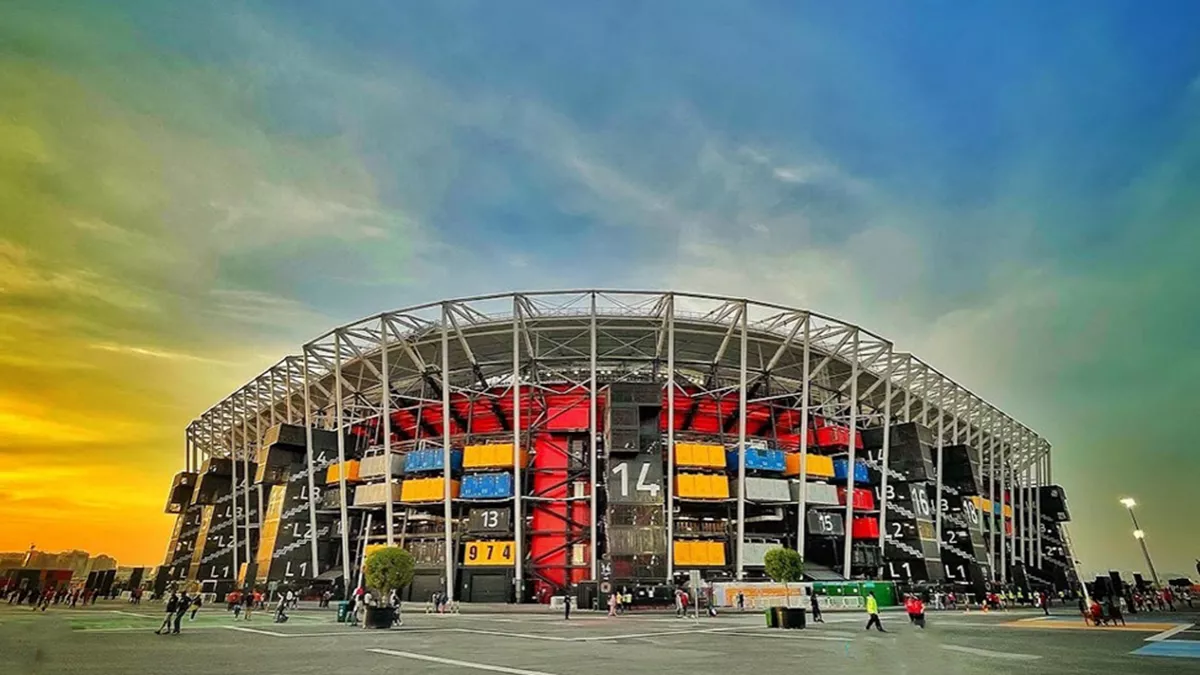
