Radiance covers a standalone brick fireplace in a mid-century ranch home in Broad Ripple, Indiana. The clients rarely used their existing wood-burning fireplace and wanted to change its function. We proposed an ambient lighting piece that still hosts the traditional qualities of the hearth. As an artist and an architect, the clients’ liberal and eclectic design aesthetic allowed for a great degree of freedom and risk-taking during development. They considered this project as commissioned artwork rather than a client-based architectural intervention, adding to their collection in the home. Radiance is intended to exploit the qualities of the hearth by re-centering the focus of the home and providing an ambient environmental effect. The project was initiated through the clients’ interest in our plight sketch prototype, based on its subtle reactive lighting effects and human tracery. We expanded on these ideas, focusing on the visual and systematic complexities of the work. By creating simple geometry and interactions at local levels we could render complex reactions and forms in the overall scheme. Though it was developed and organized through its sub-components, the result is a continuous system that reacts uniformly.
DESIGN:
Radiance was inspired by various shelf mushrooms, based on their form, organizational structure, and component geometry. The mushroom has a distinguishing set of gills that alternate in lengths from the stem’s center point. The lengths of these gills form a repetitive pattern intended to cover the largest surface area under each mushroom cap. This pattern has been abstracted into our system to arrange each pod, defined as a radial set of 16 plastic components with an LED placed directly behind each. The wiring for the LEDs is embedded within the surface of milled MDF, further expressing the pod’s organizational system. A Passive Infrared Sensor is located at the centroid of each pod, acting as the trigger for the parts around it. Surface area coverage was important for the project as the poured plastic components and electronics are expensive and time-intensive. The patterning made coverage of the fireplace feasible meeting both our design criteria for density and fit within our timeline. A Grasshopper definition was developed to create the overall pattern and generate final fabrication files, including toolpaths for acrylic and MDF milling, as well as wire length calculations for each component.
DETAILS:
We constructed a steel frame that would enclose the existing fireplace, giving us the ability to fabricate most of the project offsite and assemble, predominantly, in their home. The frame bolts together so it can be disassembled for travel and reassembled onsite. All hardware is recessed in the frame to maintain clearance around the fireplace, and each corner embeds set screws in order to tighten against the fireplace and level out the project without drilling into the brick. Three sides were assembled completely before sliding the piece around the fireplace. Then the fourth access wall was then assembled utilizing embedded magnets in the MDF for attachment to the steel.
The MDF is the structural armature for all wiring, sensors, circuit boards, and plastic components. On the front side, the main LED wiring is exposed to express the organizational pattern while the reverse side contains all sensor, power, and serial wiring. Color is applied to this layer and masked with clear acrylic. The acrylic acts as a protective layer for the paint and brings out the richness of its color. Its milled areas catch the light of the LED’s, traveling through its clear portions. This tooling occurs in areas where the pods do not overlap, further expressing order as well as adding texture. To create an ambient and subtle reactive lighting piece we found it is necessary to dim all 512 LEDs individually. To do so, we developed our own Printed Circuit Board (PCB) manufactured through a third party vendor. This PCB houses our Integrated Circuits (TLC5940NT dip-28, made by Texas Instruments) utilizing Pulse Width Modulation (PWM or dimming) on each of its 16 outputs. This allows for the individual fading of each LED. Each of our PCBs corresponds with a pod of 16 elements. These elements pulse slowly out from the center when the sensor is triggered. The Passive Infrared sensor (PIR) is controlled by allowing only a small viewing angle through the acrylic surface, blocking infrared light from all but a designated cone of space off of the surface. These viewing cones have been tuned based on the existing spatial conditions of furniture, walls, and function of the home. Pods are in groups of three and run independently off of eleven individual Arduino Pro Mini microcontrollers. Each urethane plastic component is part of a multistep mold making process. We began by iteratively 3D printing potential forms. The positive powder prints are then sanded and coated in preparation for a two-part urethane rubber. Points in the mold were created to locate 3d printed jigs used to place a bolt and plastic spacer in each part which fastens to the MDF. We chose Smooth-Cast 325 as our poured plastic material due to its fast cure time, durability, and translucency. 512 hand-poured components were created at 12-13 parts per hour with very little variation between parts.
INTERACTION:
There are two pulses that occur after triggering a pod’s sensor. A primary ‘pulse’, that fades to full intensity and quickly fades off, followed by a secondary ‘pulse’ which fades on quickly but dims slowly over nearly a minute. This pattern can be interrupted as new users trigger a pulse creating the dynamic lighting effect seen in our video. Similar to the lighting effects of fire, Radiance creates dynamic changes in intensities across it surface. This makes the piece enticing to watch and because the pulses fade in and out so smoothly the lighting is not overbearing. There is a distinct difference in the lighting qualities throughout the day and into the night as the piece becomes more and more the central component bringing warmth and light into the home.
