There have been many discussions in the current discourse over tool development and customization by architects and designers. An equally important argument here is the testing of the tools. This testing can be a continuous process through years of practice when certain tools are used, calibrated, and improved over the years, by software developers or by designers themselves, since design programming tools are open source now. Custom tools need to be tested before being implemented in practice and a continuous calibration is required before its commercial (or rather practical) usage. However, practice is also a way of testing the tools, with continuous calibration and evolution, but feasibility depends on the costs and time involved.
Gregory Epps’ London-based firm RoboFold developed and released the tool ‘KingKong’ earlier this year after a series of in-house testing and calibration, matched with Epps’ years of experience in the field of curved folding. KingKong is a plugin for Grasshopper (a popular parametric tool for Rhinoceros 3D) which simulates the process of curved folding in a digital medium, aids in designing architectural façade systems using curved folding, and has the potential of integrating with robotic fabrication for the paneling systems.
This linear approach from design to fabrication forms the core of the firm, which is tested continuously through regular workshops in the London studio & fabrication facility of RoboFold. Some of the recent workshops incorporated the use of the tools created by RoboFold, specifically KingKong where participants were allowed to test the physical experimentations in the digital medium for prototypical fabrication.
Two-day workshops offered at RoboFold on a monthly basis are focussed on basic concepts of curved folding, tested on paper, with analysis and geometric studies of physical models. The data is then fed to a digital medium and simulated and altered as per design requirements using the specialized tool. This is where the tool calibration comes into the picture; as such workshops form a part of the continuous tool development and testing by the firm. The digital simulations then lead to fabrication data and scaled prototypes are developed.