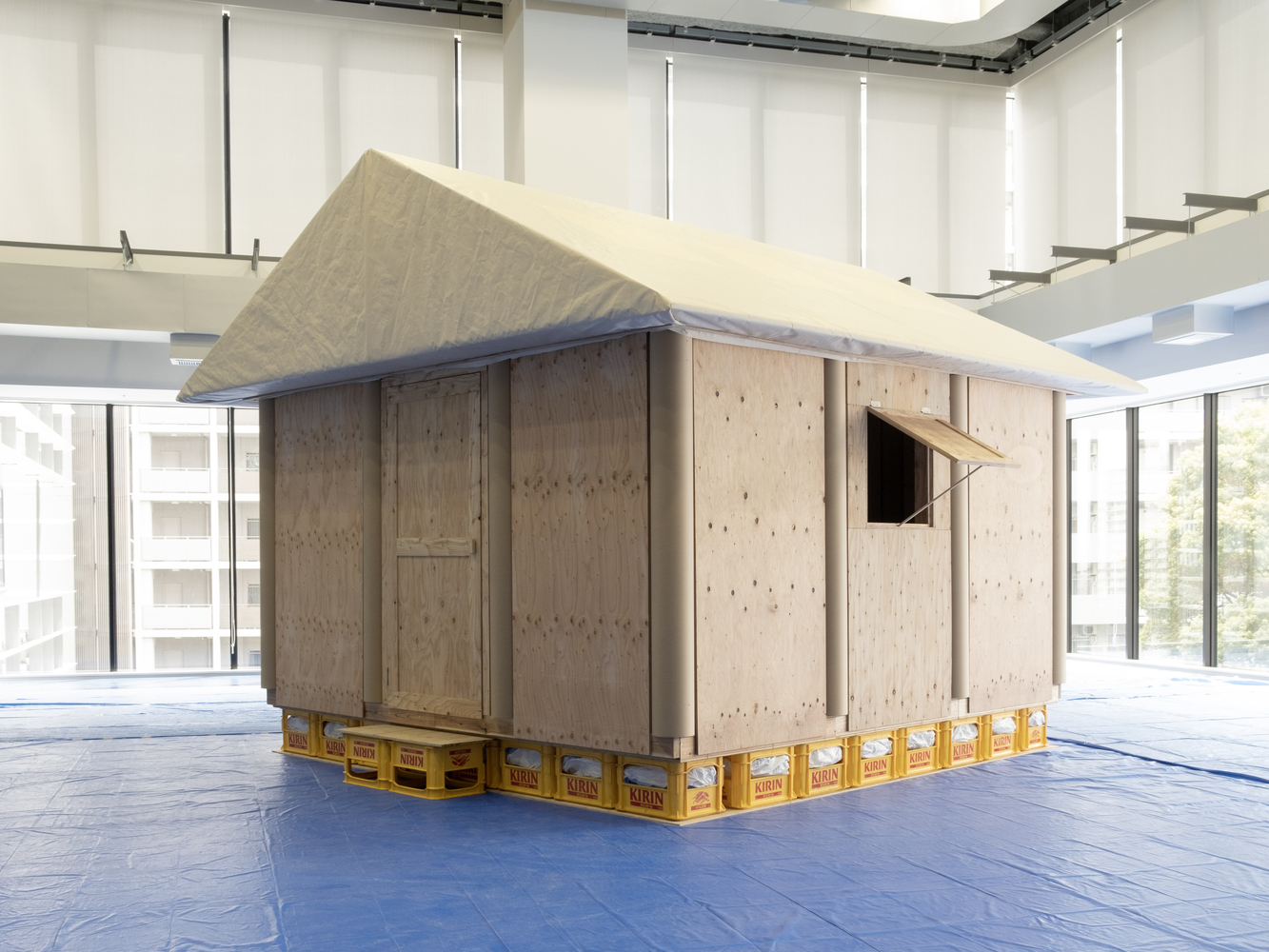
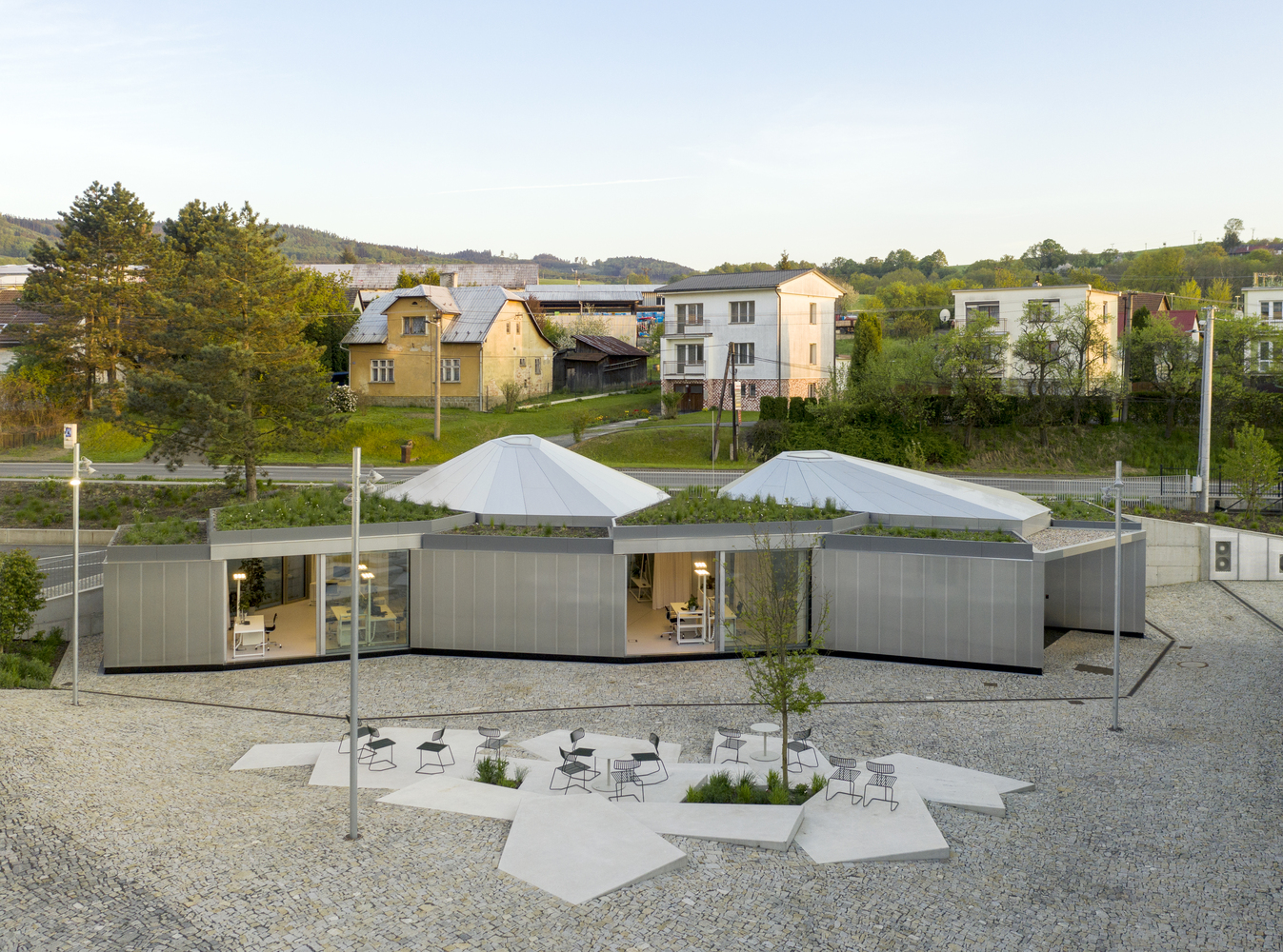