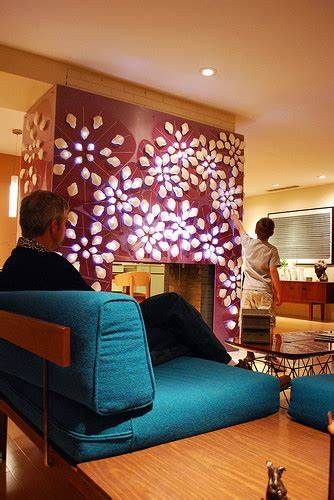
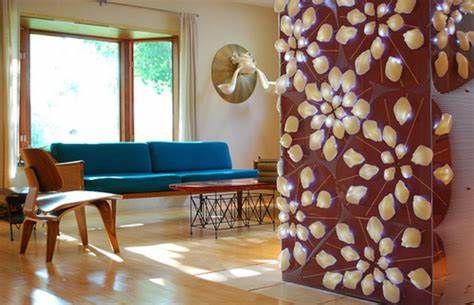
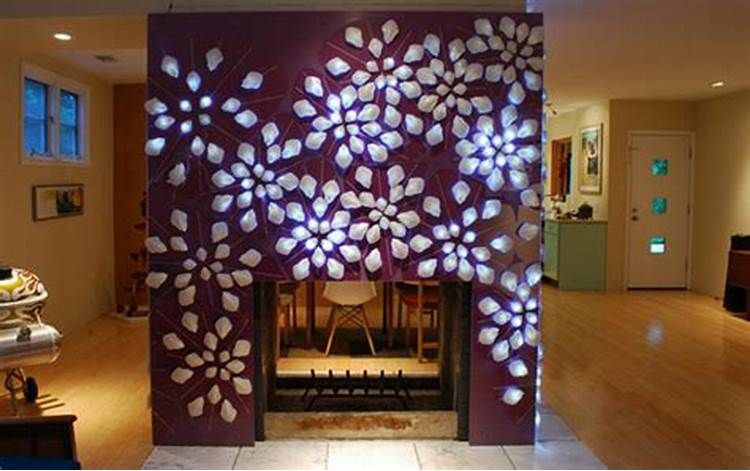
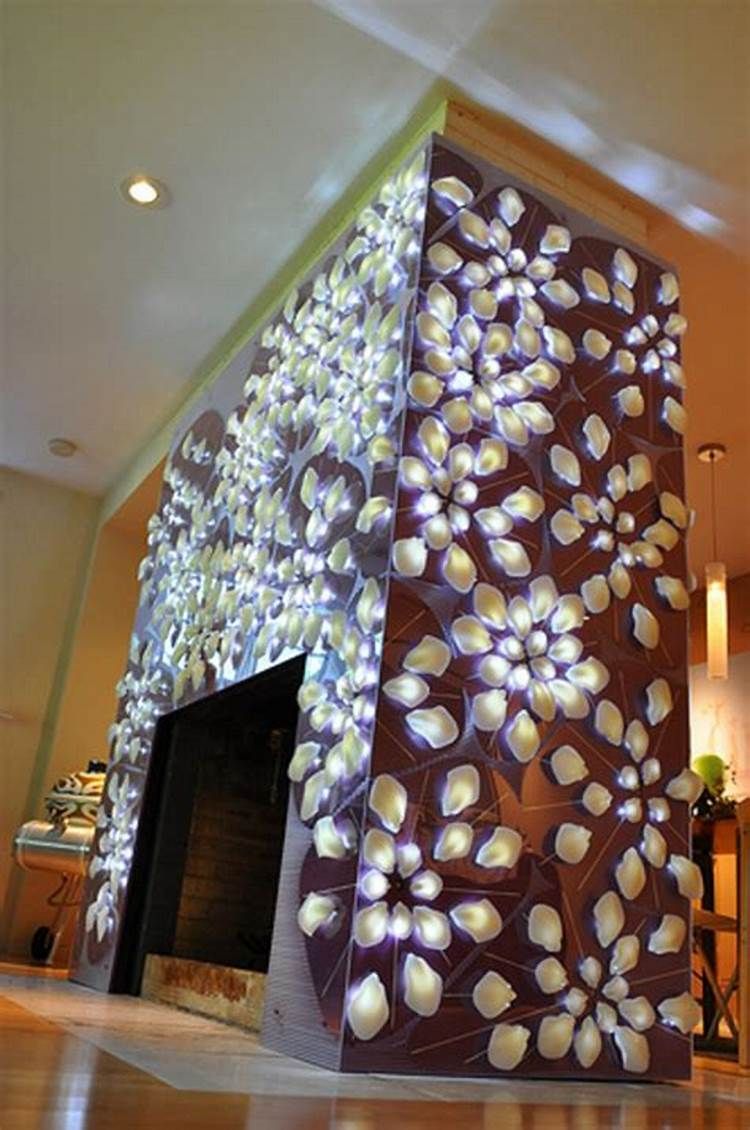