The bigger argument here is about the testing of customized tools created by designers. A gap, however, is observed in the design industry where designers and architects are creating their customized tools, and software companies are creating many advanced and stable platforms to be used by designers. Integration in the design and software industry is required today to create better working platforms and continuous design processes.
A successful example of such an integration is Gehry Technologies emerging out of Gehry Partners due to the need for a parallel AEC setup for complex modeling solutions. Such developments were on a halt for many years and have started to pick up recently with specialized modeling groups and computational design cells in design firms. Testing of tools is as important as creating the tools, to avoid a failure in the long run, before it is too late to realize and rectify the problem. Design and software industries need to be well integrated into this era of computational design before designers take the challenge of creatin
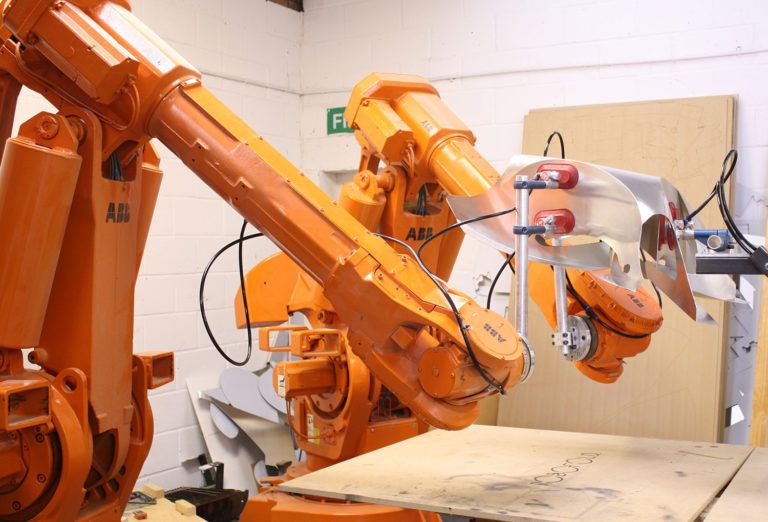
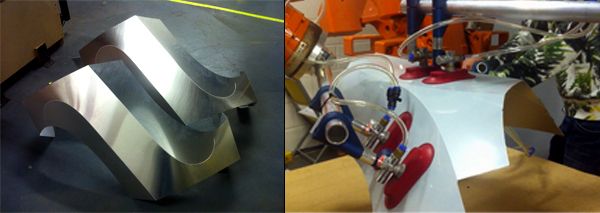
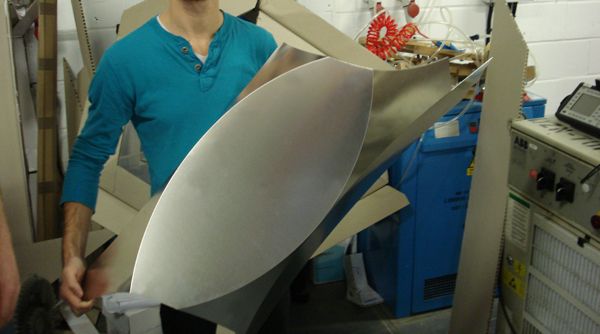

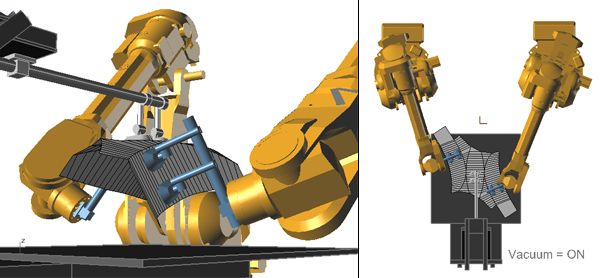
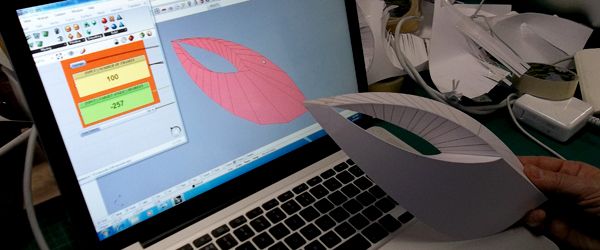

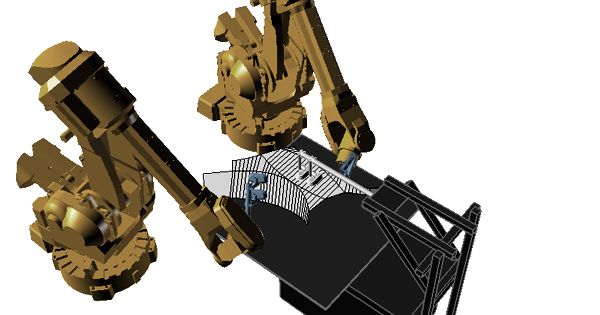
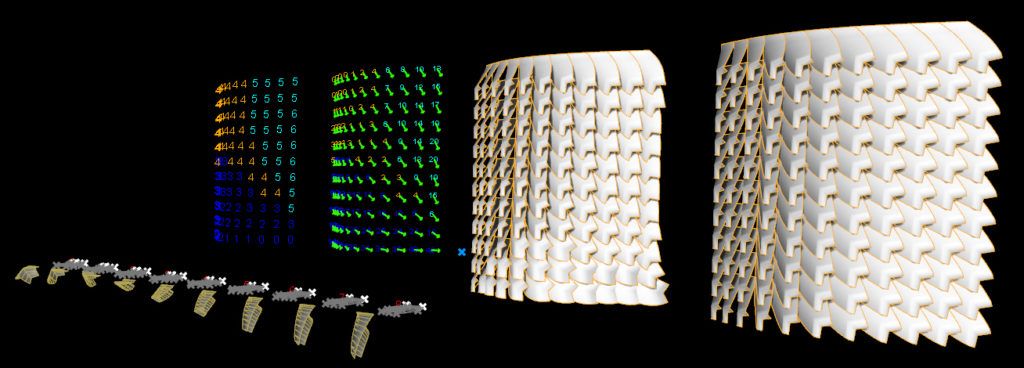
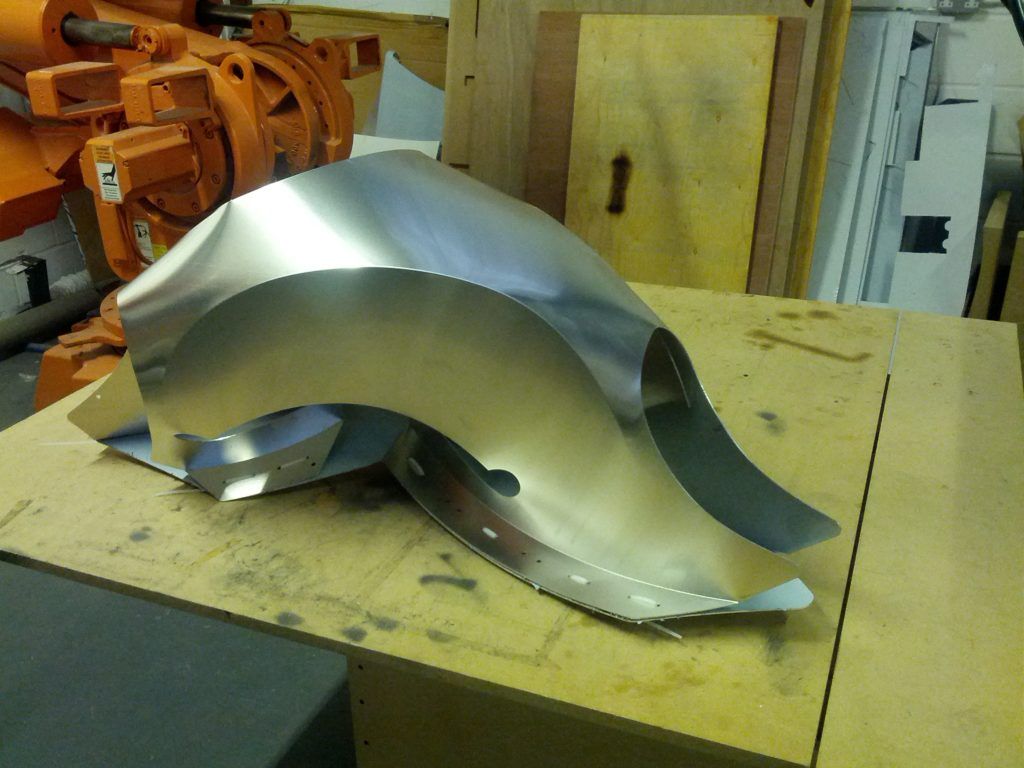
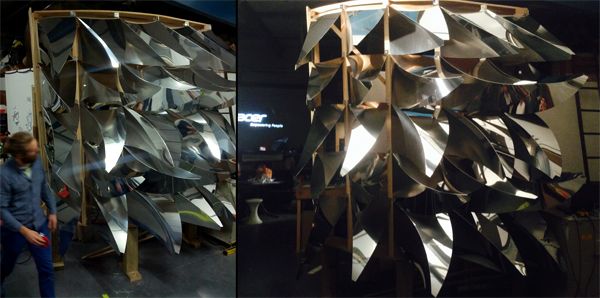
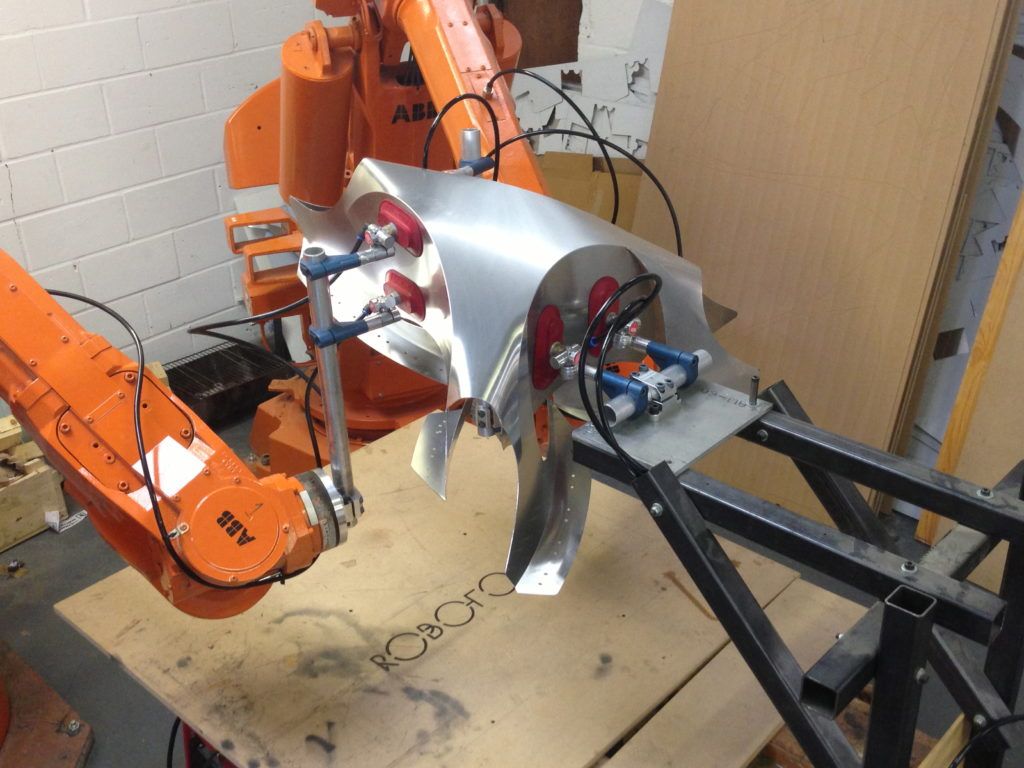
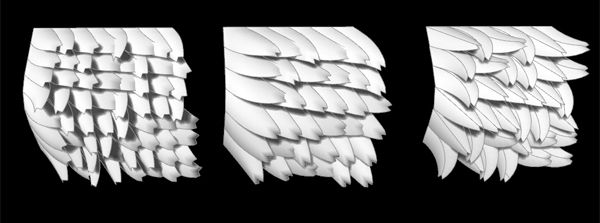
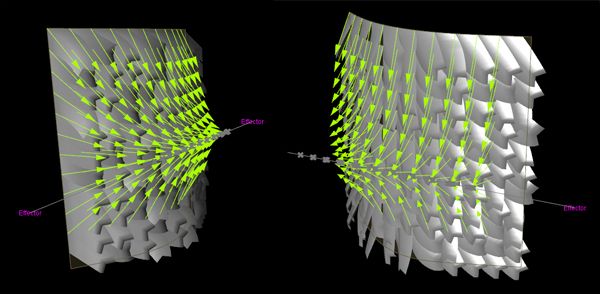
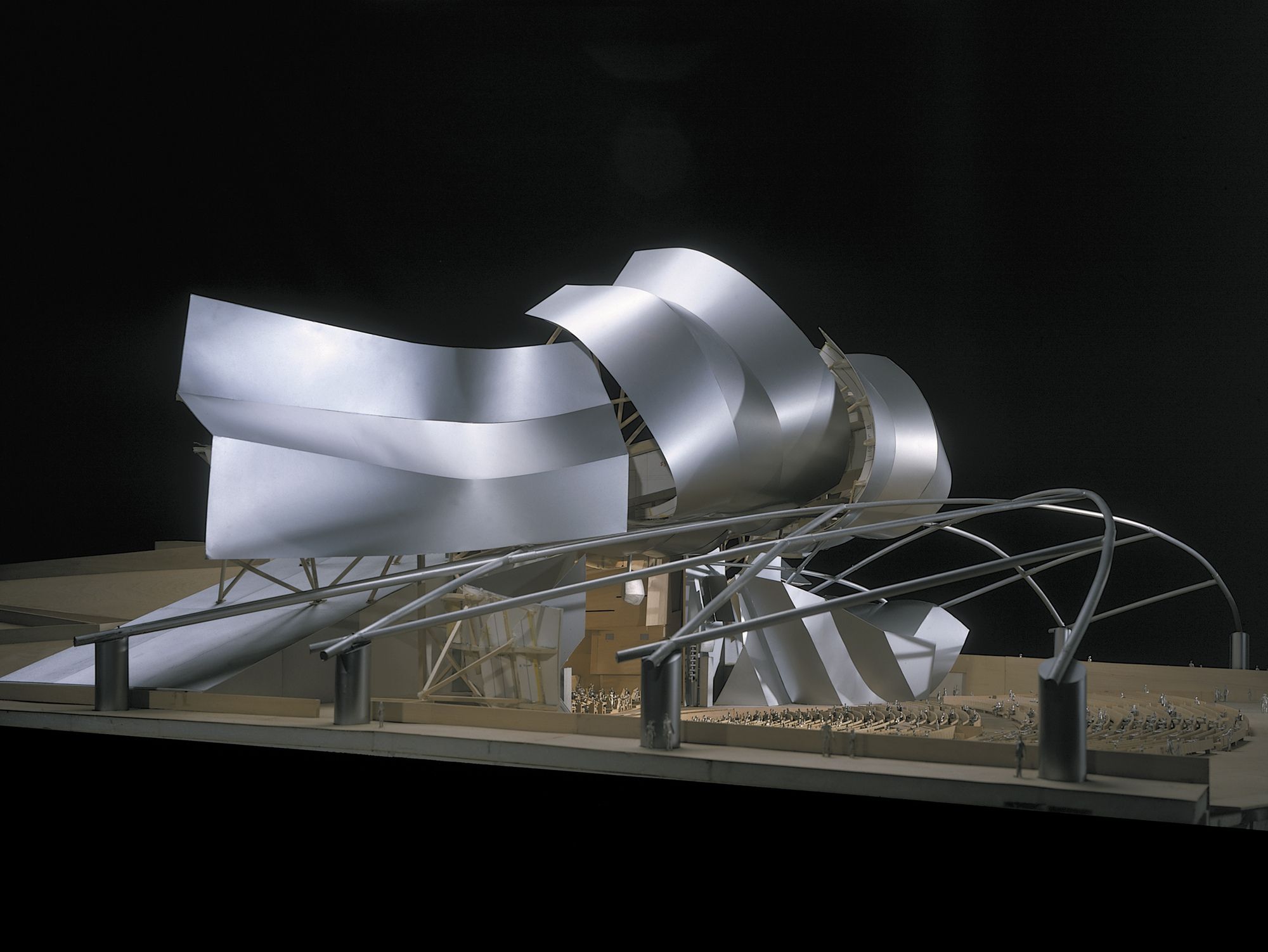
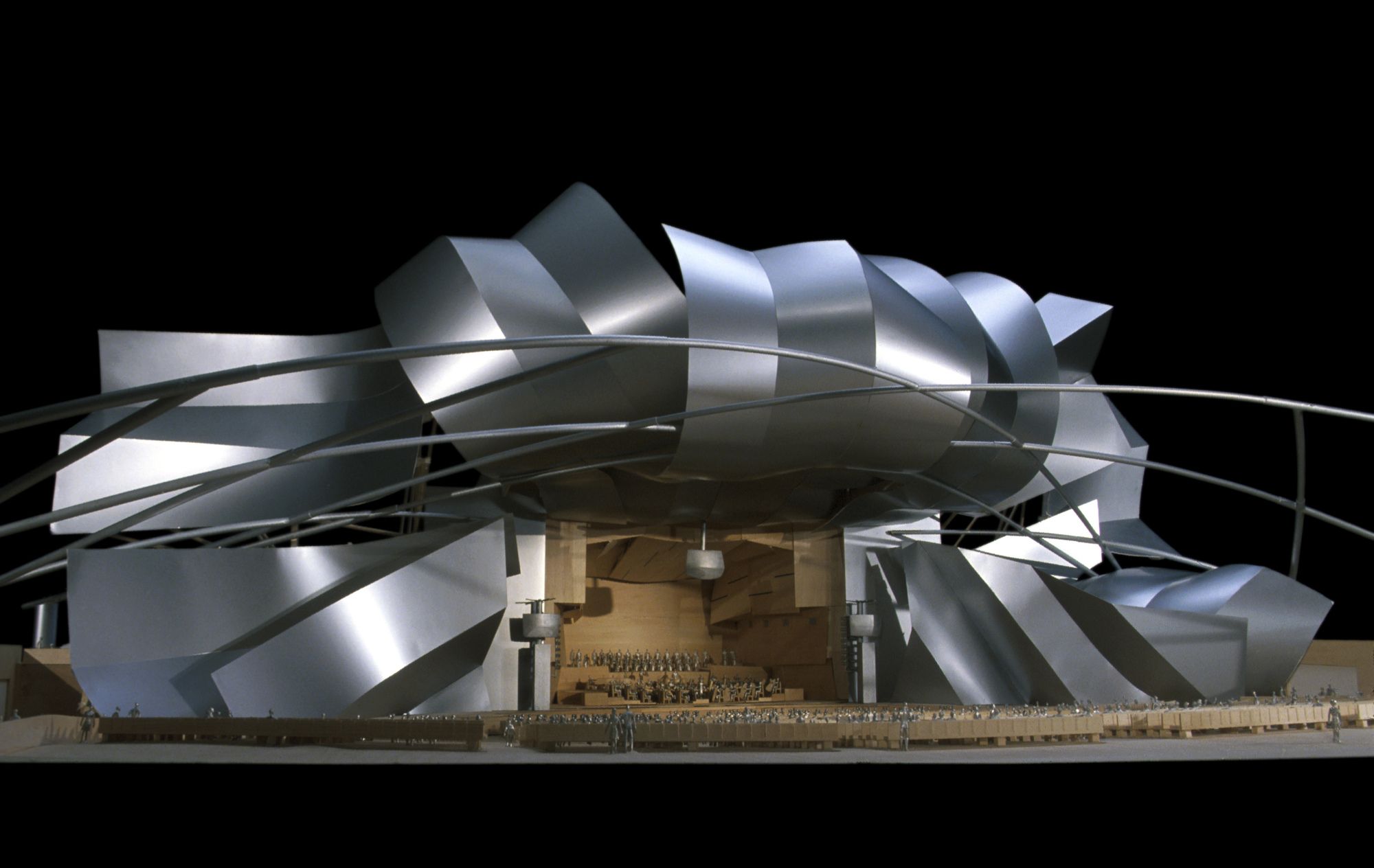
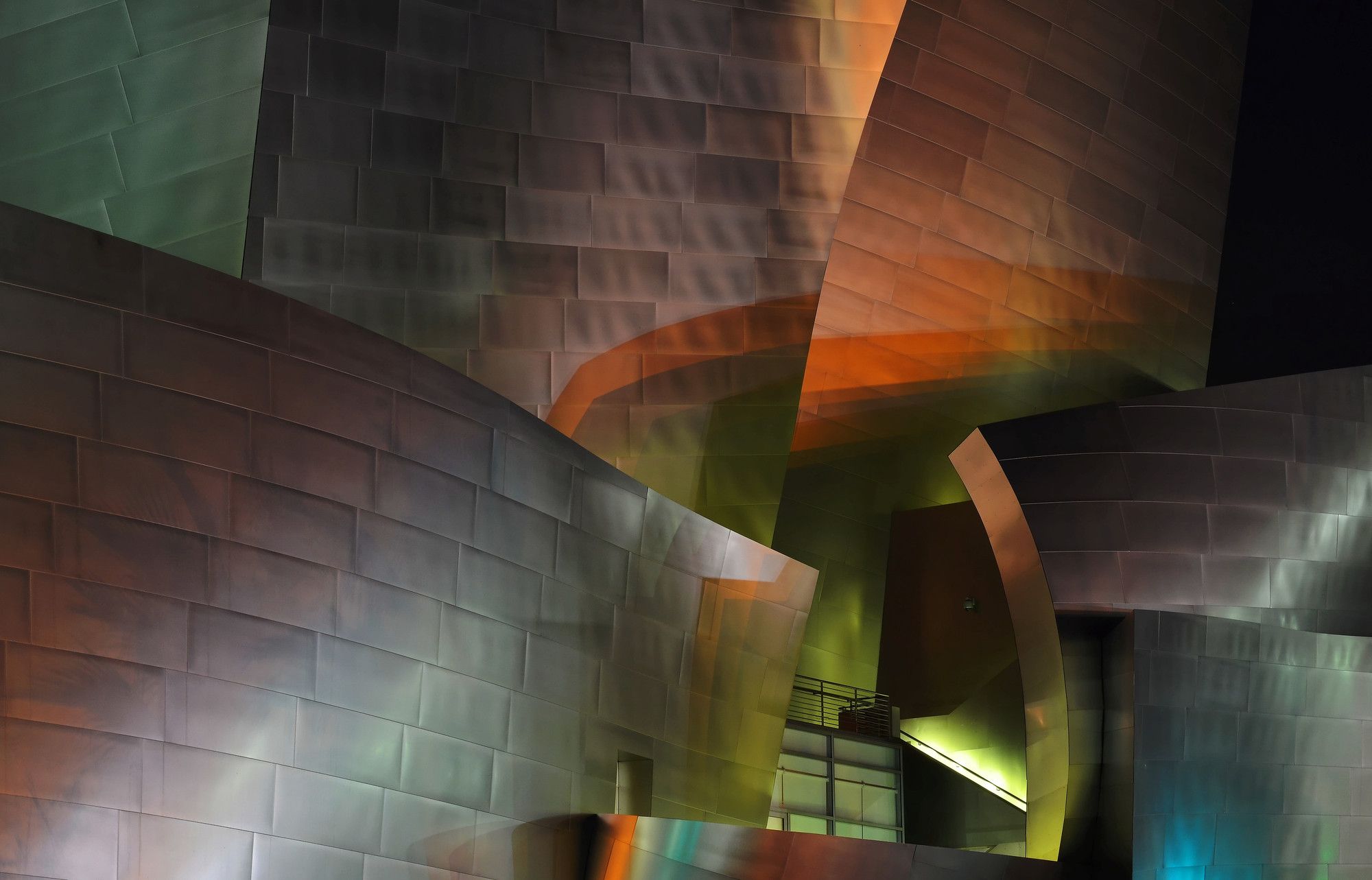
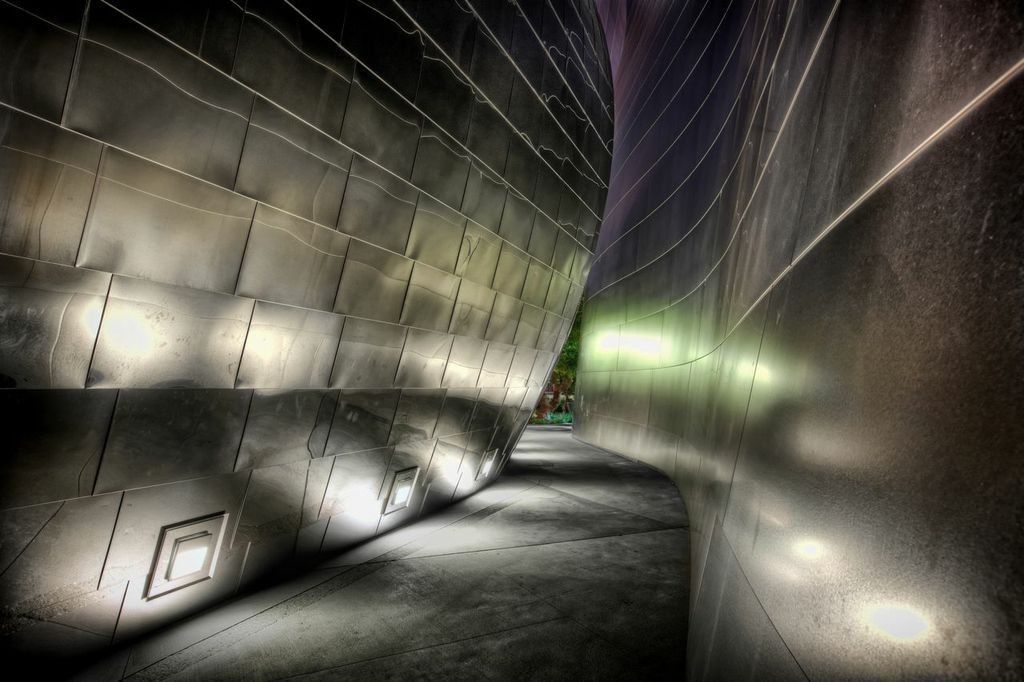