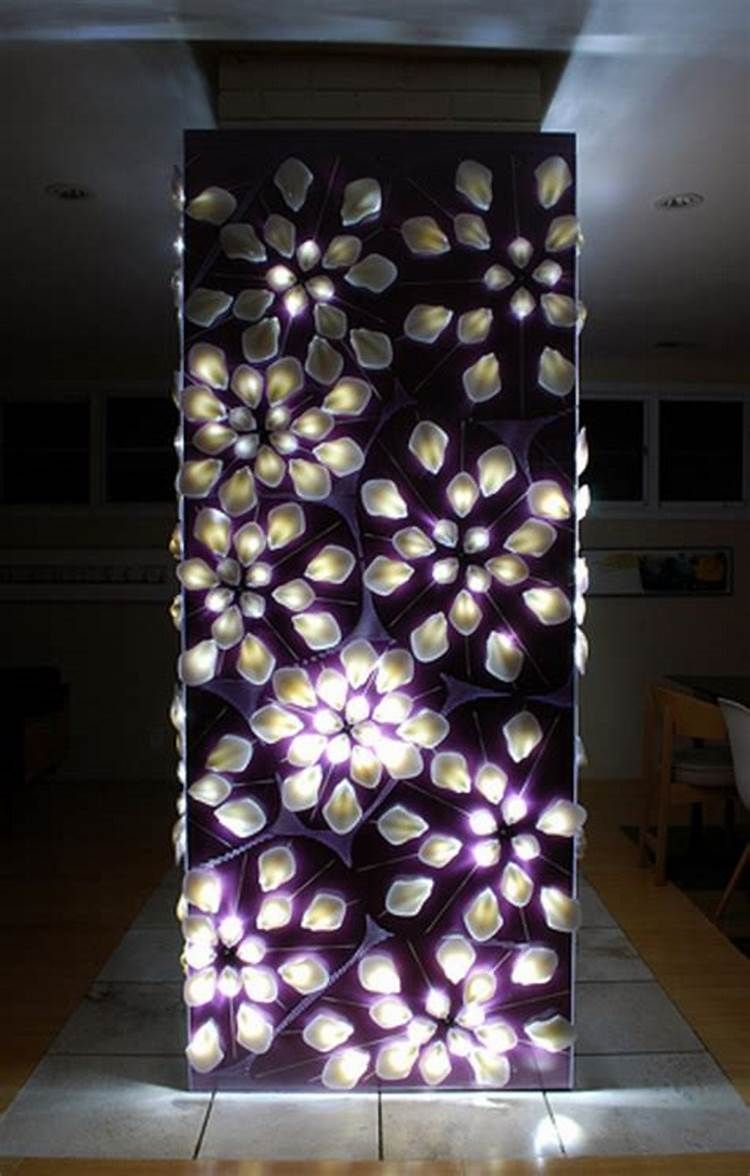
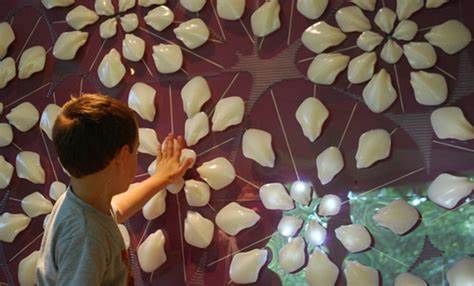
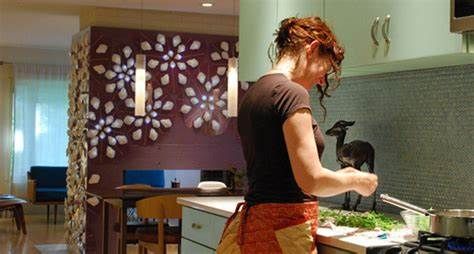
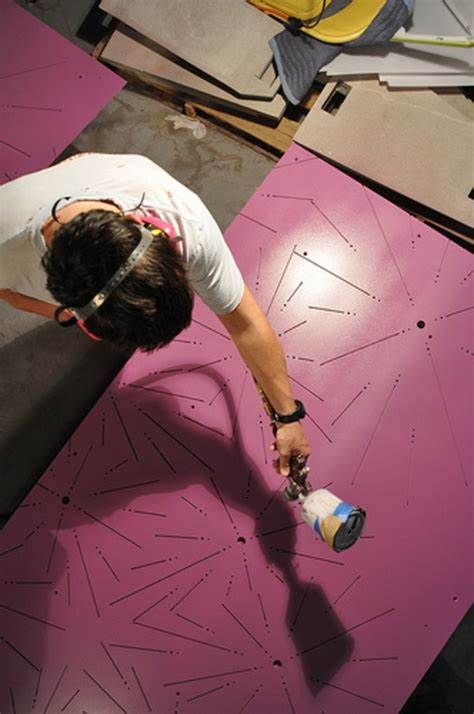